Vector Tooling Technologies
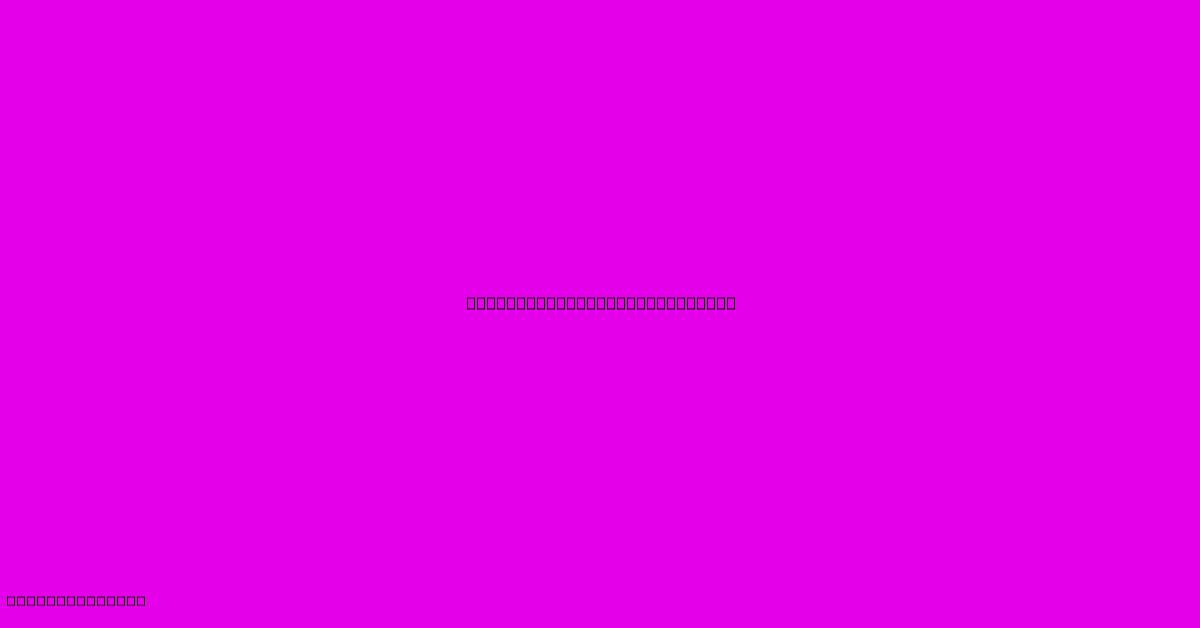
Discover more detailed and exciting information on our website. Click the link below to start your adventure: Visit Best Website mr.cleine.com. Don't miss out!
Table of Contents
Revolutionizing Manufacturing: A Deep Dive into Vector Tooling Technologies
Vector tooling technologies represent a significant advancement in manufacturing processes, offering unparalleled precision, efficiency, and flexibility. This article explores the intricacies of this innovative approach, examining its core principles, applications, and the transformative impact it's having on various industries.
What is Vector Tooling?
Unlike traditional tooling methods that rely on fixed geometries, vector tooling employs dynamic, computer-controlled processes. Think of it as "printing" tools instead of machining them from a solid block. This allows for intricate, highly customized designs that would be impossible or prohibitively expensive with conventional techniques. The "vector" in the name refers to the use of mathematical vectors to define the tool's shape and path during the manufacturing process.
Core Principles of Vector Tooling:
- Additive Manufacturing Integration: Vector tooling often leverages additive manufacturing (AM) technologies like 3D printing to create the tools themselves. This allows for rapid prototyping and the production of complex geometries with internal channels and features.
- Computer-Aided Design (CAD) & Computer-Aided Manufacturing (CAM): Sophisticated CAD/CAM software is crucial. These programs not only design the tools but also generate the precise instructions for the manufacturing process, ensuring accuracy and repeatability.
- Real-time Adjustment & Feedback: Many vector tooling systems incorporate real-time feedback mechanisms, allowing for adjustments during the manufacturing process based on sensor data. This enhances precision and minimizes errors.
- Material Flexibility: Vector tooling is compatible with a wide range of materials, from metals and polymers to composites, expanding the possibilities for tool creation.
Applications Across Industries:
The versatility of vector tooling makes it applicable across numerous industries:
- Aerospace: Creating lightweight, high-strength components with complex internal structures for aircraft and spacecraft.
- Automotive: Manufacturing intricate parts for vehicles, improving efficiency and reducing production time.
- Medical Devices: Producing highly precise surgical instruments and implants with customized designs.
- Electronics: Creating complex molds and tooling for microelectronics manufacturing.
