Tpi Technology
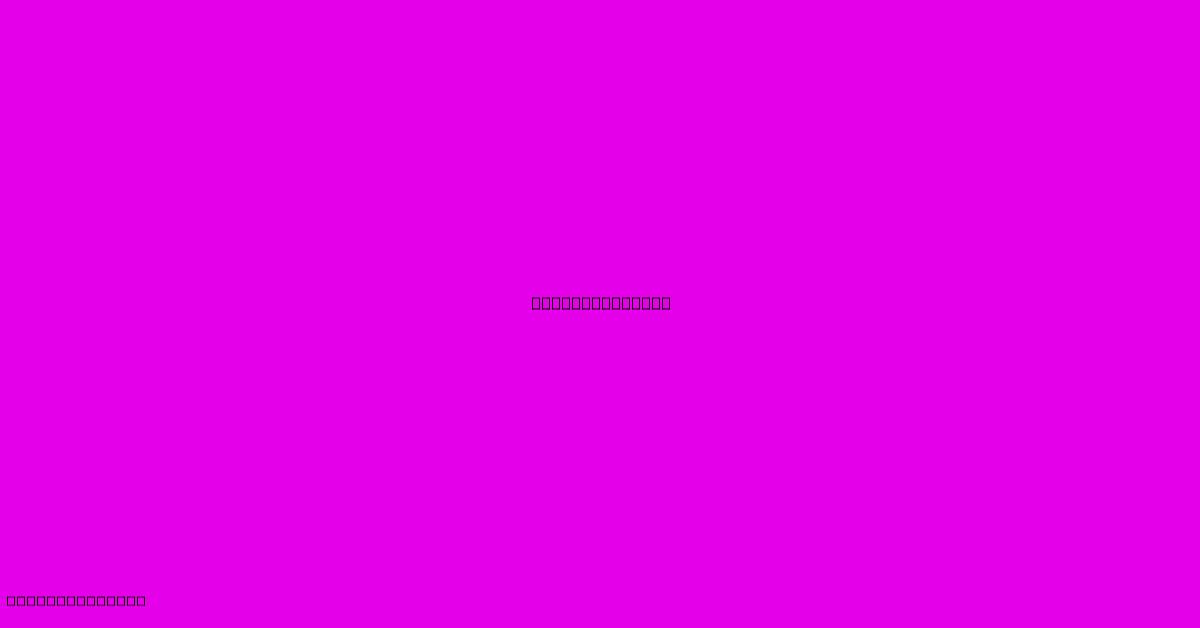
Discover more detailed and exciting information on our website. Click the link below to start your adventure: Visit Best Website mr.cleine.com. Don't miss out!
Table of Contents
TPI Technology: Transforming Industries Through Precision and Innovation
TPI (Thin Plate Insert) technology represents a significant advancement in manufacturing, offering a compelling alternative to traditional machining processes. This innovative approach utilizes thin, precision-engineered metal inserts to create intricate and highly accurate parts. This article delves into the core principles of TPI technology, its applications across various industries, and the advantages it offers over conventional methods.
What is TPI Technology?
TPI technology involves embedding thin, precisely shaped metal inserts into a supporting substrate, typically a polymer or composite material. These inserts, often made from materials like carbide or high-speed steel, provide the cutting edge for machining operations. The substrate acts as a support structure, allowing for complex geometries and increased tool life.
This contrasts sharply with traditional solid carbide tools. TPI tools are significantly lighter and more flexible, resulting in several key benefits:
- Reduced Vibration: The lighter weight minimizes vibration during machining, leading to improved surface finish and accuracy.
- Increased Tool Life: The flexible nature of the substrate helps to absorb shocks and vibrations, extending the life of the inserts.
- Enhanced Machining Capabilities: TPI tools can achieve tighter tolerances and finer surface finishes than traditional methods.
- Cost-Effectiveness: Although the initial investment might seem higher, the extended tool life and reduced downtime translate to significant cost savings in the long run.
Applications Across Industries
TPI technology's versatility has led to its adoption in a wide array of industries:
- Aerospace: The demanding precision requirements of aerospace manufacturing make TPI an ideal choice for producing intricate components with tight tolerances.
- Automotive: In automotive manufacturing, TPI tools help create complex parts for engines, transmissions, and other critical systems.
- Medical Devices: The ability to create highly accurate and intricate medical devices is critical, and TPI technology provides the precision needed.
- Electronics: The miniaturization trend in electronics demands high-precision machining, making TPI technology a valuable tool.
