Surface Finish Technologies
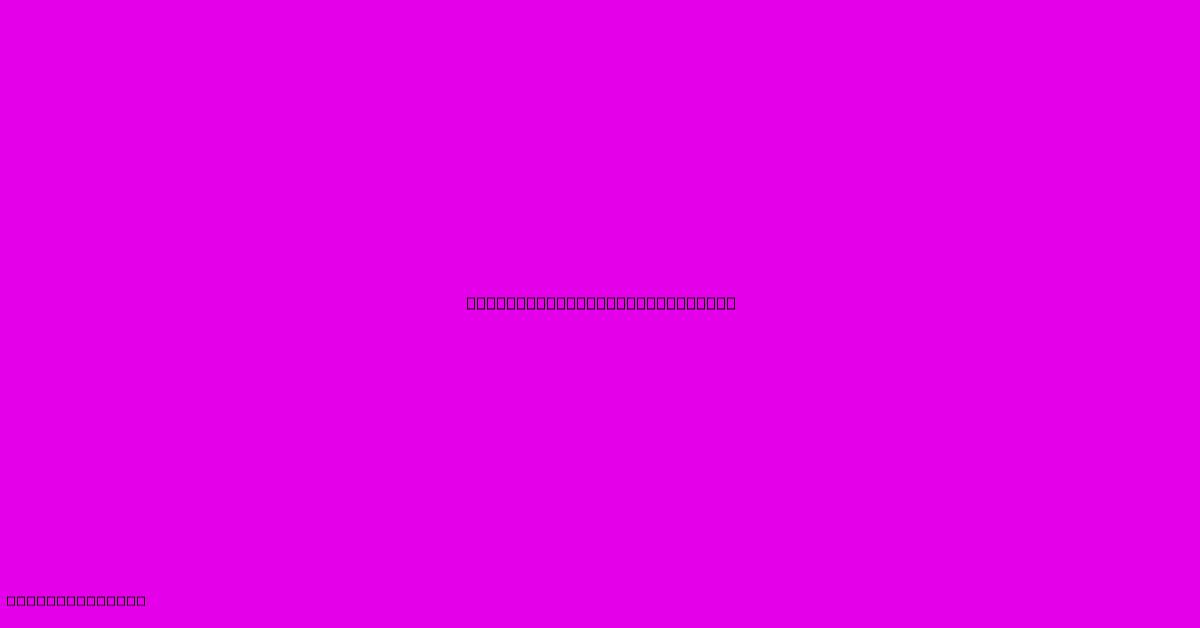
Discover more detailed and exciting information on our website. Click the link below to start your adventure: Visit Best Website mr.cleine.com. Don't miss out!
Table of Contents
Mastering Surface Finish Technologies: A Comprehensive Guide
Surface finish, the final layer of a manufactured component, significantly impacts its performance, lifespan, and aesthetic appeal. Understanding and controlling surface finish technologies is crucial across numerous industries, from aerospace and automotive to medical devices and consumer electronics. This comprehensive guide explores the key aspects of surface finish technologies, delving into various methods, their applications, and the factors influencing their selection.
What is Surface Finish?
Surface finish refers to the texture and characteristics of a component's outermost layer. It's defined by various parameters including roughness (Ra, Rz), waviness, and lay. These parameters affect crucial properties like:
- Friction and Wear: Smooth surfaces reduce friction, leading to enhanced efficiency and extended component life.
- Corrosion Resistance: Proper surface finish can significantly improve corrosion resistance, protecting against environmental degradation.
- Aesthetics: The visual appeal of a product is heavily influenced by its surface finish, impacting consumer perception and market value.
- Fatigue Strength: Surface imperfections can act as stress concentrators, potentially reducing the fatigue strength of a component.
- Bonding and Adhesion: Surface treatments often prepare surfaces for better adhesion of coatings or joining processes.
Common Surface Finish Technologies:
Numerous techniques are employed to achieve desired surface finishes. They can be broadly categorized as mechanical, chemical, electrochemical, or thermal processes.
1. Mechanical Processes:
- Machining: Processes like turning, milling, grinding, and honing use cutting tools to remove material, providing various levels of surface roughness. The choice of cutting tool, feed rate, and depth of cut significantly influence the final finish.
- Grinding: A high-precision abrasive process, used to achieve very fine surface finishes and high dimensional accuracy.
- Polishing: A finishing process using fine abrasives to achieve highly smooth, reflective surfaces. This is often employed for aesthetic purposes or where extremely low friction is required.
- Honing: Uses abrasive stones or hones to refine the surface finish after machining, achieving superior dimensional accuracy and surface smoothness.
- Lapping: A very precise finishing process that uses very fine abrasives to create extremely smooth, flat surfaces. Often used for optical components or precision engineering parts.
2. Chemical Processes:
- Chemical Etching: Uses chemical solutions to selectively remove material from the surface, producing textured or patterned finishes. Often used for micromachining or creating decorative effects.
