New Cast Technology
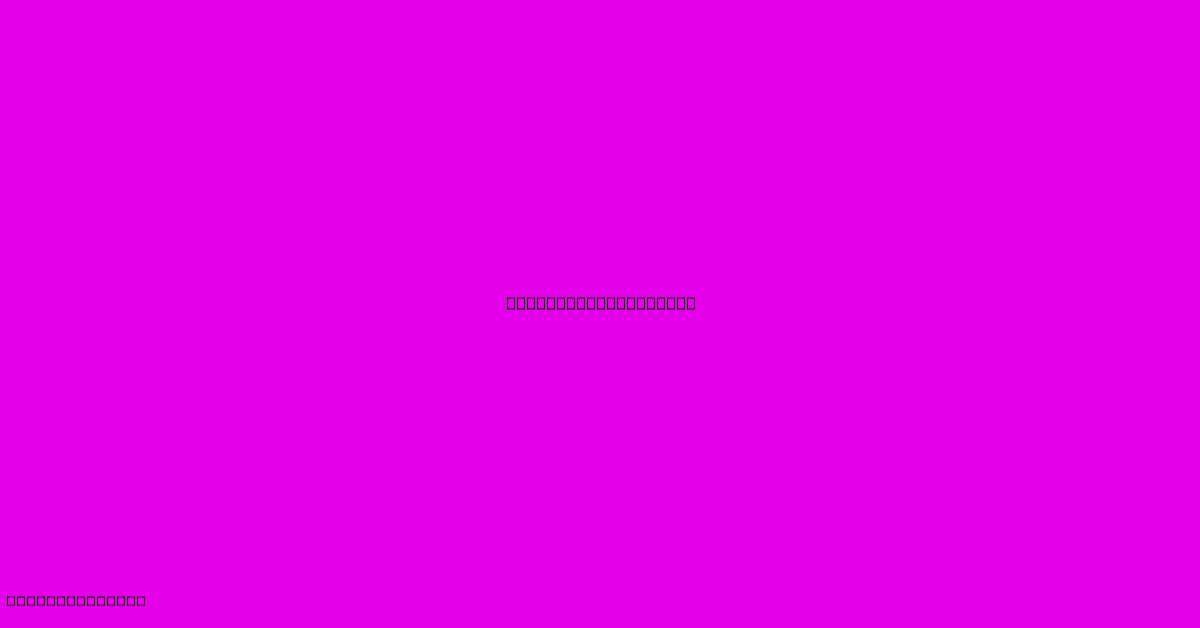
Discover more detailed and exciting information on our website. Click the link below to start your adventure: Visit Best Website mr.cleine.com. Don't miss out!
Table of Contents
Revolutionizing the Foundry: Exploring New Casting Technologies
The world of metal casting, a cornerstone of manufacturing for centuries, is undergoing a dramatic transformation. New casting technologies are emerging, pushing the boundaries of what's possible in terms of precision, efficiency, and material versatility. This article delves into some of the most promising advancements, highlighting their impact on various industries.
Beyond Traditional Methods: The Need for Innovation
Traditional casting methods, like sand casting and investment casting, while reliable, have limitations. They often suffer from lower dimensional accuracy, higher surface roughness, and limitations in producing complex geometries. The increasing demand for lightweight, high-strength components with intricate designs necessitates the development of more sophisticated techniques.
1. 3D Printing (Additive Manufacturing) in Metal Casting:
This revolutionary technology is rapidly reshaping the casting landscape. 3D printing allows for the creation of highly complex parts with internal channels and intricate features impossible to achieve using traditional methods. This opens up new possibilities in aerospace, medical implants, and automotive industries, where lightweight and high-performance parts are crucial.
- Benefits: Unmatched design flexibility, reduced material waste, faster prototyping, and the potential for on-demand manufacturing.
- Challenges: Cost, build speed, and the need for specialized materials remain hurdles to overcome.
2. High-Pressure Die Casting (HPDC):
HPDC is a well-established process, but ongoing advancements are boosting its capabilities. Higher pressures and improved die materials enable the production of thinner-walled, more intricate parts with superior surface finish. This is particularly beneficial for automotive components, where weight reduction and design complexity are paramount.
- Benefits: High production rates, excellent dimensional accuracy, and superior surface finish.
- Challenges: High initial investment costs, limited design complexity in some cases, and potential for die wear.
3. Investment Casting (Lost-Wax Casting) Enhancements:
While a traditional method, investment casting continues to evolve. Advancements in ceramic shell technology, along with improved vacuum and pressure casting techniques, are leading to higher precision, finer surface detail, and the ability to cast more complex shapes.
