Metal Work Technology
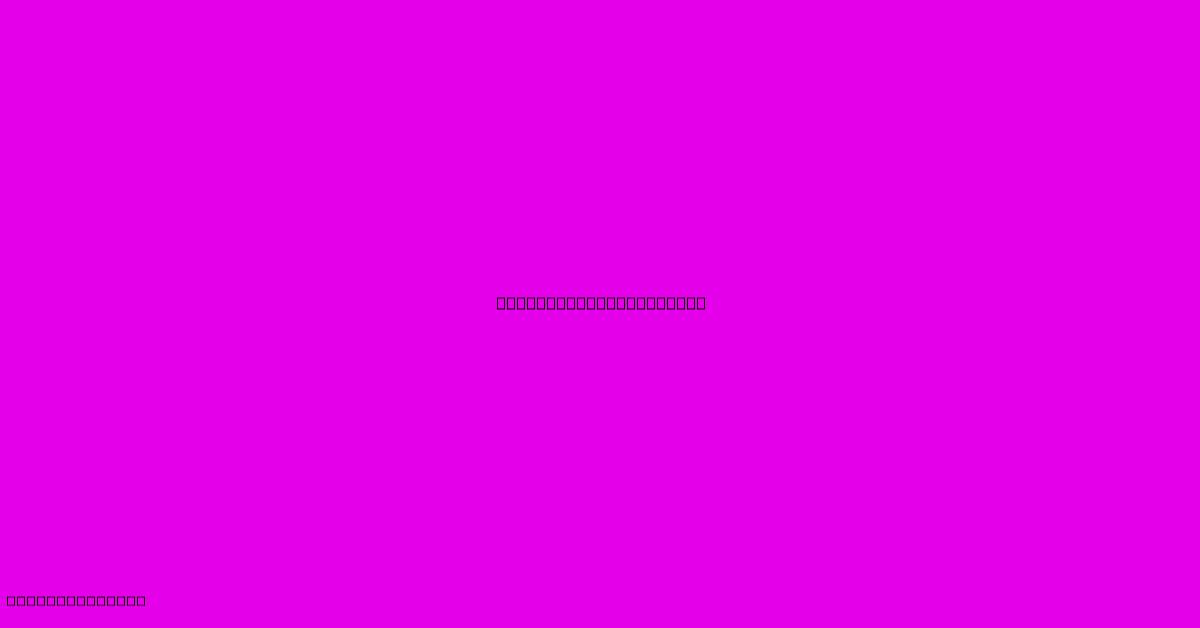
Discover more detailed and exciting information on our website. Click the link below to start your adventure: Visit Best Website mr.cleine.com. Don't miss out!
Table of Contents
Mastering Metal: A Deep Dive into Metal Work Technology
Metalworking technology encompasses a vast array of processes used to shape and modify metals into functional and aesthetic forms. From ancient blacksmithing to modern-day CNC machining, the evolution of these techniques has revolutionized industries and continues to drive innovation. This comprehensive guide delves into the key aspects of metal work technology, exploring its diverse methods, applications, and future trends.
Fundamental Metalworking Processes:
Metalworking processes can be broadly categorized into several key techniques:
1. Casting: This ancient method involves melting metal and pouring it into a mold. Once cooled and solidified, the metal takes the shape of the mold. Casting offers high flexibility in creating complex shapes but can result in less precise dimensions. Different casting methods exist, including:
- Sand Casting: Uses sand molds, offering cost-effectiveness for large-scale production.
- Investment Casting (Lost-Wax Casting): Creates highly detailed parts using a wax pattern.
- Die Casting: Employs metal molds for high-volume production of consistent parts.
2. Forming: Forming processes shape metal without removing material. Common forming methods include:
- Rolling: Reduces the thickness of a metal sheet by passing it through rollers.
- Forging: Shaping metal by hammering or pressing it using dies. Forging enhances metal strength.
- Extrusion: Pushing heated metal through a die to create a specific shape, often used for long, continuous profiles.
- Drawing: Pulling metal through a die to reduce its diameter, creating wires or tubes.
- Bending: Forming metal into a desired angle or curve.
3. Machining: Machining employs cutting tools to remove material, achieving precise dimensions and surface finishes. Key machining processes include:
- Turning: Rotating a workpiece against a cutting tool to create cylindrical shapes.
- Milling: Using rotating cutters to remove material from a stationary workpiece.
- Drilling: Creating holes in a workpiece using a rotating drill bit.
- Grinding: Removing material using abrasive wheels for high precision and surface smoothness.
- Computer Numerical Control (CNC) Machining: Automated machining controlled by computer programs, enabling high precision and repeatability. This is a cornerstone of modern metalworking.
4. Joining: Joining methods unite metal pieces without casting or forming. Popular joining techniques include:
- Welding: Melting and fusing metal pieces together using heat and often filler material. Different welding methods exist (e.g., arc welding, MIG welding, TIG welding).
