Select Machining Technologies
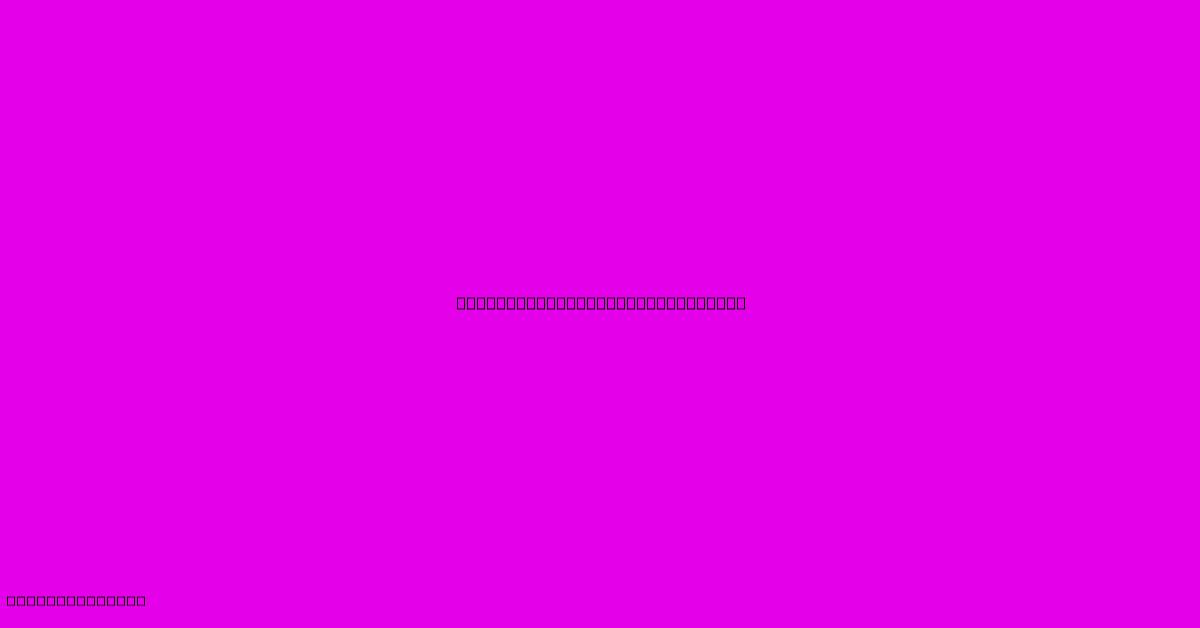
Discover more detailed and exciting information on our website. Click the link below to start your adventure: Visit Best Website mr.cleine.com. Don't miss out!
Table of Contents
Selecting the Right Machining Technology: A Comprehensive Guide
Selecting the appropriate machining technology is crucial for achieving optimal results in manufacturing. The choice depends on a multitude of factors, including material properties, desired tolerances, production volume, and budget constraints. This article provides a comprehensive overview of various machining technologies, highlighting their strengths and weaknesses to guide you in making informed decisions.
Understanding the Basics of Machining
Machining involves removing material from a workpiece using a cutting tool. This process transforms raw materials into precise components with specific shapes and dimensions. Different machining technologies utilize various cutting methods and tools, each with unique capabilities and limitations.
Key Machining Technologies: A Detailed Comparison
1. Turning:
- Process: A rotating workpiece is shaped by a cutting tool moving along its axis.
- Applications: Producing cylindrical parts like shafts, pins, and bushings.
- Strengths: High material removal rates, excellent surface finish, suitable for mass production.
- Weaknesses: Limited in creating complex geometries.
2. Milling:
- Process: A rotating cutting tool removes material from a stationary or slowly moving workpiece.
- Applications: Creating complex shapes, slots, and pockets. Widely used in mold and die making.
- Strengths: Versatility in shaping, capable of producing intricate designs.
- Weaknesses: Can be slower than turning for simple parts, requires skilled operators.
3. Drilling:
- Process: Creating holes in workpieces using a rotating drill bit.
- Applications: Widely used in various industries for creating holes of various sizes and depths.
- Strengths: Simple and efficient for hole creation.
- Weaknesses: Limited in creating complex hole geometries.
4. Grinding:
- Process: Removing material using an abrasive wheel.
- Applications: Achieving high precision and surface finish, ideal for sharpening tools and finishing parts.
- Strengths: Excellent surface finish, high precision, capable of processing hard materials.
- Weaknesses: Can be slower than other methods, generates heat.
5. EDM (Electrical Discharge Machining):
- Process: Material removal through electrical discharges between the workpiece and an electrode.
- Applications: Machining hard-to-machine materials like hardened steel and ceramics, creating complex shapes.
