Pultrusion Technology
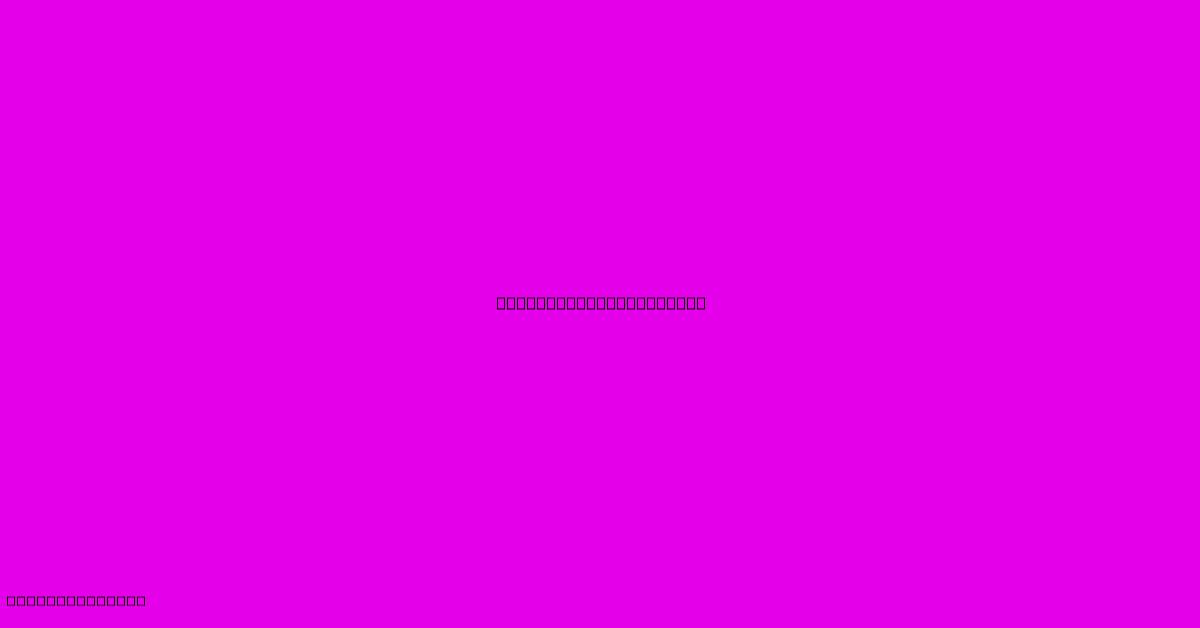
Discover more detailed and exciting information on our website. Click the link below to start your adventure: Visit Best Website mr.cleine.com. Don't miss out!
Table of Contents
Pultrusion Technology: A Comprehensive Guide
Pultrusion is a continuous manufacturing process used to create composite materials with a wide range of applications. Understanding its intricacies is key to appreciating its versatility and importance in various industries. This article provides a comprehensive overview of pultrusion technology, covering its process, advantages, limitations, and applications.
What is Pultrusion?
Pultrusion is a process that produces continuous composite profiles of constant cross-section. Think of it as a sophisticated "pull-through" method where reinforcing fibers are saturated with resin, then pulled through a heated die to cure and solidify into the desired shape. This creates strong, lightweight, and durable parts with exceptional design flexibility.
The Pultrusion Process: A Step-by-Step Breakdown
The pultrusion process involves several key stages:
-
Fiber Preparation: Reinforcement fibers, such as fiberglass, carbon fiber, aramid fiber, or basalt fiber, are fed into the process. These fibers are often pre-cut or supplied in continuous tows.
-
Resin Impregnation: The fibers are saturated with a thermosetting resin system, typically polyester, vinyl ester, epoxy, or polyurethane. This ensures proper bonding between the fibers and the matrix material.
-
Pulling Through the Die: The resin-impregnated fibers are pulled through a precisely engineered heated die. The die's shape determines the final profile of the composite material.
-
Curing: The heat within the die initiates the curing process of the resin, solidifying the composite material around the fibers. Careful temperature control is crucial for achieving optimal mechanical properties.
-
Cutting and Finishing: Once the material is cured, it's pulled from the die and cut to the desired length. Further finishing steps, such as sawing, sanding, or coating, might be employed.
Advantages of Pultrusion
Pultrusion offers numerous advantages over other composite manufacturing processes:
- High Production Rates: Pultrusion allows for the continuous production of composite profiles, leading to high output and cost-effectiveness.
- Precise Dimensional Control: The use of a die ensures consistent and precise dimensions for the final product.
- Excellent Mechanical Properties: The process creates strong, lightweight, and durable components with high strength-to-weight ratios.
- Versatile Material Options: A wide range of fiber and resin combinations can be utilized, enabling customization of the final product's properties.
