Tubing Technology
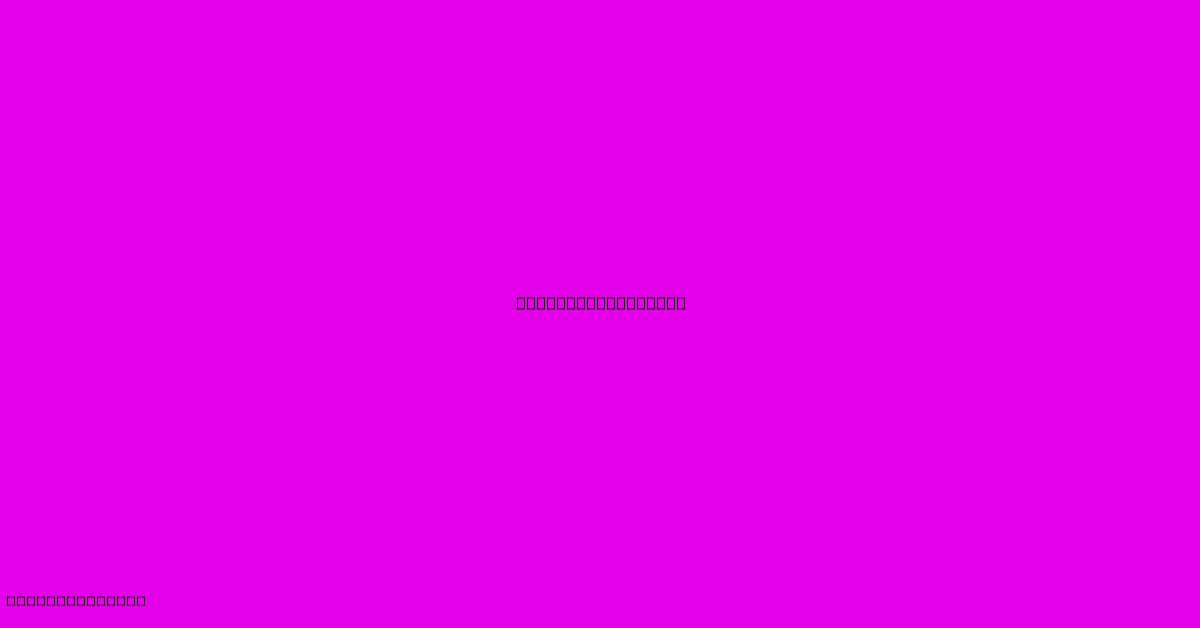
Discover more detailed and exciting information on our website. Click the link below to start your adventure: Visit Best Website mr.cleine.com. Don't miss out!
Table of Contents
Tubing Technology: A Deep Dive into Material Science and Applications
Tubing technology encompasses the design, manufacturing, and application of hollow cylindrical structures, known as tubes, used across a vast range of industries. This technology extends far beyond simple pipes; it's a sophisticated field involving advanced material science, precise manufacturing processes, and specialized engineering to achieve optimal performance in diverse applications.
Understanding the Fundamentals:
The core of tubing technology lies in material selection and manufacturing techniques. The choice of material heavily influences the tube's properties, determining its suitability for specific applications. Common materials include:
-
Metals: Steel (carbon steel, stainless steel, alloy steel), aluminum, copper, brass, and titanium are widely used due to their strength, durability, and resistance to various environmental factors. The specific alloy composition dictates the tube's mechanical properties, corrosion resistance, and temperature tolerance.
-
Plastics: Polyvinyl chloride (PVC), polyethylene (PE), polypropylene (PP), and polytetrafluoroethylene (PTFE) are frequently used for their lightweight, corrosion resistance, and cost-effectiveness. However, their temperature and pressure limitations need careful consideration.
-
Ceramics: Used in high-temperature applications or where exceptional chemical inertness is needed. These are often more brittle than metallic or plastic options.
-
Composites: Combining different materials (e.g., fiber-reinforced polymers) to achieve a unique combination of properties, such as high strength-to-weight ratio and tailored stiffness.
Manufacturing Processes:
The manufacturing process significantly impacts the final tube's quality, precision, and cost. Common methods include:
-
Drawing: Pulling a heated metal billet through a die to reduce its diameter and create a tube. This process is suitable for high precision and consistent wall thickness.
-
Extrusion: Forcing a heated material through a die to create a continuous tube. This method is widely used for plastics and some metals.
-
Rolling: Used for larger diameter tubes, this involves passing a metal slab between rollers to form a cylindrical shape.
-
Welding: Joining separate metal sheets or strips to form a cylindrical tube. This method allows for large-diameter tubes and customizable wall thicknesses.
Applications Across Industries:
The versatility of tubing technology allows its application in numerous sectors:
1. Oil and Gas: High-pressure and high-temperature resistant tubing is crucial for drilling, transportation, and refining operations. Advanced materials and specialized coatings are often used to handle corrosive fluids and extreme conditions.