- Strengths: Can machine virtually any conductive material, capable of creating intricate geometries.
- Weaknesses: Slower process, requires specialized equipment and expertise.
6. Laser Cutting:
- Process: Material removal using a high-powered laser beam.
- Applications: Cutting thin sheets of metal, plastics, and wood with high precision.
- Strengths: High precision, fast cutting speed, minimal heat-affected zone.
- Weaknesses: Limited to thin materials, can be expensive.
7. Water Jet Cutting:
- Process: Material removal using a high-pressure jet of water mixed with abrasive particles.
- Applications: Cutting a wide range of materials, including metals, ceramics, and composites.
- Strengths: Versatile, minimal heat-affected zone, capable of cutting thick materials.
- Weaknesses: Can be slower than other methods, requires specialized equipment.
Factors Influencing Technology Selection
The optimal machining technology depends on several critical factors:
- Material: The material's hardness, machinability, and thermal properties dictate the suitable machining process.
- Geometry: Complex shapes often require milling or EDM, while simple shapes can be efficiently produced using turning.
- Tolerances: Grinding and EDM are preferred for achieving tight tolerances.
- Surface Finish: Grinding and polishing provide excellent surface finishes.
- Production Volume: High-volume production often favors automated turning and milling.
- Cost: Consider the initial investment in equipment, tooling, and operating costs.
Conclusion
Choosing the right machining technology is a critical decision that impacts the efficiency, quality, and cost of manufacturing. A thorough understanding of the capabilities and limitations of each process, coupled with careful consideration of the project-specific requirements, is vital for achieving optimal results. Consulting with experienced machinists and engineers can provide invaluable insights and guidance throughout the selection process.
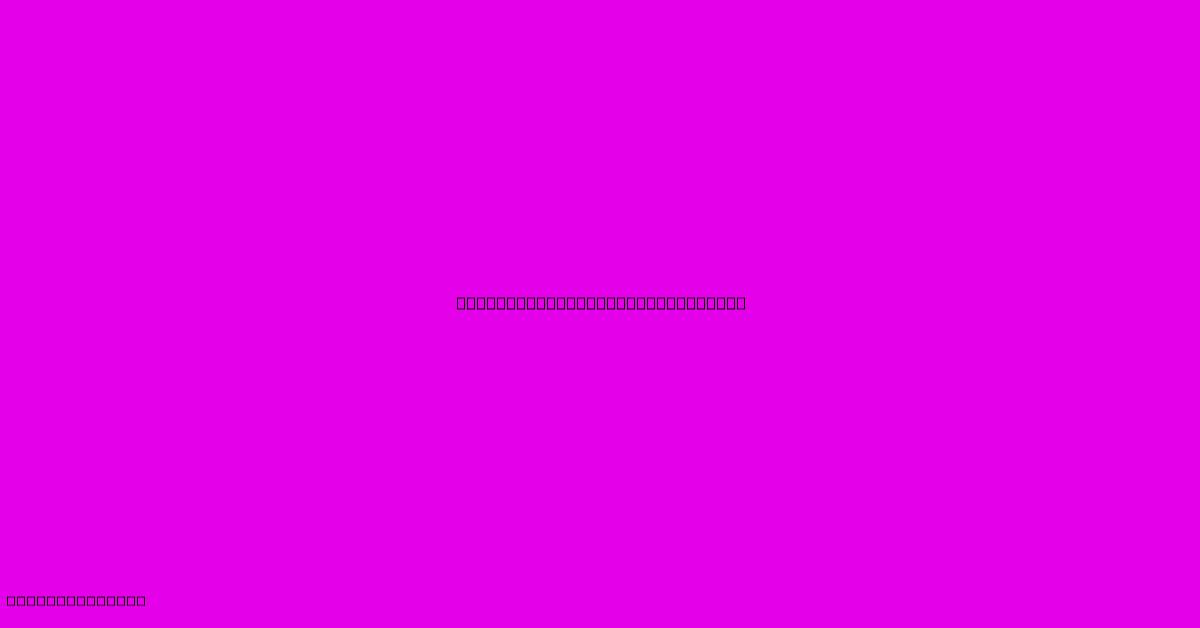
Thank you for visiting our website wich cover about Select Machining Technologies. We hope the information provided has been useful to you. Feel free to contact us if you have any questions or need further assistance. See you next time and dont miss to bookmark.
Featured Posts
-
Fabio Ochoa En Colombia Su Regreso
Dec 24, 2024
-
Water Technology Companies
Dec 24, 2024
-
Technology Upgrades
Dec 24, 2024
-
Whats In Gaetzs Ethics Report
Dec 24, 2024
-
Ss And C Technologies Windsor Ct
Dec 24, 2024