Rotating Composite Technologies
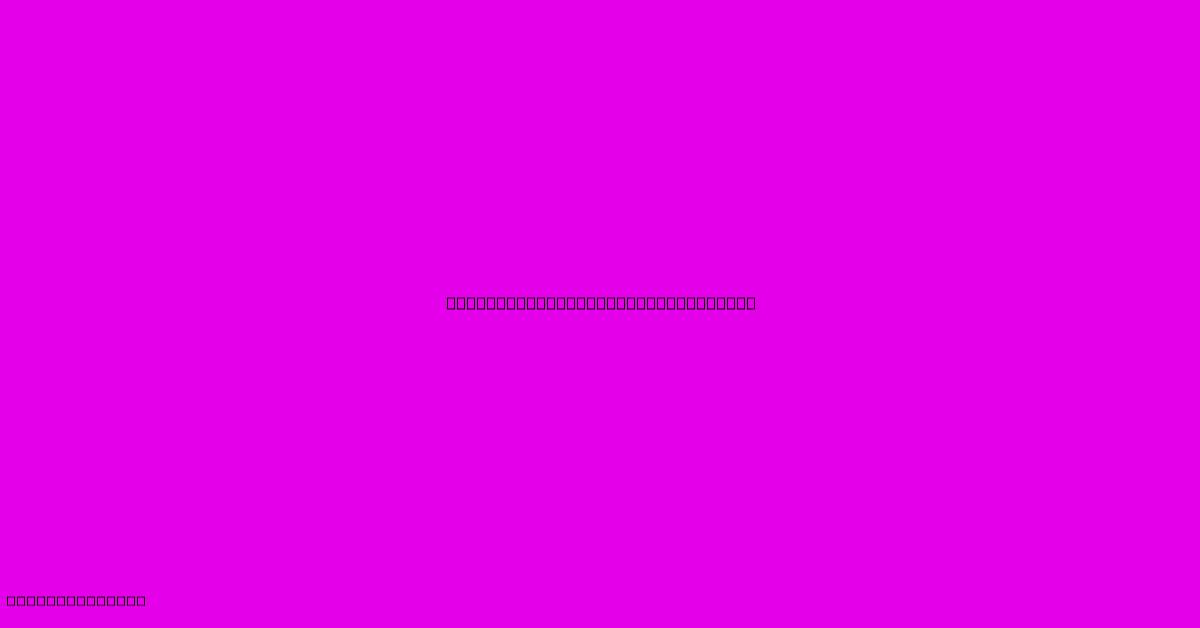
Discover more detailed and exciting information on our website. Click the link below to start your adventure: Visit Best Website mr.cleine.com. Don't miss out!
Table of Contents
Rotating Composite Technologies: Revolutionizing Performance and Efficiency
Rotating composite technologies represent a significant advancement in various engineering fields. This article explores the core principles, applications, and future prospects of this innovative approach to material science and mechanical engineering.
What are Rotating Composite Technologies?
Rotating composite technologies involve the manufacturing of composite materials using a rotating process. This process allows for the controlled alignment and distribution of fibers within a matrix, resulting in superior mechanical properties compared to traditional composite fabrication methods. The rotating process can take several forms, including centrifugal casting, filament winding, and pultrusion variations, each offering unique advantages depending on the desired outcome.
Key Advantages of Rotating Composites:
-
Enhanced Mechanical Properties: The precise fiber orientation achieved through rotation leads to significantly improved strength, stiffness, and fatigue resistance along specific axes. This is particularly crucial for applications requiring high performance under demanding conditions.
-
Lightweight Construction: Rotating composites frequently result in lighter structures compared to traditional materials, offering significant benefits in weight-sensitive applications such as aerospace and automotive engineering.
-
Tailored Design: The rotational process enables highly customized material properties by controlling fiber type, orientation, and volume fraction. This permits engineers to optimize the composite for specific performance requirements.
-
Improved Durability: The controlled fiber alignment contributes to enhanced resistance against cracking and other forms of damage, extending the lifespan of components.
-
Cost-Effectiveness (in certain applications): While initial investment in specialized equipment might be higher, the potential for reduced material waste and increased efficiency can lead to cost savings in mass production scenarios.
Applications of Rotating Composite Technologies:
The versatility of rotating composites has led to their adoption across a wide range of industries:
-
Aerospace: Rotating composites are extensively used in aircraft components, including rotor blades, fuselage sections, and engine parts, to reduce weight and improve fuel efficiency.
-
Automotive: Lighter vehicles with improved fuel economy are made possible through the use of rotating composites in body panels, chassis components, and drive shafts.
-
Wind Energy: Rotating composites enhance the performance of wind turbine blades by increasing their strength-to-weight ratio and resistance to fatigue.