- Chemical Milling: A subtractive process removing material from a surface using chemical etchants. This technique is widely used in aerospace and automotive industries.
3. Electrochemical Processes:
- Electroplating: A process where a thin layer of metal is deposited onto a surface using an electric current. This enhances corrosion resistance, wear resistance, and aesthetics.
- Electropolishing: An electrochemical process that removes surface irregularities, resulting in a highly polished and smooth finish. Often used for medical implants and high-precision parts.
- Anodizing: An electrochemical process that creates a protective oxide layer on the surface of metals, particularly aluminum. This improves corrosion resistance, durability, and aesthetic qualities.
4. Thermal Processes:
- Shot Peening: A process that bombards the surface with small metallic shot, creating compressive residual stresses. This increases fatigue strength and corrosion resistance.
Selecting the Right Surface Finish Technology:
The optimal surface finish technology depends on several factors:
- Material Properties: The material's machinability, susceptibility to corrosion, and other properties influence the choice of process.
- Desired Finish: The required surface roughness, waviness, and lay dictate the selection of a specific technique.
- Cost: Different processes have varying costs, influencing the final decision.
- Production Volume: High-volume production may favor automated processes, while low-volume production may allow for more specialized techniques.
- Environmental Impact: The environmental impact of each process should be considered for sustainable manufacturing practices.
Conclusion:
Mastering surface finish technologies is crucial for achieving optimal performance and longevity in various applications. Understanding the different techniques, their advantages, limitations, and the influencing factors is essential for engineers and manufacturers. The selection of the right process is a critical step in ensuring high-quality products and meeting specific performance requirements. Continuous advancements in surface finish technologies promise even greater precision, efficiency, and sustainability in the future.
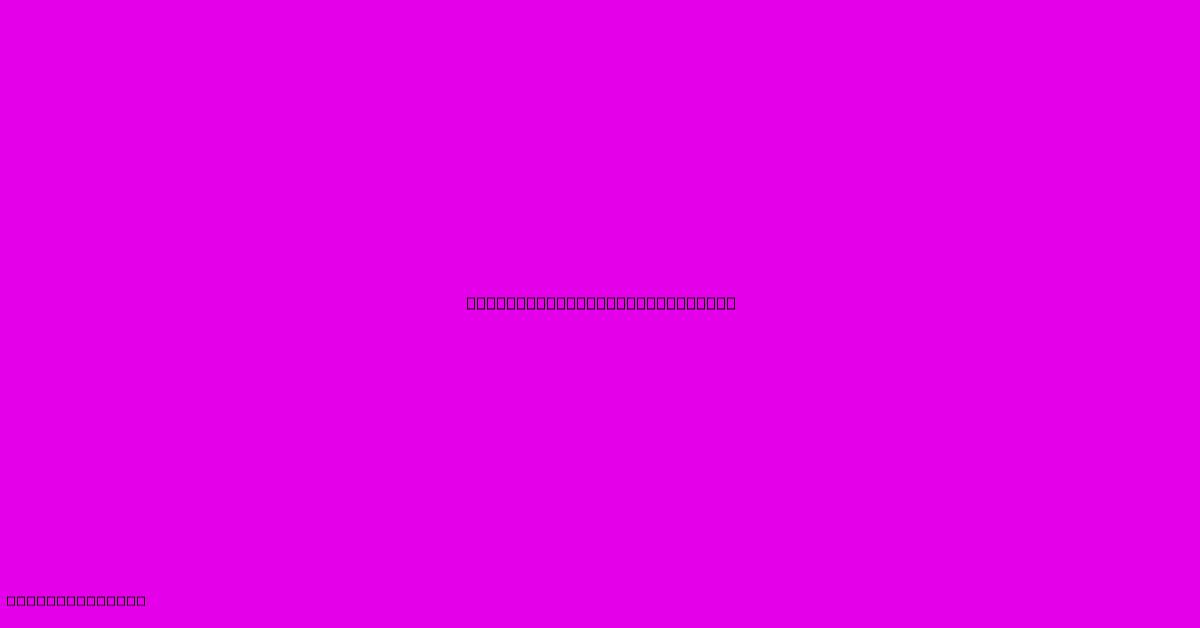
Thank you for visiting our website wich cover about Surface Finish Technologies. We hope the information provided has been useful to you. Feel free to contact us if you have any questions or need further assistance. See you next time and dont miss to bookmark.
Featured Posts
-
Johansson Reacts To Josts Jokes Live
Dec 23, 2024
-
Diaz And Salah Liverpools 6 Goal Victory
Dec 23, 2024
-
Lideranca Em Risco Sporting Empata
Dec 23, 2024
-
Eastern Institute Of Technology Napier
Dec 23, 2024
-
Jornada 18 Liga Resumen Madrid Vs Sevilla
Dec 23, 2024