Peening Technologies Ct
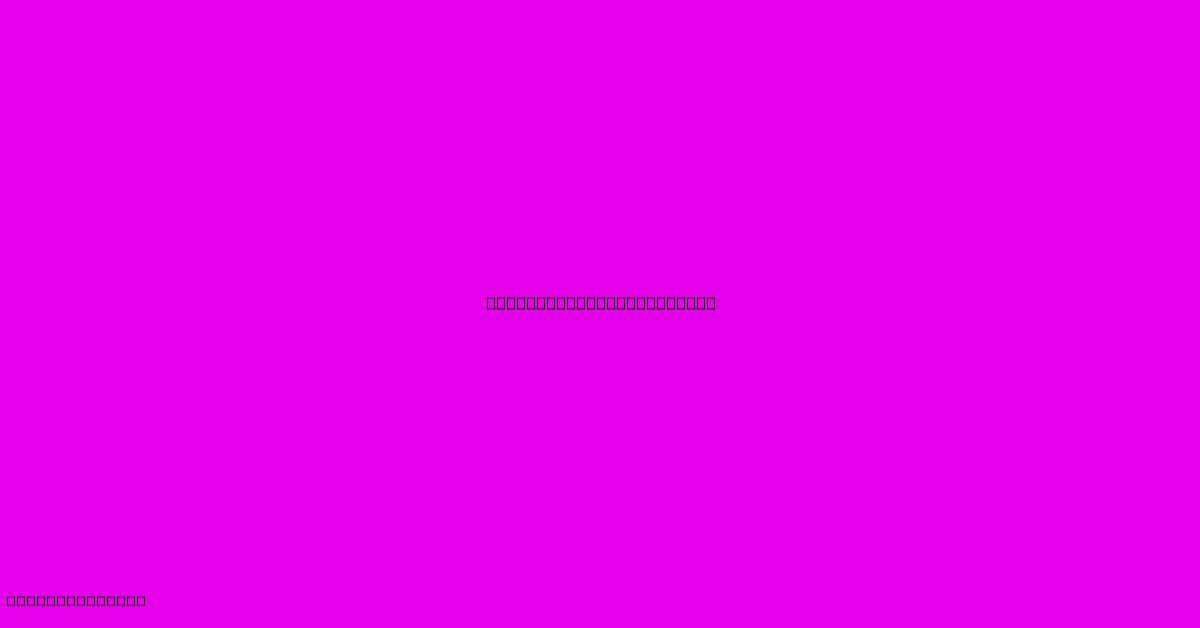
Discover more detailed and exciting information on our website. Click the link below to start your adventure: Visit Best Website mr.cleine.com. Don't miss out!
Table of Contents
Peening Technologies: A Deep Dive into Cold Treatment Processes
Peening technologies represent a family of cold work surface treatment processes used to enhance the fatigue life, durability, and corrosion resistance of metallic components. These techniques involve impacting a component's surface with numerous small, high-velocity projectiles, inducing compressive residual stresses within the material's near-surface layer. This compressive stress acts as a counterforce against tensile stresses introduced during service, delaying or preventing fatigue crack initiation and propagation. Let's explore the various aspects of peening technologies.
Types of Peening Technologies:
Several methods fall under the umbrella of peening technologies, each with its own advantages and applications:
1. Shot Peening: This is the most common peening method. It uses small, spherical projectiles (shot) propelled by compressed air or centrifugal force to impact the component's surface. Shot peening is highly versatile and can be applied to a wide range of components and geometries. The size and material of the shot, along with the peening intensity, can be carefully controlled to achieve the desired surface finish and residual stress profile.
2. UltraSonic Peening (USP): USP uses high-frequency ultrasonic vibrations to create a hammering effect on the component's surface. This method is particularly beneficial for complex geometries and delicate components where traditional shot peening might cause damage.
3. Laser Peening: This advanced technique uses high-energy laser pulses to generate a plasma shock wave that induces compressive residual stresses. Laser peening is highly precise and can achieve deep and uniform compressive layers, ideal for critical aerospace and energy applications. It also offers the advantage of being a non-contact process.
4. Water Jet Peening: A relatively newer technology, water jet peening uses high-velocity water jets to create the peening effect. This technique offers certain advantages, such as reduced noise and environmental impact compared to shot peening.
Benefits of Peening Technologies:
The adoption of peening technologies brings several significant advantages:
-
Enhanced Fatigue Life: The primary benefit is a substantial increase in the fatigue life of components, particularly those subjected to cyclic loading. Compressive residual stresses counteract the tensile stresses responsible for crack initiation.
-
Improved Corrosion Resistance: Compressive stresses hinder the formation and propagation of corrosion pits, improving resistance to corrosion.
-
Increased Strength and Durability: The cold working process can result in a slight increase in the material's surface hardness and yield strength.
-
Stress Relief: In some instances, peening can be used to reduce existing tensile stresses, preventing stress corrosion cracking.
