Precision Machining Technology
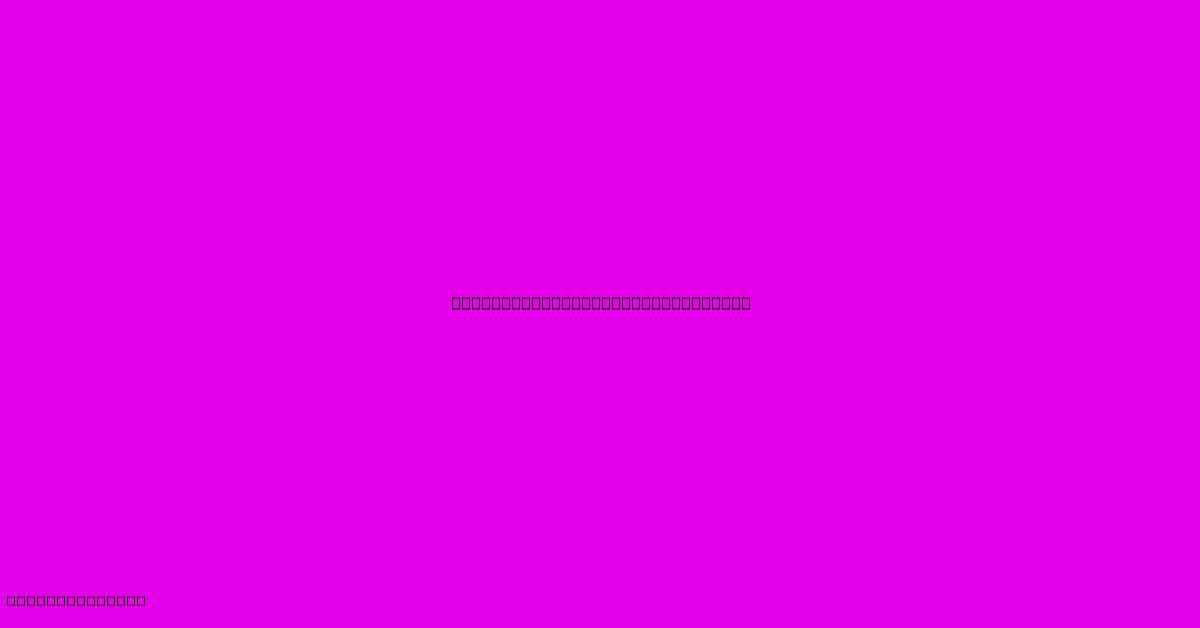
Discover more detailed and exciting information on our website. Click the link below to start your adventure: Visit Best Website mr.cleine.com. Don't miss out!
Table of Contents
Precision Machining Technology: Achieving Micron-Level Accuracy
Precision machining is a critical manufacturing process that produces parts with extremely tight tolerances, often measured in microns (millionths of a meter). This level of accuracy is essential for a wide range of industries, from aerospace and medical devices to automotive and electronics. This article delves into the technology, processes, and applications of precision machining.
Understanding Precision Machining
Precision machining goes beyond standard machining techniques. It demands sophisticated machinery, highly skilled operators, and meticulous quality control. The goal is not just to remove material, but to create parts with dimensional accuracy, surface finish, and geometric form that meet stringent specifications. This often involves specialized tooling, advanced computer numerical control (CNC) machines, and precise measurement systems.
Key Processes in Precision Machining
Several key processes contribute to achieving precision in machining:
1. CNC Machining: Computer Numerical Control (CNC) machining is the backbone of precision machining. CNC machines use computer programs to control the movement of cutting tools, ensuring consistent and repeatable accuracy. Different types of CNC machining include:
- Milling: Removes material from a workpiece using rotating cutters. Precision milling involves advanced techniques like high-speed machining (HSM) for improved surface finish and reduced tool wear.
- Turning: Shapes a workpiece by rotating it against a cutting tool. Precision turning is crucial for creating cylindrical parts with precise diameters and lengths.
- Drilling: Creates holes in a workpiece using drills of varying sizes and shapes. Precision drilling requires sophisticated techniques to ensure accurate hole placement and size.
- Grinding: Uses abrasive wheels to remove small amounts of material, achieving extremely fine surface finishes and high dimensional accuracy.
2. Electro Discharge Machining (EDM): EDM uses electrical discharges to erode material from a workpiece, enabling the creation of complex shapes and extremely fine details in hard-to-machine materials.
3. Laser Machining: Employs a high-powered laser beam to precisely cut, engrave, or mark materials. Laser machining offers high precision and minimal heat-affected zones.
4. Wire EDM: A specialized form of EDM that uses a thin wire electrode to cut intricate shapes in conductive materials.
Materials Commonly Used in Precision Machining
The choice of material greatly influences the final product's properties and the machining process itself. Common materials used include:
- Metals: Aluminum, stainless steel, titanium alloys, and various specialty alloys are frequently machined to create high-strength, durable components.
