Total Tooling Technology
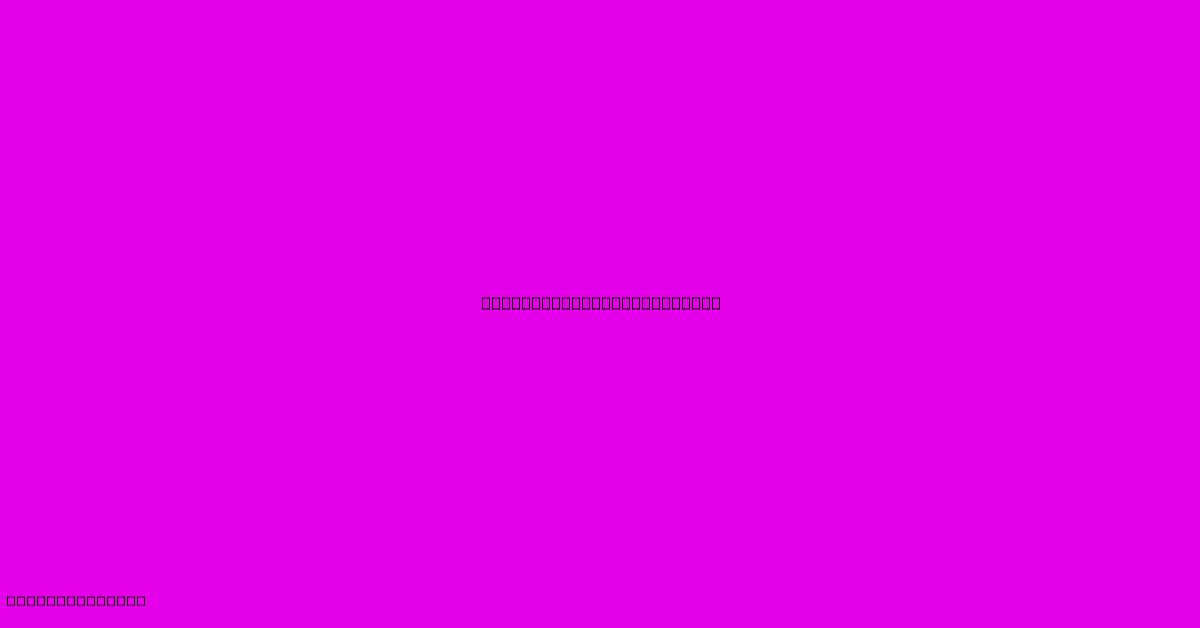
Discover more detailed and exciting information on our website. Click the link below to start your adventure: Visit Best Website mr.cleine.com. Don't miss out!
Table of Contents
Total Tooling Technology: Revolutionizing Manufacturing Efficiency
Total Tooling Technology (TTT) represents a paradigm shift in manufacturing, moving beyond simply providing tools to encompassing a comprehensive, integrated approach to tooling management. This approach significantly impacts efficiency, productivity, and overall profitability. This article delves into the core principles of TTT, its benefits, and how it's reshaping modern manufacturing processes.
What is Total Tooling Technology?
TTT is more than just acquiring and using tools; it's a holistic strategy focused on optimizing the entire lifecycle of tooling, from design and procurement to maintenance, usage, and disposal. It leverages advanced technologies and data-driven insights to improve every aspect of tooling management. Key elements include:
- Advanced Tool Design and Manufacturing: Utilizing technologies like CAD/CAM, simulation software, and advanced materials to create highly efficient and durable tools. This stage focuses on optimizing tool performance and lifespan.
- Intelligent Tool Management Systems: Implementing software solutions that track tool usage, maintenance schedules, and inventory levels in real-time. This provides complete visibility into the tooling process, enabling proactive decision-making.
- Predictive Maintenance: Utilizing data analysis and sensor technology to predict potential tool failures before they occur. This minimizes downtime and prevents costly production interruptions.
- Automated Tooling Processes: Integrating robotic systems and automated guided vehicles (AGVs) to streamline tool handling, changing, and storage. This improves speed, accuracy, and consistency.
- Data Analytics and Reporting: Analyzing collected data to identify areas for improvement, optimize tool performance, and reduce waste. This data-driven approach continually refines the tooling process.
Benefits of Implementing Total Tooling Technology
Adopting TTT offers significant advantages across various aspects of manufacturing:
- Increased Productivity: Streamlined processes and reduced downtime lead to higher production output.
- Improved Quality: Precise tool management and maintenance ensure consistent product quality.
- Reduced Costs: Minimized waste, extended tool life, and fewer production interruptions translate into significant cost savings.
- Enhanced Safety: Automated processes and predictive maintenance reduce the risk of workplace accidents.
