Polyjet Technology
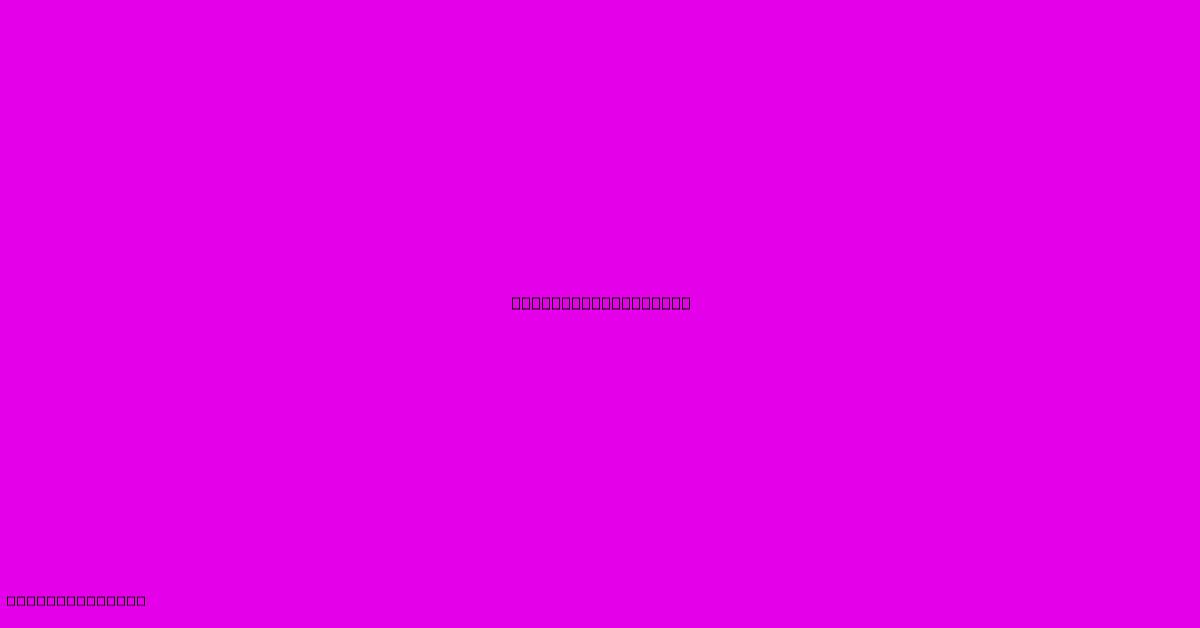
Discover more detailed and exciting information on our website. Click the link below to start your adventure: Visit Best Website mr.cleine.com. Don't miss out!
Table of Contents
PolyJet Technology: A Deep Dive into High-Resolution 3D Printing
PolyJet technology is a leading additive manufacturing (AM) process renowned for its ability to produce incredibly detailed and accurate 3D printed parts. Unlike other technologies that build layer by layer with melted material, PolyJet utilizes a unique photopolymerization process, offering unmatched precision and versatility. This article delves into the intricacies of PolyJet, exploring its strengths, limitations, and diverse applications.
How PolyJet Technology Works:
At the heart of PolyJet lies a printhead that precisely jets photopolymer resins onto a build tray. These liquid resins are cured almost instantly by exposure to UV light, building the 3D model layer by layer with microscopic accuracy. The process is similar to inkjet printing, but instead of ink, it uses highly specialized photopolymers. This allows for the creation of intricate geometries, fine details, and complex internal structures. A key advantage is the ability to use multiple materials simultaneously, creating parts with different properties within a single print.
Key aspects of the PolyJet process include:
- High Resolution: PolyJet boasts extremely high resolution, enabling the creation of parts with incredibly fine details, smooth surfaces, and precise dimensions. This is particularly beneficial for applications requiring intricate features or realistic textures.
- Multiple Material Printing: The ability to use different materials in a single print allows for the creation of functional prototypes with varying stiffness, flexibility, color, and transparency. This opens doors to more realistic simulations and advanced product development.
- Fast Build Speeds: Compared to some other additive manufacturing technologies, PolyJet offers relatively fast build speeds, making it suitable for rapid prototyping and low-volume production runs.
- Support Structures: PolyJet uses water-soluble support structures, which are easily removed after printing, leaving clean and finished parts. This simplifies post-processing and reduces the risk of damaging delicate features.
- Variety of Materials: A wide range of materials are available, catering to specific mechanical properties, aesthetics, and applications. Options range from rigid materials for structural components to flexible materials for soft goods simulations.
Advantages of PolyJet 3D Printing:
- Exceptional Detail and Accuracy: Ideal for applications demanding high precision, such as intricate jewelry, dental models, and medical devices.