- Brazing: Joining metal parts using a filler metal with a lower melting point than the base metal.
- Soldering: Similar to brazing, but uses a filler metal with an even lower melting point.
- Riveting: Fastening metal pieces using rivets.
- Bolting: Using bolts and nuts to securely connect metal components.
5. Finishing: Metal finishing enhances the appearance and properties of metal parts. This includes processes like:
- Polishing: Creating a smooth, shiny surface.
- Plating: Applying a thin layer of another metal to improve corrosion resistance or aesthetics.
- Painting/Coating: Protecting metal from corrosion and enhancing appearance.
- Heat Treating: Altering the metal's microstructure to improve its properties (e.g., strength, hardness).
Applications of Metalworking Technology:
Metalworking technology finds applications across numerous industries:
- Automotive: Manufacturing car bodies, engines, and components.
- Aerospace: Producing aircraft parts, engines, and spacecraft structures.
- Construction: Creating structural elements, tools, and machinery.
- Manufacturing: Producing a wide range of goods, from consumer products to industrial equipment.
- Medical: Creating surgical instruments, implants, and medical devices.
Future Trends in Metalworking Technology:
The field of metalworking is constantly evolving, with several key trends shaping its future:
- Additive Manufacturing (3D Printing): Creating metal parts layer by layer from a digital design, offering design flexibility and reduced material waste.
- Automation and Robotics: Increased use of robots and automated systems to improve efficiency and precision.
- Smart Manufacturing: Integration of data analytics and AI to optimize metalworking processes.
- Sustainable Practices: Focus on reducing environmental impact through efficient resource use and waste reduction.
Conclusion:
Metalworking technology is a critical field driving innovation across diverse industries. Understanding the various processes, their applications, and emerging trends is essential for anyone involved in manufacturing, engineering, or related fields. As technology continues to advance, the possibilities for metalworking are only set to expand further.
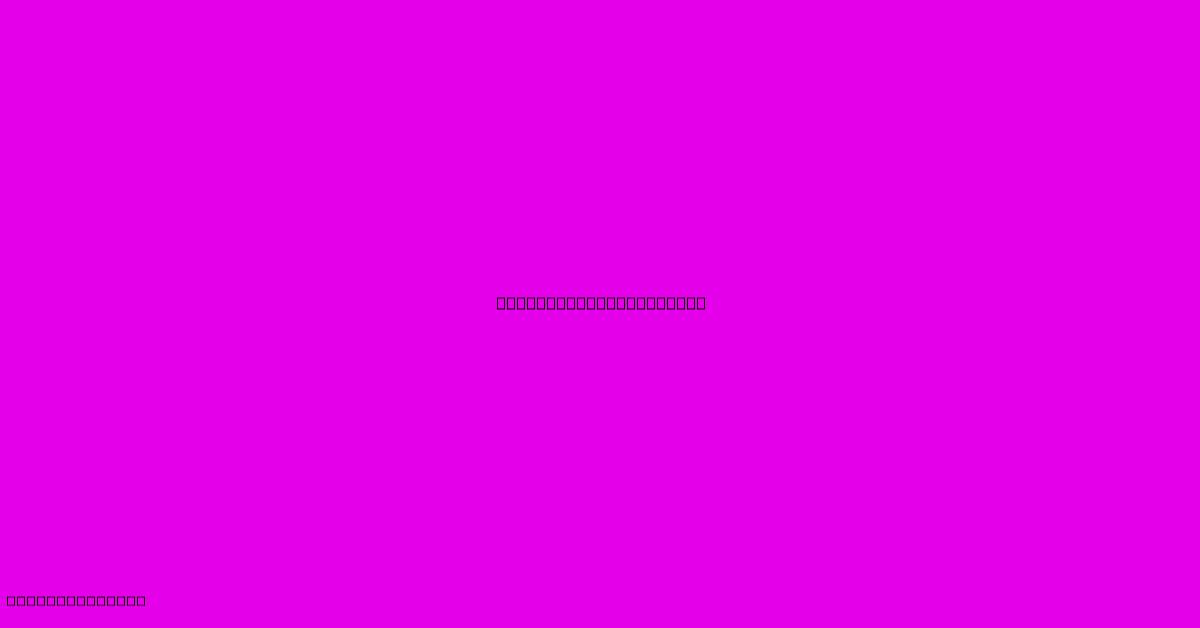
Thank you for visiting our website wich cover about Metal Work Technology. We hope the information provided has been useful to you. Feel free to contact us if you have any questions or need further assistance. See you next time and dont miss to bookmark.
Featured Posts
-
Clarix Technologies
Dec 23, 2024
-
Align Technology Internship
Dec 23, 2024
-
Optimal Solutions And Technologies
Dec 23, 2024
-
Manchester United X Bournemouth Onde Assistir
Dec 23, 2024
-
Kejutan Arab Saudi Juru Kunci Grup
Dec 23, 2024