Metal Removal Technologies
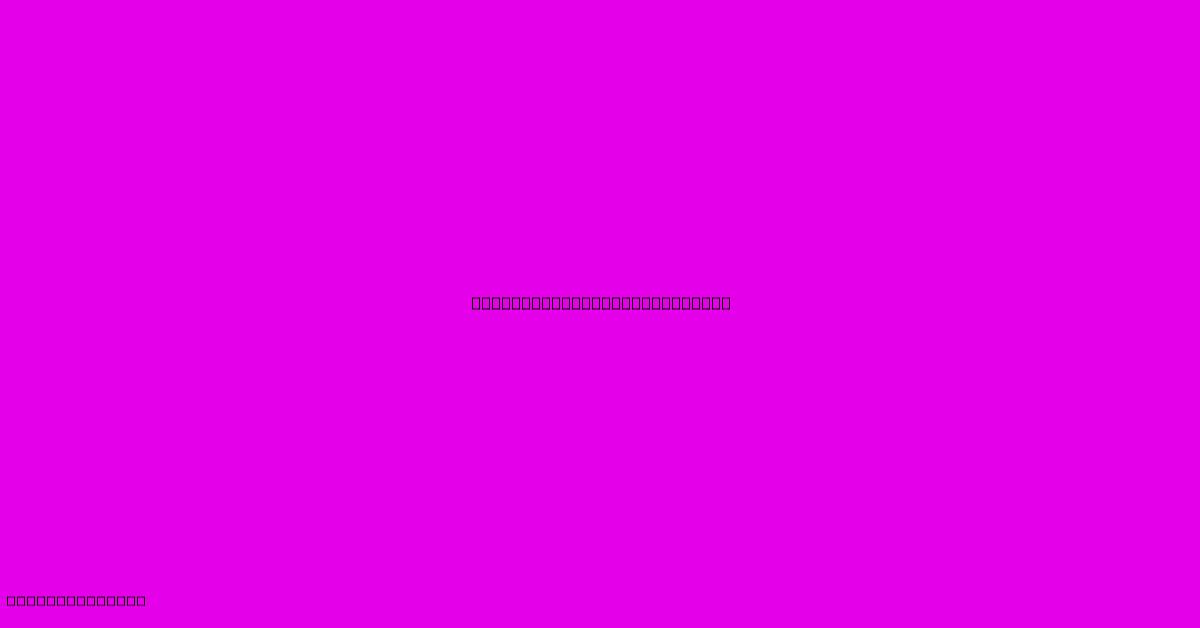
Discover more detailed and exciting information on our website. Click the link below to start your adventure: Visit Best Website mr.cleine.com. Don't miss out!
Table of Contents
Metal Removal Technologies: A Comprehensive Overview
Metal removal, also known as machining, is a crucial process in manufacturing, shaping metal components into their desired forms and dimensions. This involves removing unwanted material from a workpiece using various techniques. The choice of method depends on factors like the material's properties, the desired precision, production volume, and cost considerations. Let's explore the key metal removal technologies:
1. Turning:
This is one of the oldest and most common metal removal processes. A rotating workpiece is cut by a single-point cutting tool, creating cylindrical shapes. Turning can produce various features like shafts, pins, and shoulders.
- Sub-processes: Facing, boring, parting, threading.
- Advantages: High material removal rate, relatively low cost, versatile.
- Disadvantages: Limited to rotational symmetry, can generate significant heat and vibration.
2. Milling:
Milling uses a rotating multi-point cutting tool to remove material from a workpiece, enabling the creation of complex shapes and features. Different types of milling exist, including face milling, end milling, and peripheral milling.
- Sub-processes: Pocket milling, slotting, contour milling.
- Advantages: High versatility, capable of producing intricate geometries.
- Disadvantages: Can be slower than turning for simple shapes, requires more sophisticated machines.
3. Drilling:
Drilling creates cylindrical holes in a workpiece. A rotating drill bit removes material as it penetrates the material. Different drill bit designs cater to various hole sizes and materials.
- Sub-processes: Reaming, tapping, counterboring.
- Advantages: Simple and efficient for hole creation.
- Disadvantages: Limited to cylindrical holes, can be challenging in hard materials.
4. Grinding:
Grinding uses abrasive wheels to remove small amounts of material, achieving high surface finish and precision. It's often used for finishing operations or sharpening tools.
- Sub-processes: Surface grinding, cylindrical grinding, internal grinding.
- Advantages: High precision, excellent surface finish.
- Disadvantages: Slow material removal rate, requires specialized equipment.
5. Shaping and Planing:
These processes use a reciprocating tool to remove material from a workpiece. Shaping cuts horizontally, while planing cuts vertically. They are less common due to slower material removal compared to modern methods.
- Advantages: Capable of creating complex shapes, relatively simple machines.
- Disadvantages: Slow, limited precision compared to modern techniques.
6. Broaching:
Broaching uses a multi-tooth tool to remove material in a single pass, creating complex internal and external shapes like keyways and splines. It's highly efficient for high-volume production.
- Advantages: High production rates, precise dimensions.
- Disadvantages: High initial tool cost, limited to specific shapes.
