Piping Technology
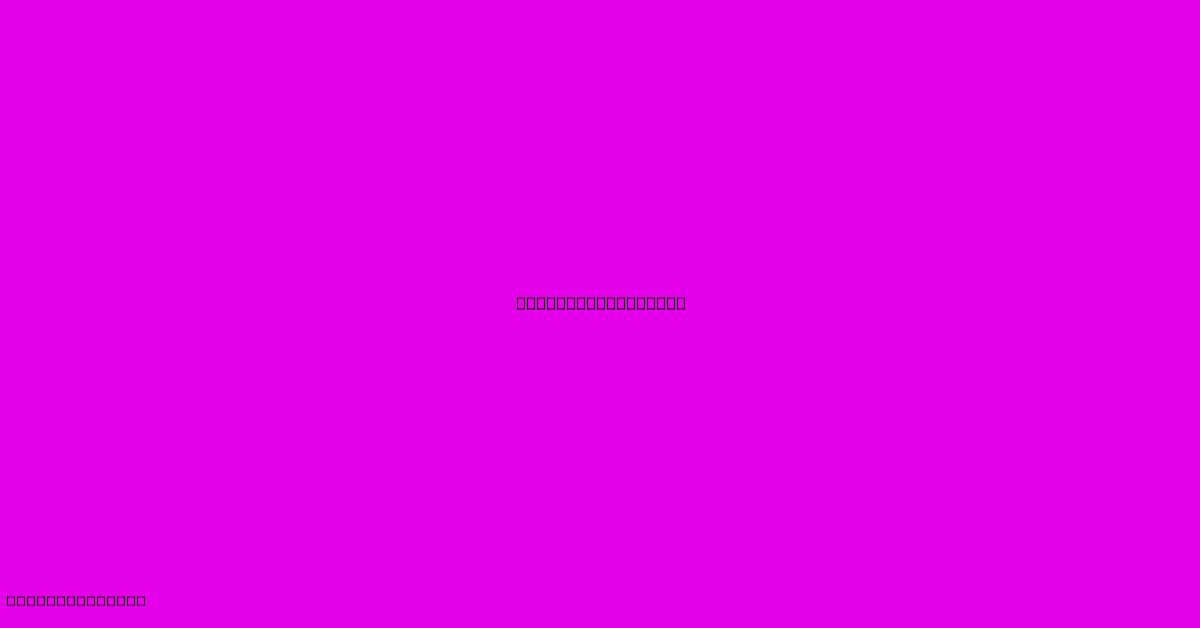
Discover more detailed and exciting information on our website. Click the link below to start your adventure: Visit Best Website mr.cleine.com. Don't miss out!
Table of Contents
Piping Technology: A Comprehensive Overview
Piping technology encompasses the design, fabrication, installation, and maintenance of piping systems used to transport fluids (liquids, gases, slurries) in various industries. From simple domestic plumbing to complex industrial processes, piping systems are critical infrastructure, demanding careful consideration at every stage. This article explores the key aspects of piping technology.
1. Design Considerations:
The design phase is paramount, impacting safety, efficiency, and cost-effectiveness. Several crucial factors are considered:
-
Fluid Properties: The characteristics of the transported fluid (temperature, pressure, viscosity, corrosiveness) dictate material selection, pipe diameter, and flow rate calculations. Highly corrosive fluids might require specialized materials like stainless steel or exotic alloys.
-
Process Requirements: The specific application dictates the system's complexity. A simple water supply system differs vastly from a high-pressure steam line in a power plant. Factors such as flow rates, pressure drops, and required safety features must be carefully integrated into the design.
-
Safety Regulations: Adherence to industry-specific safety standards (e.g., ASME B31 codes for pressure piping) is mandatory. These standards outline design criteria, material specifications, and testing procedures to minimize risks.
-
Environmental Considerations: Minimizing environmental impact is a growing concern. Leak detection systems, proper material selection to avoid corrosion and leaching, and strategies for minimizing emissions are vital aspects of modern piping design.
-
Economic Factors: Balancing initial costs with long-term operational expenses is crucial. The selection of materials, pipe diameter, and support systems all have implications for overall costs. Life cycle cost analysis is a valuable tool in making informed design decisions.
2. Materials Selection:
The choice of piping materials depends on factors such as fluid properties, operating temperature and pressure, and cost. Common materials include:
-
Carbon Steel: A widely used material due to its strength and cost-effectiveness, suitable for many applications. However, it’s susceptible to corrosion.
-
Stainless Steel: Offers superior corrosion resistance, making it suitable for handling corrosive fluids or in harsh environments.
-
Ductile Iron: Strong and ductile, providing good resistance to pressure and impact.
-
PVC, CPVC, and other Plastics: Lightweight and corrosion-resistant, ideal for low-pressure applications handling non-aggressive fluids.
-
Exotic Alloys: Used in demanding applications requiring high corrosion resistance and strength at extreme temperatures and pressures.
