Plating Technology
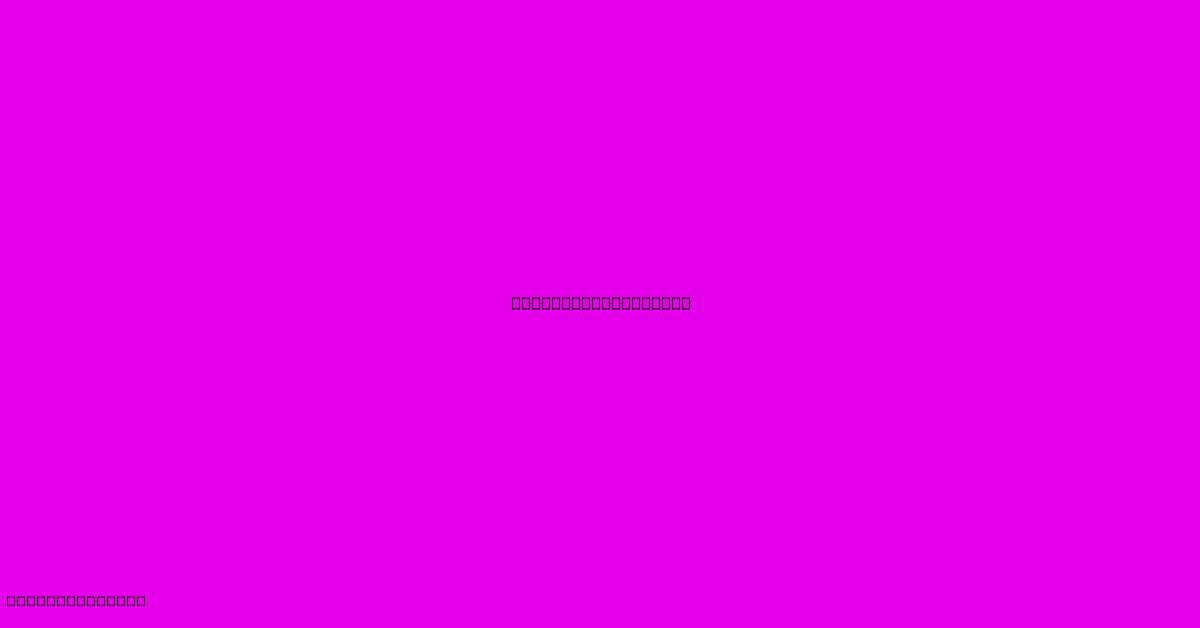
Discover more detailed and exciting information on our website. Click the link below to start your adventure: Visit Best Website mr.cleine.com. Don't miss out!
Table of Contents
Plating Technology: A Deep Dive into Surface Enhancement
Plating technology, also known as electrodeposition, is a crucial process in various industries, offering a cost-effective and efficient method for enhancing the surface properties of materials. This process involves depositing a thin layer of a metal or other material onto a substrate, resulting in improved aesthetics, corrosion resistance, wear resistance, and other desirable characteristics. This article will explore the intricacies of plating technology, encompassing its diverse applications, underlying principles, and future trends.
The Science Behind Plating:
At the heart of plating lies electrochemistry. The process typically involves immersing a substrate (the object to be plated) into an electrolyte solution containing the desired plating metal ions. An electric current is then passed through the solution, causing the metal ions to migrate to the cathode (the substrate) and deposit as a solid layer. The anode, often made of the same plating metal, provides the source of ions.
Several factors influence the quality and properties of the resulting plating:
-
Electrolyte Composition: The choice of electrolyte is crucial, as it dictates the deposition rate, plating efficiency, and the microstructure of the deposited layer. Different electrolytes are used for different metals and desired properties.
-
Current Density: The amount of current applied per unit area affects the plating rate and the quality of the deposit. Too high a current density can lead to a porous or rough deposit, while too low a current density may result in slow plating or non-uniform coverage.
-
Temperature: Temperature influences the solubility of metal ions in the electrolyte and the rate of the chemical reactions. Careful temperature control is necessary to optimize the plating process.
-
pH: The pH of the electrolyte significantly impacts the deposition rate and the quality of the deposit.
-
Substrate Preparation: Proper cleaning and pre-treatment of the substrate are essential for ensuring good adhesion of the plating layer. This often involves processes such as degreasing, pickling, and activation.
Types of Plating Processes:
Various plating techniques exist, each tailored to specific applications and materials:
-
Electroplating: The most common method, using an electric current to deposit the metal.
-
Electroless Plating: This chemical plating process doesn't require an external electric current; the metal is reduced by a chemical reducing agent in the solution. It's often used for uniform coating of complex shapes.
-
Immersion Plating: A displacement plating process where a more reactive metal displaces a less reactive metal from the solution, creating a thin plating layer.
-
Brush Plating: A localized plating method where the plating solution is applied directly to the surface using a brush-like electrode.
Commonly Plated Metals and Their Applications:
Plating technologies are utilized across diverse industries:
-
Chromium Plating: Known for its high hardness, corrosion resistance, and aesthetic appeal, chromium plating is used on automotive parts, plumbing fixtures, and decorative items.
