Plastic Mould Technology
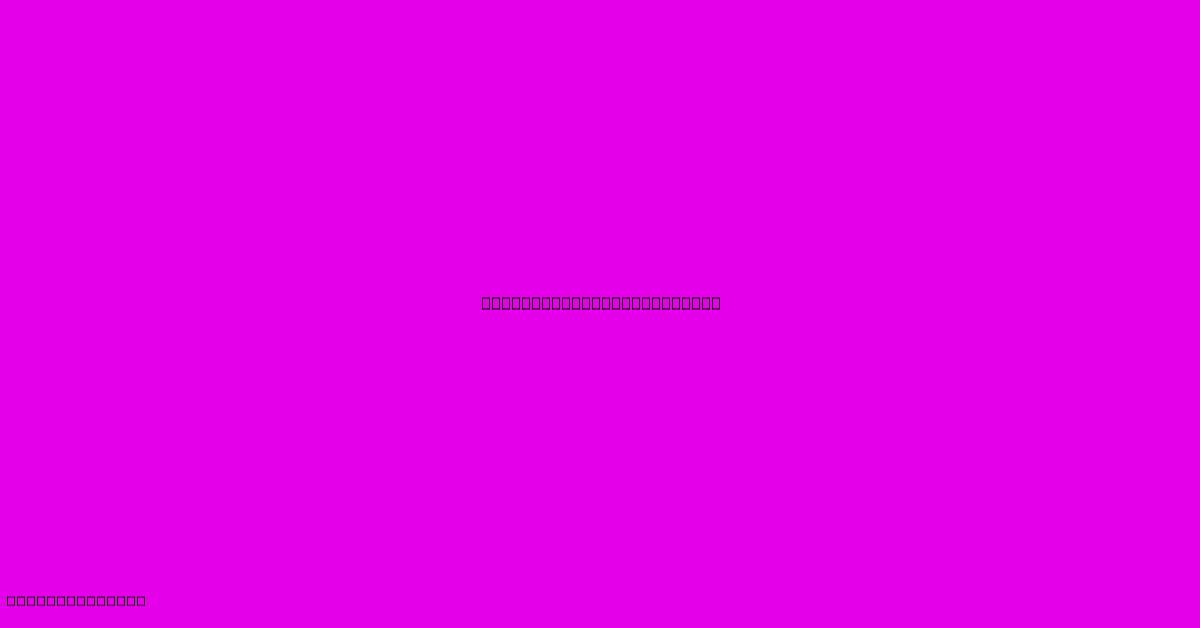
Discover more detailed and exciting information on our website. Click the link below to start your adventure: Visit Best Website mr.cleine.com. Don't miss out!
Table of Contents
Mastering the Art of Plastic Mould Technology: A Comprehensive Guide
Plastic molding is the cornerstone of countless industries, from automotive manufacturing to consumer goods production. Understanding plastic mould technology is crucial for anyone involved in product design, manufacturing, or supply chain management. This comprehensive guide explores the intricacies of this vital process, delving into its various types, advantages, and the future of innovation.
What is Plastic Mould Technology?
Plastic mould technology encompasses the processes involved in creating plastic parts using molds. A mold is a precisely engineered cavity that shapes molten plastic into a desired form. High-pressure injection, compression, or other methods force the molten plastic into the mold, where it cools and solidifies, creating the final product. The precision and repeatability of this process make it incredibly efficient for mass production.
Types of Plastic Moulding Processes:
Several methods exist, each with its own strengths and applications:
1. Injection Molding: This is the most prevalent method, ideal for high-volume production of complex parts. Molten plastic is injected into a tightly closed mold under high pressure.
- Advantages: High production rates, excellent dimensional accuracy, intricate designs possible.
- Disadvantages: High initial investment in tooling, less suitable for very low-volume production.
2. Compression Molding: Plastic material is placed into a heated mold and compressed until it takes the shape of the cavity.
- Advantages: Simple tooling, suitable for thermosetting plastics.
- Disadvantages: Lower production rates compared to injection molding, limited design complexity.
3. Blow Molding: Used for creating hollow plastic parts like bottles. A heated plastic tube is inflated within a mold to create the desired shape.
- Advantages: Cost-effective for hollow parts, excellent for large-scale production.
- Disadvantages: Not suitable for complex shapes, limitations on wall thickness control.
4. Rotational Molding: A hollow mold is filled with plastic powder, rotated, and heated until the plastic melts and fuses to the mold's inner surface.
- Advantages: Can produce large, hollow parts with uniform wall thickness.
- Disadvantages: Relatively slow production speed, limited design complexity.
5. Thermoforming: A plastic sheet is heated and then formed into a desired shape using vacuum or pressure.
- Advantages: Versatile, relatively low tooling cost, suitable for prototyping and short runs.
