Technology Of Machine Tools
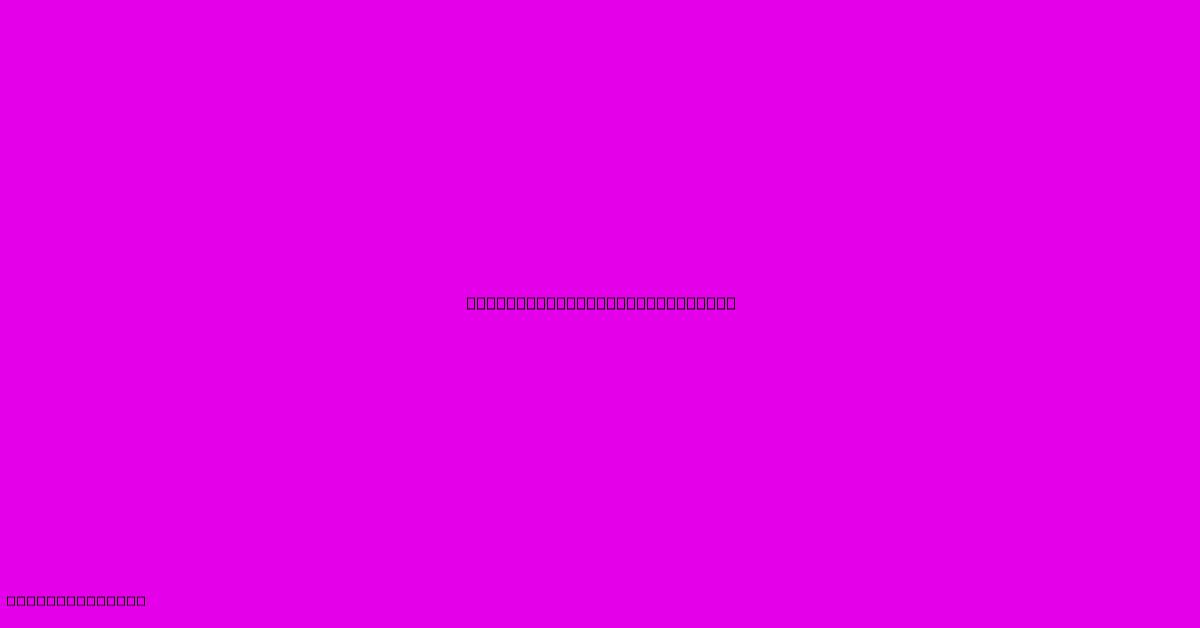
Discover more detailed and exciting information on our website. Click the link below to start your adventure: Visit Best Website mr.cleine.com. Don't miss out!
Table of Contents
The Technology of Machine Tools: A Deep Dive into Precision and Automation
The world of manufacturing relies heavily on machine tools – sophisticated machines that shape raw materials into precise components. From the intricate gears of a watch to the robust chassis of a car, machine tools are the backbone of modern industry. Understanding their technology is crucial for anyone involved in engineering, manufacturing, or even simply appreciating the complexities of modern production. This article will delve into the core technologies that drive these powerful instruments.
I. Core Principles of Machine Tool Technology:
Machine tools operate on fundamental mechanical principles, leveraging controlled movements to remove material from a workpiece. These principles are often combined and refined to achieve specific manufacturing goals.
-
Material Removal: This is the primary function. Methods include turning (removing material from a rotating workpiece), milling (using rotating cutters to shape a stationary workpiece), drilling (creating holes), grinding (using abrasive materials for fine finishing), and many others.
-
Precise Movement: Accuracy is paramount. Machine tools employ various mechanisms to achieve precise linear and rotational movements, often guided by numerical control (NC) systems. These systems translate digital instructions into precise movements, enabling the creation of complex shapes with micron-level accuracy.
-
Tooling: The tools used are specialized for different materials and operations. Cutting tools (drills, mills, lathes) are made from high-speed steel (HSS), carbide, or even diamond, depending on the material being processed and the desired finish.
-
Workholding: Securely holding the workpiece is vital for accuracy and safety. Chucks, vises, and fixtures are employed to hold workpieces in place during machining.
II. Evolution of Machine Tool Technology:
The technology of machine tools has dramatically evolved, progressing through several key stages:
-
Manual Machine Tools: Early machine tools were manually operated, requiring skilled machinists to control all movements. While simple, they were limited in speed and precision.
-
Numerical Control (NC) Machine Tools: The introduction of NC programming revolutionized the industry. NC machines use pre-programmed instructions to control their movements, significantly increasing efficiency and accuracy. This allowed for complex shapes and high-volume production.
-
Computer Numerical Control (CNC) Machine Tools: CNC machines represent a further advancement, utilizing computer processing power to interpret and execute NC programs. CNC machines offer enhanced flexibility, programmability, and monitoring capabilities. They often incorporate sophisticated features like closed-loop control systems for enhanced precision.
-
Adaptive Control Machine Tools: These advanced machines adapt their operations in real-time based on sensor feedback. This allows for consistent machining despite variations in material properties or tool wear, resulting in improved quality and efficiency.
