Powder Coating Technologies
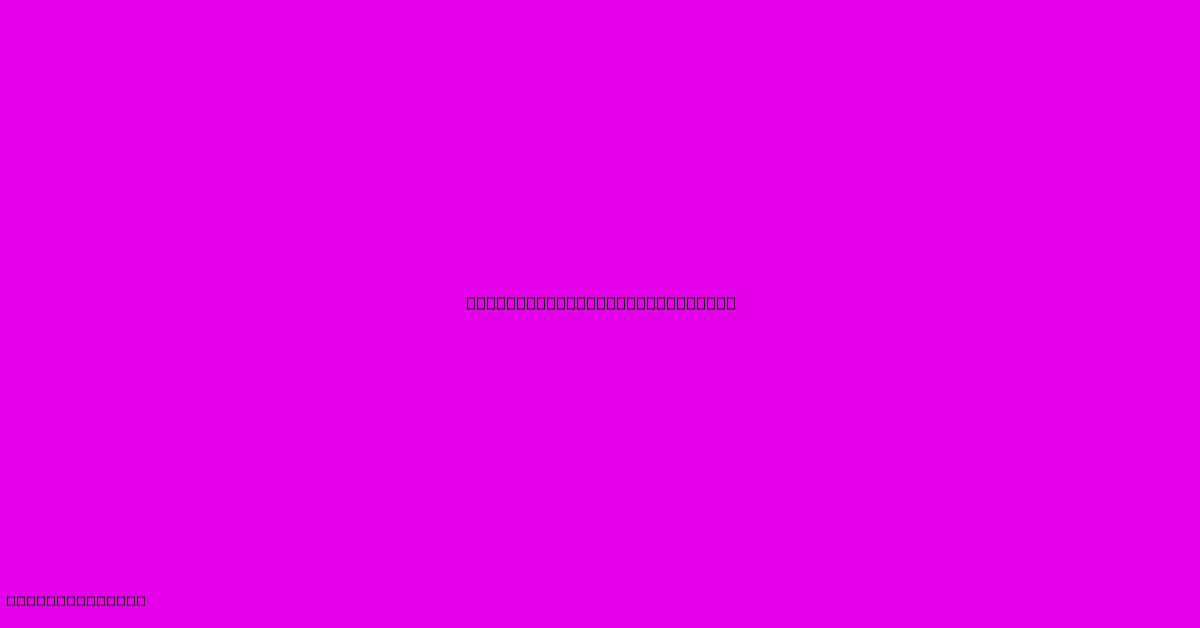
Discover more detailed and exciting information on our website. Click the link below to start your adventure: Visit Best Website mr.cleine.com. Don't miss out!
Table of Contents
Powder Coating Technologies: A Comprehensive Guide
Powder coating is a durable and aesthetically pleasing finish applied to a wide range of materials, from metal furniture to automotive parts. Unlike liquid paint, powder coating uses finely ground powder that is electrostatically charged and then cured under heat. This process delivers a superior finish known for its resilience and longevity. This article delves into the various technologies involved in powder coating, exploring the process, advantages, and applications.
Understanding the Powder Coating Process
The powder coating process involves several key stages:
1. Pre-treatment: This crucial initial step prepares the substrate for optimal adhesion. Methods include:
- Degreasing: Removing oils, grease, and other contaminants using solvents or alkaline cleaners.
- Phosphate Conversion Coating: Creating a crystalline phosphate layer on the metal surface to enhance corrosion resistance and paint adhesion.
- Chromate Conversion Coating: (Less common due to environmental concerns) Forms a chromate layer for excellent corrosion protection and adhesion.
2. Powder Application: The pre-treated substrate is then coated with the powder. Common application methods include:
- Electrostatic Spraying: The most widely used method. Powder is charged and sprayed onto the grounded substrate, adhering due to electrostatic attraction. This allows for even coating and minimal waste.
- Fluidized Bed Coating: The substrate is immersed in a fluidized bed of powder, which is agitated by air. This method is suitable for complex shapes and provides a uniform coating.
- Electrostatic Fluidized Bed Coating: Combines the advantages of both electrostatic spraying and fluidized bed coating for superior efficiency and coating quality.
3. Curing: After application, the coated part is cured in an oven at high temperatures (typically 350-400°F or 175-200°C). This process melts the powder, allowing it to flow and form a continuous, uniform film. The exact curing temperature and time depend on the type of powder and the desired properties of the coating.
4. Post-Cure Operations (Optional): Depending on the application, additional steps may be necessary, including:
- Inspection: To ensure the quality and uniformity of the coating.
- Packaging: For protection during transport and storage.
Types of Powder Coatings
Powder coatings are available in a wide range of formulations, each with unique properties:
- Polyester: A versatile and widely used type, offering good UV resistance, color retention, and flexibility.
