New Welding Technology 2023
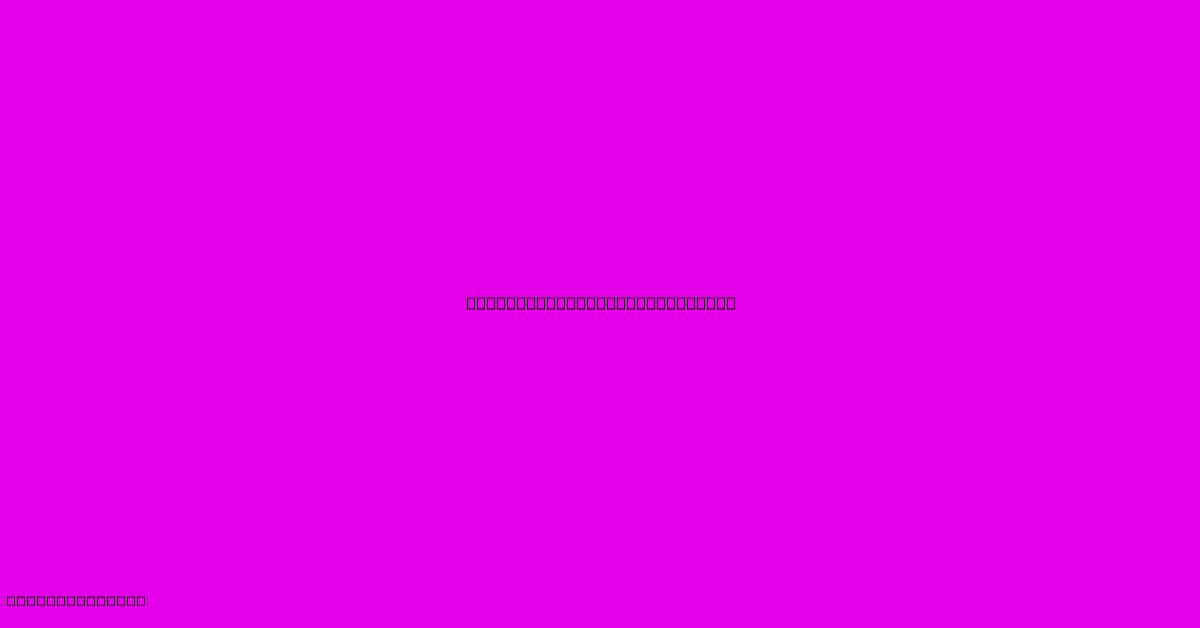
Discover more detailed and exciting information on our website. Click the link below to start your adventure: Visit Best Website mr.cleine.com. Don't miss out!
Table of Contents
Revolutionizing the Weld: New Welding Technologies in 2023
The world of welding is constantly evolving, driven by the need for higher efficiency, improved quality, and greater safety. 2023 has seen a surge in innovative welding technologies, promising to reshape various industries. From advancements in established techniques to entirely new approaches, this year's innovations are rewriting the rules of joining materials.
1. AI-Powered Welding Automation:
One of the most significant trends is the integration of Artificial Intelligence (AI) into welding processes. AI-powered systems offer several key advantages:
- Improved Weld Quality: AI algorithms can analyze real-time data from sensors, adjusting parameters like voltage, current, and travel speed to ensure optimal weld penetration and minimize defects. This results in significantly higher consistency and reduces the need for rework.
- Enhanced Efficiency: By automating tasks like seam tracking and parameter optimization, AI can drastically increase welding speed and productivity. This is particularly beneficial for high-volume manufacturing.
- Predictive Maintenance: AI can predict potential equipment failures by analyzing sensor data, allowing for proactive maintenance and minimizing downtime.
2. Additive Manufacturing (3D Printing) in Welding:
While not strictly welding in the traditional sense, additive manufacturing techniques like Directed Energy Deposition (DED) are increasingly used for metal joining and repair. DED uses a laser or electron beam to melt and fuse metal powder onto a substrate, allowing for the creation of complex shapes and the repair of damaged parts. Key benefits include:
- Complex Geometry Fabrication: DED enables the creation of parts with intricate designs that are impossible to produce using conventional welding methods.
- Material Flexibility: A wide range of metals and alloys can be used in DED processes, opening up possibilities for new material combinations and applications.
- Repair and Reclamation: DED provides a cost-effective way to repair damaged components, extending their lifespan and reducing waste.
3. Advanced Welding Processes:
Existing welding techniques are also undergoing significant refinements:
- Friction Stir Welding (FSW): FSW, a solid-state welding process, is gaining popularity due to its ability to produce high-quality welds with minimal distortion and reduced heat input. Advancements in tooling and process control are expanding its applicability to a wider range of materials.