- Robotics: Enabling the creation of custom end-effectors and tooling for robots, enhancing their adaptability.
Advantages of Vector Tooling:
- Increased Speed & Efficiency: Reduced lead times due to the streamlined design and manufacturing processes.
- Enhanced Precision & Accuracy: Minimized errors and improved dimensional accuracy compared to traditional methods.
- Greater Design Flexibility: Ability to create complex shapes and geometries that were previously impossible.
- Cost Savings: Lower tooling costs in some cases, especially for low-volume production runs of complex parts.
- Reduced Material Waste: Additive manufacturing minimizes material waste compared to subtractive methods.
Challenges and Future Trends:
Despite its advantages, vector tooling still faces challenges:
- High Initial Investment: The specialized equipment and software can be expensive.
- Skill Requirements: Operators require specialized training in CAD/CAM software and the operation of AM equipment.
- Material Limitations: Not all materials are suitable for all AM processes used in vector tooling.
Future trends point toward:
- Increased Automation: Further integration of AI and machine learning to optimize the process.
- Multi-Material Tooling: The ability to create tools from multiple materials for enhanced functionality.
- Hybrid Manufacturing Processes: Combining vector tooling with traditional methods for optimal results.
Conclusion:
Vector tooling technologies represent a paradigm shift in manufacturing. By combining the power of computer-aided design, additive manufacturing, and dynamic control, this innovative approach delivers unparalleled precision, speed, and flexibility. While challenges remain, the benefits are clear, making vector tooling a critical technology driving innovation across various industries for years to come. The ongoing development and refinement of this technology will undoubtedly lead to even more transformative applications in the future.
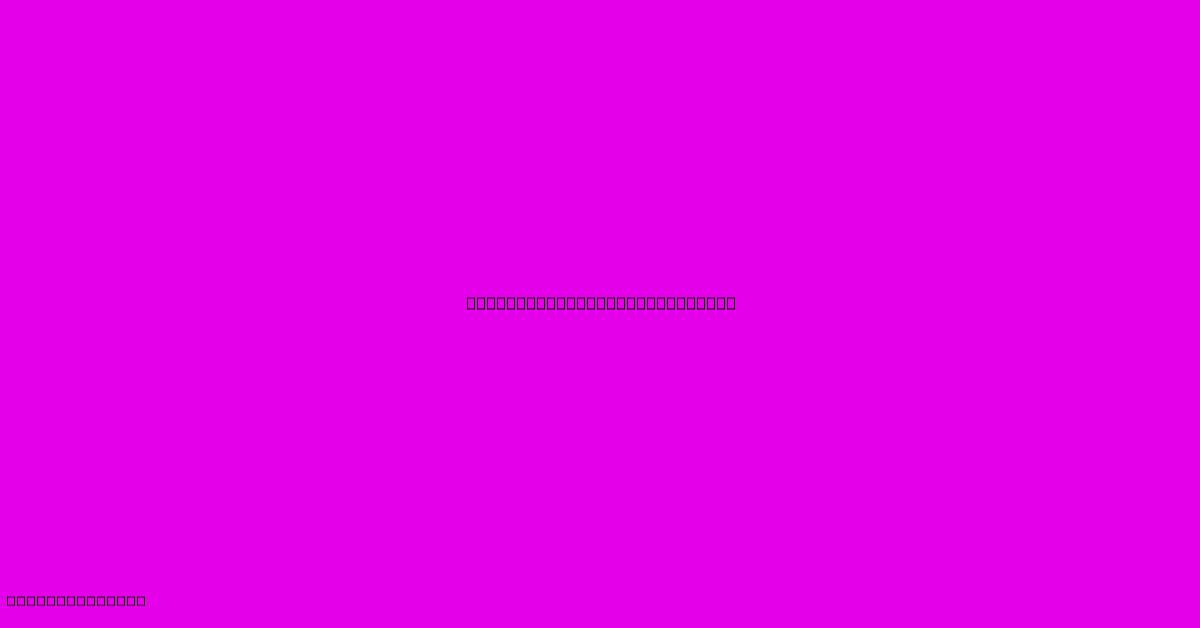
Thank you for visiting our website wich cover about Vector Tooling Technologies. We hope the information provided has been useful to you. Feel free to contact us if you have any questions or need further assistance. See you next time and dont miss to bookmark.
Featured Posts
-
Mi Technologies Inc
Jan 03, 2025
-
Bunch Technology Gmbh
Jan 03, 2025
-
Advanced Materials Technology
Jan 03, 2025
-
Technology Coordinator Salary
Jan 03, 2025
-
Wipro Technologies Review
Jan 03, 2025