-
Nickel Plating: Offers good corrosion resistance and a smooth finish, commonly used as an undercoat for other platings or as a decorative finish itself.
-
Zinc Plating: Provides excellent corrosion protection, particularly for steel, widely used in fasteners, automotive parts, and hardware.
-
Gold Plating: Used in electronics for its excellent conductivity and corrosion resistance, also used in jewelry for its decorative value.
-
Silver Plating: Valued for its high electrical conductivity and reflectivity, used in electrical contacts and mirrors.
Advantages and Disadvantages of Plating:
Advantages:
- Improved Corrosion Resistance: Protects the base metal from environmental degradation.
- Enhanced Wear Resistance: Increases the lifespan of components subject to wear and tear.
- Improved Appearance: Offers aesthetic appeal and a high-quality finish.
- Cost-Effective: Often a more economical solution than using solid materials.
- Versatile: Can be applied to a wide range of substrates and materials.
Disadvantages:
- Potential for Environmental Concerns: Some plating solutions contain hazardous chemicals that require careful disposal.
- Limited Thickness: Plating layers are typically thin, so heavy wear or corrosion can eventually damage the base metal.
- Stress and Hydrogen Embrittlement: Some plating processes can introduce stress or hydrogen embrittlement into the substrate, affecting its mechanical properties.
Future Trends in Plating Technology:
Research and development in plating technology are continuously improving its efficiency, sustainability, and capabilities:
- Green Plating: Development of environmentally friendly plating solutions and processes that minimize waste and harmful chemical use.
- Nanotechnology in Plating: Incorporating nanoparticles into the plating bath to enhance the properties of the resulting deposit.
- Pulse Plating: Using pulsed current instead of direct current to improve the quality and efficiency of the plating process.
- Advanced Surface Characterization Techniques: Utilizing sophisticated analytical tools to better understand and control the plating process.
In conclusion, plating technology remains a vital surface engineering process, constantly evolving to meet the demands of diverse industries. Its ability to enhance the properties of materials while maintaining cost-effectiveness makes it an indispensable tool for various applications, from everyday consumer products to advanced technologies. The ongoing focus on sustainability and innovation ensures that plating technology will continue to play a significant role in shaping the future of materials science and engineering.
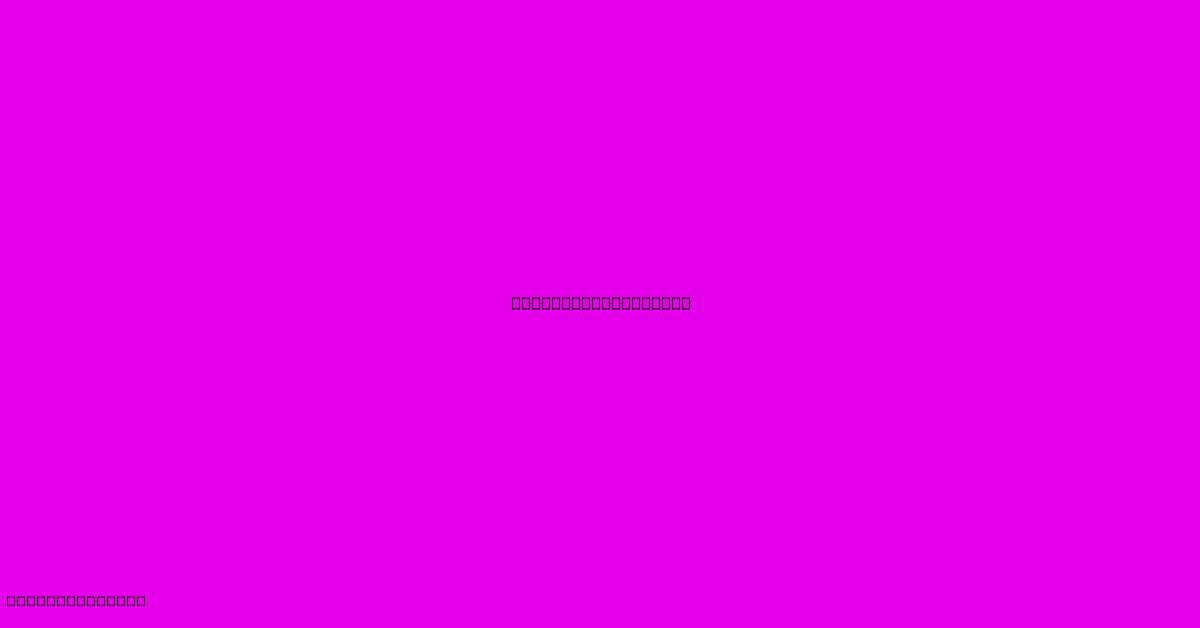
Thank you for visiting our website wich cover about Plating Technology. We hope the information provided has been useful to you. Feel free to contact us if you have any questions or need further assistance. See you next time and dont miss to bookmark.
Featured Posts
-
Babynamen Trend Emilia And Noah Fuehren
Dec 29, 2024
-
Paralegal Technology Jobs
Dec 29, 2024
-
Piping Technology And Products Houston Texas
Dec 29, 2024
-
Bengals Win Overtime Game
Dec 29, 2024
-
Where To Watch Patriots Vs Chargers
Dec 29, 2024