- Disadvantages: Limited in terms of intricate designs, potential for inconsistent wall thickness.
Key Considerations in Plastic Mould Technology:
- Material Selection: The choice of plastic resin significantly impacts the final product's properties, including strength, flexibility, and durability.
- Mold Design: Precise mold design is paramount for achieving accurate and consistent part dimensions. CAD/CAM software plays a crucial role in this process.
- Tooling Materials: The mold itself is made from durable materials like steel or aluminum, chosen for their wear resistance and ability to withstand high temperatures and pressures.
- Quality Control: Implementing rigorous quality control measures throughout the process is critical for ensuring product consistency and minimizing defects.
The Future of Plastic Mould Technology:
The industry is constantly evolving, driven by advancements in materials science, automation, and digital technologies. Some key trends include:
- Additive Manufacturing: 3D printing is increasingly used for rapid prototyping and low-volume production of molds.
- Automation and Robotics: Automated systems enhance efficiency and precision in molding operations.
- Sustainable Materials: The industry is exploring bio-based plastics and recyclable materials to reduce environmental impact.
- Smart Manufacturing: Data analytics and machine learning are being integrated to optimize production processes and improve quality control.
Conclusion:
Plastic mould technology is a sophisticated and dynamic field that underpins a vast array of industries. Understanding the different molding processes, material considerations, and emerging trends is vital for anyone seeking to innovate and excel in this crucial sector. The continuous advancements in this field promise further efficiency, sustainability, and innovation in the years to come.
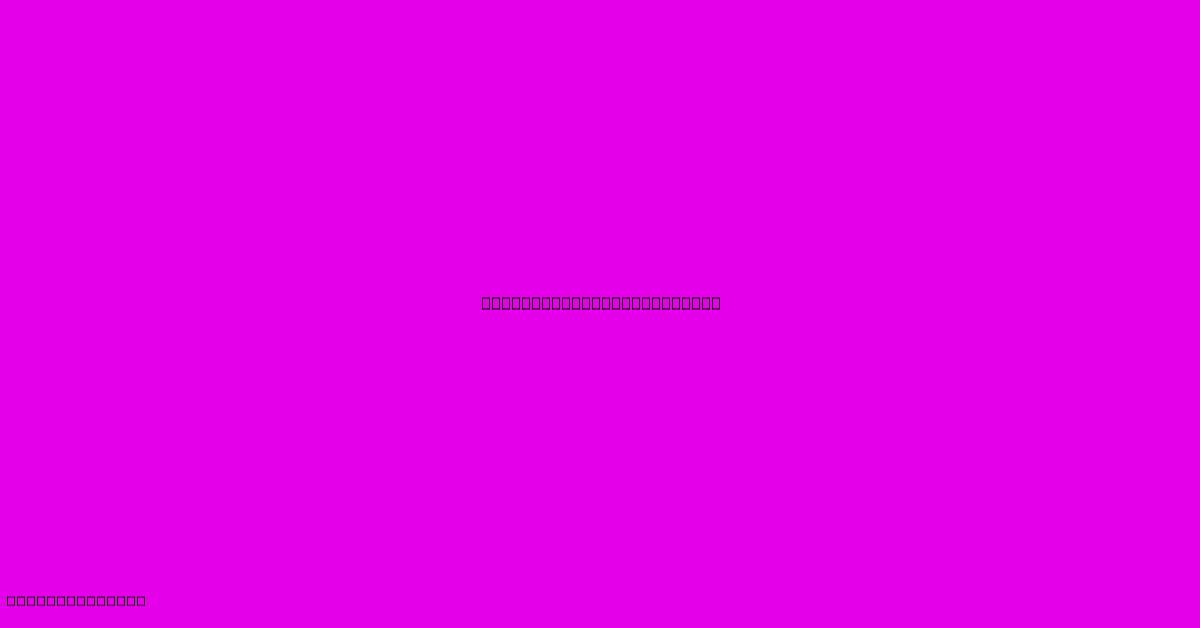
Thank you for visiting our website wich cover about Plastic Mould Technology. We hope the information provided has been useful to you. Feel free to contact us if you have any questions or need further assistance. See you next time and dont miss to bookmark.
Featured Posts
-
Liverpool Dominates Leicester 3 1 Victory
Dec 28, 2024
-
Definitive Technology 8060
Dec 28, 2024
-
Midwestern Technology
Dec 28, 2024
-
Technological Knowledge Refers To
Dec 28, 2024
-
Ya Khochu Buti Z Toboyu Peremozhnitsya Kholostyaka Tsey Zagolovok Korotkiy Pryamiy I Mistit Klyuchove Slovo Vin Takozh Pidkreslyuye Golovnu Temu
Dec 28, 2024