Rotary Kiln Technology
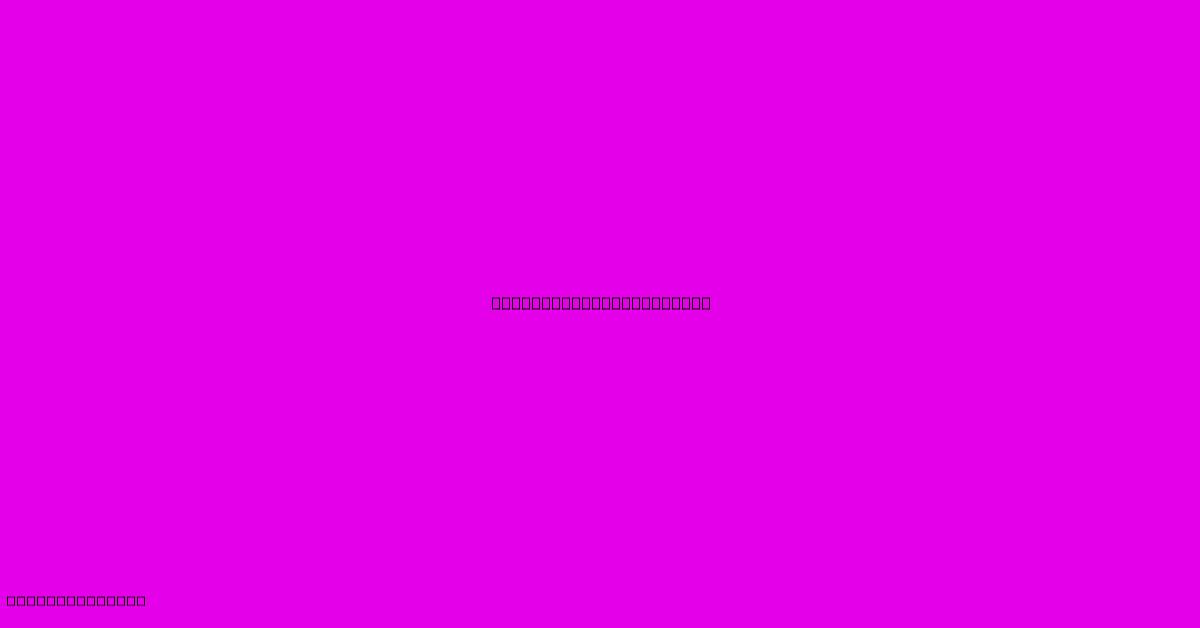
Discover more detailed and exciting information on our website. Click the link below to start your adventure: Visit Best Website mr.cleine.com. Don't miss out!
Table of Contents
Rotary Kiln Technology: A Deep Dive into Industrial Thermal Processing
Rotary kilns are indispensable pieces of equipment in various industries, serving as workhorses for thermal processing applications. This article delves into the intricacies of rotary kiln technology, exploring its principles, applications, advantages, and limitations.
What is a Rotary Kiln?
A rotary kiln is a long, cylindrical rotating furnace used to process materials through indirect or direct heating. Its design incorporates a slightly inclined cylinder that slowly rotates, allowing material to move gradually through the kiln as it's exposed to high temperatures. The continuous rotation ensures uniform heating and prevents material from sticking to the kiln's walls. The heat source can vary significantly depending on the application, ranging from burning fossil fuels to using electric heating elements.
Key Components of a Rotary Kiln System:
- Kiln Shell: The robust cylindrical structure made of steel or refractory materials, designed to withstand high temperatures and pressures.
- Rotating Mechanism: Typically driven by a gear and pinion system or rollers, ensuring smooth and consistent rotation.
- Burners: Used to introduce heat into the kiln. Different burner types exist, depending on the fuel used (natural gas, oil, coal, etc.) and desired temperature profile.
- Preheater: A component often integrated into the system to preheat the incoming material, improving energy efficiency.
- Cooling System: For cooling the processed material before discharge.
- Dust Collection System: Crucial for environmental protection, capturing and removing particulate matter from the exhaust gases.
- Feed and Discharge Systems: These mechanisms facilitate the continuous introduction of raw materials and the removal of processed products.
Working Principle of a Rotary Kiln:
The process begins with the raw material being fed into the higher end of the inclined kiln. As the kiln rotates, the material gradually moves down the incline, encountering progressively higher temperatures. The heat source, located at the lower end, transfers thermal energy to the material, inducing the desired physical or chemical transformations. These transformations can include drying, calcination, reduction, oxidation, and other processes depending on the application. The processed material is eventually discharged from the lower end of the kiln.
Applications of Rotary Kiln Technology:
Rotary kilns find applications across a wide spectrum of industries:
- Cement Production: One of the most prominent uses, rotary kilns are essential for the production of clinker, a key ingredient in cement.
- Lime Production: Kilns are used to calcine limestone into quicklime (calcium oxide), a critical material in various industries, including construction and steelmaking.