- Better Inventory Management: Real-time tracking and optimized inventory levels minimize storage costs and prevent shortages.
- Data-Driven Decision Making: Access to detailed data facilitates informed decisions regarding tool selection, maintenance, and overall process optimization.
Implementing Total Tooling Technology: A Step-by-Step Approach
Implementing TTT requires a structured approach:
- Assessment: Evaluate current tooling practices, identifying areas for improvement and potential bottlenecks.
- Planning: Develop a comprehensive plan outlining goals, timelines, and resource allocation.
- Technology Selection: Choose appropriate software and hardware solutions that align with specific needs.
- Implementation: Introduce new technologies and processes gradually, ensuring proper training for personnel.
- Monitoring and Optimization: Continuously monitor performance, collect data, and make adjustments to refine the system.
The Future of Total Tooling Technology
The future of TTT is closely linked to advancements in digital technologies like:
- Artificial Intelligence (AI): AI-powered systems can analyze vast amounts of data to predict tool failures with greater accuracy and optimize tool designs.
- Internet of Things (IoT): Connected tools and sensors provide real-time data, enabling proactive maintenance and improved decision-making.
- Digital Twins: Creating virtual representations of tools and processes allows for simulations and optimization before implementation.
Conclusion:
Total Tooling Technology represents a fundamental shift in how manufacturers manage their tooling resources. By embracing a comprehensive, data-driven approach, companies can dramatically improve efficiency, reduce costs, and enhance the overall quality of their products. The future of manufacturing lies in leveraging these advanced technologies to achieve greater levels of productivity and competitiveness.
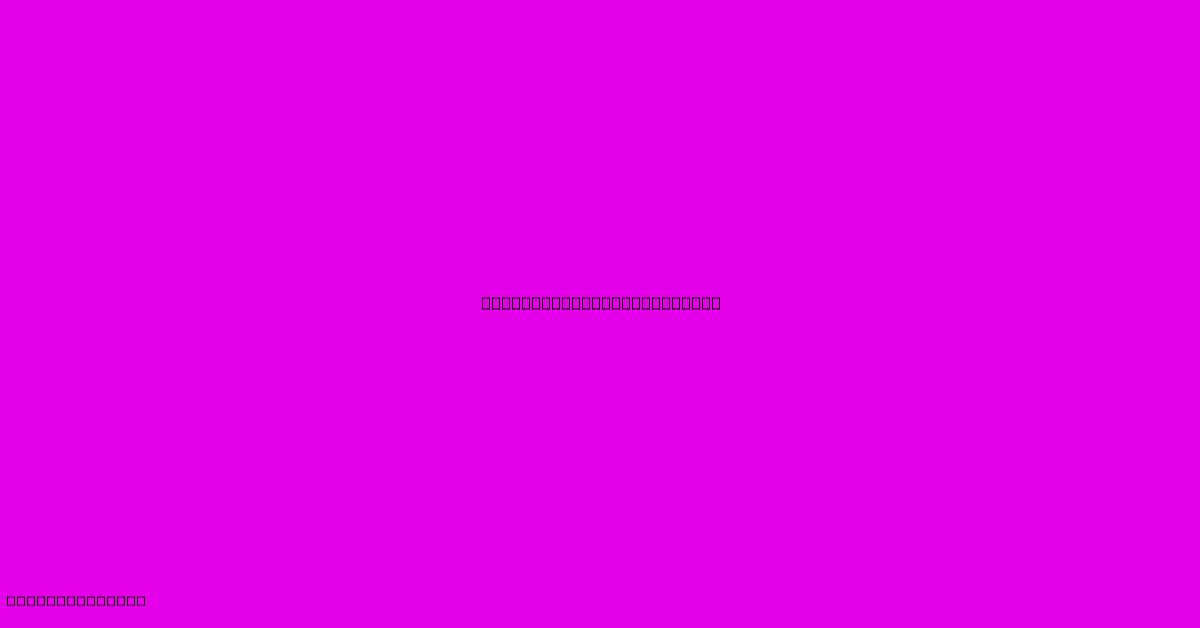
Thank you for visiting our website wich cover about Total Tooling Technology. We hope the information provided has been useful to you. Feel free to contact us if you have any questions or need further assistance. See you next time and dont miss to bookmark.
Featured Posts
-
Keeping Nfl Fans Netflixs Plan
Dec 26, 2024
-
Boxing Day Regina Family Activities 2024
Dec 26, 2024
-
Boxing Day Test 2024 Kohlis Performance Questioned
Dec 26, 2024
-
Technological Stagnation
Dec 26, 2024
-
Nosferatu Review Eggers Dracula
Dec 26, 2024