Metal Finishing Technologies
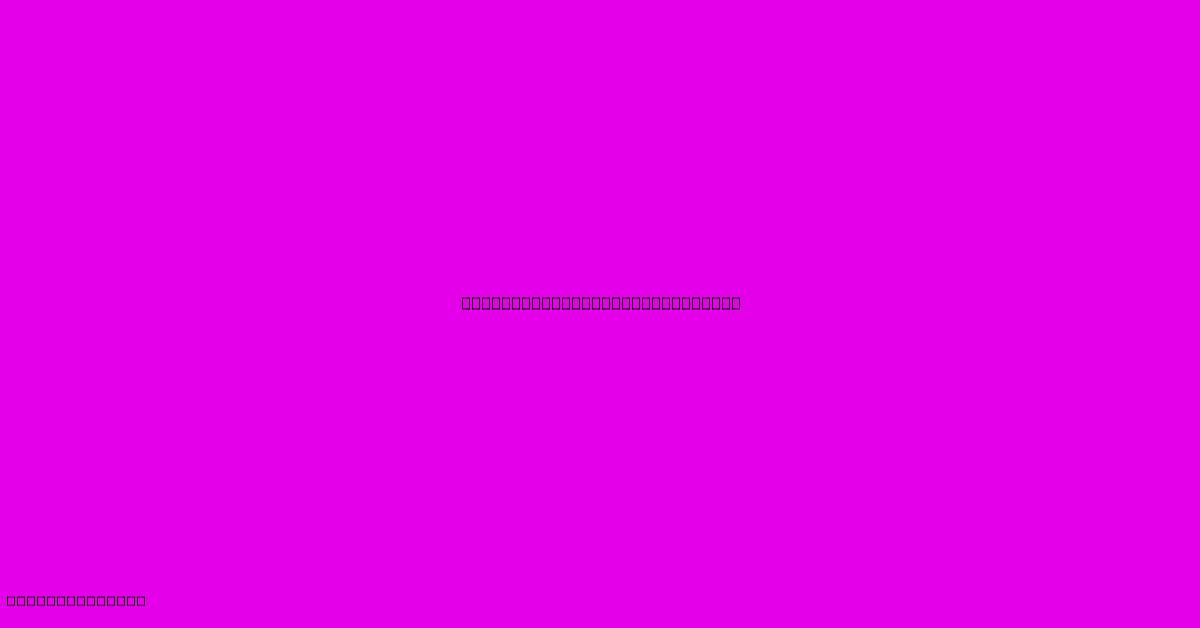
Discover more detailed and exciting information on our website. Click the link below to start your adventure: Visit Best Website mr.cleine.com. Don't miss out!
Table of Contents
Metal Finishing Technologies: Enhancing Aesthetics and Performance
Metal finishing encompasses a broad range of processes aimed at enhancing the surface properties of metals. These processes improve aesthetics, corrosion resistance, wear resistance, and other critical performance characteristics. From decorative finishes for jewelry to protective coatings for automotive parts, metal finishing plays a crucial role in numerous industries. This article delves into various key metal finishing technologies.
1. Electroplating: A Foundation of Metal Finishing
Electroplating, a cornerstone of metal finishing, involves depositing a thin layer of metal onto a substrate using an electric current. This process offers excellent control over coating thickness and uniformity.
Types of Electroplating:
- Chrome plating: Known for its hardness, corrosion resistance, and high reflectivity, chrome plating is widely used in automotive parts, plumbing fixtures, and decorative items.
- Nickel plating: Offers good corrosion resistance and acts as an undercoat for other plating processes like chrome. It's commonly used in electronics and appliances.
- Zinc plating: Provides excellent corrosion protection, especially for steel components. It's often used in fasteners and automotive parts.
- Gold plating: Employed for its excellent conductivity, corrosion resistance, and attractive appearance, gold plating is commonly found in electronics and jewelry.
- Silver plating: Used for its conductivity and reflectivity, making it suitable for tableware, electronics, and jewelry.
Advantages of Electroplating:
- Excellent corrosion protection: Provides a barrier against environmental factors.
- Enhanced wear resistance: Increases the durability of metal components.
- Improved aesthetics: Creates attractive and uniform surface finishes.
- Cost-effective: Relatively inexpensive for many applications.
2. Electroless Plating: Chemical Deposition for Uniform Coatings
Unlike electroplating, electroless plating doesn't require an external electric current. Instead, it relies on a chemical reduction process to deposit metal onto the substrate. This method is particularly effective for achieving uniform coatings on complex shapes.
Applications of Electroless Plating:
- Electronics: Creating uniform conductive layers on circuit boards.
- Medical devices: Producing biocompatible coatings on implants.
- Aerospace: Applying wear-resistant coatings on components.
