Waterjet Technologies
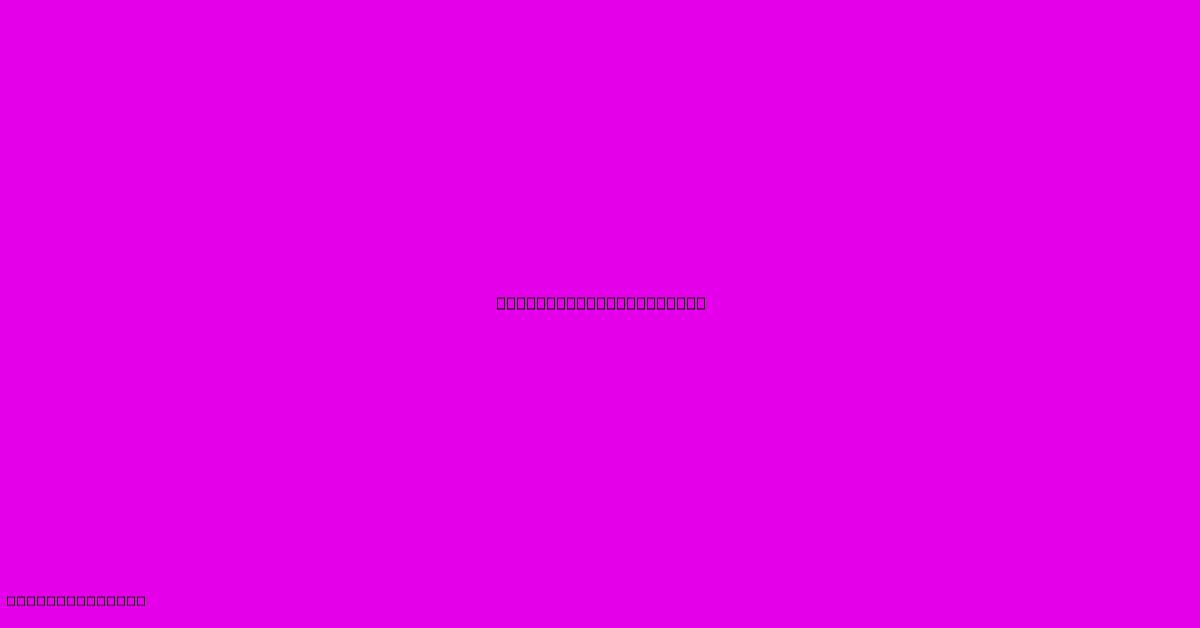
Discover more detailed and exciting information on our website. Click the link below to start your adventure: Visit Best Website mr.cleine.com. Don't miss out!
Table of Contents
Mastering the Power of Water: A Deep Dive into Waterjet Technologies
Waterjet technology, a high-pressure cutting method utilizing a jet of water mixed with an abrasive, has revolutionized numerous industries. Its versatility and precision make it a powerful tool for various applications, from intricate metalwork to delicate fabric cutting. This article delves into the intricacies of waterjet technology, exploring its mechanisms, advantages, applications, and future trends.
Understanding the Mechanics of Waterjet Cutting
At its core, waterjet cutting harnesses the immense power of pressurized water. A pump, often exceeding 60,000 psi, forces water through a tiny nozzle, creating a high-velocity jet capable of cutting through a wide array of materials. For harder materials like steel or granite, an abrasive, typically garnet, is added to the water stream, significantly enhancing its cutting capabilities. This abrasive intensifies the cutting power, allowing for precise cuts in even the toughest substances.
The process is remarkably versatile. The cutting head's ability to move in multiple axes enables complex shapes and designs. Furthermore, the process is relatively clean, producing minimal heat and noise compared to other cutting methods such as laser or plasma cutting. This minimal heat generation is crucial for heat-sensitive materials, preventing warping or damage.
Advantages of Waterjet Technology
Waterjet cutting offers numerous benefits over traditional methods:
- Versatility: Cuts a wide range of materials, including metals, stone, glass, composites, and textiles, without needing to change tools.
- Precision: Achieves highly accurate cuts with minimal kerf (the width of the cut), resulting in reduced material waste and improved dimensional accuracy.
- Minimal Heat Affected Zone (HAZ): The low heat generation prevents warping and damage to heat-sensitive materials, preserving their integrity.
- Reduced Material Waste: Precise cutting minimizes material loss, contributing to cost savings and sustainability.
- Clean Cutting Process: Produces minimal noise and dust, making it a cleaner and more environmentally friendly option.
- No Tool Wear: Unlike traditional cutting methods, the abrasive garnet is the only consumable, reducing tool maintenance costs and downtime.
Diverse Applications Across Industries
The versatility of waterjet technology has led to its widespread adoption across numerous sectors:
- Manufacturing: Cutting metal sheets, pipes, and other components for automotive, aerospace, and shipbuilding industries.