- Energy: From oil and gas to renewable energy sources, TPI technology contributes to the efficient and precise creation of components.
Advantages of TPI Technology Over Traditional Machining
Compared to traditional solid carbide tools, TPI technology offers several key advantages:
- Higher Accuracy and Precision: TPI tools consistently produce parts with superior accuracy and tighter tolerances.
- Improved Surface Finish: Reduced vibration leads to significantly smoother surface finishes.
- Increased Productivity: Longer tool life translates to less downtime and higher productivity.
- Reduced Tool Wear: The flexible substrate absorbs shocks, extending the lifespan of the inserts.
- Better Material Removal Rates: TPI technology often allows for faster material removal rates.
The Future of TPI Technology
TPI technology continues to evolve, with ongoing research and development focusing on:
- New Materials: Exploration of advanced materials for both inserts and substrates.
- Improved Designs: Optimization of insert geometries and substrate configurations.
- Automated Processes: Integration of TPI tools into automated machining systems.
Conclusion
TPI technology has revolutionized various industries by offering a superior approach to precision machining. Its ability to produce highly accurate, high-quality parts with increased efficiency and cost-effectiveness makes it a compelling solution for a wide range of applications. As research and development continue to advance this innovative technology, its impact on manufacturing will only grow in the years to come. The future of manufacturing is increasingly precision-driven, and TPI technology is at the forefront of that evolution.
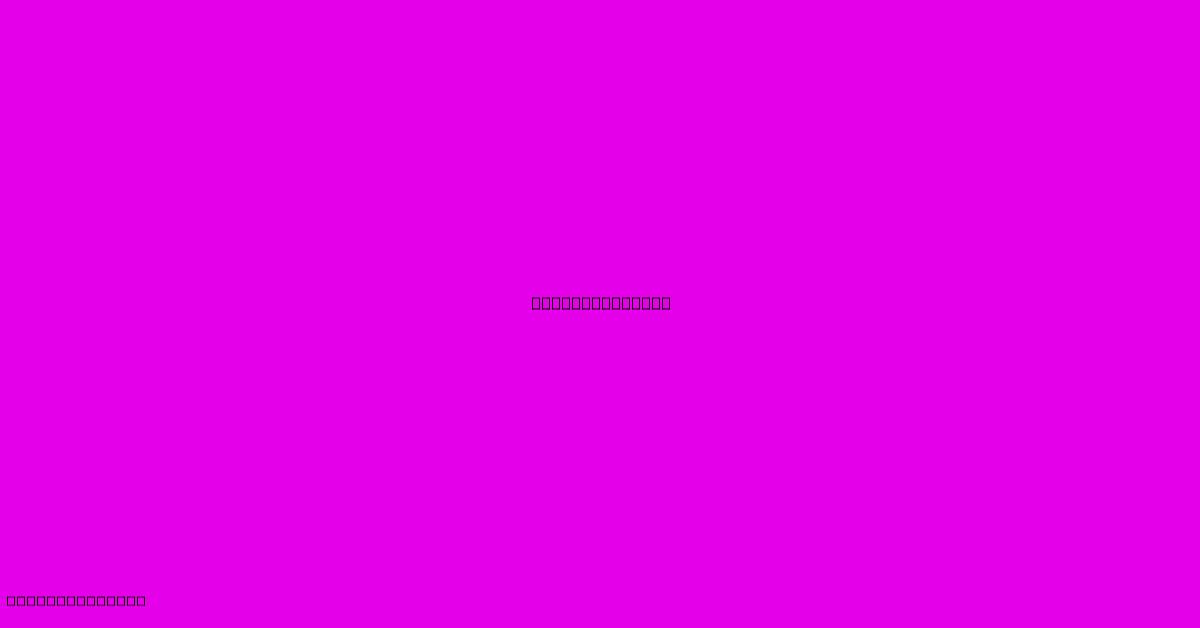
Thank you for visiting our website wich cover about Tpi Technology. We hope the information provided has been useful to you. Feel free to contact us if you have any questions or need further assistance. See you next time and dont miss to bookmark.
Featured Posts
-
Institute Of Police Technology And Management Iptm
Jan 04, 2025
-
Mid America Technology Center Oklahoma
Jan 04, 2025
-
Atex Technologies Inc
Jan 04, 2025
-
Carbon Carbon Advanced Technologies
Jan 04, 2025
-
Wagstaff Inc And Applied Technologies
Jan 04, 2025