Technology In Welding
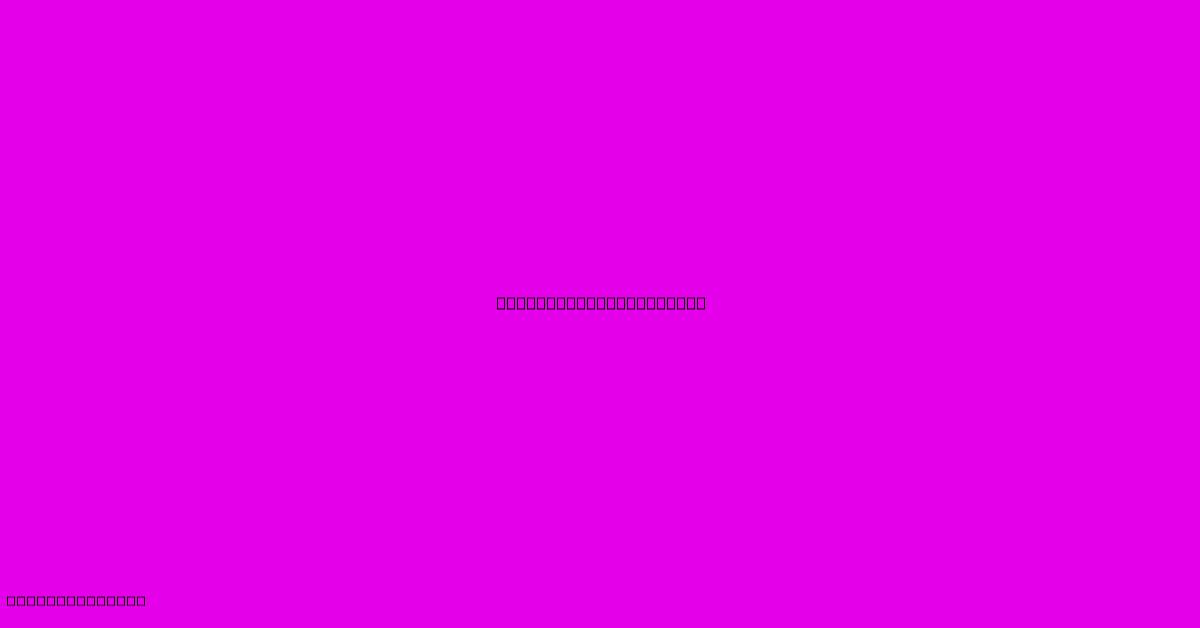
Discover more detailed and exciting information on our website. Click the link below to start your adventure: Visit Best Website mr.cleine.com. Don't miss out!
Table of Contents
Revolutionizing the Weld: How Technology is Transforming the Welding Industry
Welding, a process as old as civilization itself, is undergoing a dramatic transformation thanks to advancements in technology. From the humble arc welder to sophisticated robotic systems, technological innovation is enhancing efficiency, precision, and safety within the welding industry. This article delves into the key technological advancements reshaping how we weld.
1. Robotic Welding: Precision and Efficiency Redefined
Robotic welding systems have revolutionized manufacturing and production lines. These automated systems offer unparalleled precision and repeatability, consistently producing high-quality welds with minimal variation.
Advantages of Robotic Welding:
- Increased Speed and Efficiency: Robots can work continuously without breaks, significantly increasing production rates compared to manual welding.
- Improved Consistency and Quality: Robotic welds are remarkably consistent, minimizing defects and reducing the need for rework.
- Enhanced Safety: Robots handle dangerous tasks, protecting human welders from hazardous environments and potential injuries.
- Complex Weld Applications: Robots can handle intricate and complex weld geometries that would be difficult or impossible for human welders.
Types of Robotic Welding:
- Arc Welding: The most common type, using robotic arms to manipulate welding torches.
- Laser Welding: Precise and high-speed welding using laser beams.
- Resistance Spot Welding: Used for joining sheet metal parts, ideal for automotive manufacturing.
2. Advanced Welding Processes: Beyond Traditional Methods
Modern welding techniques go beyond the traditional methods. New processes leverage advanced technologies to improve weld quality, efficiency, and material compatibility.
Examples of Advanced Welding Processes:
- Friction Stir Welding (FSW): A solid-state welding process that creates strong joints without melting the base materials. Ideal for joining difficult-to-weld metals like aluminum.
- Laser Beam Welding (LBW): Offers excellent precision and depth of penetration, suitable for applications requiring high-quality welds in thin materials.
- Electron Beam Welding (EBW): A high-vacuum process creating deep and narrow welds with exceptional penetration and minimal heat-affected zones. Used in high-precision aerospace and medical applications.
- Plasma Arc Welding (PAW): Utilizes a high-velocity plasma arc to produce deep and narrow welds, with superior control compared to traditional arc welding.