2. Automotive: Tubing forms critical components in vehicle structures, braking systems, fuel lines, and exhaust systems. Lightweight materials such as aluminum and advanced alloys are preferred for fuel efficiency and performance.
3. Aerospace: High-strength, lightweight alloys and composite materials are vital for aircraft and spacecraft structures, hydraulic systems, and fuel lines. Rigorous quality control and testing are essential due to the demanding safety standards.
4. Medical: Biocompatible materials are essential for medical tubing used in catheters, implants, and drug delivery systems. Sterility and biocompatibility are paramount considerations.
5. Construction: Steel and other metal tubing are used extensively in building frameworks, scaffolding, and support structures. Durability, strength, and cost-effectiveness are crucial selection criteria.
Future Trends:
Advancements in materials science and manufacturing technologies continue to shape the future of tubing technology. Key trends include:
-
Additive Manufacturing: 3D printing offers the potential to create highly customized tubes with complex geometries and internal structures.
-
Smart Tubing: Integration of sensors and actuators into tubing enables real-time monitoring of pressure, temperature, and flow rates, enhancing efficiency and safety.
-
Sustainable Materials: The increasing focus on environmental sustainability is driving research into biodegradable and recycled materials for tubing applications.
Conclusion:
Tubing technology is a critical aspect of modern engineering and manufacturing. The ongoing advancements in materials, manufacturing techniques, and applications ensure that tubing will continue to play a vital role in diverse industries for years to come. Its importance spans from supporting our daily lives through infrastructure to enabling groundbreaking innovations in high-tech sectors.
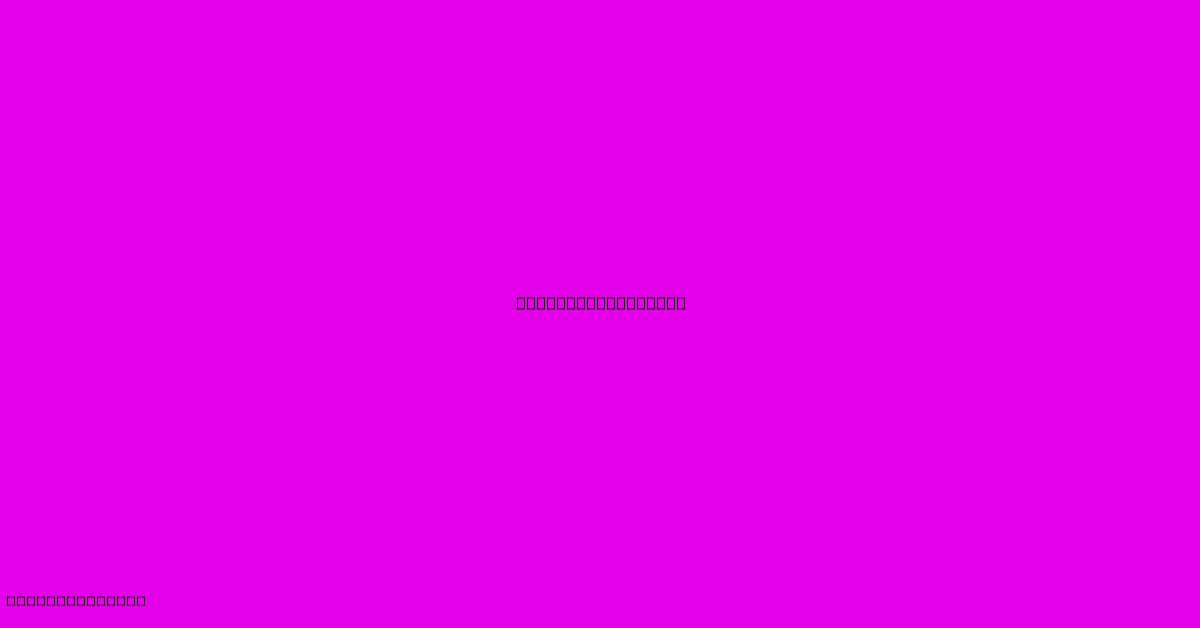
Thank you for visiting our website wich cover about Tubing Technology. We hope the information provided has been useful to you. Feel free to contact us if you have any questions or need further assistance. See you next time and dont miss to bookmark.
Featured Posts
-
Infoworld Technology Of The Year
Dec 21, 2024
-
A A Y A A A A Y A A A Y A A A A Y A A A Y A A A A Y A A A Y A A A A A Y A A A Y A A A A Y A A A Y A A A A Y A A A Y A
Dec 21, 2024
-
Coval Vacuum Technology Inc
Dec 21, 2024
-
Edm Technologies
Dec 21, 2024
-
Maytag Commercial Technology Dryer Not Heating
Dec 21, 2024