Surface Mount Technology Assembly
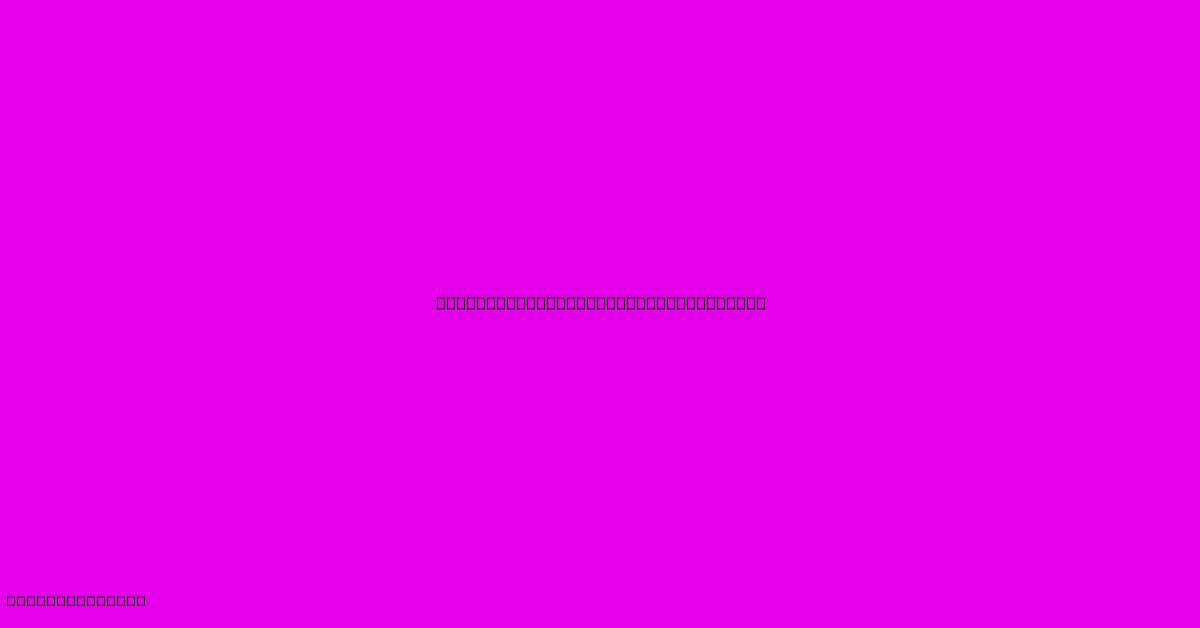
Discover more detailed and exciting information on our website. Click the link below to start your adventure: Visit Best Website mr.cleine.com. Don't miss out!
Table of Contents
Surface Mount Technology (SMT) Assembly: A Comprehensive Guide
Surface Mount Technology (SMT) has revolutionized electronics manufacturing, enabling smaller, lighter, and more efficient devices. This comprehensive guide will explore the intricacies of SMT assembly, covering its advantages, processes, and challenges.
What is Surface Mount Technology (SMT)?
SMT is a method of assembling electronic components directly onto the surface of printed circuit boards (PCBs). Unlike through-hole technology (THT), where components are inserted into holes drilled in the board, SMT components are placed on the surface and soldered. This significantly reduces the size and weight of electronic devices, improves performance, and enhances manufacturing efficiency.
Advantages of SMT Assembly:
- Miniaturization: SMT allows for smaller component sizes, leading to smaller and more compact devices.
- Higher Density: More components can be fitted onto a PCB of the same size compared to THT.
- Reduced Weight: Lighter devices are achieved due to smaller components and less material usage.
- Improved Performance: Smaller components often have better performance characteristics and reduced parasitic capacitance and inductance.
- Increased Speed: Automated assembly processes significantly speed up manufacturing.
- Lower Cost (in many cases): While initial investment in SMT equipment can be high, automation often leads to lower per-unit costs for high-volume production.
- Enhanced Reliability: SMT joints often exhibit higher reliability compared to THT joints, especially with proper reflow soldering.
The SMT Assembly Process:
The SMT assembly process typically involves the following stages:
1. PCB Preparation: The PCB is inspected for defects and cleaned to ensure proper adhesion.
2. Stencil Printing: A stencil (thin metal sheet with precisely cut apertures) is placed on the PCB, and solder paste is applied through the apertures using a squeegee. This process deposits the correct amount of solder paste onto the PCB pads where the components will be placed.
