Solid Sealing Technology
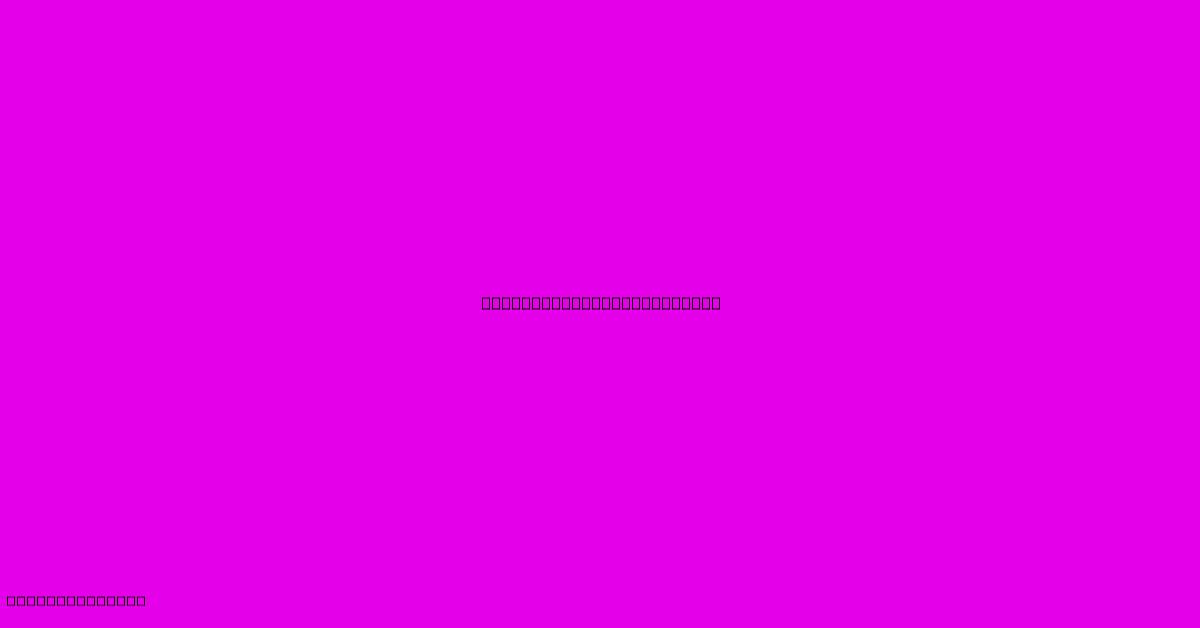
Discover more detailed and exciting information on our website. Click the link below to start your adventure: Visit Best Website mr.cleine.com. Don't miss out!
Table of Contents
Solid Sealing Technology: A Revolution in Leak Prevention
Solid sealing technology represents a significant advancement in leak prevention across various industries. Unlike traditional sealing methods that rely on elastomers or other flexible materials, solid seals offer a unique combination of durability, reliability, and longevity. This article will delve into the principles, applications, and advantages of this innovative technology.
Understanding Solid Sealing Technology
Solid sealing technology utilizes rigid, non-deformable materials to create a leak-proof barrier. This contrasts sharply with traditional gasket materials, which rely on compression to create a seal. Solid seals, often made from materials like metals, ceramics, or advanced polymers, achieve sealing through precise machining, surface finishing, and often the application of specialized coatings. The seal is formed by the precise mating of two surfaces, creating a hermetic barrier that prevents leakage of liquids, gases, or even fine particulates.
Key Characteristics of Solid Seals:
- High Pressure Resistance: Solid seals excel in high-pressure applications where traditional seals may fail due to compression set or deformation.
- Temperature Stability: Many solid seal materials exhibit excellent temperature resistance, maintaining their integrity in extreme hot or cold conditions.
- Chemical Resistance: Depending on the material chosen, solid seals can offer superior resistance to a wide range of chemicals and solvents.
- Long Service Life: The non-deformable nature of solid seals contributes to their exceptionally long service life, reducing maintenance and replacement costs.
- Improved Reliability: Their consistent performance under varying conditions enhances overall system reliability.
Applications of Solid Sealing Technology
Solid sealing technology finds applications across a wide range of industries, including:
- Automotive: Sealing engine components, transmissions, and fuel systems.
- Aerospace: Critical sealing in aircraft engines, hydraulic systems, and spacecraft.
- Oil & Gas: Sealing high-pressure pipelines, valves, and wellheads.
- Chemical Processing: Sealing reactors, pumps, and other process equipment.
- Pharmaceutical Manufacturing: Ensuring sterile and leak-free environments in production processes.
- Nuclear Power: Critical sealing in reactors and other nuclear components.