- Epoxy: Known for its excellent chemical resistance and hardness, often used in industrial applications.
- Hybrid (Polyester/Epoxy): Combines the benefits of both polyester and epoxy, offering a balance of durability, flexibility, and chemical resistance.
- Acrylic: Offers good flexibility and UV resistance, ideal for applications requiring a smooth finish.
- Urethane: Provides exceptional durability, scratch and abrasion resistance, making it suitable for high-impact environments.
Advantages of Powder Coating
Powder coating offers several advantages over traditional liquid painting:
- Superior Durability: Powder coatings are extremely resistant to chipping, scratching, and fading.
- Excellent Corrosion Protection: They offer superior protection against rust and corrosion.
- Environmentally Friendly: Powder coatings are low in volatile organic compounds (VOCs), making them a more environmentally responsible choice.
- Cost-Effective: Less waste and faster curing times can lead to significant cost savings.
- Wide Range of Colors and Finishes: Available in a vast array of colors, textures, and finishes, offering extensive design possibilities.
Applications of Powder Coating
The versatility of powder coating makes it suitable for a wide range of applications, including:
- Automotive Parts: Wheels, bumpers, and other exterior components.
- Appliances: Refrigerators, washing machines, and other household appliances.
- Furniture: Metal chairs, tables, and other outdoor furniture.
- Industrial Equipment: Machinery, tools, and other industrial components.
- Architectural Products: Metal railings, doors, and window frames.
Conclusion
Powder coating technology offers a superior, durable, and environmentally friendly finish for a diverse range of applications. Understanding the various technologies involved, from pre-treatment to curing, allows for optimal selection of the right process and powder coating type for specific requirements. The ongoing evolution of powder coating technologies promises even more innovative and sustainable solutions in the future.
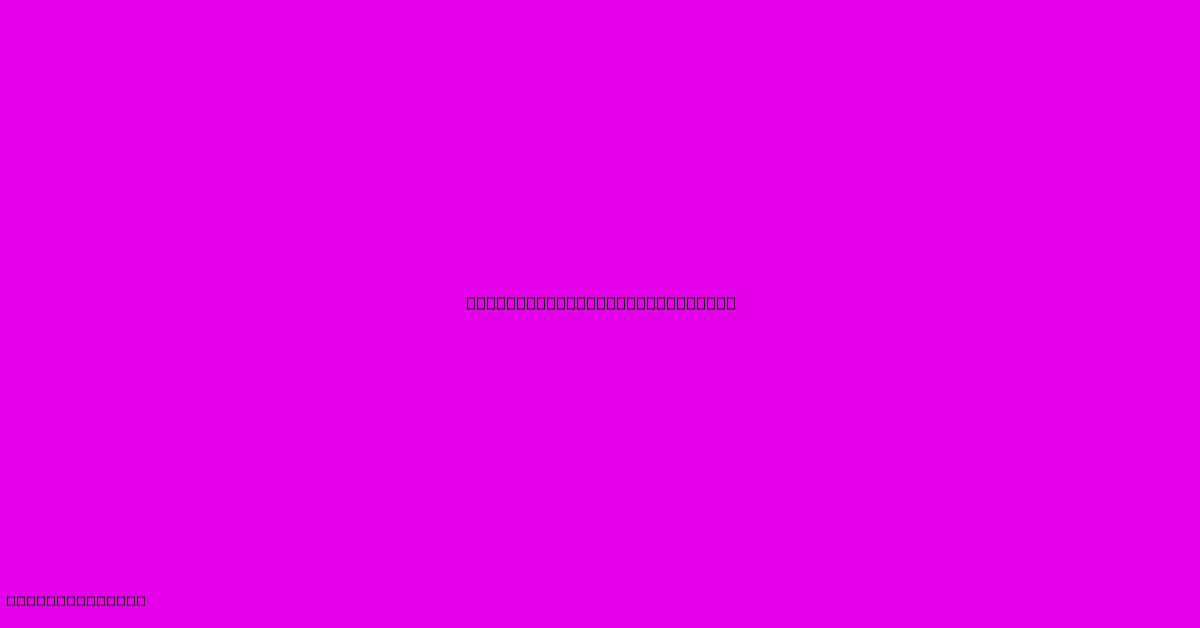
Thank you for visiting our website wich cover about Powder Coating Technologies. We hope the information provided has been useful to you. Feel free to contact us if you have any questions or need further assistance. See you next time and dont miss to bookmark.
Featured Posts
-
Week 16 Nfl Standings Afc And Nfc
Dec 23, 2024
-
European Football Madrids Ascent
Dec 23, 2024
-
En Directo Tottenham Vs Liverpool
Dec 23, 2024
-
Commanders Beat Eagles 36 32
Dec 23, 2024
-
Ponte Tocantins Maranhao Desaba Vitimas
Dec 23, 2024