Pvd Technology
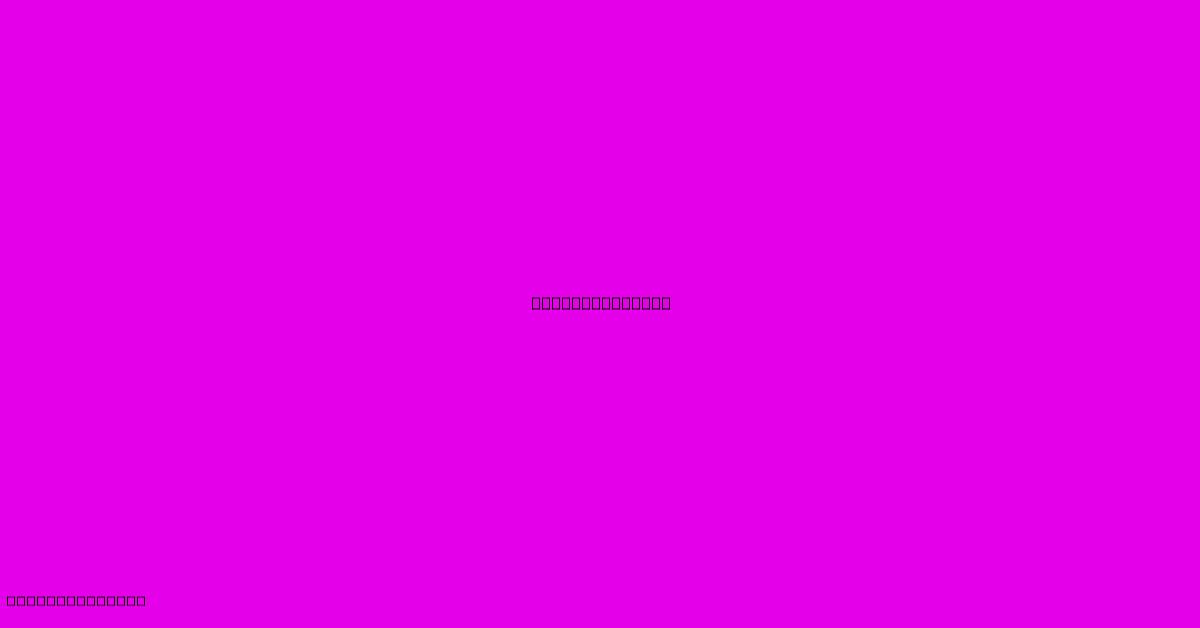
Discover more detailed and exciting information on our website. Click the link below to start your adventure: Visit Best Website mr.cleine.com. Don't miss out!
Table of Contents
Understanding PVD Technology: A Deep Dive into Physical Vapor Deposition
Physical Vapor Deposition (PVD) is a sophisticated coating process used to deposit thin films of various materials onto substrates. Unlike chemical vapor deposition (CVD), PVD doesn't involve chemical reactions during the deposition process. Instead, it relies on physical processes to transfer material from a source to a substrate. This results in coatings with exceptional properties, making PVD a crucial technology across diverse industries.
How PVD Works: A Step-by-Step Process
The core principle behind PVD involves converting a solid material into a gaseous phase and then depositing this vapor onto a target substrate. This typically involves several key steps:
-
Evaporation/Sputtering: The source material, often a solid target, is transformed into a vapor. This can happen through several methods:
- Evaporation: The material is heated until it evaporates. This method is suitable for materials with relatively low melting points.
- Sputtering: The target material is bombarded with energetic ions (usually argon), causing atoms to be ejected and propelled towards the substrate. This method is preferred for high-melting-point materials and offers better control over film properties.
- Arc Evaporation: A high-voltage arc is used to evaporate the source material. This technique is particularly effective for creating dense, high-quality films.
-
Ionization (Optional): In some PVD techniques, the vaporized atoms are ionized, giving them a positive charge. This allows for better control over the deposition process, leading to improved film quality and adhesion.
-
Transport: The vaporized atoms (or ions) travel through a vacuum chamber to the substrate. The vacuum is crucial to prevent collisions with air molecules, ensuring a uniform and high-quality coating.
-
Deposition: The vaporized atoms condense onto the substrate, forming a thin film. The substrate's temperature and other parameters significantly influence the film's properties.
-
Cooling: After deposition, the coated substrate is cooled down to stabilize the film.
Types of PVD Techniques:
Several variations of PVD exist, each with its own advantages and applications:
- Magnetron Sputtering: A widely used technique employing magnetic fields to confine and enhance the ionization of the sputtering gas, resulting in higher deposition rates and improved film quality.
- Arc Evaporation: Characterized by its ability to deposit high-melting-point materials and create very dense films.
- Electron Beam Evaporation: Uses a high-energy electron beam to evaporate the source material, enabling precise control over the deposition process.
- Pulsed Laser Deposition (PLD): A laser is used to ablate the target material, creating a plume of vapor that is deposited onto the substrate. This technique is known for its ability to create complex films with precise stoichiometry.