Applications of Peening Technologies:
The versatility of peening technologies makes them applicable across diverse industries and applications:
-
Aerospace: Aircraft components, turbine blades, and engine parts are frequently subjected to shot peening to enhance their fatigue resistance and extend their lifespan.
-
Automotive: Critical components in vehicles, including springs, axles, and gears, can benefit from improved fatigue life and durability through peening.
-
Medical Implants: Peening can improve the durability and corrosion resistance of medical implants, such as orthopedic devices.
-
Oil and Gas: Components used in the oil and gas industry, operating under high stress and corrosive environments, often undergo peening treatment.
Choosing the Right Peening Technology:
Selecting the appropriate peening method depends on several factors:
-
Component geometry and material: Complex geometries may be better suited to USP or laser peening, while simple shapes can be effectively treated with shot peening. Material properties also influence the choice of process and parameters.
-
Desired residual stress level and depth: The required level of compressive stress dictates the intensity and method of peening.
-
Cost and processing time: Different peening methods vary in cost and processing speed.
-
Environmental considerations: Methods like water jet peening offer advantages in noise reduction and environmental impact.
Conclusion:
Peening technologies are crucial for enhancing the performance and reliability of metal components across numerous industries. Understanding the various types of peening, their benefits, and applications allows engineers to select the most suitable method for specific needs, ensuring the longevity and safety of critical parts. Further research and development are continually pushing the boundaries of these technologies, leading to even more sophisticated and effective applications in the future.
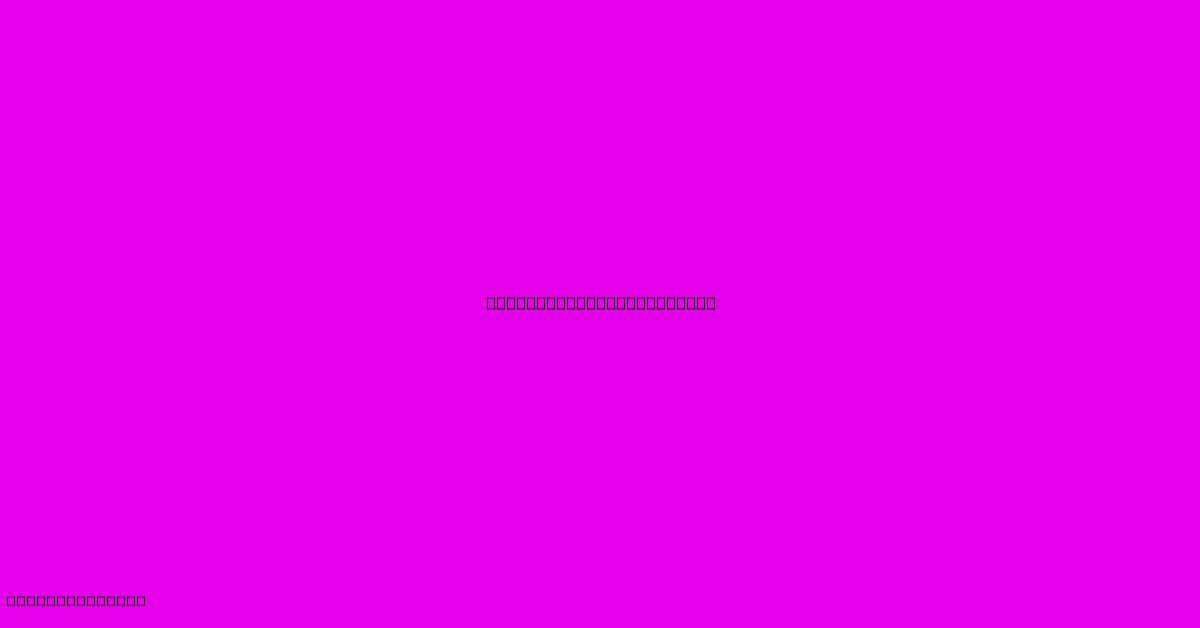
Thank you for visiting our website wich cover about Peening Technologies Ct. We hope the information provided has been useful to you. Feel free to contact us if you have any questions or need further assistance. See you next time and dont miss to bookmark.
Featured Posts
-
Creative Technology Las Vegas
Jan 01, 2025
-
Technology For Nonprofits
Jan 01, 2025
-
La Crosse Technology Weather Station Manual
Jan 01, 2025
-
Presidente Aprova Ldo 2025 Principais Pontos
Jan 01, 2025
-
A A A A Y A A Y A A A A A A A A Ye A A A A Y A A A Y A A A A Y A A A A A Y A A Y A A A A A A A A A Y A Y A A A A Y A A Y A A A A A A A A Ye A A A A Y A A A Y A A A A Y A A A A A Y A A Y A A A A A A Y A A A A A Y A A Y A A A A A A A A Ye A A A A Y A A A Y A A A A Y A A A A A Y A A Y A A A A A A Y A A A A A A A A A A A A A A A Y A A Y A
Jan 01, 2025