- Multi-material Capabilities: Allows for the creation of parts with integrated functionalities and realistic simulations.
- Smooth Surface Finish: Requires minimal post-processing for a high-quality finish.
- Rapid Prototyping: Suitable for quickly creating functional prototypes and testing designs.
- Biocompatibility (Specific Materials): Some PolyJet materials are biocompatible, making them suitable for medical applications.
Limitations of PolyJet 3D Printing:
- Material Properties: While versatile, PolyJet materials generally exhibit lower strength and durability compared to materials used in other AM processes like SLS or SLA.
- Cost: The cost of PolyJet printers and materials is relatively high compared to other 3D printing technologies.
- Post-curing: Parts often require post-curing to enhance durability and stability.
- Limited Scalability: While suitable for rapid prototyping and low-volume production, PolyJet might not be the most cost-effective solution for large-scale manufacturing.
Applications of PolyJet Technology:
PolyJet's versatility makes it applicable across a wide range of industries:
- Healthcare: Dental models, surgical guides, anatomical models, hearing aids.
- Automotive: Concept models, functional prototypes, interior design mock-ups.
- Aerospace: Detailed models, functional prototypes, tooling.
- Consumer Products: Product design prototypes, mock-ups, and small-batch production.
- Jewelry: Detailed jewelry designs and prototypes.
Conclusion:
PolyJet 3D printing offers a unique blend of high resolution, speed, and material versatility. While cost and material limitations exist, its ability to produce highly detailed and accurate parts makes it an invaluable tool for rapid prototyping, design verification, and low-volume manufacturing across diverse industries. The technology continues to evolve, with ongoing improvements in material properties and print speeds promising even greater capabilities in the future.
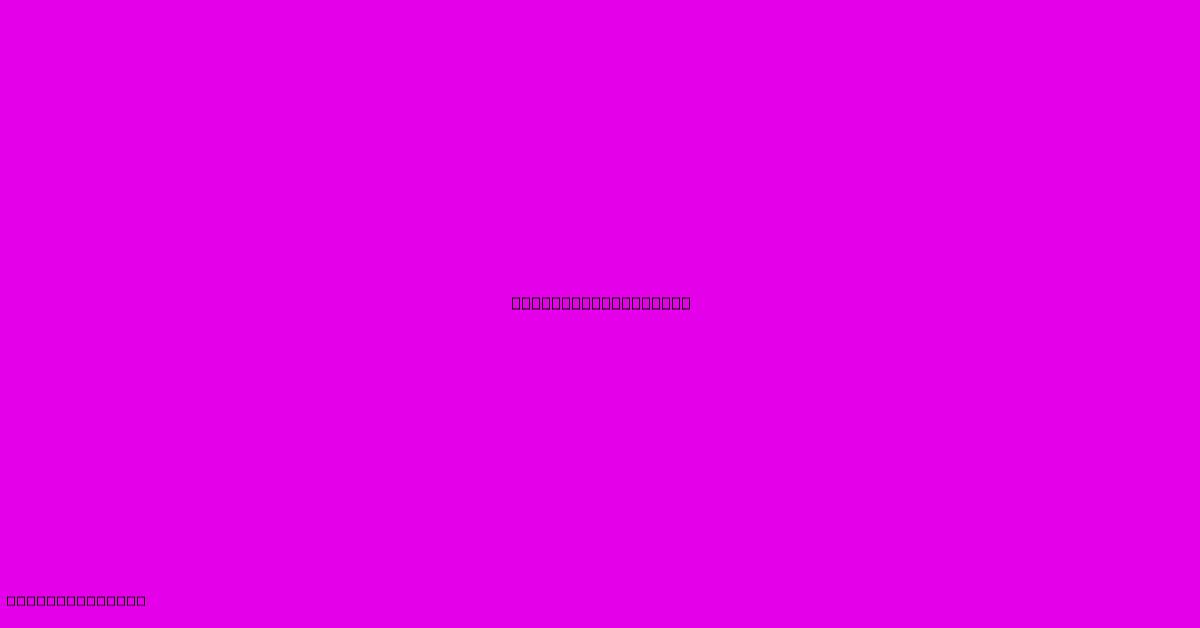
Thank you for visiting our website wich cover about Polyjet Technology. We hope the information provided has been useful to you. Feel free to contact us if you have any questions or need further assistance. See you next time and dont miss to bookmark.
Featured Posts
-
New Years Eve 2024 Australia Countdown
Dec 31, 2024
-
Motion Control Technology
Dec 31, 2024
-
Business Process Technologies
Dec 31, 2024
-
Graver Technologies Inc
Dec 31, 2024
-
Brighton Villa Match Penalty Debate
Dec 31, 2024