3. Component Placement: Automated placement machines pick and place surface mount components onto the solder paste on the PCB. High-speed vision systems ensure accurate placement.
4. Reflow Soldering: The PCB is passed through a reflow oven, where the solder paste melts and creates solder joints between the components and the PCB pads. The temperature profile in the oven is critical for creating strong and reliable joints.
5. Inspection: Automated optical inspection (AOI) systems verify the quality of the solder joints and component placement. X-ray inspection is sometimes used to detect hidden defects.
6. Cleaning (optional): The PCB may be cleaned to remove any residual flux from the soldering process.
Challenges in SMT Assembly:
- Component Size: Handling extremely small components requires precise equipment and careful process control.
- Solder Paste Management: Controlling the viscosity and printing of solder paste is critical for reliable joints.
- Temperature Control: Precise control of the reflow oven temperature profile is crucial for optimal solder joint formation.
- Inspection and Testing: Detecting defects in increasingly complex PCBs requires advanced inspection technologies.
- Material Compatibility: Different materials used in components and the PCB must be compatible to prevent issues like delamination or solder bridging.
Conclusion:
Surface Mount Technology (SMT) is a critical enabler of modern electronics manufacturing, delivering significant advantages in size, weight, performance, and cost. Understanding the process and its challenges is crucial for anyone involved in the design, manufacturing, or testing of electronic devices. The ongoing advancements in SMT technology promise even smaller, faster, and more reliable electronic products in the future.
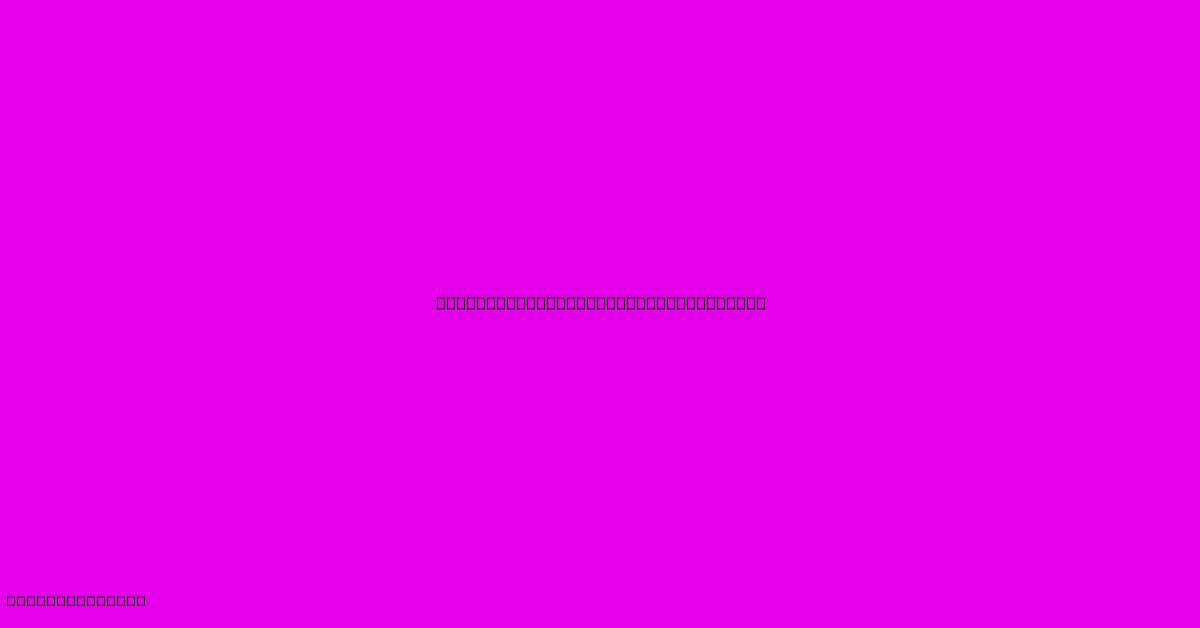
Thank you for visiting our website wich cover about Surface Mount Technology Assembly. We hope the information provided has been useful to you. Feel free to contact us if you have any questions or need further assistance. See you next time and dont miss to bookmark.
Featured Posts
-
University Of Technology Baghdad
Dec 28, 2024
-
Leicester City Vs Liverpool Live Score
Dec 28, 2024
-
Premier League Score Liverpool Leicester
Dec 28, 2024
-
Mercato Fofana De Retour En France
Dec 28, 2024
-
Hasil Bri Liga 1 Persija Menang Atas Malut
Dec 28, 2024