Tube Bending Technology
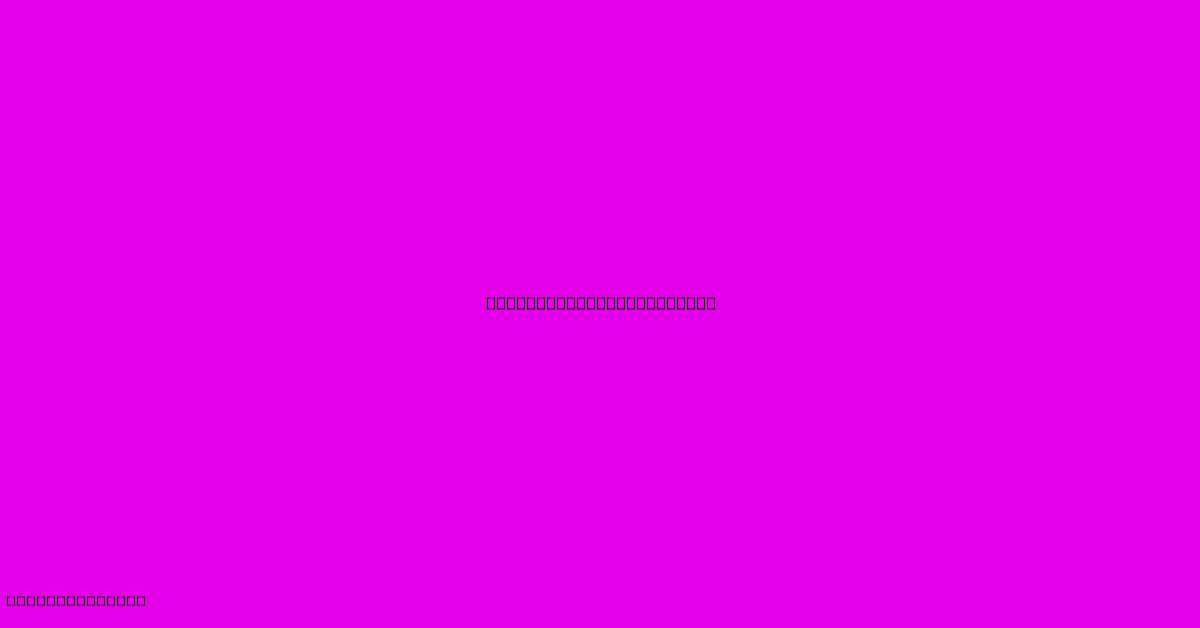
Discover more detailed and exciting information on our website. Click the link below to start your adventure: Visit Best Website mr.cleine.com. Don't miss out!
Table of Contents
Mastering the Bend: A Deep Dive into Tube Bending Technology
Tube bending is a crucial manufacturing process used across numerous industries, from automotive and aerospace to furniture and medical devices. It involves precisely shaping tubular components without compromising their structural integrity or internal diameter. This article explores the diverse technologies involved, their applications, and the factors influencing the selection of the most appropriate method.
Understanding the Fundamentals:
Before diving into specific techniques, let's establish a common understanding. Tube bending is fundamentally about creating a controlled deformation in a tube's material. The goal is to achieve the desired bend radius and angle without causing wrinkles, kinks, or wall thinning – defects that weaken the component and compromise its functionality.
Key Considerations in Tube Bending:
Several factors dictate the choice of bending method:
- Tube Material: The material's properties (e.g., ductility, strength, thickness) significantly impact the bending process and the suitability of different techniques. Steel, aluminum, copper, and stainless steel each require tailored approaches.
- Tube Diameter and Wall Thickness: Larger diameter tubes and those with thicker walls demand more powerful machinery and potentially different bending methods compared to smaller, thinner tubes.
- Bend Radius: The required bend radius influences the selection of the bending method and the tooling involved. Tight radii require specialized techniques to avoid damage.
- Bend Angle: The desired angle of the bend also affects the method chosen, particularly for complex shapes.
- Production Volume: High-volume production often favors automated methods for efficiency, while lower-volume projects might utilize manual or semi-automated techniques.
Common Tube Bending Technologies:
Several methods exist for bending tubes, each offering advantages and disadvantages:
1. Rotary Draw Bending: This is a highly precise and versatile method suitable for both small and large-diameter tubes. A rotating die pulls the tube around a fixed former, creating the desired bend. It's widely used due to its ability to produce tight bends with minimal wall thinning.
