Surface Mount Technology Vs. Through Hole
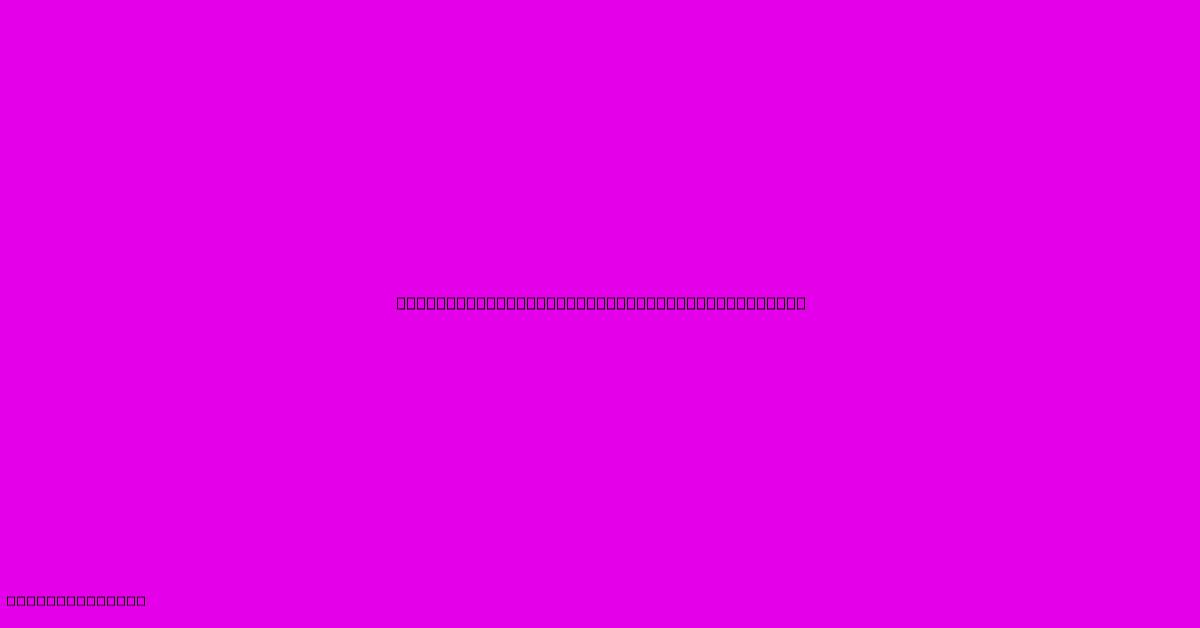
Discover more detailed and exciting information on our website. Click the link below to start your adventure: Visit Best Website mr.cleine.com. Don't miss out!
Table of Contents
Surface Mount Technology (SMT) vs. Through-Hole Technology (THT): A Comprehensive Comparison
Choosing the right technology for your electronic circuit board can significantly impact its performance, cost, and size. Two dominant methods stand out: Surface Mount Technology (SMT) and Through-Hole Technology (THT). This article delves into the key differences, advantages, and disadvantages of each, helping you make an informed decision.
Understanding Surface Mount Technology (SMT)
SMT involves mounting electronic components directly onto the surface of a printed circuit board (PCB). These components, often smaller than their through-hole counterparts, have leads or terminals that are soldered directly to pads on the PCB's surface.
Advantages of SMT:
- Miniaturization: SMT allows for significantly smaller and more compact PCBs, ideal for portable devices and space-constrained applications.
- Higher Component Density: More components can be fitted onto a given PCB area, leading to reduced overall size and cost.
- Automated Assembly: SMT is highly automated, resulting in faster and more efficient production processes, especially for high-volume manufacturing.
- Lower Profile: The components sit flush against the PCB, resulting in a lower profile, beneficial for applications where height is a constraint.
- Improved High-Frequency Performance: The shorter leads and connections reduce parasitic inductance and capacitance, leading to better performance at higher frequencies.
Disadvantages of SMT:
- Higher Initial Investment: The equipment required for SMT assembly is expensive, making it less cost-effective for low-volume projects.
- Soldering Challenges: SMT soldering requires precise temperature control and specialized equipment to avoid damaging sensitive components.
- Component Repair/Replacement: Repairing or replacing individual components on an SMT board is more challenging and often requires specialized tools and expertise.
- Component Size Limitations: While offering miniaturization, there are limitations on the size and power handling capacity of components that can be effectively surface mounted.
- Sensitivity to Mechanical Stress: SMT components are more susceptible to damage from mechanical stress and vibration.
Understanding Through-Hole Technology (THT)
THT, the traditional method, uses components with leads that pass through holes in the PCB. These leads are then soldered on the opposite side of the board, securing the component in place.