Advantages of Solid Sealing Technology Over Traditional Methods
Compared to traditional sealing methods using O-rings, gaskets, or elastomeric seals, solid sealing technology offers several key advantages:
- Reduced Leakage: The precision of solid seals minimizes the risk of leakage, even under extreme conditions.
- Enhanced Durability: Solid seals withstand higher pressures and temperatures without deformation or failure.
- Lower Maintenance Costs: Longer service life translates to reduced maintenance and replacement expenses.
- Improved Safety: Reduced leakage risk contributes to improved safety in critical applications.
- Increased System Reliability: Consistent sealing performance enhances the overall reliability of the system.
Material Selection in Solid Sealing
The selection of the appropriate material for a solid seal is critical and depends heavily on the specific application requirements. Factors to consider include:
- Operating Pressure and Temperature: The material must withstand the expected pressure and temperature extremes.
- Chemical Compatibility: The seal material must be compatible with the fluids or gases it will be in contact with.
- Surface Finish and Machining Tolerances: Precise machining and surface finishing are crucial for achieving a leak-proof seal.
The Future of Solid Sealing Technology
Ongoing research and development efforts continue to refine solid sealing technology, leading to the development of new materials and manufacturing processes. This includes the exploration of advanced materials with enhanced properties and the use of innovative manufacturing techniques like additive manufacturing (3D printing) to create complex seal geometries. The future of solid sealing likely involves even greater precision, wider material choices, and broader application across various industries.
Conclusion:
Solid sealing technology represents a significant step forward in leak prevention, providing superior performance and reliability compared to traditional methods. Its widespread adoption across diverse industries highlights its importance in ensuring safety, efficiency, and cost-effectiveness in countless applications. As technology advances, the role of solid sealing in critical applications will only become more pronounced.
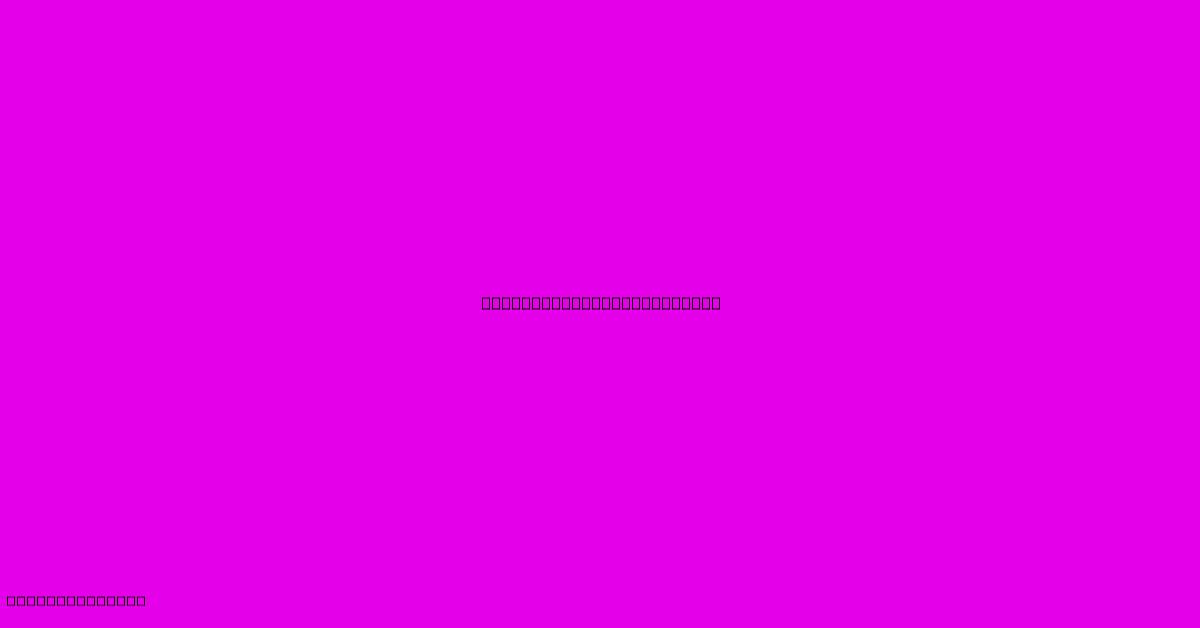
Thank you for visiting our website wich cover about Solid Sealing Technology. We hope the information provided has been useful to you. Feel free to contact us if you have any questions or need further assistance. See you next time and dont miss to bookmark.
Featured Posts
-
Zeroed In Technologies Llc Letter
Dec 26, 2024
-
Beyonce Halftime Show Country Review
Dec 26, 2024
-
Who Is Tayce Strictly Christmas Contestant
Dec 26, 2024
-
Nba Christmas Highlights 76ers Wolves Knicks Lakers
Dec 26, 2024
-
W Technology
Dec 26, 2024