- Long Length Profiles: Pultrusion can create profiles of virtually unlimited length, unlike other methods which are restricted by mold size.
Limitations of Pultrusion
While highly efficient, pultrusion has certain limitations:
- Cross-Section Limitations: The process is limited to creating parts with constant cross-sections. Complex shapes or variable cross-sections require more intricate and costly tooling.
- Tooling Costs: Developing custom dies for specific profiles can be expensive.
- Resin Selection: Not all resin systems are suitable for pultrusion. The resin must possess specific properties, such as good flow and cure characteristics.
Applications of Pultrusion
Pultrusion's versatility makes it suitable for a diverse range of applications across various industries:
- Construction: Pultruded profiles are used in structural applications, such as reinforcing bars, beams, and columns.
- Transportation: They find use in automotive parts, railway components, and marine structures.
- Infrastructure: Pultruded components are employed in bridges, walkways, and other infrastructure projects.
- Electrical and Telecommunications: Pultruded fiberglass poles and conduits are widely used for supporting electrical lines and cables.
- Sporting Goods: Pultrusion is utilized in the creation of fishing rods, hockey sticks, and other sporting equipment.
Future Trends in Pultrusion
Ongoing research and development are focused on improving the efficiency, versatility, and sustainability of the pultrusion process. This includes exploring new materials, optimizing resin systems, and developing advanced control systems for enhanced precision and quality.
Conclusion
Pultrusion technology plays a vital role in the manufacturing of high-performance composite materials. Its ability to produce strong, lightweight, and durable components at high production rates makes it an attractive and cost-effective solution for numerous industries. Understanding its capabilities and limitations is essential for leveraging its full potential in a wide array of applications.
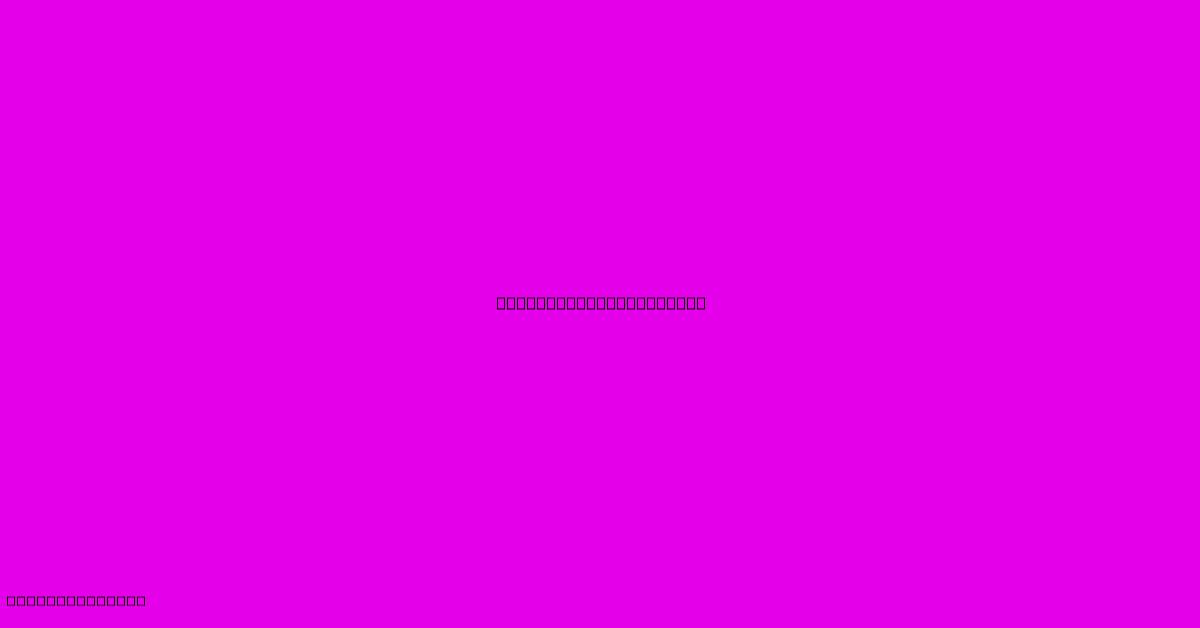
Thank you for visiting our website wich cover about Pultrusion Technology. We hope the information provided has been useful to you. Feel free to contact us if you have any questions or need further assistance. See you next time and dont miss to bookmark.
Featured Posts
-
Nihilism And Technology
Dec 31, 2024
-
Uk New Years Eve Dining Rise
Dec 31, 2024
-
Facebook Technology Stack
Dec 31, 2024
-
Player Ratings Ipswich 2 0 Chelsea Win
Dec 31, 2024
-
Sydney 2024 New Year Fireworks
Dec 31, 2024