Scs Technology
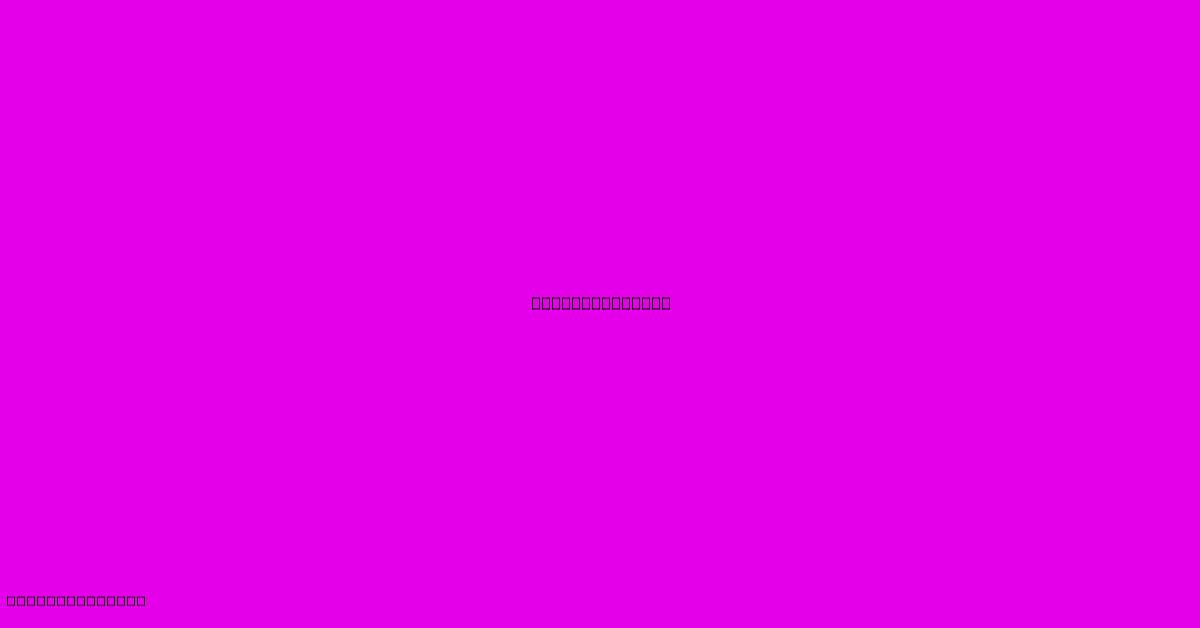
Discover more detailed and exciting information on our website. Click the link below to start your adventure: Visit Best Website mr.cleine.com. Don't miss out!
Table of Contents
Decoding SCS Technology: A Deep Dive into its Applications and Future
Introduction:
SCS, or Substrate Conformal Coating technology, is a revolutionary advancement in the world of electronics manufacturing and beyond. It's a precise, automated process used to apply thin, uniform coatings to complex three-dimensional substrates. Unlike traditional methods, SCS excels at reaching intricate geometries and offering superior conformal coverage, leading to enhanced product performance and reliability. This article will explore the intricacies of SCS technology, its diverse applications, and its promising future.
What is Substrate Conformal Coating?
Substrate Conformal Coating (SCC) goes beyond simple surface coating. It's about creating a uniform, thin layer of material that precisely follows the contours of a three-dimensional object, regardless of its complexity. This level of conformity is critical for protecting sensitive electronics and components from various environmental factors.
Key Characteristics of SCS Technology:
- Precision and Uniformity: SCS ensures a consistent coating thickness across the entire substrate, even in recessed areas and sharp corners. This consistency is crucial for achieving optimal performance and protection.
- Conformal Coverage: The coating perfectly adheres to the substrate's three-dimensional shape, providing complete protection against environmental hazards.
- Automated Process: Modern SCS systems are largely automated, ensuring high throughput, reproducibility, and reduced manual labor.
- Material Versatility: Various materials can be used as coatings, depending on the specific application, including polymers, ceramics, and metals. This versatility allows for tailoring the coating's properties (e.g., electrical insulation, chemical resistance, thermal conductivity).
Applications of SCS Technology:
The applications of SCS technology are vast and constantly expanding. Its precision and conformal coating capabilities have made it invaluable in various industries:
1. Electronics Manufacturing: This is perhaps the most significant application of SCS. It's used to protect printed circuit boards (PCBs), microchips, and other electronic components from:
- Moisture and Humidity: Preventing corrosion and short circuits.
- Temperature Fluctuations: Enhancing thermal stability and preventing damage from extreme temperatures.
- Physical Shock and Vibration: Providing mechanical protection and reducing damage from impacts.
- Chemical Exposure: Protecting against harsh chemicals and solvents.
