Precision Tool Technologies
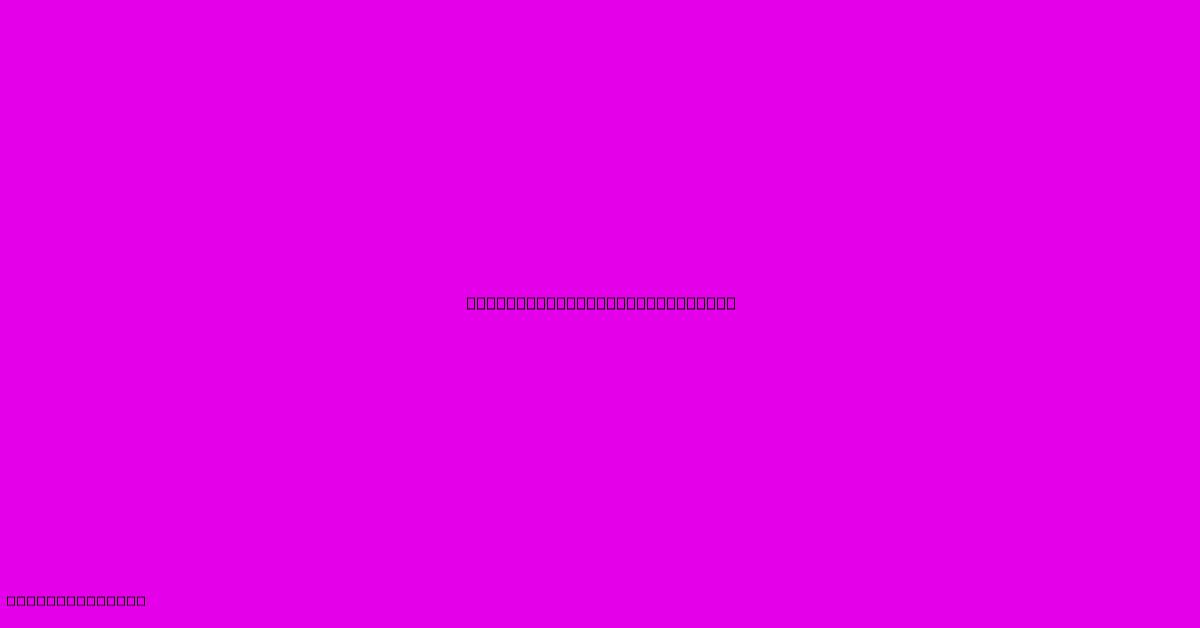
Discover more detailed and exciting information on our website. Click the link below to start your adventure: Visit Best Website mr.cleine.com. Don't miss out!
Table of Contents
Precision Tool Technologies: Shaping the Future of Manufacturing
Precision tool technologies are the backbone of modern manufacturing, enabling the creation of intricate components with unparalleled accuracy and efficiency. From microscopic components in electronics to large-scale parts in aerospace, these technologies are essential for producing high-quality, reliable products across diverse industries. This article delves into the key aspects of precision tool technologies, exploring their advancements, applications, and future trends.
Understanding Precision Tool Technologies
Precision tool technologies encompass a wide range of techniques and equipment designed to manufacture parts with extremely tight tolerances. This precision is achieved through the use of advanced materials, sophisticated manufacturing processes, and precise measurement systems. Key elements include:
-
Advanced Materials: The tools themselves are often crafted from exceptionally durable and wear-resistant materials like carbide, cermets, cubic boron nitride (CBN), and polycrystalline diamond (PCD). These materials ensure longevity and maintain dimensional accuracy even after extended use.
-
Sophisticated Manufacturing Processes: The creation of precision tools requires advanced manufacturing processes, including:
- CNC Machining: Computer Numerical Control (CNC) machining allows for highly precise and repeatable automated cutting and shaping of tools.
- Electro Discharge Machining (EDM): EDM uses electrical discharges to erode material, ideal for creating complex shapes and intricate details in hard-to-machine materials.
- Laser Cutting & Engraving: Laser technology offers precision cutting and engraving for creating intricate designs and features on tools.
- Grinding & Honing: Grinding and honing processes refine the surface finish of tools, ensuring smooth operation and extended lifespan.
-
Precise Measurement Systems: Quality control is paramount in precision tool technology. Advanced measurement systems, such as coordinate measuring machines (CMMs) and laser scanning systems, ensure that tools meet the required specifications and tolerances.
Applications Across Industries
The applications of precision tool technologies span numerous industries:
-
Aerospace: Precision tools are vital for manufacturing lightweight yet incredibly strong components for aircraft and spacecraft. The tolerances required are extremely tight, demanding the highest level of precision.
-
Automotive: From engine components to body panels, precision tools are essential for producing high-quality automotive parts. The efficiency and accuracy provided by these technologies contribute to the reliability and performance of vehicles.