- Laser Welding: Laser welding continues to evolve, with higher-power lasers and advanced beam control systems enabling faster welding speeds and improved precision. This makes it ideal for applications requiring high accuracy and minimal heat-affected zones.
- Hybrid Welding: Combining different welding processes, like laser and arc welding, offers synergistic benefits. Hybrid processes can achieve higher welding speeds, improved penetration, and better overall weld quality.
4. Robotics and Automation:
Robotics are playing an increasingly crucial role in modern welding, offering:
- Improved Safety: Robots can handle dangerous and repetitive welding tasks, reducing the risk of injury to human welders.
- Increased Precision: Robots offer exceptional accuracy and repeatability, leading to higher quality welds and lower defect rates.
- Flexible Automation: Robotic welding systems can be easily reprogrammed to adapt to different welding tasks and product designs.
5. Focus on Sustainability:
The welding industry is also increasingly focusing on sustainability:
- Reduced Energy Consumption: New welding processes and equipment designs are aimed at reducing energy consumption and improving efficiency.
- Waste Reduction: Advancements in welding techniques minimize weld defects, reducing the need for rework and material waste.
- Recycled Materials: The use of recycled materials in welding is becoming more common, contributing to a circular economy.
Conclusion:
The innovations in welding technology in 2023 are transforming the industry, offering enhanced efficiency, improved quality, and increased safety. AI, additive manufacturing, advanced welding processes, and automation are driving this transformation, paving the way for a more productive, sustainable, and innovative future of welding. The coming years will undoubtedly witness even more groundbreaking advancements in this crucial field.
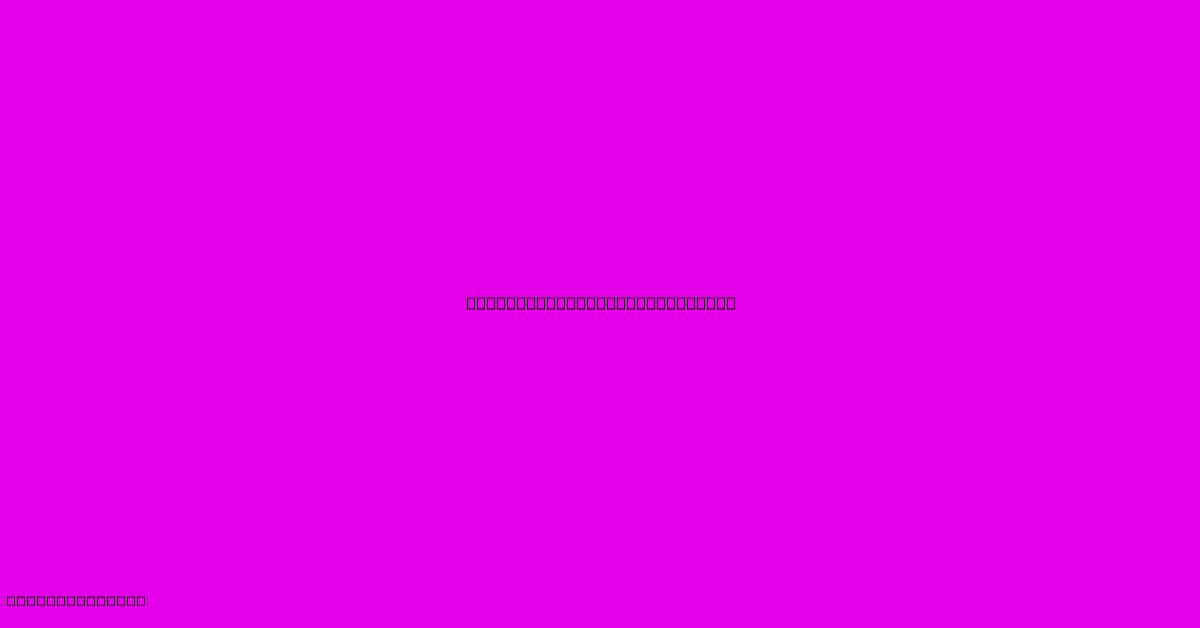
Thank you for visiting our website wich cover about New Welding Technology 2023. We hope the information provided has been useful to you. Feel free to contact us if you have any questions or need further assistance. See you next time and dont miss to bookmark.
Featured Posts
-
Arsenal At Palace Full Game Summary
Dec 22, 2024
-
Crystal Palace Vs Arsenal Jesus Double
Dec 22, 2024
-
Chiefs Qb Ankle Injury Update
Dec 22, 2024
-
Chiefs Win Again Mahomes Close Victory
Dec 22, 2024
-
Partido Aston Villa Manchester City Resultado
Dec 22, 2024