2. Medical Devices: SCS technology plays a vital role in the manufacturing of medical devices, ensuring the reliability and safety of implantable devices and diagnostic tools by:
- Biocompatibility: Using biocompatible coating materials to minimize adverse reactions in the body.
- Sterilization: Applying coatings that withstand sterilization processes.
- Improved Durability: Enhancing the lifespan and performance of medical implants and tools.
3. Aerospace and Defense: The demanding requirements of the aerospace and defense industries make SCS technology ideal for protecting sensitive equipment from:
- Extreme Temperatures: Withstanding high temperatures and thermal cycling.
- High Vibration: Withstanding the extreme vibrations experienced during launch and flight.
- Harsh Environments: Protecting against corrosive substances and extreme weather conditions.
4. Automotive Industry: SCS contributes to improving the reliability and longevity of automotive components through:
- Corrosion Protection: Protecting metal parts from rust and degradation.
- Enhanced Performance: Improving the performance of electronic sensors and actuators.
- Improved Aesthetics: Providing a smooth and uniform finish to various components.
The Future of SCS Technology:
Research and development in SCS technology continue to advance, promising even more efficient and versatile applications. Future developments may include:
- Advanced Materials: The exploration and implementation of new coating materials with enhanced properties, such as self-healing capabilities or improved conductivity.
- Improved Process Control: The development of more sophisticated control systems for even greater precision and uniformity in coating application.
- Integration with Additive Manufacturing: Combining SCS with 3D printing technologies to create complex, coated parts directly.
- Miniaturization: Applying SCS technology to increasingly smaller and more complex micro-devices.
Conclusion:
Substrate Conformal Coating technology represents a significant advancement in material science and manufacturing. Its ability to provide precise, uniform coatings to complex three-dimensional substrates has opened up a world of possibilities across diverse industries. As research continues, the applications and capabilities of SCS technology are poised to expand further, leading to innovations in various fields and improvements in the reliability and performance of numerous products.
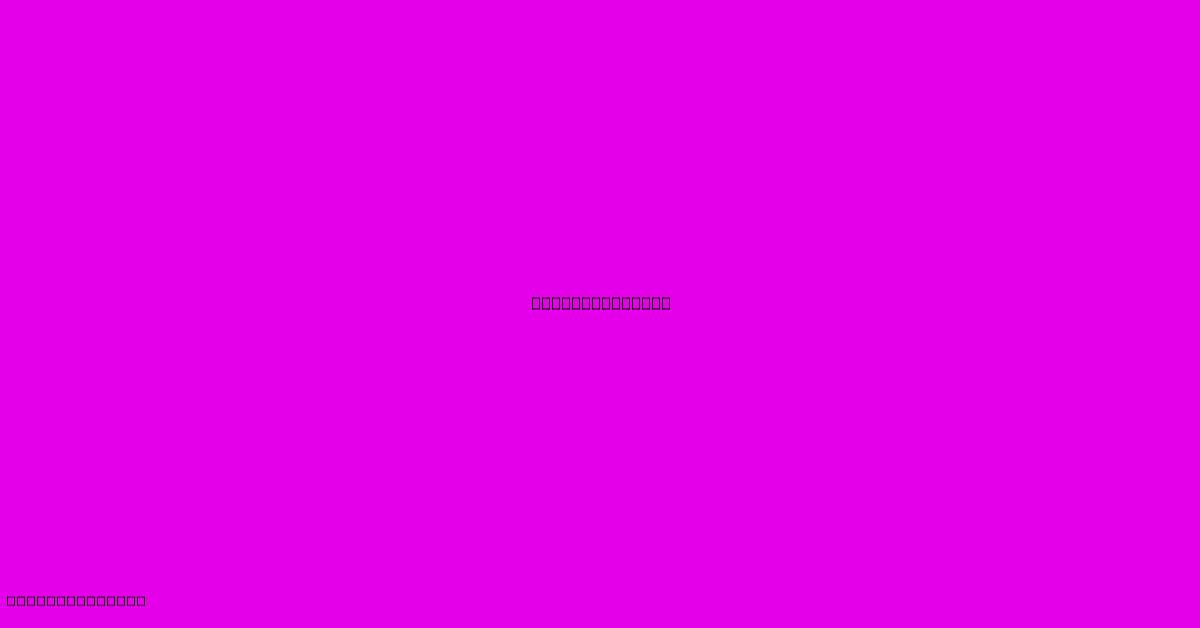
Thank you for visiting our website wich cover about Scs Technology. We hope the information provided has been useful to you. Feel free to contact us if you have any questions or need further assistance. See you next time and dont miss to bookmark.
Featured Posts
-
Love Actually Directors Surprise Confession
Dec 25, 2024
-
Is Beta Technologies A Public Company
Dec 25, 2024
-
New Roofing Technology 2023
Dec 25, 2024
-
Blackrock Technology Opportunities Fund
Dec 25, 2024
-
Pentagon Technologies
Dec 25, 2024