3. Sensor Technology and Data Analytics: Optimizing the Welding Process
Sensors and data analytics are becoming integral to modern welding. Sensors monitor various parameters during the welding process, providing real-time feedback and data that can be analyzed to optimize weld quality and efficiency.
Applications of Sensor Technology:
- Weld Pool Monitoring: Sensors track the size and shape of the weld pool, providing crucial information for process control.
- Temperature Measurement: Accurate temperature monitoring helps prevent defects and ensures proper weld formation.
- Real-Time Data Analysis: Sophisticated software analyzes data collected by sensors, identifying potential problems and optimizing the welding process.
- Predictive Maintenance: Data analytics helps predict potential equipment failures, allowing for timely maintenance and reducing downtime.
4. Augmented and Virtual Reality (AR/VR): Training and Design Enhancements
AR/VR technologies are changing how welders are trained and how welding designs are developed. AR overlays can guide welders during complex welds, while VR simulations provide realistic training environments without the risks associated with real-world welding.
Benefits of AR/VR in Welding:
- Improved Training Efficiency: VR simulations provide a safe and repeatable environment for welder training.
- Enhanced Design Visualization: AR and VR allow engineers to visualize weld designs before production, improving efficiency and reducing errors.
- Remote Collaboration: AR/VR technologies facilitate remote collaboration between welders and engineers.
5. The Future of Welding Technology: A Look Ahead
The welding industry is poised for continued technological advancement. We can expect further integration of AI and machine learning, leading to more autonomous and adaptive welding systems. Additive manufacturing (3D printing) is also significantly impacting the industry, allowing for the creation of complex parts with intricate welds. The future of welding will be defined by increased automation, greater precision, enhanced safety, and unprecedented levels of efficiency.
The integration of these technologies is not merely enhancing the speed and efficiency of welding; it's fundamentally altering the skillset required, improving safety protocols, and driving innovation across diverse industries. The future of welding is bright, and it's driven by the relentless pursuit of technological advancement.
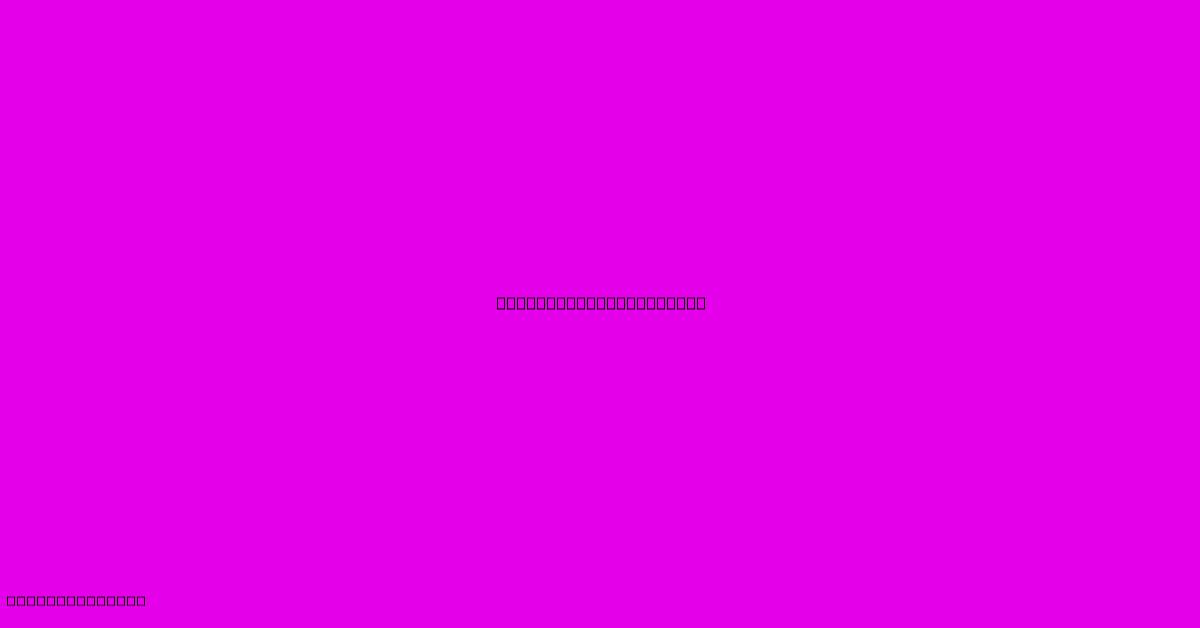
Thank you for visiting our website wich cover about Technology In Welding. We hope the information provided has been useful to you. Feel free to contact us if you have any questions or need further assistance. See you next time and dont miss to bookmark.
Featured Posts
-
Advances In Hip Replacement Technology
Jan 04, 2025
-
Endrun Technologies
Jan 04, 2025
-
Applied Signal Technology Raytheon
Jan 04, 2025
-
Alvin Sherman Library Research And Information Technology Center
Jan 04, 2025
-
United Technologies Benefits
Jan 04, 2025