Applications of PVD Technology:
The versatility of PVD makes it indispensable in numerous industries:
- Cutting Tools: PVD coatings enhance the hardness, wear resistance, and corrosion resistance of cutting tools, extending their lifespan and improving machining efficiency. Examples include TiN, TiAlN, and CrN coatings.
- Decorative Coatings: PVD is used to create aesthetically pleasing and durable coatings on jewelry, watches, and other decorative items. Colors ranging from gold and silver to vibrant blues and blacks are achievable.
- Medical Implants: Biocompatible PVD coatings improve the osseointegration and bioactivity of medical implants, reducing the risk of rejection and improving patient outcomes.
- Optical Coatings: PVD is used to deposit thin films with specific optical properties, such as anti-reflective coatings on lenses and mirrors.
- Electronics: PVD plays a crucial role in the fabrication of electronic components, depositing conductive, insulating, or barrier layers.
Advantages of PVD Coatings:
- Superior Adhesion: PVD coatings exhibit excellent adhesion to the substrate, making them durable and resistant to delamination.
- Excellent Hardness and Wear Resistance: Many PVD coatings possess exceptional hardness and wear resistance, prolonging the lifespan of coated components.
- Enhanced Corrosion Resistance: PVD coatings can provide superior protection against corrosion, extending the service life of components in harsh environments.
- Precise Control over Film Thickness and Properties: PVD techniques allow for precise control over the film thickness, composition, and microstructure, resulting in tailored properties.
- Wide Range of Materials: PVD can be used to deposit a broad range of materials, enabling the creation of coatings with diverse properties.
Conclusion:
Physical Vapor Deposition is a powerful and versatile technology that continues to play a significant role in various industries. Its ability to create high-quality, durable, and precisely tailored coatings makes it an essential tool for enhancing the performance and lifespan of numerous components. As research and development continue, PVD is expected to play an even greater role in shaping future technologies.
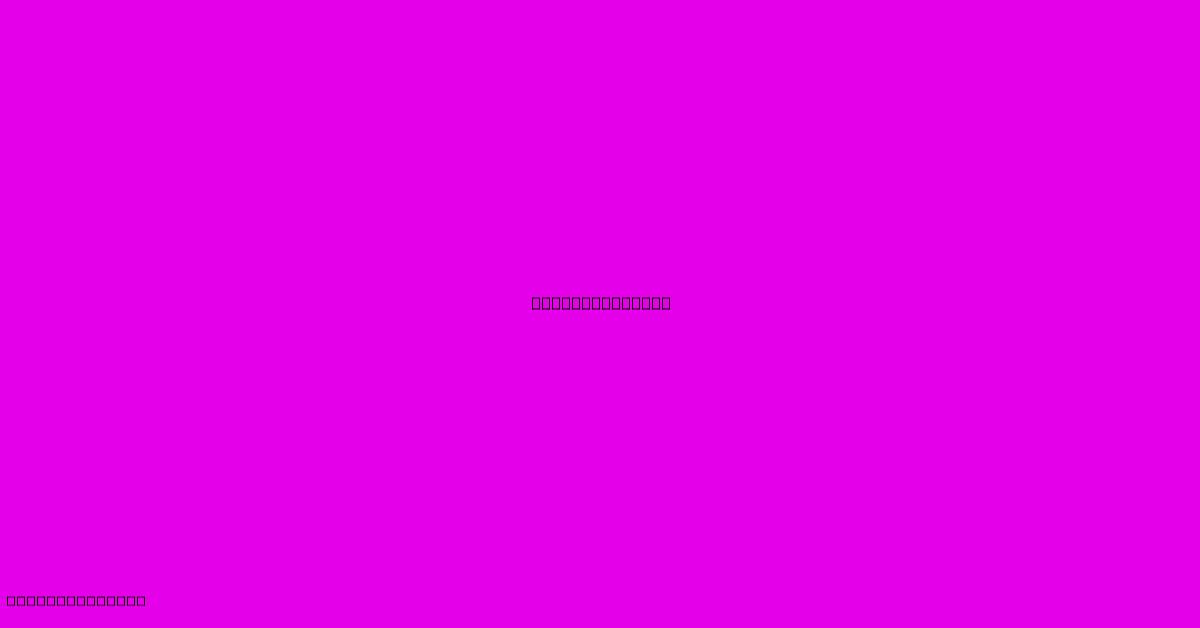
Thank you for visiting our website wich cover about Pvd Technology. We hope the information provided has been useful to you. Feel free to contact us if you have any questions or need further assistance. See you next time and dont miss to bookmark.
Featured Posts
-
Empoli Atalanta Minuto A Minuto
Dec 23, 2024
-
Wolves Vs Leicester Pereiras Dream Win
Dec 23, 2024
-
Kenan Yildiz Ile Juventus Un Zaferi
Dec 23, 2024
-
Rams Beat Jets 19 9 Recap
Dec 23, 2024
-
Cardinals Lose Playoff Bid Ends
Dec 23, 2024