-
Sporting Goods: The high strength-to-weight ratio of rotating composites is exploited in the manufacturing of high-performance sporting equipment like golf clubs, tennis rackets, and bicycle frames.
-
Medical Devices: Biocompatible rotating composites are increasingly used in orthopedic implants and other medical devices requiring strength, biocompatibility, and durability.
Types of Rotating Composite Manufacturing Processes:
Several key methods utilize rotation for composite material creation:
-
Centrifugal Casting: This method uses centrifugal force to distribute fibers within a mold, resulting in a uniform composite structure. It is particularly suitable for creating cylindrical components.
-
Filament Winding: This technique involves winding continuous fibers onto a rotating mandrel, allowing for precise control over fiber orientation and the creation of complex shapes.
-
Pultrusion (with rotational enhancements): While traditional pultrusion is linear, incorporating rotational elements can improve fiber alignment and enhance the properties of the final product.
Challenges and Future Directions:
Despite the numerous advantages, challenges remain:
-
Scalability: Scaling up production to meet high-volume demands can be challenging for some rotating composite manufacturing processes.
-
Cost: While potentially cost-effective in mass production, the initial investment in specialized equipment can be significant.
-
Process Optimization: Further research and development are needed to optimize the various rotating composite manufacturing processes to achieve even higher performance and efficiency.
The future of rotating composite technologies is bright. Continued research and development will focus on:
-
Advanced Materials: Incorporating novel fibers and matrices to further enhance performance characteristics.
-
Automation: Developing automated manufacturing processes to increase efficiency and reduce production costs.
-
Hybrid Composites: Combining rotating composites with other advanced materials to create hybrid structures with enhanced properties.
In conclusion, rotating composite technologies are revolutionizing materials science and engineering, offering superior mechanical properties, lightweight construction, and tailored design capabilities. As research and development continue, the applications and benefits of rotating composites will undoubtedly expand across numerous industries.
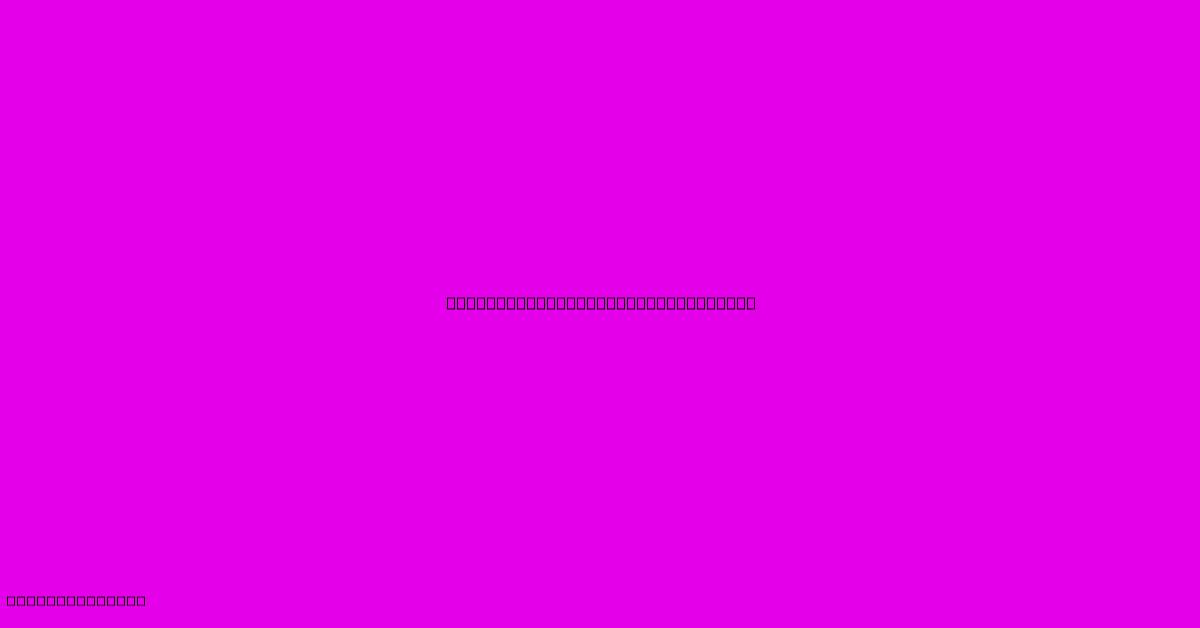
Thank you for visiting our website wich cover about Rotating Composite Technologies. We hope the information provided has been useful to you. Feel free to contact us if you have any questions or need further assistance. See you next time and dont miss to bookmark.
Featured Posts
-
Cranial Technologies Annandale
Jan 04, 2025
-
Group14 Technologies Moses Lake
Jan 04, 2025
-
Embion Technologies
Jan 04, 2025
-
Poet Technologies Forum
Jan 04, 2025
-
Stevens Institute Of Technology Tours
Jan 04, 2025