- Plastics: Certain plastics offer high precision and dimensional stability, making them suitable for many applications.
- Ceramics: Used when high hardness, wear resistance, and thermal stability are required.
Applications of Precision Machining
The versatility of precision machining makes it applicable across numerous industries:
- Aerospace: Creating lightweight yet incredibly strong components for aircraft and spacecraft.
- Medical Devices: Manufacturing precise implants, surgical instruments, and microfluidic devices.
- Automotive: Producing high-precision engine components, transmission parts, and other critical components.
- Electronics: Creating intricate components for computers, smartphones, and other electronic devices.
- Optics: Producing lenses, mirrors, and other optical components with exceptional surface quality and dimensional accuracy.
Quality Control and Measurement
Ensuring the quality of precision-machined parts requires rigorous quality control measures:
- Dimensional Inspection: Using advanced measuring equipment like coordinate measuring machines (CMMs) and optical comparators to verify the dimensions of the machined parts.
- Surface Finish Inspection: Assessing the surface roughness and texture to ensure it meets the specified requirements.
- Material Testing: Analyzing the material properties to ensure they meet the desired standards.
The Future of Precision Machining
Advancements in technology continue to push the boundaries of precision machining. Developments like:
- Additive Manufacturing (3D Printing): Offers new possibilities for creating complex shapes and internal features previously impossible with traditional machining.
- Artificial Intelligence (AI) and Machine Learning (ML): Enhancing machine control, predicting tool wear, and optimizing machining parameters for improved efficiency and accuracy.
Precision machining is a crucial technology driving innovation in various fields. Its ability to produce parts with micron-level accuracy is essential for creating high-performance, reliable, and advanced products across diverse industries. As technology evolves, the capabilities of precision machining will undoubtedly continue to advance, pushing the limits of what's possible in manufacturing.
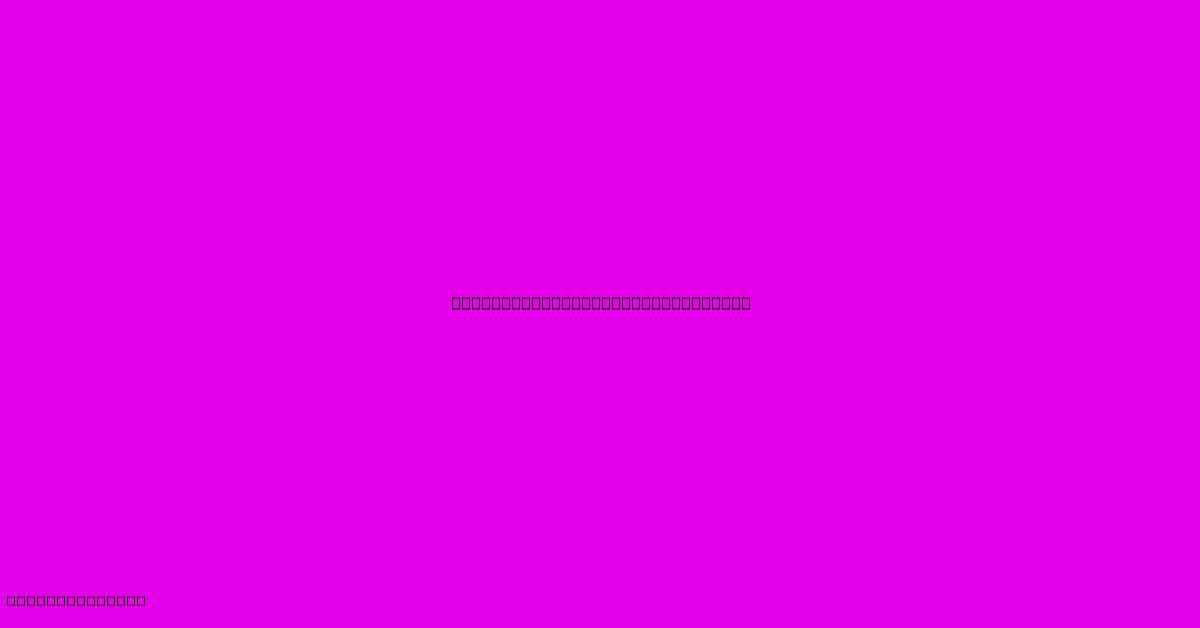
Thank you for visiting our website wich cover about Precision Machining Technology. We hope the information provided has been useful to you. Feel free to contact us if you have any questions or need further assistance. See you next time and dont miss to bookmark.
Featured Posts
-
Northern Lights Technology
Dec 21, 2024
-
Timberland Pro Mens Anti Fatigue Technology Replacement Insole
Dec 21, 2024
-
Titan Technologies Jobs
Dec 21, 2024
-
Utang Triliunan Antv Lakukan Phk Massal
Dec 21, 2024
-
The Voice Kids Melissa Memeti Ha Vinto
Dec 21, 2024