- Stone Fabrication: Shaping and cutting granite, marble, and other stone materials for countertops, sculptures, and architectural features.
- Food Processing: Precisely cutting food products without causing damage or contamination.
- Textile Industry: Cutting fabrics for apparel and other textile products.
- Aerospace: Cutting composite materials with high precision, crucial for building lightweight and high-strength components.
- Automotive: Manufacturing various components such as engine parts and chassis components.
Future Trends in Waterjet Technology
Continuous innovation drives advancements in waterjet technology:
- Improved Pump Technology: Higher pressure pumps are being developed to further enhance cutting speed and efficiency.
- Automated Systems: Increased automation through robotic integration leads to higher throughput and reduced labor costs.
- Advanced Abrasives: The development of more efficient and environmentally friendly abrasives is an ongoing focus.
- Hybrid Systems: Combining waterjet cutting with other technologies, such as laser cutting, to leverage the strengths of both methods.
Conclusion
Waterjet technology has undeniably transformed numerous industries. Its versatility, precision, and environmentally friendly nature establish it as a superior cutting solution for a wide range of applications. As technology continues to advance, waterjet cutting promises even greater efficiency, precision, and sustainability, solidifying its position as a cornerstone of modern manufacturing and processing.
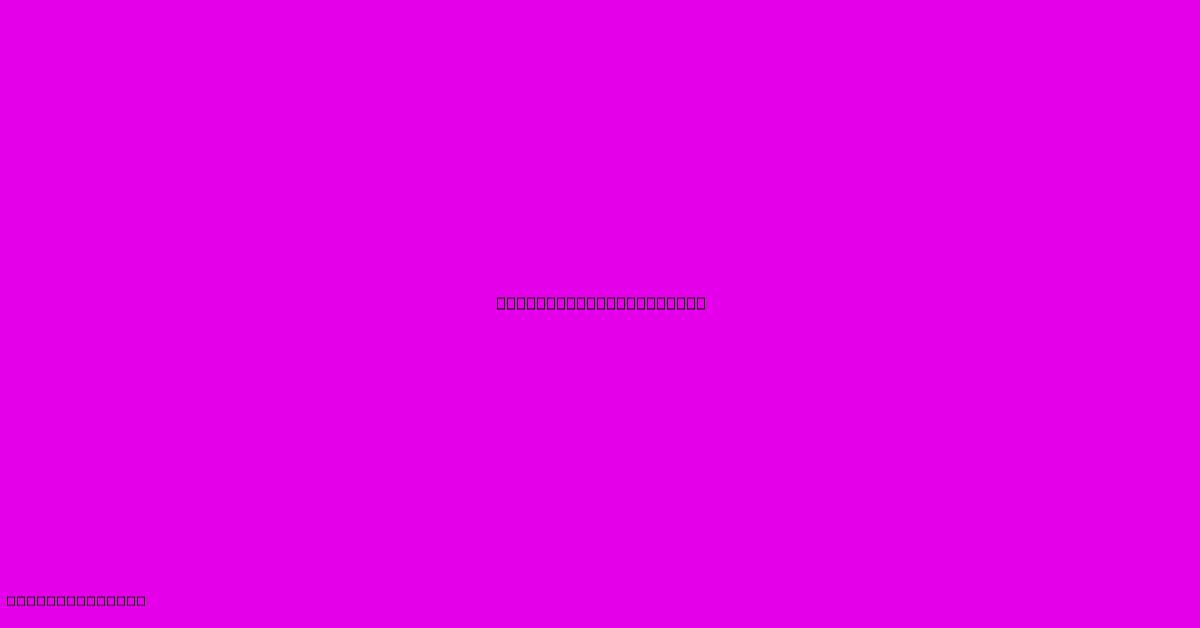
Thank you for visiting our website wich cover about Waterjet Technologies. We hope the information provided has been useful to you. Feel free to contact us if you have any questions or need further assistance. See you next time and dont miss to bookmark.
Featured Posts
-
Pioneer Technology And Arts Academy Colorado Springs
Dec 24, 2024
-
Optimasi On Page Pastikan Kata Kunci Terpilih Tertanam Secara Alami Di Dalam Judul H1 Sub Judul H2 H3 Meta Deskripsi Dan Di Sepanjang Isi Artikel Gunakan Variasi Kata Kunci Untuk Menghindari Keyword Stuffing Optimalkan Gambar Dengan Alt Text Yang Relevan Dengan Kata Kunci
Dec 24, 2024
-
Delonghi Ceramic Technology Eco
Dec 24, 2024
-
Remington Pro Multi Styler With Twist And Curl Technology Reviews
Dec 24, 2024
-
Web Development Technology
Dec 24, 2024