Pneumatic Technology
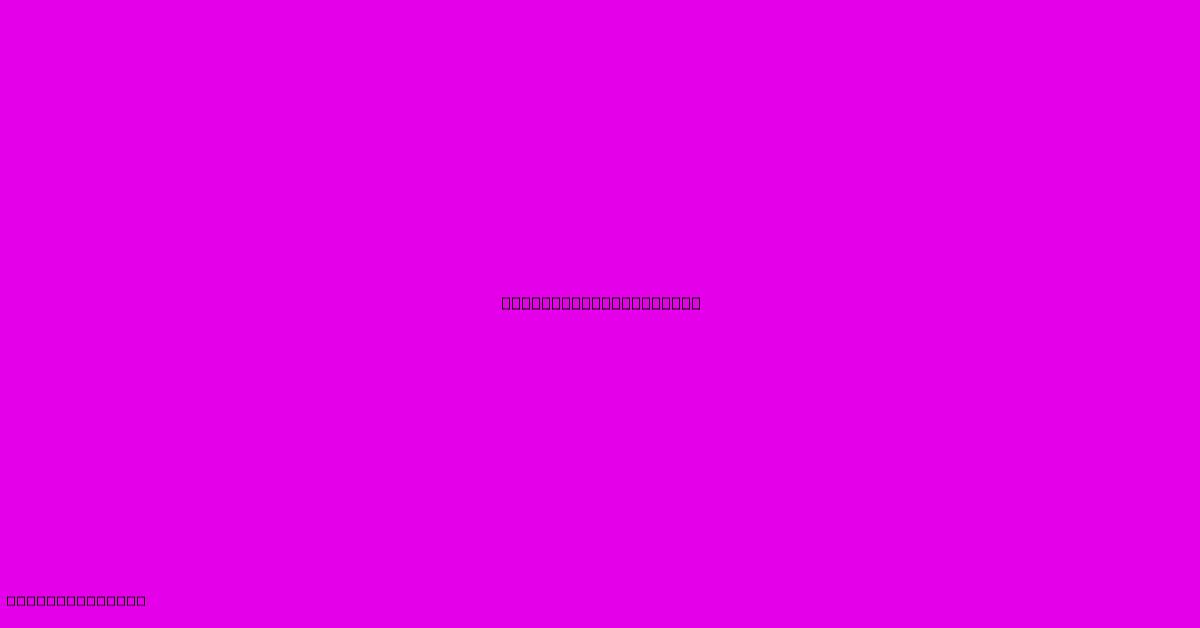
Discover more detailed and exciting information on our website. Click the link below to start your adventure: Visit Best Website mr.cleine.com. Don't miss out!
Table of Contents
Understanding Pneumatic Technology: Powering Industries with Compressed Air
Pneumatic technology harnesses the power of compressed air to perform a wide range of tasks across various industries. From powering heavy machinery in manufacturing to delicate movements in medical devices, its versatility and reliability make it a cornerstone of modern engineering. This article delves into the fundamentals of pneumatic systems, exploring their components, applications, advantages, and disadvantages.
What is Pneumatic Technology?
Pneumatic systems use compressed air as a power source to generate mechanical motion. Unlike hydraulic systems which use liquids, pneumatics relies on the compressibility of air, allowing for energy storage and controlled release. This compressed air is generated by a compressor and then channeled through a network of tubes, valves, and actuators to perform the desired function.
Key Components of a Pneumatic System:
- Air Compressor: The heart of the system, compressing atmospheric air to a higher pressure. Different types exist, each suited to specific needs and pressure requirements.
- Air Receiver Tank: Stores compressed air, providing a buffer to smooth out pressure fluctuations and ensure a consistent supply.
- Air Treatment Units: Filters, regulators, and lubricators clean, regulate, and lubricate the compressed air, protecting components from damage and ensuring optimal performance.
- Valves: Control the flow and direction of compressed air, enabling precise manipulation of actuators. Solenoid valves, often controlled electrically, are commonly used.
- Actuators: Convert the energy of compressed air into mechanical motion. Common types include pneumatic cylinders (linear motion) and rotary actuators (rotary motion).
- Tubing and Fittings: Connect the various components, ensuring the efficient and safe flow of compressed air.
Advantages of Pneumatic Systems:
- Safety: Compressed air is generally safer than hydraulic fluid in many applications, reducing fire and environmental hazards.
- Simplicity and Reliability: Pneumatic systems are relatively simple to design, install, and maintain, with fewer components prone to failure compared to some other technologies.
- Cost-Effectiveness: The initial investment and maintenance costs are often lower compared to hydraulic or electric systems, especially for simpler applications.
- Cleanliness: Suitable for applications where cleanliness is paramount, as compressed air leaves no residue.
- Versatility: Pneumatic systems can be adapted to a wide range of applications and easily integrated with other technologies.