3. Fabrication and Construction:
Fabrication techniques vary based on pipe material and system complexity. Common methods include:
-
Welding: A widely used joining technique, requiring skilled welders to ensure strong, leak-tight joints. Different welding processes (e.g., TIG, MIG, SMAW) are employed depending on material and application.
-
Flanged Connections: Offer ease of assembly and disassembly, suitable for applications requiring frequent maintenance or modifications.
-
Threaded Connections: Suitable for smaller diameter pipes and lower pressure applications.
-
Compression Fittings: Provide a reliable seal without welding or threading, commonly used in plumbing and smaller-scale systems.
Proper installation techniques, including proper support and anchoring, are critical for system integrity and longevity.
4. Maintenance and Inspection:
Regular inspection and maintenance are essential to ensure the long-term reliability and safety of piping systems. This includes:
-
Visual Inspection: Checking for signs of corrosion, leaks, or damage.
-
Non-Destructive Testing (NDT): Techniques such as ultrasonic testing, radiographic testing, and magnetic particle testing are used to detect internal flaws without damaging the pipe.
-
Leak Detection: Employing sensors and monitoring systems to identify and address leaks promptly.
-
Preventive Maintenance: Scheduled cleaning, lubrication, and component replacement to prevent failures.
5. Advanced Piping Technologies:
The field is constantly evolving, with advancements focused on improving efficiency, safety, and sustainability:
-
Smart Piping Systems: Incorporating sensors and data analytics for real-time monitoring and predictive maintenance.
-
Advanced Materials: Development of new materials with enhanced corrosion resistance, strength, and durability.
-
Improved Joining Techniques: Developing faster, more reliable, and less labor-intensive joining methods.
Conclusion:
Piping technology is a critical field impacting numerous industries. Understanding the design, material selection, fabrication, installation, and maintenance aspects is crucial for ensuring safe, efficient, and cost-effective fluid transport systems. Continuous advancements in this field promise further improvements in safety, reliability, and sustainability.
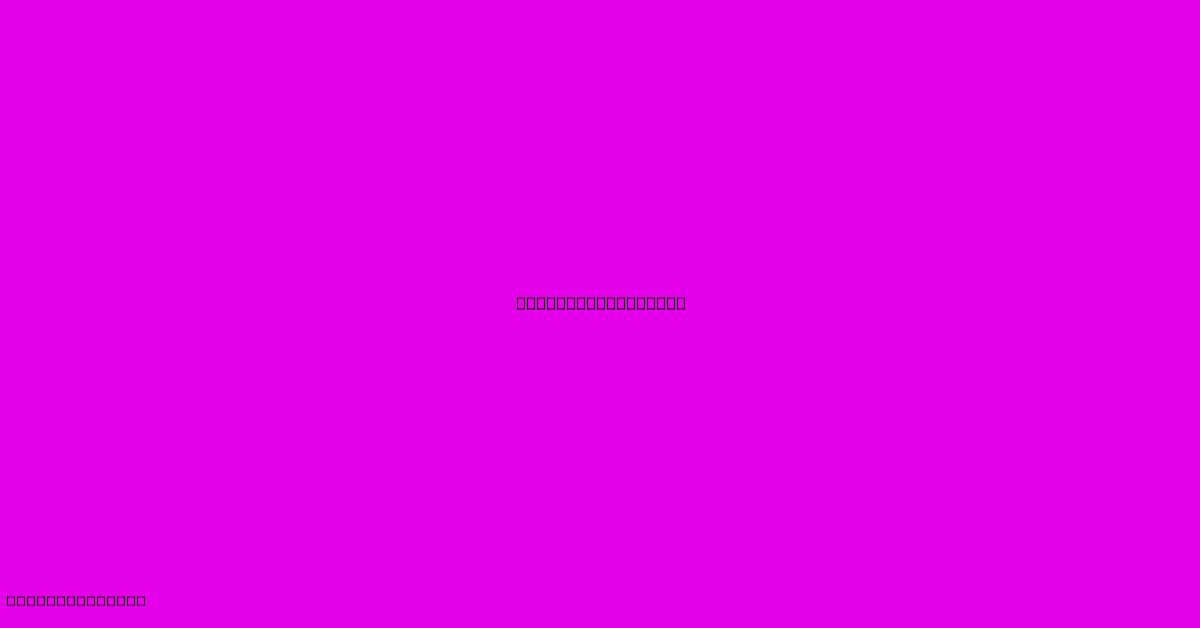
Thank you for visiting our website wich cover about Piping Technology. We hope the information provided has been useful to you. Feel free to contact us if you have any questions or need further assistance. See you next time and dont miss to bookmark.
Featured Posts
-
Hannity Earhardt Announce News
Dec 28, 2024
-
Zebra Technologies Holtsville Ny
Dec 28, 2024
-
Arsenal Secures 1 0 Win Against Ipswich
Dec 28, 2024
-
Technology Of France
Dec 28, 2024
-
Fashion Technology Trends
Dec 28, 2024