Push In Technology
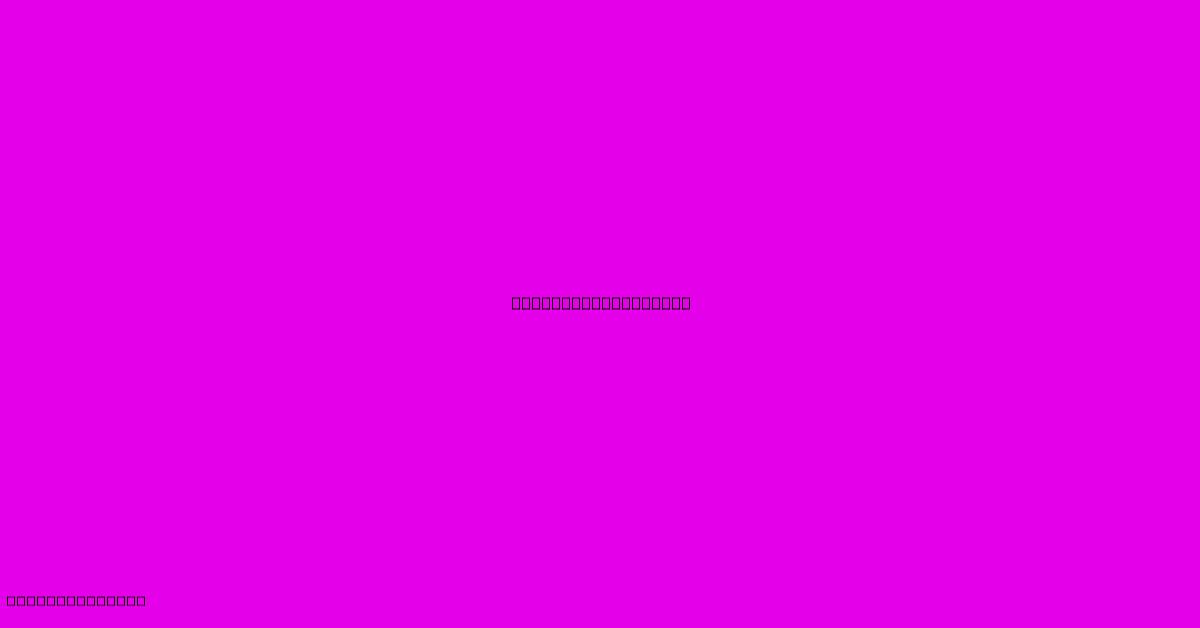
Discover more detailed and exciting information on our website. Click the link below to start your adventure: Visit Best Website mr.cleine.com. Don't miss out!
Table of Contents
Push-In Technology: Revolutionizing Manufacturing and Beyond
Push-in technology, a seemingly simple yet profoundly impactful innovation, is reshaping various industries by simplifying assembly processes and enhancing product design. This method, often referred to as push-fit technology or snap-fit technology, involves joining components without the need for screws, rivets, or adhesives. Instead, it utilizes precisely engineered parts that securely interlock when pushed together, creating a strong and reliable connection. Let's delve deeper into the mechanics, applications, advantages, and future potential of this revolutionary technology.
How Push-In Technology Works
The core principle behind push-in technology lies in the strategic design of mating components. One part features a precisely molded receptacle, often incorporating undercut features or spring clips, while the other possesses complementary protrusions or tabs. When the protruding part is pushed into the receptacle, the elastic deformation of the material within the receptacle creates a secure, often audible "click," indicating a successful connection. The design ensures a tight fit, resisting separation while still allowing for disassembly, albeit sometimes requiring more force.
Different techniques are employed to optimize push-in connections depending on the application and material properties:
- Undercuts: These recesses in the receptacle trap the protrusions, preventing disengagement.
- Spring clips: These flexible elements create a gripping action, enhancing holding power.
- Latches: These mechanisms provide additional security and prevent accidental disconnection.
The precision required in manufacturing push-in components is crucial for ensuring proper function and durability. Even slight deviations in dimensions can compromise the connection's strength and reliability.
Applications Across Industries
The versatility of push-in technology extends across numerous industries, impacting product design and manufacturing processes significantly:
1. Automotive: Used extensively in dashboards, interior trim, and other components, push-in technology reduces assembly time, minimizes weight, and improves aesthetics.
2. Electronics: Ideal for connecting circuit boards, housings, and other delicate components, it simplifies assembly and enhances reliability in consumer electronics, medical devices, and industrial equipment.
3. Appliances: From refrigerators to washing machines, push-in technology streamlines manufacturing, reduces production costs, and enhances the overall quality and durability of appliances.
4. Furniture: Modern furniture designs often incorporate push-in connections for quick assembly and easy disassembly, catering to modern lifestyles and efficient logistics.