7. Electrochemical Machining (ECM):
ECM uses an electrochemical process to remove material. An electric current dissolves the workpiece material, enabling the creation of complex shapes in difficult-to-machine materials.
- Advantages: Can machine hard materials, produces complex geometries.
- Disadvantages: Requires specialized equipment, slower than traditional methods.
8. Electrical Discharge Machining (EDM):
EDM uses electrical sparks to remove material. A series of controlled sparks erode the workpiece, allowing for precise machining of intricate shapes, including those with undercuts.
- Advantages: Can machine very hard materials, creates complex shapes.
- Disadvantages: Slow process, requires specialized equipment.
9. Laser Cutting:
Laser cutting uses a high-powered laser beam to melt and vaporize material, creating precise cuts. It is particularly suited for thin sheet metal and intricate designs.
- Advantages: High precision, fast for thin materials, minimal heat-affected zone.
- Disadvantages: Can be expensive, limited to certain materials and thicknesses.
Choosing the Right Technology:
The selection of the appropriate metal removal technology depends on several factors:
- Material Properties: Hardness, toughness, machinability.
- Desired Accuracy and Finish: Tolerance requirements, surface roughness.
- Production Volume: High volume favors processes like broaching, while low volume might justify more versatile methods.
- Cost: Balancing initial investment in equipment and tooling with operational costs.
- Complexity of the Part: Simple shapes can be produced efficiently using turning, while complex parts may require milling, EDM, or ECM.
This overview provides a foundation for understanding the diverse range of metal removal technologies. Further research into specific processes is crucial for effective implementation in any manufacturing environment. Understanding the strengths and limitations of each technique is essential for optimizing efficiency, precision, and cost-effectiveness in metalworking operations.
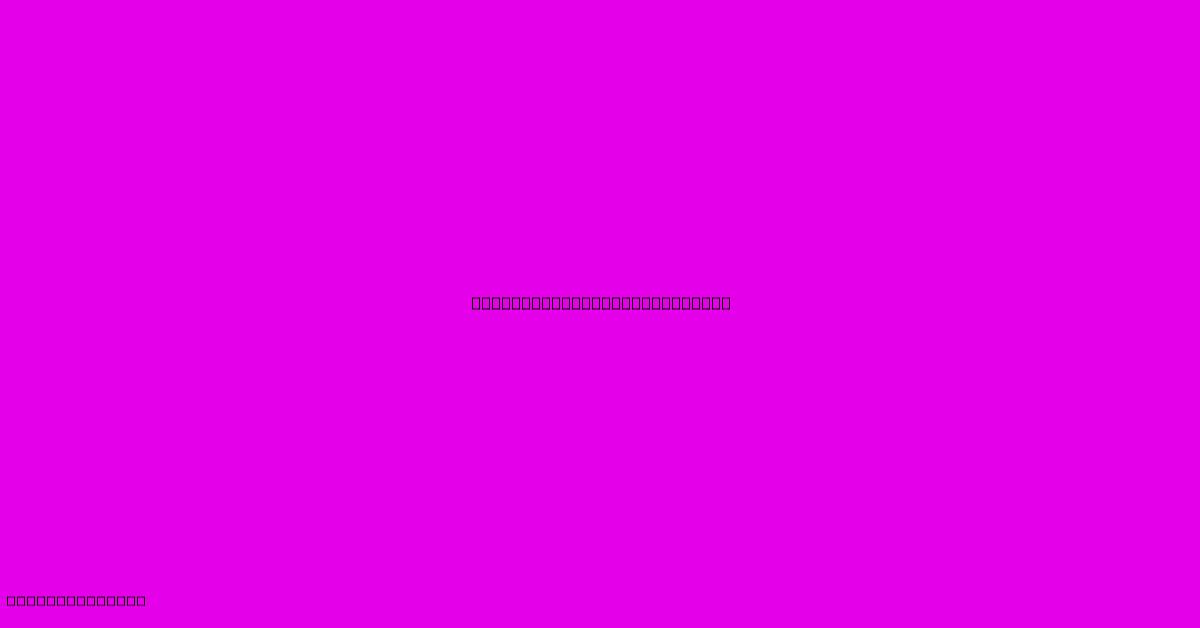
Thank you for visiting our website wich cover about Metal Removal Technologies. We hope the information provided has been useful to you. Feel free to contact us if you have any questions or need further assistance. See you next time and dont miss to bookmark.
Featured Posts
-
Rochester Institute Of Technology Game Design
Dec 31, 2024
-
Supply Technologies Mn
Dec 31, 2024
-
Jobs For Textile Technology
Dec 31, 2024
-
Riset Kata Kunci Yang Komprehensif Gunakan Alat Riset Kata Kunci Untuk Menemukan Istilah Pencarian Yang Relevan Seperti Analisis Saham Adani Adani Wilmar Prospek Investasi Adani Enterprises Dan Lain Lain Incorporasikan Kata Kunci Ini Secara Alami Dalam Judul Subjudul Dan Isi Artikel
Dec 31, 2024
-
Guide To Nye 2024 Fireworks Viewing
Dec 31, 2024