-
Direct Numerical Control (DNC) Machine Tools: DNC systems link multiple CNC machines to a central computer, allowing for centralized control and data management across an entire manufacturing facility.
III. Key Technologies in Modern Machine Tools:
Modern machine tools are characterized by sophisticated technologies aimed at enhancing precision, efficiency, and automation:
-
Advanced Control Systems: These systems employ sophisticated algorithms and feedback loops to optimize machine performance and compensate for errors.
-
High-Speed Machining (HSM): HSM techniques use higher cutting speeds and feeds, significantly reducing machining time. This requires robust machine structures and specialized tooling.
-
Sensor Technology: Sensors monitor various parameters like tool wear, cutting forces, and temperature, enabling real-time adjustments and preventing issues.
-
Automation and Robotics: Robotics and automation systems integrate seamlessly with machine tools to automate material handling, loading/unloading, and other tasks, increasing productivity.
-
Computer-Aided Manufacturing (CAM): CAM software plays a crucial role in generating the NC programs that control the machine tools. CAM software simulates machining processes, allowing for optimization and error detection before actual production.
IV. The Future of Machine Tool Technology:
The future of machine tools involves further advancements in:
-
Artificial Intelligence (AI): AI and machine learning algorithms will play an increasingly important role in optimizing machine parameters, predicting failures, and enhancing overall performance.
-
Additive Manufacturing (3D Printing): While different from subtractive machining, additive manufacturing is becoming increasingly integrated with traditional machine tools to create hybrid manufacturing processes.
-
Internet of Things (IoT): Connecting machine tools through the IoT allows for real-time monitoring, predictive maintenance, and remote diagnostics.
In conclusion, the technology of machine tools is a complex and constantly evolving field. The ongoing development of new materials, control systems, and automation techniques continues to push the boundaries of precision, efficiency, and productivity in manufacturing across various industries. Understanding the fundamentals of this technology is crucial for anyone seeking to innovate and advance in the world of modern manufacturing.
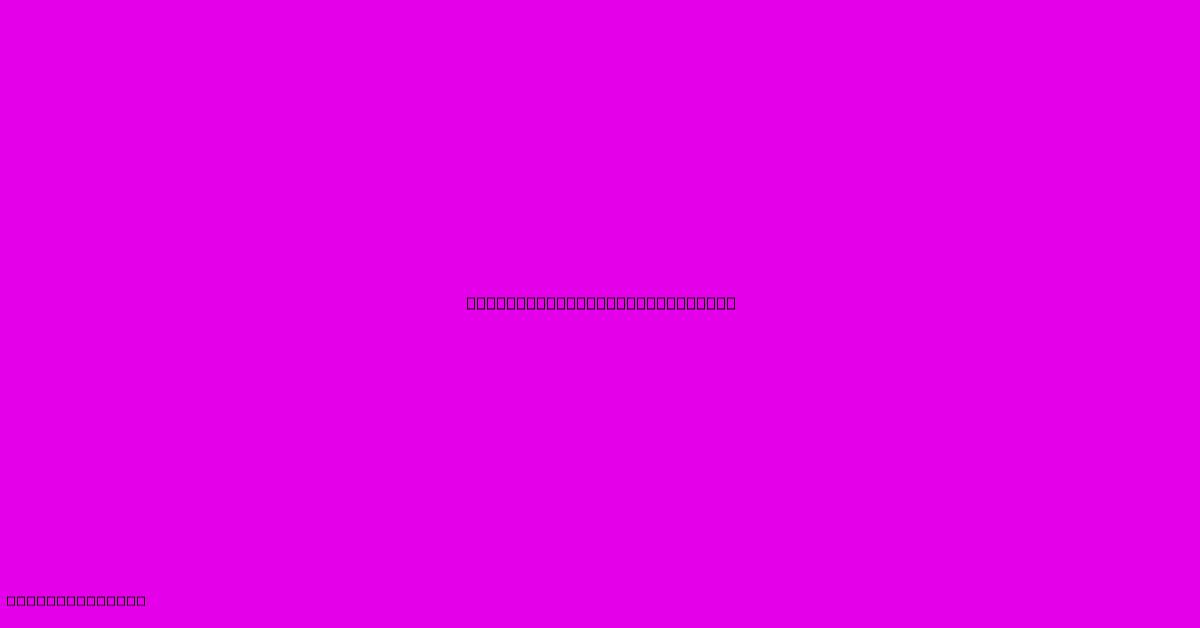
Thank you for visiting our website wich cover about Technology Of Machine Tools. We hope the information provided has been useful to you. Feel free to contact us if you have any questions or need further assistance. See you next time and dont miss to bookmark.
Featured Posts
-
Wetterwarnung Bremen Kein Feuerwerk An Silvester
Jan 01, 2025
-
New Years Eve London Firework Show
Jan 01, 2025
-
Florida Rs Technology
Jan 01, 2025
-
Anp Technologies
Jan 01, 2025
-
Nussmeier Leads Lsu Against Baylor
Jan 01, 2025