Advantages of THT:
- Lower Initial Investment: The equipment required for THT assembly is relatively inexpensive, making it a more accessible option for smaller projects and prototyping.
- Easier Component Repair/Replacement: Individual components are easier to repair or replace on a THT board, using simpler tools and techniques.
- Robustness: THT components are generally more robust and less susceptible to mechanical stress and vibration.
- Higher Power Handling: Larger components, capable of handling higher power levels, are typically easier to implement using THT.
- Simpler Soldering: THT soldering is generally simpler and less demanding, requiring less specialized equipment.
Disadvantages of THT:
- Larger PCB Size: THT leads require larger holes and spacing between components, resulting in larger PCBs.
- Lower Component Density: Fewer components can be placed on a given board area, compared to SMT.
- Slower Production: Manual assembly is common with THT, leading to slower and less efficient production processes.
- Higher Profile: The leads extending through the board result in a higher profile, which can be a limitation in some applications.
- Higher Parasitic Inductance: Longer leads introduce more parasitic inductance and capacitance, potentially affecting high-frequency performance.
Choosing Between SMT and THT:
The choice between SMT and THT depends on several factors, including:
- Production Volume: High-volume production favors SMT due to its automation capabilities. Low-volume production might be more suited for THT.
- Budget: The initial investment in equipment is a crucial consideration.
- Product Size and Weight: Applications requiring miniaturization benefit from SMT.
- Component Size and Power Requirements: High-power applications might necessitate THT.
- Repair and Maintainability: Ease of repair is often a key factor for some applications.
- Frequency Performance: High-frequency applications benefit from the lower parasitic components of SMT.
In many modern designs, a combination of SMT and THT is employed, leveraging the advantages of both technologies to achieve optimal results. The final decision hinges on a careful evaluation of your specific project requirements and constraints.
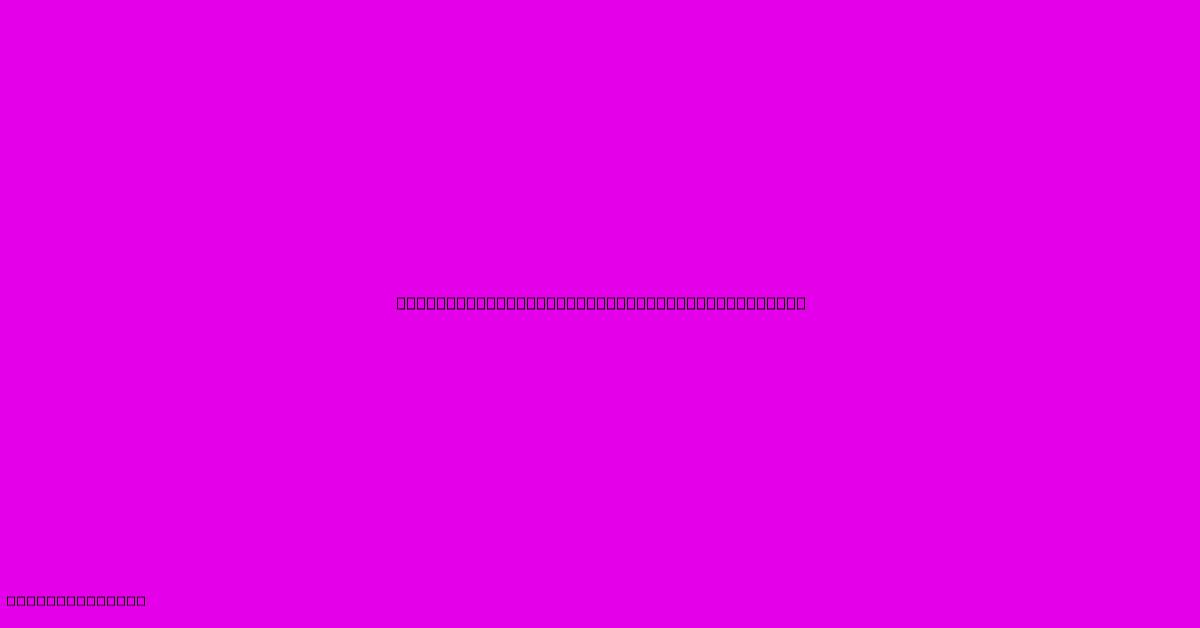
Thank you for visiting our website wich cover about Surface Mount Technology Vs. Through Hole. We hope the information provided has been useful to you. Feel free to contact us if you have any questions or need further assistance. See you next time and dont miss to bookmark.
Featured Posts
-
Team Technologies
Jan 05, 2025
-
Anti Counterfeiting Technology
Jan 05, 2025
-
Omega Digital Technologies
Jan 05, 2025
-
Fashion Institute Of Technology Transfer
Jan 05, 2025
-
Certified Space Technology
Jan 05, 2025