Smd Technologies
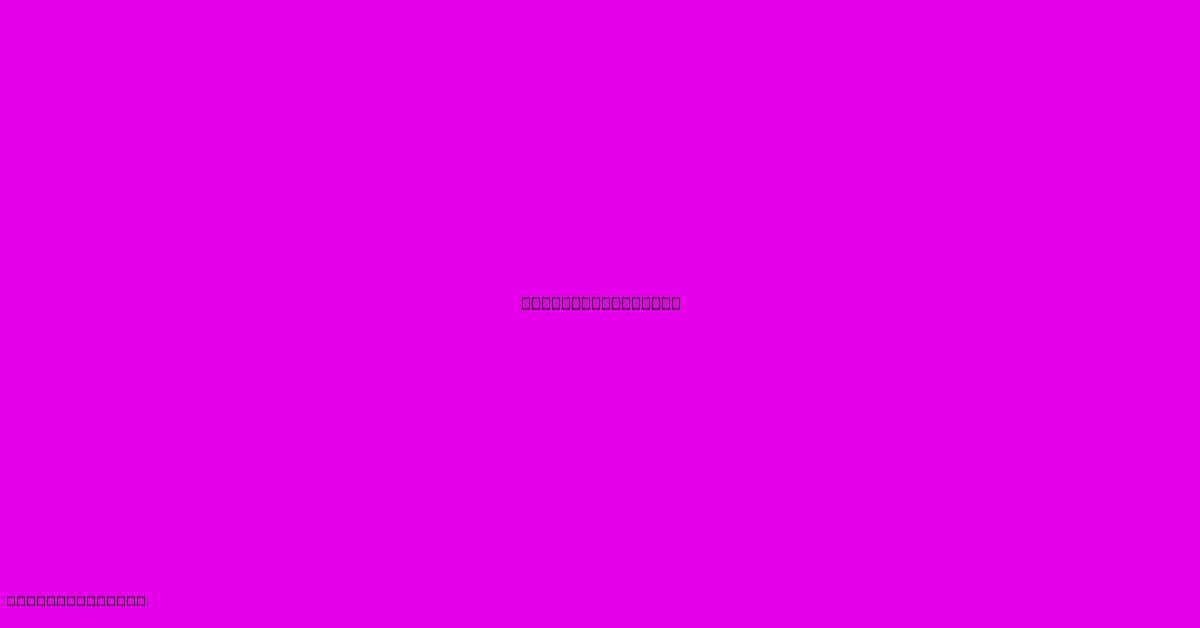
Discover more detailed and exciting information on our website. Click the link below to start your adventure: Visit Best Website mr.cleine.com. Don't miss out!
Table of Contents
SMD Technologies: A Deep Dive into Surface Mount Devices
Surface Mount Devices (SMDs) have revolutionized the electronics industry, enabling smaller, more efficient, and cost-effective circuit boards. This article delves into the world of SMD technologies, exploring their advantages, disadvantages, and the various aspects that make them a cornerstone of modern electronics.
What are SMDs?
SMDs are electronic components designed to be mounted or soldered directly onto the surface of a printed circuit board (PCB), unlike through-hole components which have leads that pass through the board. This surface mounting allows for significantly higher component density and miniaturization. The size of SMDs is typically designated using a metric code, such as 0603, 0805, or 1206, which represent their dimensions in millimeters.
Advantages of SMD Technology:
-
Miniaturization: SMDs enable the creation of significantly smaller and thinner electronic devices. This is crucial in applications where space is limited, such as smartphones, wearable technology, and laptops.
-
Higher Component Density: More components can be placed on a given PCB area compared to through-hole technology, leading to smaller and lighter products.
-
Improved Performance: SMDs generally have lower inductance and capacitance, leading to improved high-frequency performance. Shorter trace lengths also reduce signal delays.
-
Automated Assembly: SMDs are ideally suited for automated assembly processes, resulting in faster production times and lower labor costs.
-
Reduced Costs: The automation and higher component density contribute to lower overall manufacturing costs.
-
Enhanced Reliability: Properly manufactured and assembled SMDs offer excellent reliability and durability.
Disadvantages of SMD Technology:
-
Soldering Complexity: Soldering SMDs requires specialized equipment and skills, particularly for smaller components. Reflow soldering is typically used, which involves heating the entire board to melt the solder paste simultaneously.
-
Inspection Challenges: Inspecting soldered SMDs can be more challenging due to their small size. Microscopic inspection or automated optical inspection (AOI) may be necessary.
-
Component fragility: SMDs are more susceptible to damage during handling and assembly compared to through-hole components.
