Subsea Coating Technologies
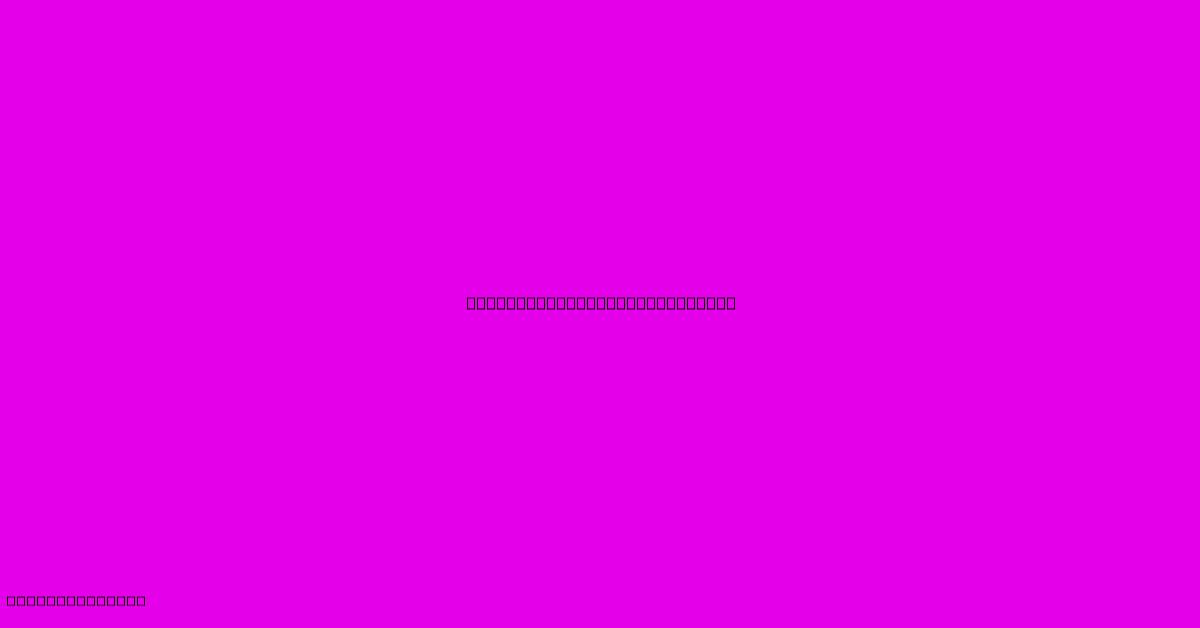
Discover more detailed and exciting information on our website. Click the link below to start your adventure: Visit Best Website mr.cleine.com. Don't miss out!
Table of Contents
Subsea Coating Technologies: Protecting Against a Hostile Environment
The subsea environment presents a unique and aggressive challenge for any structure or equipment. Constant exposure to seawater, high pressure, extreme temperatures, and corrosive elements demands robust and reliable protection. This is where subsea coating technologies play a crucial role, ensuring the longevity and functionality of critical infrastructure in offshore oil and gas, renewable energy, and other subsea operations.
Understanding the Challenges of the Subsea Environment
Before delving into the specific technologies, it's crucial to understand the harsh conditions subsea coatings must withstand:
- Corrosion: Saltwater is highly corrosive, accelerating the degradation of metallic structures. This is exacerbated by the presence of dissolved oxygen, hydrogen sulfide, and other aggressive ions.
- Cathodic Disbondment: This process occurs when the protective coating is compromised, allowing the underlying metal to become cathodically protected, leading to further corrosion and coating detachment.
- Biofouling: Marine organisms, such as barnacles and mussels, can attach to surfaces, increasing drag and reducing efficiency, as well as potentially compromising the coating's integrity.
- Hydrostatic Pressure: The immense pressure at depth can affect the coating's adhesion and performance.
- Abrasion: Movement of water, debris, and even marine life can cause abrasive wear on the coating.
Key Subsea Coating Technologies
Several technologies are employed to combat these challenges. Here are some of the most prominent:
1. Epoxy Coatings: These are widely used due to their excellent adhesion, chemical resistance, and relatively low cost. However, their performance can be limited in extreme conditions. Different formulations exist, offering varied properties tailored to specific requirements. High-build epoxy coatings offer superior thickness and protection against harsh environments.
2. Polyurethane Coatings: Polyurethane coatings provide excellent flexibility and impact resistance, making them suitable for applications where abrasion is a concern. Their resistance to seawater and UV degradation also contributes to their popularity. Two-component polyurethane coatings provide superior durability and chemical resistance.
3. Fusion Bonded Epoxy (FBE) Coatings: FBE coatings are applied in a specialized process that involves powder coating followed by curing. This technique results in a very durable and uniform coating with excellent adhesion and chemical resistance. FBE is particularly effective in pipeline protection.