3. Anodizing: Surface Oxidation for Aluminum
Anodizing is an electrochemical process that creates a thick, protective oxide layer on aluminum and its alloys. This layer enhances corrosion resistance, wear resistance, and provides a base for further coloring or sealing.
Types of Anodizing:
- Hard anodizing: Creates a very hard, wear-resistant coating suitable for aerospace and industrial applications.
- Architectural anodizing: Produces a decorative and durable finish for building exteriors.
4. Powder Coating: Durable Polymer Coatings
Powder coating applies dry powder paint to a metal substrate, which is then cured using heat. This process produces a durable, chip-resistant, and aesthetically pleasing finish.
Advantages of Powder Coating:
- Excellent durability: Highly resistant to chipping and scratching.
- Wide range of colors and textures: Offers great design flexibility.
- Environmentally friendly: Uses less solvent than traditional liquid paints.
5. Chemical Conversion Coatings: Phosphate, Chromate, and Others
Chemical conversion coatings modify the surface of a metal through chemical reactions, creating a protective layer. These coatings offer corrosion resistance and improve paint adhesion.
Examples of Chemical Conversion Coatings:
- Phosphate coatings: Commonly used on steel to enhance paint adhesion and corrosion resistance.
- Chromate coatings: Provide excellent corrosion protection but are increasingly restricted due to environmental concerns.
Choosing the Right Metal Finishing Technology:
Selecting the appropriate metal finishing technology depends on several factors, including:
- Type of metal: Different metals require different finishing processes.
- Desired properties: Corrosion resistance, wear resistance, aesthetics, and cost all play a role.
- Application: The intended use of the finished part will dictate the best approach.
Metal finishing is a dynamic field constantly evolving with new technologies and advancements. Understanding the various options available is crucial for choosing the optimal process to meet specific performance and aesthetic requirements.
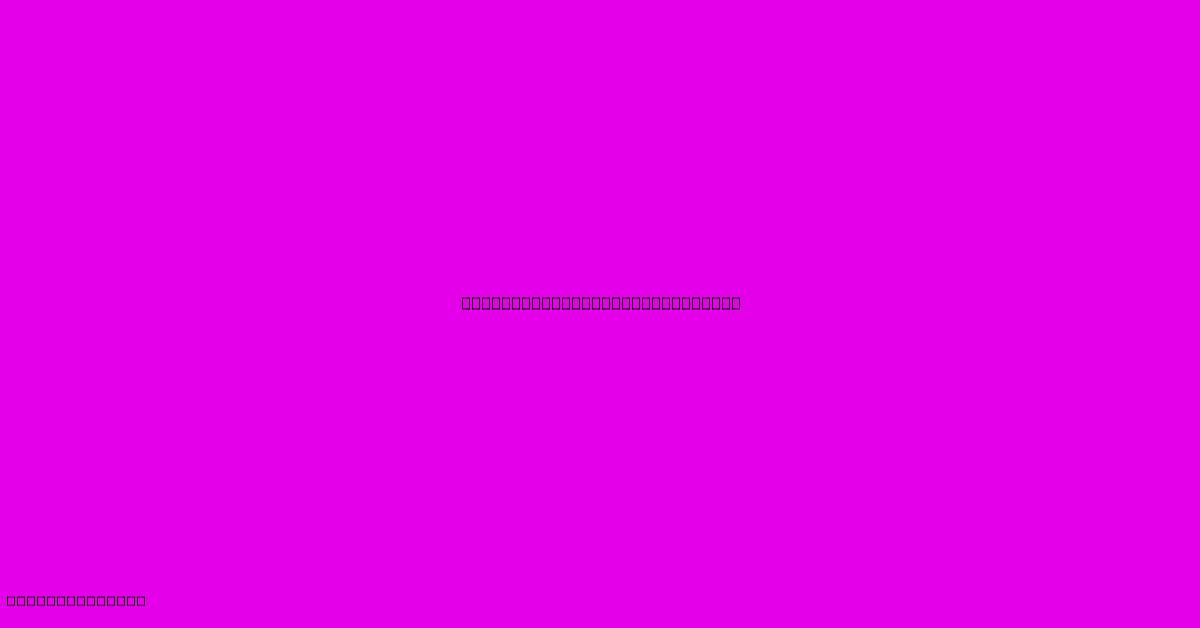
Thank you for visiting our website wich cover about Metal Finishing Technologies. We hope the information provided has been useful to you. Feel free to contact us if you have any questions or need further assistance. See you next time and dont miss to bookmark.
Featured Posts
-
Mysterio Sr Death Confirmed
Dec 21, 2024
-
Malaysia Tersingkir Aff Pelatih Tak Cari Alasan
Dec 21, 2024
-
The Voice Kids 3 Melissa Memeti Vince
Dec 21, 2024
-
Blockchain Technology Reduces Fraud And Improves Efficiency
Dec 21, 2024
-
El Technologies
Dec 21, 2024