-
Repair Difficulties: Repairing or replacing a faulty SMD component can be significantly more difficult than replacing a through-hole component. Specialized tools and skills are often required.
Types of SMD Components:
SMDs encompass a wide range of electronic components, including:
- Resistors: Used to control current flow in a circuit.
- Capacitors: Used to store electrical energy.
- Inductors: Used to store energy in a magnetic field.
- Integrated Circuits (ICs): Complex electronic circuits integrated onto a single chip.
- Transistors: Used for amplification and switching.
- Diodes: Used to allow current to flow in only one direction.
Applications of SMD Technology:
SMD technology is ubiquitous in modern electronics, finding applications in a vast array of devices, including:
-
Smartphones and Tablets: The miniaturization and high component density are crucial for these portable devices.
-
Wearable Electronics: SMDs enable the creation of small, lightweight wearable devices such as smartwatches and fitness trackers.
-
Automotive Electronics: SMDs are used extensively in modern vehicles for various control systems and infotainment.
-
Medical Devices: The reliability and miniaturization of SMDs are important in medical devices such as pacemakers and implantable sensors.
-
Aerospace and Defense: The robustness and reliability of SMDs are critical in these demanding applications.
Conclusion:
SMD technology has fundamentally changed the landscape of electronics manufacturing. Its advantages in miniaturization, performance, and cost-effectiveness have made it indispensable for a wide variety of applications. While there are challenges associated with soldering and repair, the benefits far outweigh the drawbacks, ensuring that SMDs will continue to be a dominant force in the electronics industry for the foreseeable future. Further advancements in materials, manufacturing processes, and design techniques will only solidify SMDs' position as the preferred technology for increasingly complex and sophisticated electronics.
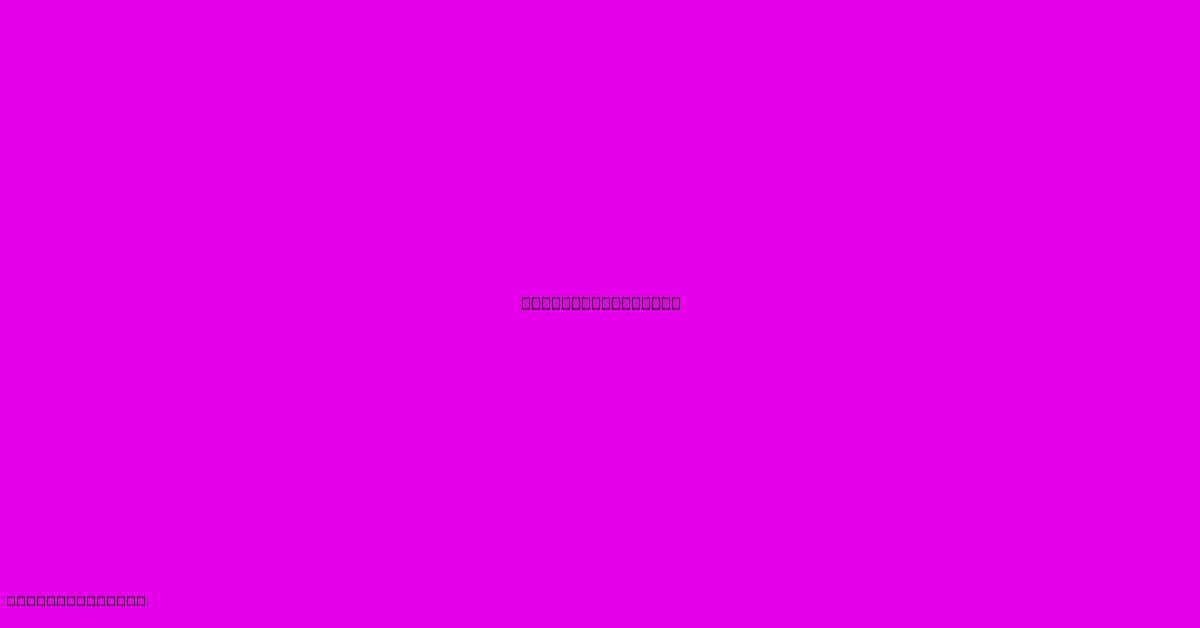
Thank you for visiting our website wich cover about Smd Technologies. We hope the information provided has been useful to you. Feel free to contact us if you have any questions or need further assistance. See you next time and dont miss to bookmark.
Featured Posts
-
Global Technology Solutions Group
Dec 31, 2024
-
Linda Lavin Alice Star 87 Dies
Dec 31, 2024
-
Commanders Player Proposes After Playoff
Dec 31, 2024
-
Music City Bowl Odds 2024
Dec 31, 2024
-
Allied Technologies International Inc
Dec 31, 2024