4. Polyolefin Coatings: These coatings, including polyethylene and polypropylene, offer excellent chemical resistance and flexibility. They are often used in applications requiring high resistance to abrasion and impact, such as pipelines and risers. Cross-linked polyethylene (XLPE) provides even greater durability.
5. Zinc-Rich Coatings: These coatings provide sacrificial protection against corrosion. The zinc particles act as an anode, protecting the underlying metal. They are frequently used as a primer coat under other coatings.
6. Specialized Coatings: Advanced coatings are constantly being developed, including those incorporating advanced materials like: * Ceramics: For improved abrasion and corrosion resistance. * Nanomaterials: For enhanced barrier properties and self-healing capabilities. * Anti-fouling agents: To prevent biofouling.
Application Methods and Considerations
The successful application of subsea coatings requires careful consideration of several factors:
- Surface Preparation: Thorough surface cleaning and preparation are crucial for ensuring proper adhesion. This may involve blasting, grinding, or other surface treatment techniques.
- Application Techniques: Coatings can be applied by various methods, including spraying, brushing, or dipping. The choice of method depends on the coating type, surface geometry, and environmental conditions.
- Inspection and Quality Control: Regular inspection and quality control are vital to ensure the coating's integrity and performance throughout its service life. Non-destructive testing methods (NDT) such as ultrasonic testing and holiday detection are commonly employed.
Conclusion
Subsea coating technologies are essential for protecting critical infrastructure in the challenging subsea environment. The choice of coating system depends on the specific application, environmental conditions, and budget constraints. Ongoing research and development continue to improve the performance and longevity of subsea coatings, ensuring the continued success of subsea operations.
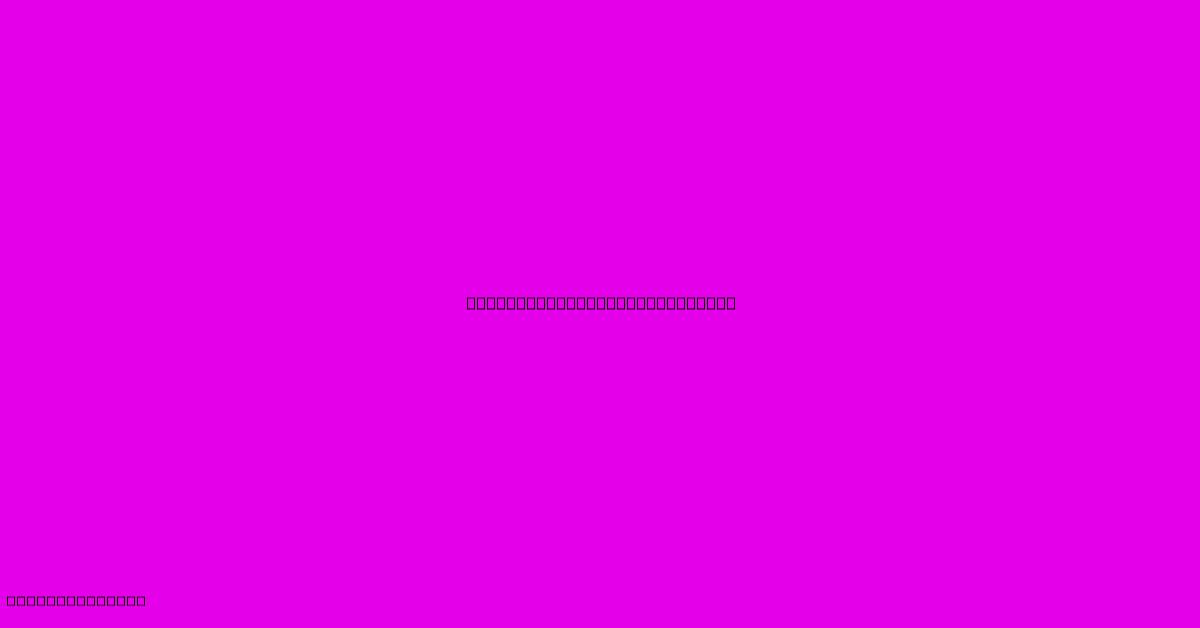
Thank you for visiting our website wich cover about Subsea Coating Technologies. We hope the information provided has been useful to you. Feel free to contact us if you have any questions or need further assistance. See you next time and dont miss to bookmark.
Featured Posts
-
Cma Technology Solutions
Jan 03, 2025
-
Esg Technology Solutions
Jan 03, 2025
-
Related Words For Technology
Jan 03, 2025
-
Dynatrace Technology Support
Jan 03, 2025
-
Oregon Technologies
Jan 03, 2025