Motor Control Technology
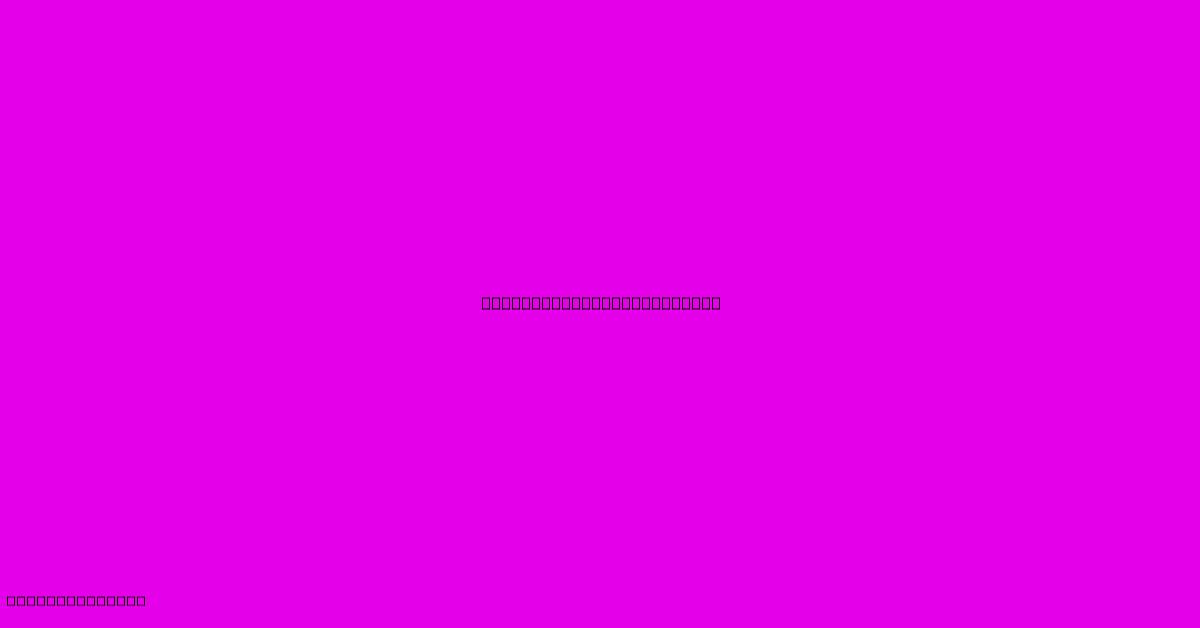
Discover more detailed and exciting information on our website. Click the link below to start your adventure: Visit Best Website mr.cleine.com. Don't miss out!
Table of Contents
Mastering Motion: A Deep Dive into Motor Control Technology
Motor control technology is the backbone of countless modern applications, from the smallest robotic actuators to the largest industrial machinery. Understanding its intricacies is key to appreciating the advancements driving automation and efficiency across various sectors. This article explores the core principles, diverse types, and future trends shaping this vital field.
What is Motor Control Technology?
Motor control technology encompasses the systems and techniques used to regulate and manage the speed, torque, and position of electric motors. This precise manipulation is achieved through sophisticated electronic circuits and algorithms that interface with the motor, allowing for seamless operation and control. The goal is to optimize motor performance based on specific application demands, maximizing efficiency and minimizing energy consumption.
Types of Motor Control Systems
Several methods exist for controlling electric motors, each with its own strengths and weaknesses:
1. Open-Loop Control: This simpler approach uses pre-determined commands to drive the motor. Feedback from the motor's output is not incorporated into the control algorithm. While less complex and cost-effective, open-loop control is less accurate and prone to errors due to external disturbances. Applications often include simple fan speed control.
2. Closed-Loop Control: In contrast, closed-loop control employs feedback mechanisms to continually monitor the motor's actual performance and compare it to the desired setpoint. This feedback, often from sensors like encoders or tachometers, allows for precise adjustments, ensuring the motor operates as intended despite variations in load or other external influences. Closed-loop systems are highly accurate and robust, ideal for applications requiring precise positioning or speed control like robotics and CNC machining. PID (Proportional-Integral-Derivative) control is a common and effective closed-loop algorithm.
3. Vector Control: Designed for AC motors, particularly those in high-performance applications, vector control allows for independent control of torque and flux. This sophisticated technique significantly improves dynamic response and efficiency, enabling precise control even under varying load conditions.
4. Direct Torque Control (DTC): DTC offers a simpler alternative to vector control, eliminating the need for complex coordinate transformations. It directly controls the motor's torque and flux through switching patterns, providing fast response and high-efficiency operation.
Key Components of a Motor Control System
A typical motor control system comprises several essential components:
- Microcontroller/Processor: The "brain" of the system, responsible for executing the control algorithms and processing sensor feedback.