- Benefits: Excellent surface finish, high dimensional accuracy for intricate designs, and suitability for a wide range of alloys.
- Challenges: Relatively high cost, longer lead times compared to some other methods.
4. Near-Net Shape Casting:
This approach focuses on minimizing material removal after casting. Techniques like rheocasting and thixoforming allow for the creation of preforms closer to the final part shape, reducing machining time and waste. This leads to significant cost savings and improved sustainability.
- Benefits: Reduced machining, lower material waste, and improved efficiency.
- Challenges: Requires specialized equipment and expertise.
5. Reactive Casting Processes:
These processes involve in-situ reactions during casting to create novel alloys or composites with unique properties. This enables the production of parts with tailored mechanical, thermal, or electrical characteristics.
- Benefits: Creation of materials with tailored properties, potential for new functionalities.
- Challenges: Requires specialized knowledge and control of reaction kinetics.
The Future of Casting Technology:
The future of casting technologies looks bright. Ongoing research and development efforts are focusing on:
- Automation and digitalization: Integrating AI and automation to optimize casting processes and improve quality control.
- Sustainable materials: Utilizing recycled materials and developing environmentally friendly casting processes.
- Advanced alloys and composites: Exploring new materials with enhanced properties for specific applications.
The convergence of these advancements will create a new era of high-precision, efficient, and sustainable metal casting, impacting various industries and enabling the creation of innovative and high-performance products. The challenge lies in effectively integrating these innovations to achieve optimal performance and cost-effectiveness while addressing environmental concerns.
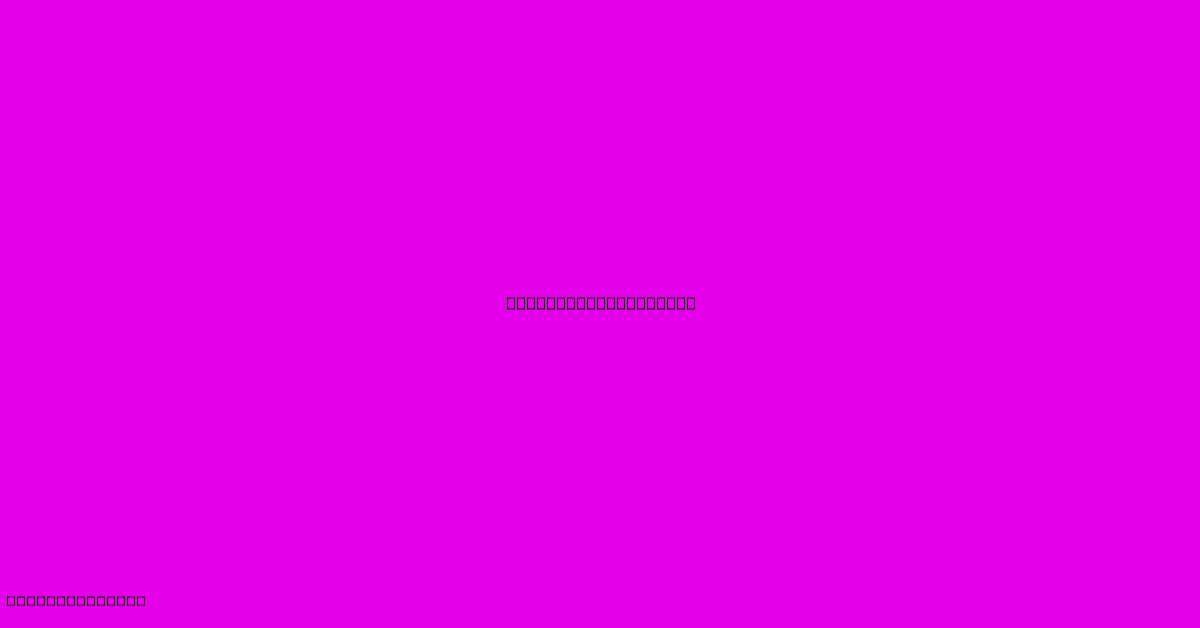
Thank you for visiting our website wich cover about New Cast Technology. We hope the information provided has been useful to you. Feel free to contact us if you have any questions or need further assistance. See you next time and dont miss to bookmark.
Featured Posts
-
Hda Technology Inc
Jan 02, 2025
-
Bcforward India Technologies Private Limited
Jan 02, 2025
-
2002 In Technology
Jan 02, 2025
-
Technology Discord
Jan 02, 2025
-
Criminal Justice Technology Jobs
Jan 02, 2025