-
Electronics: The miniaturization of electronic components requires incredibly precise tools for manufacturing microchips, circuit boards, and other delicate parts. Precision tool technologies are instrumental in the advancement of electronics.
-
Medical Devices: The production of medical devices demands the utmost precision. Precision tools are critical for creating implants, surgical instruments, and other components that require high accuracy and biocompatibility.
-
Energy: Precision tools play a significant role in manufacturing components for power generation, particularly in wind turbines and nuclear power plants. Their accuracy is crucial for ensuring the reliability and safety of these energy systems.
Future Trends in Precision Tool Technologies
The field of precision tool technology is constantly evolving. Several key trends are shaping its future:
-
Additive Manufacturing (3D Printing): 3D printing allows for the creation of complex tool geometries that would be impossible to produce using traditional methods. This opens up new possibilities for tool design and customization.
-
Artificial Intelligence (AI) and Machine Learning (ML): AI and ML are being integrated into precision tool technologies to optimize processes, improve accuracy, and predict tool wear. This leads to increased efficiency and reduced downtime.
-
Nanotechnology: The development of nanotechnology is enabling the creation of tools with unprecedented levels of precision, allowing for the manufacture of extremely small and intricate components.
-
Sustainable Materials and Processes: The industry is moving towards the use of more sustainable materials and processes, reducing environmental impact while maintaining high levels of precision.
Conclusion
Precision tool technologies are fundamental to modern manufacturing, driving innovation and enabling the production of high-quality goods across diverse sectors. Ongoing advancements in materials, processes, and measurement systems are continually pushing the boundaries of precision, ensuring that these technologies remain at the forefront of industrial progress. The future of precision tool technologies promises even greater accuracy, efficiency, and sustainability, shaping the next generation of manufacturing capabilities.
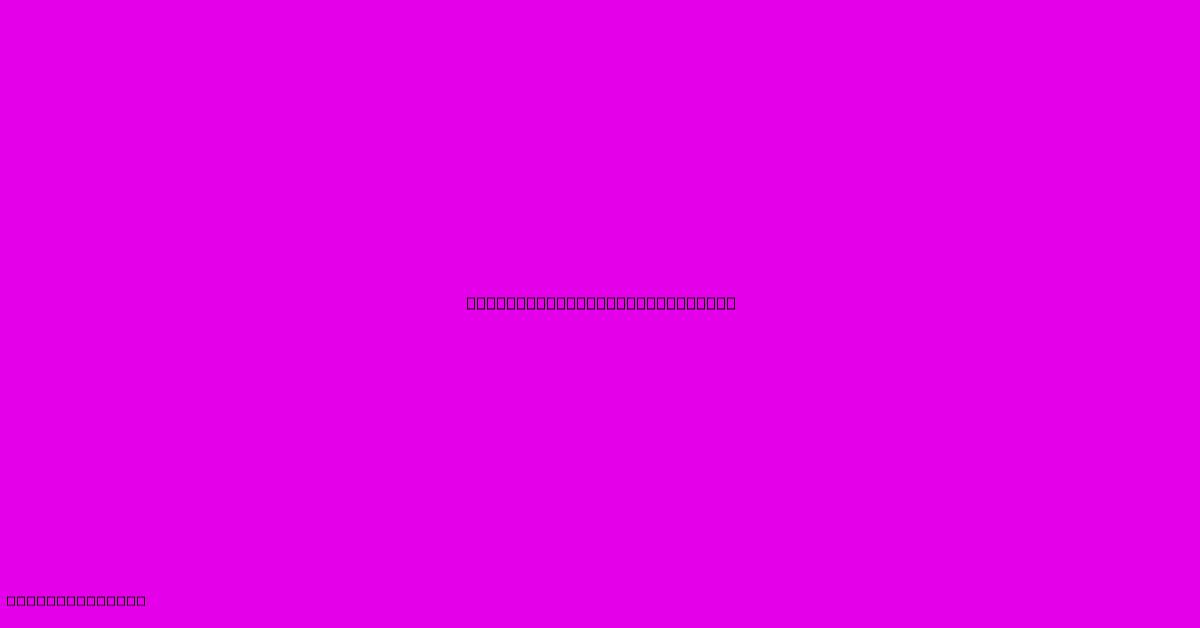
Thank you for visiting our website wich cover about Precision Tool Technologies. We hope the information provided has been useful to you. Feel free to contact us if you have any questions or need further assistance. See you next time and dont miss to bookmark.
Featured Posts
-
Masters In Information Technology Jobs
Jan 04, 2025
-
Educational Technology Specialist Jobs
Jan 04, 2025
-
Newgen Technology
Jan 04, 2025
-
Integra Technologies Wichita
Jan 04, 2025
-
Zapata Technologies
Jan 04, 2025