- Metallurgy: Rotary kilns are employed in the processing of ores and the production of various metals.
- Waste Treatment: Incineration and thermal treatment of hazardous wastes.
- Chemical Processing: Various chemical reactions and processes requiring controlled heating.
- Mineral Processing: Calcination and other thermal treatments of minerals.
Advantages of Rotary Kilns:
- Continuous Operation: Enables high throughput and consistent product quality.
- Uniform Heating: The rotating nature ensures even heat distribution.
- Versatility: Adaptable to a wide range of materials and processes.
- Scalability: Kilns can be designed to various sizes, catering to different production capacities.
Limitations of Rotary Kilns:
- High Capital Cost: The initial investment for purchasing and installing a rotary kiln can be substantial.
- High Energy Consumption: Depending on the application and design, energy consumption can be significant.
- Maintenance Requirements: Regular maintenance is necessary to ensure optimal performance and longevity.
- Environmental Concerns: Exhaust gases can contain pollutants, necessitating effective emission control systems.
Future Trends in Rotary Kiln Technology:
Research and development are ongoing to improve the efficiency and sustainability of rotary kilns. This includes:
- Improved Burner Technology: More efficient burners with lower emissions.
- Advanced Control Systems: Sophisticated control systems for optimizing kiln operation and reducing energy consumption.
- Alternative Fuels: Exploring the use of alternative fuels and renewable energy sources to reduce reliance on fossil fuels.
- Waste Heat Recovery: Implementing systems to recover and reuse waste heat, improving energy efficiency.
Conclusion:
Rotary kiln technology plays a vital role in a broad range of industries, providing a reliable and efficient means for thermal processing. Ongoing advancements are focused on improving sustainability, efficiency, and reducing the environmental impact of these powerful machines. Understanding the principles and applications of rotary kilns is crucial for anyone involved in materials processing and manufacturing.
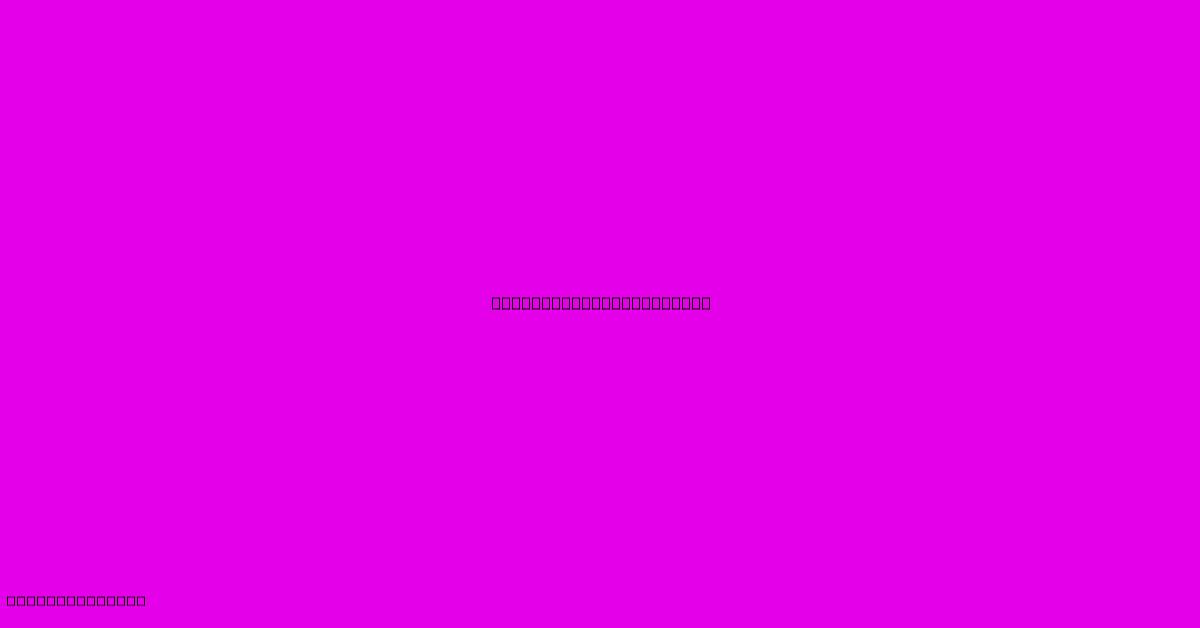
Thank you for visiting our website wich cover about Rotary Kiln Technology. We hope the information provided has been useful to you. Feel free to contact us if you have any questions or need further assistance. See you next time and dont miss to bookmark.
Featured Posts
-
Wolfsburg X Borussia Palpite 22 12
Dec 23, 2024
-
Vall Technologies
Dec 23, 2024
-
Real Madrid X Sevilla Horario Palpites E Onde Ver
Dec 23, 2024
-
Resultado Real Madrid Sevilla Goles
Dec 23, 2024
-
Technological Acquisition
Dec 23, 2024