Disadvantages of Pneumatic Systems:
- Energy Efficiency: Compressed air systems can be less energy-efficient than electric or hydraulic systems, especially for high-power applications. Energy loss during compression can be significant.
- Noise: Compressed air systems can be noisy, requiring sound dampening measures in some instances.
- Temperature Sensitivity: The performance of pneumatic systems can be affected by temperature variations.
- Limited Force: Compared to hydraulic systems, pneumatic systems typically generate lower forces for a given size and pressure.
- Environmental Concerns: The energy consumption for air compression can contribute to environmental impact.
Applications of Pneumatic Technology:
The versatility of pneumatic technology makes it applicable across numerous sectors:
- Manufacturing: Automation of assembly lines, robotic arms, material handling, and machine control.
- Automotive: Tire inflation, braking systems, and various assembly processes.
- Food and Beverage: Packaging, material handling, and process control.
- Medical: Surgical tools, prosthetic devices, and respiratory equipment.
- Aerospace: Flight control systems, landing gear, and other critical functions.
Future Trends in Pneumatic Technology:
The field is constantly evolving, with innovations focusing on:
- Increased Energy Efficiency: New compressor designs and system optimization strategies are continuously being developed.
- Improved Control and Precision: Advances in valve technology and control systems enable finer control over pneumatic actuators.
- Integration with other Technologies: Pneumatic systems are increasingly being integrated with electronics, robotics, and other automation technologies.
- Miniaturization: The development of smaller, more compact pneumatic components is expanding the range of applications.
In conclusion, pneumatic technology offers a robust and versatile solution for a wide spectrum of industrial and commercial applications. While it has certain limitations, ongoing advancements are continuously improving its efficiency, precision, and overall performance, ensuring its continued relevance in the years to come. Understanding its fundamentals and capabilities is crucial for engineers and technicians working in various industries.
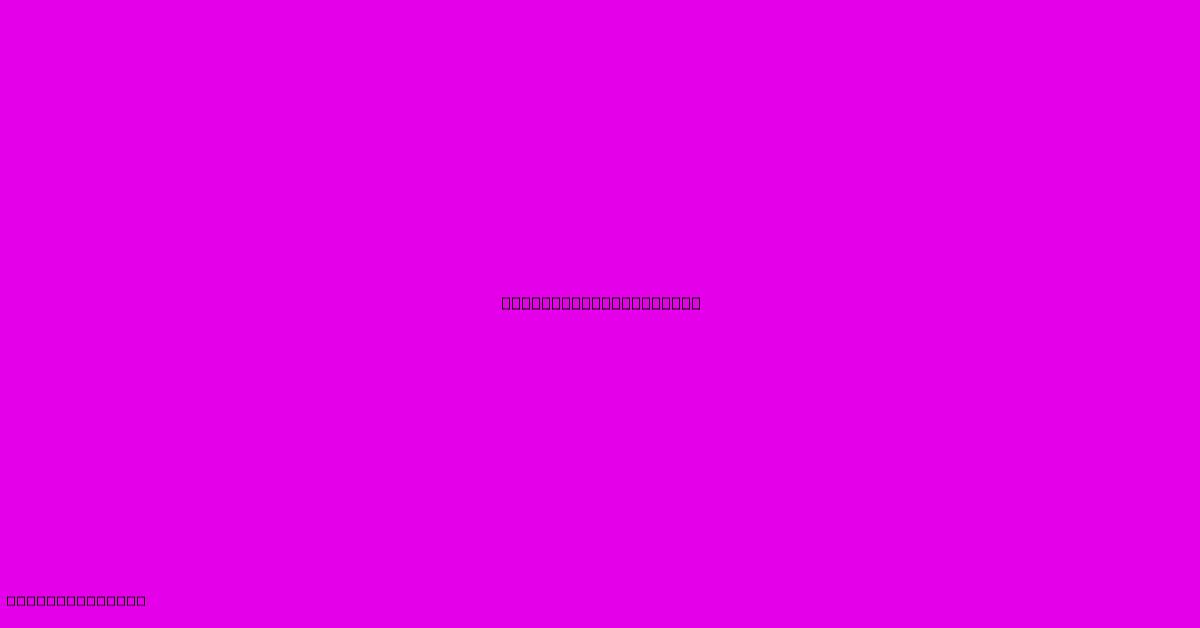
Thank you for visiting our website wich cover about Pneumatic Technology. We hope the information provided has been useful to you. Feel free to contact us if you have any questions or need further assistance. See you next time and dont miss to bookmark.
Featured Posts
-
Mo Salah Pecahkan Rekor Luis Suarez Vs West Ham
Dec 30, 2024
-
Wind And Snow Warning East Yorkshire
Dec 30, 2024
-
Summit Technologies Inc
Dec 30, 2024
-
Ssi Technology
Dec 30, 2024
-
Smart Construction Technology
Dec 30, 2024