Plating Technologies
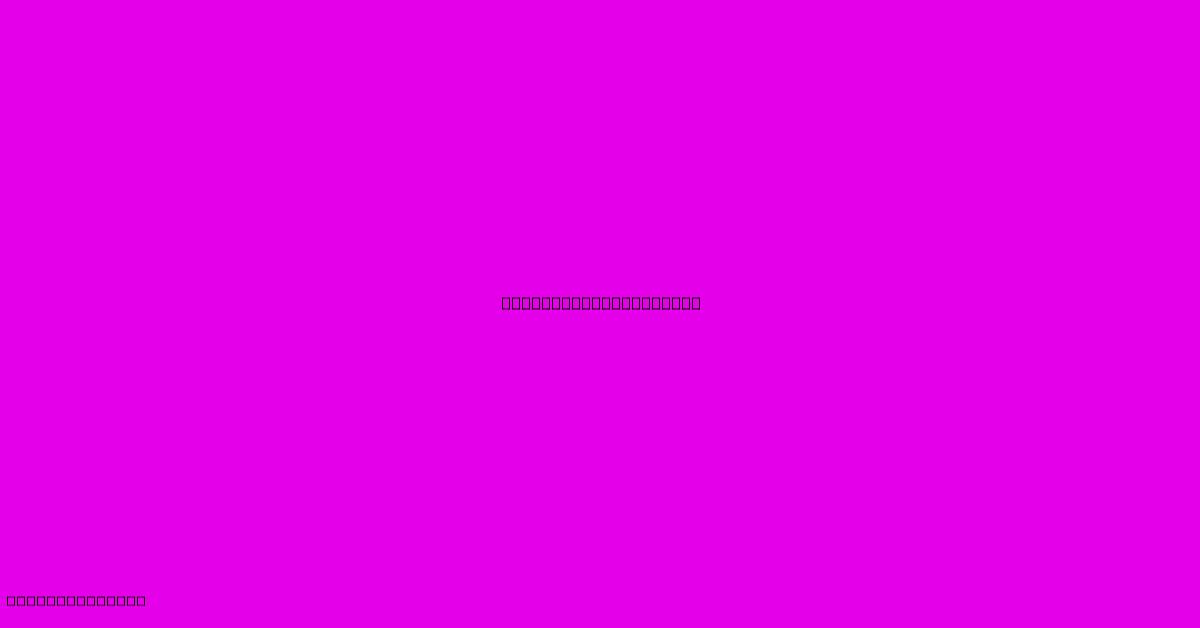
Discover more detailed and exciting information on our website. Click the link below to start your adventure: Visit Best Website mr.cleine.com. Don't miss out!
Table of Contents
Plating Technologies: A Deep Dive into Surface Enhancement
Plating technologies encompass a diverse range of processes used to deposit a thin layer of material onto a substrate, significantly enhancing its properties. This article explores the various plating methods, their applications, and the factors influencing their selection.
What is Plating?
Plating, also known as electroplating, is a technique where a metal coating is applied to a conductive surface using an electrochemical process. This process involves immersing the substrate in an electrolyte solution containing the desired metal ions and applying an electric current. The metal ions then migrate to the substrate and deposit, forming a thin, adherent layer. While electroplating is the most common method, other plating technologies exist, each with its unique advantages and limitations.
Types of Plating Technologies:
Several methods exist beyond traditional electroplating, each suited for specific applications and materials. These include:
1. Electroplating:
- Mechanism: This is the most prevalent method, utilizing an electric current to deposit metal ions from a solution onto a conductive substrate. The substrate acts as the cathode, and a metal anode releases ions into the solution.
- Advantages: Relatively inexpensive, versatile, allows for precise control of coating thickness, excellent adhesion.
- Disadvantages: Requires conductive substrates, can be environmentally unfriendly (depending on the electrolyte used), potential for hydrogen embrittlement (in some cases).
- Applications: Automotive parts, jewelry, electronics, hardware.
2. Electroless Plating:
- Mechanism: This method doesn't require an external electric current. A chemical reducing agent in the solution reduces metal ions to their metallic form, allowing deposition onto both conductive and non-conductive surfaces.
- Advantages: Can plate non-conductive materials, uniform coating even on complex shapes.
- Disadvantages: Slower deposition rate compared to electroplating, more complex chemistry, potential for reduced adhesion in some cases.
- Applications: Electronics, printed circuit boards (PCBs), plastics.
3. Physical Vapor Deposition (PVD):
- Mechanism: Involves depositing thin films under vacuum conditions. Materials are vaporized and then deposited onto the substrate. Common techniques include sputtering and evaporation.
- Advantages: Excellent adhesion, high purity coatings, can deposit a wide range of materials.
- Disadvantages: High capital cost for equipment, slower deposition rates than electroplating, can be sensitive to substrate preparation.