2. Roll Bending: Employing three rollers, this method is ideal for bending larger diameter tubes. The rollers progressively deform the tube, generating long, gradual bends. It's often used in applications requiring large radii bends.
3. Push Bending: This technique involves pushing the tube through a die using a mandrel to maintain the internal diameter and prevent wrinkling. It's suitable for creating both tight and large radius bends in various materials.
4. Induction Bending: Utilizing induction heating to locally heat the tube, this method reduces bending forces and improves bend quality. It's particularly beneficial for materials that are difficult to bend at room temperature.
5. Mandrel Bending: A mandrel, a solid tool inserted into the tube, prevents collapsing and ensures a consistent internal diameter during bending. This enhances the overall quality and strength of the bend.
6. CNC Tube Bending: Computer Numerical Control (CNC) technology offers highly precise and automated tube bending. This improves repeatability, consistency, and efficiency, particularly beneficial for high-volume production runs of complex shapes.
Choosing the Right Technology:
The optimal tube bending technology depends on the specific project requirements. Factors like material, dimensions, bend radius, angle, and production volume need careful consideration. Consulting with experienced tube bending professionals can ensure the selection of the most effective and efficient technique.
Future Trends in Tube Bending:
Advancements in materials science and automation technology continue to shape the future of tube bending. Increased use of lightweight materials, demand for greater precision, and the integration of advanced robotics are driving innovation in this critical manufacturing process. We can anticipate further developments in CNC capabilities, advanced simulation software for optimized bending parameters, and increased adoption of sustainable practices in the tube bending industry.
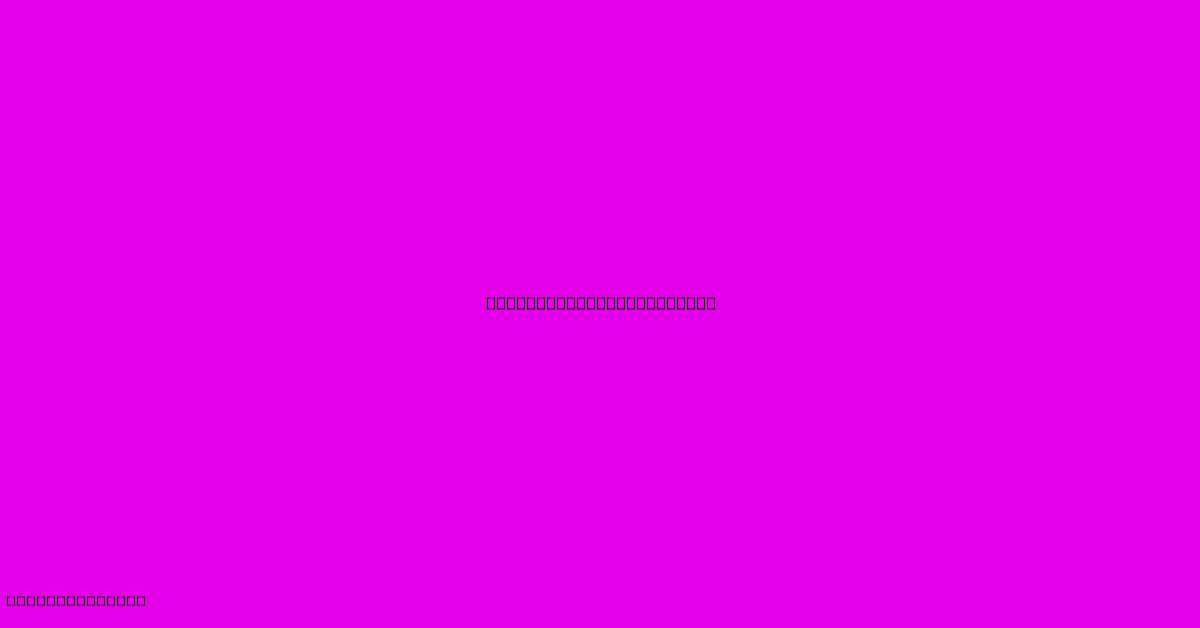
Thank you for visiting our website wich cover about Tube Bending Technology. We hope the information provided has been useful to you. Feel free to contact us if you have any questions or need further assistance. See you next time and dont miss to bookmark.
Featured Posts
-
Technological Effects Of Globalization
Dec 30, 2024
-
Serie A Assista Milan X Roma Online
Dec 30, 2024
-
Mips Technology Helmet
Dec 30, 2024
-
179
Dec 30, 2024
-
Forests 2 0 Everton Victory
Dec 30, 2024