5. Medical Devices: The ability to create sterile and reliable connections makes it suitable for various medical devices, improving safety and reducing assembly time in a clean-room environment.
Advantages of Push-In Technology
The popularity of push-in technology stems from its many advantages:
- Reduced Assembly Time: Significantly faster than traditional fastening methods.
- Lower Manufacturing Costs: Eliminates the need for fasteners, reducing material costs and labor expenses.
- Improved Aesthetics: Creates a cleaner, more seamless product design with fewer visible fasteners.
- Lightweight Designs: Reduces overall weight, especially beneficial in automotive and aerospace applications.
- Simplified Design: Streamlines the design process, simplifying product assembly and maintenance.
- Enhanced Reliability: When properly designed and manufactured, push-in connections provide a strong and reliable bond.
Challenges and Future Trends
While offering numerous benefits, push-in technology also presents some challenges:
- Design Complexity: Requires precise engineering and careful consideration of material properties and tolerances.
- Material Selection: The choice of materials significantly impacts the strength and durability of the connection.
- Fatigue and Wear: Repeated stress can lead to fatigue and weakening of the connection over time.
Future trends in push-in technology include:
- Advanced Materials: The use of high-performance polymers and composites will further enhance the strength and durability of push-in connections.
- Simulation and Optimization: Advanced simulation tools will enable more precise design and optimization of push-in components.
- Automated Assembly: Integration with automated assembly systems will increase efficiency and reduce production costs.
In conclusion, push-in technology represents a significant advancement in manufacturing and product design. Its versatility, efficiency, and cost-effectiveness continue to drive its adoption across various sectors. As technology advances, we can expect even more innovative applications and improvements to this transformative joining method.
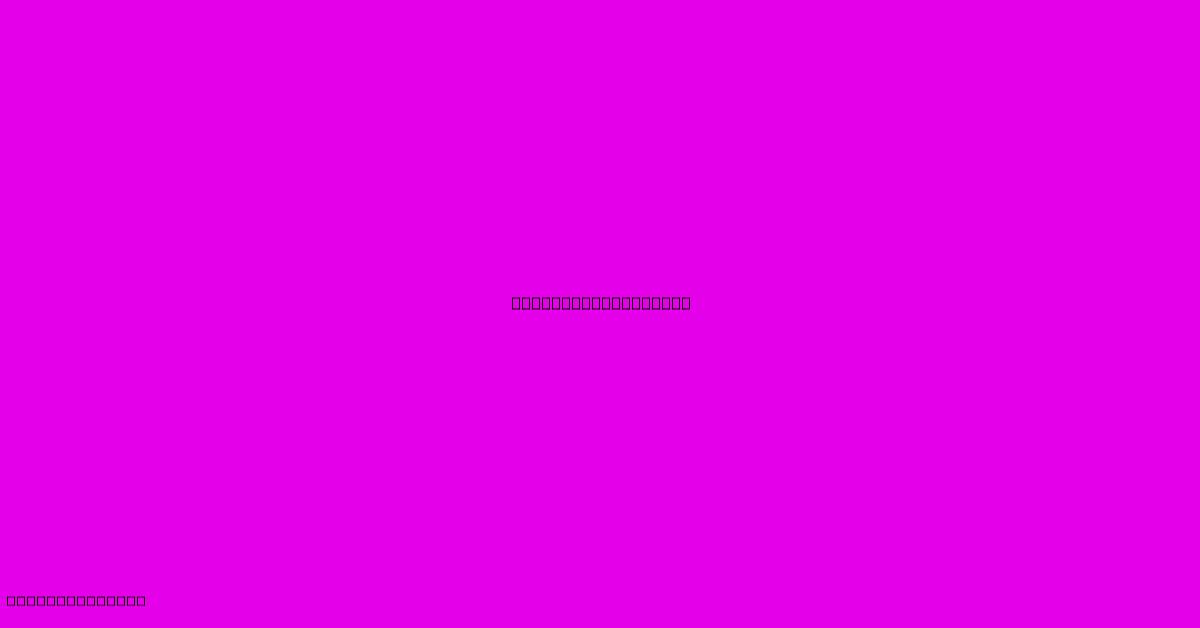
Thank you for visiting our website wich cover about Push In Technology. We hope the information provided has been useful to you. Feel free to contact us if you have any questions or need further assistance. See you next time and dont miss to bookmark.
Featured Posts
-
Lek Technology
Dec 28, 2024
-
Serge Atlaoui France Demande Son Retour
Dec 28, 2024
-
Khto Peremig U Kholostyaku 13 Divis Tut Zagolovok Intriguyuchiy Vikoristovuye Pitannya Scho Privablyuye Chitacha Ta Mistit Pryame Zaklikuvannya Do Diyi
Dec 28, 2024
-
Ss And C Technologies Glassdoor
Dec 28, 2024
-
Whats App Incompatibilidad Movil A Partir De Enero
Dec 28, 2024