- Applications: Cutting tools, decorative coatings, optical components.
4. Chemical Vapor Deposition (CVD):
- Mechanism: Similar to PVD, but occurs at higher pressures. Gaseous precursors react on the substrate surface, forming a solid film.
- Advantages: Uniform coatings on complex shapes, suitable for high-temperature applications.
- Disadvantages: Can be less precise in terms of thickness control, requires specialized equipment.
- Applications: Semiconductor industry, protective coatings for high-temperature environments.
5. Dip Coating:
- Mechanism: The substrate is immersed in a solution containing the coating material, then withdrawn at a controlled rate. The coating thickness depends on the viscosity of the solution and the withdrawal speed. Often used with paints, lacquers, and polymers rather than metals.
- Advantages: Simple and relatively inexpensive method, suitable for large-scale production.
- Disadvantages: Limited control over coating thickness and uniformity, prone to defects.
- Applications: Coating electronic components, protecting parts from corrosion.
Factors Influencing Plating Technology Selection:
The choice of plating technology depends on several factors:
- Substrate material: Conductivity, surface finish, and chemical compatibility are crucial considerations.
- Desired coating properties: Hardness, corrosion resistance, wear resistance, and aesthetics.
- Coating thickness and uniformity: The required level of precision in coating thickness and uniformity dictates the method selection.
- Cost and throughput: Balancing the cost of equipment, materials, and labor with the desired production rate.
- Environmental concerns: The environmental impact of the plating process, including waste generation and hazardous materials, must be considered.
Conclusion:
Plating technologies offer versatile solutions for enhancing the surface properties of materials, leading to improved performance and longevity. Understanding the various methods and their specific advantages and disadvantages is crucial for selecting the most appropriate technique for any given application. The future of plating will likely see increased emphasis on environmentally friendly processes and the development of new materials and techniques for advanced applications.
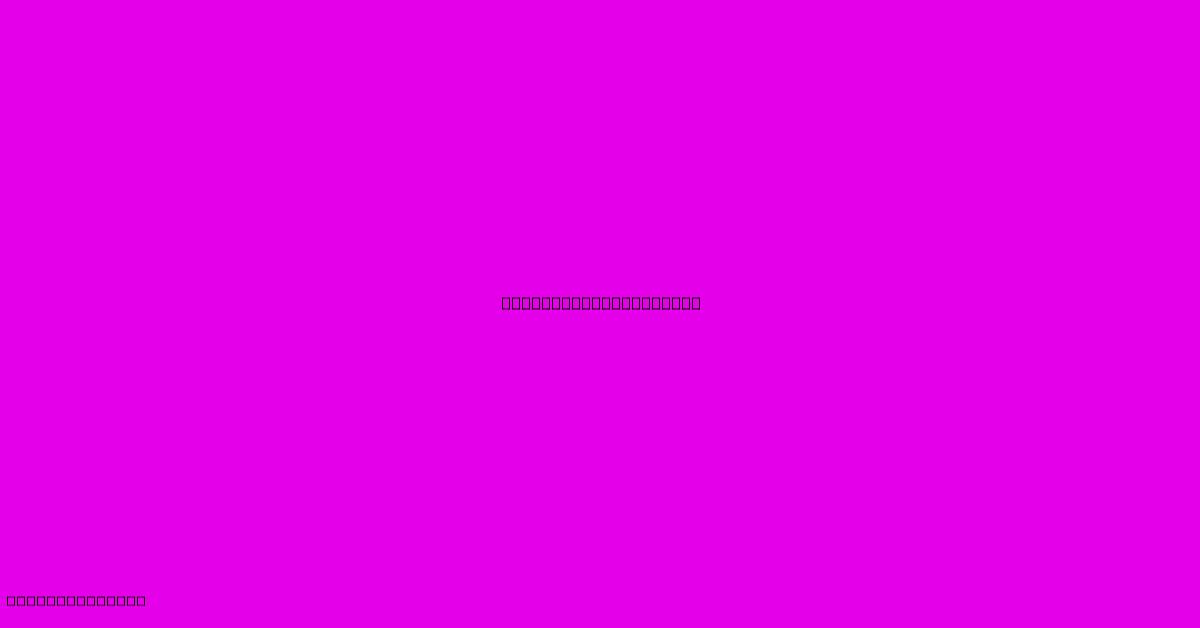
Thank you for visiting our website wich cover about Plating Technologies. We hope the information provided has been useful to you. Feel free to contact us if you have any questions or need further assistance. See you next time and dont miss to bookmark.
Featured Posts
-
Peregrine Technologies
Dec 30, 2024
-
Hyper Technology
Dec 30, 2024
-
Uniqlo Checkout Technology
Dec 30, 2024
-
East Yorkshire Snow Wind Warning
Dec 30, 2024
-
Live Blog West Ham United Vs Liverpool
Dec 30, 2024