- Power Electronics: This includes inverters, drivers, and other components that convert the input power into the appropriate form for driving the motor.
- Sensors: These devices (encoders, tachometers, current sensors) monitor the motor's performance and provide feedback to the control system.
- Feedback Control Loop: The core of closed-loop control systems, comparing the actual motor performance with the desired setpoint and making necessary adjustments.
Applications of Motor Control Technology
The versatility of motor control technology is evident across a wide range of industries and applications:
- Industrial Automation: Robotics, CNC machines, automated assembly lines.
- Automotive: Electric vehicle motors, power steering, anti-lock braking systems.
- Aerospace: Flight control systems, actuator control.
- Renewable Energy: Wind turbines, solar tracking systems.
- Home Appliances: Washing machines, refrigerators, air conditioners.
Future Trends in Motor Control Technology
The field of motor control is constantly evolving, driven by advancements in several key areas:
- Artificial Intelligence (AI) and Machine Learning (ML): AI and ML are being integrated into motor control systems to optimize performance, predict failures, and adapt to changing operating conditions.
- Power Semiconductor Advancements: More efficient and higher-power semiconductor devices are enabling the development of more compact and efficient motor control systems.
- Wireless Communication: Wireless communication protocols are enabling remote monitoring and control of motors, improving maintenance and accessibility.
Conclusion
Motor control technology is a crucial element in the modern world, empowering a wide array of applications. Its continuous evolution, driven by technological advancements and increasing demands for efficiency and precision, promises even more innovative solutions in the years to come. From optimizing energy consumption to enabling groundbreaking automation, the future of motor control is undoubtedly bright.
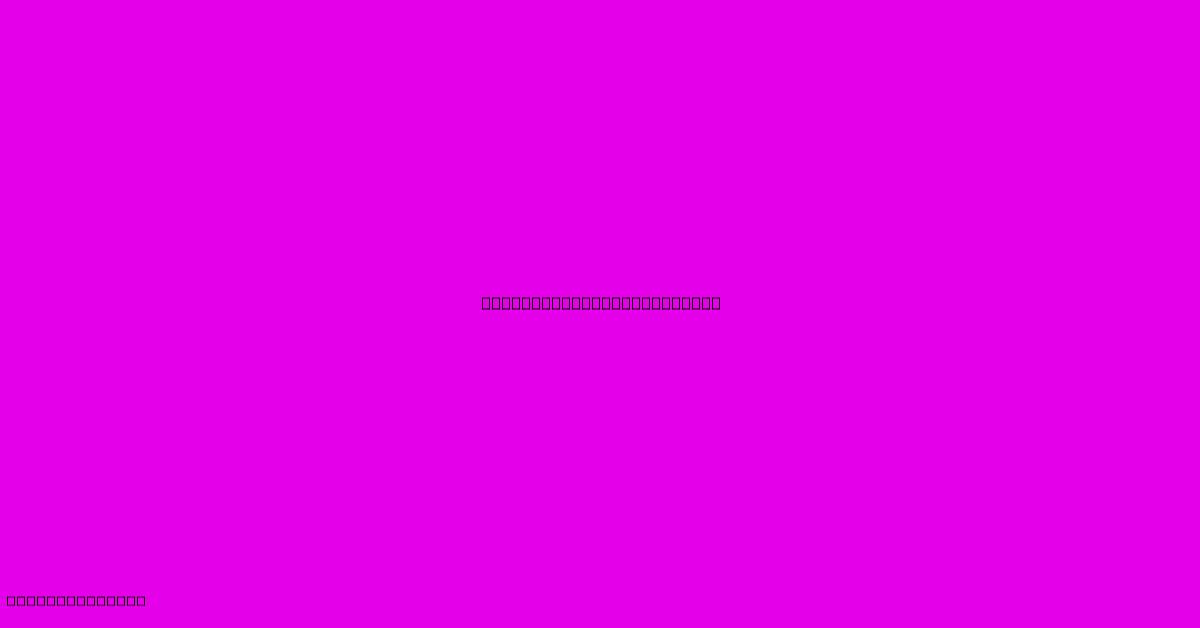
Thank you for visiting our website wich cover about Motor Control Technology. We hope the information provided has been useful to you. Feel free to contact us if you have any questions or need further assistance. See you next time and dont miss to bookmark.
Featured Posts
-
Watch Jets Vs Bills Nfl Week 17
Dec 30, 2024
-
Fluid Technology
Dec 30, 2024
-
Renaissance Technologies Salary Reddit
Dec 30, 2024
-
Avnet Technology Solutions Careers
Dec 30, 2024
-
Le Brons 40th Career Retrospective
Dec 30, 2024