Mdf Technology
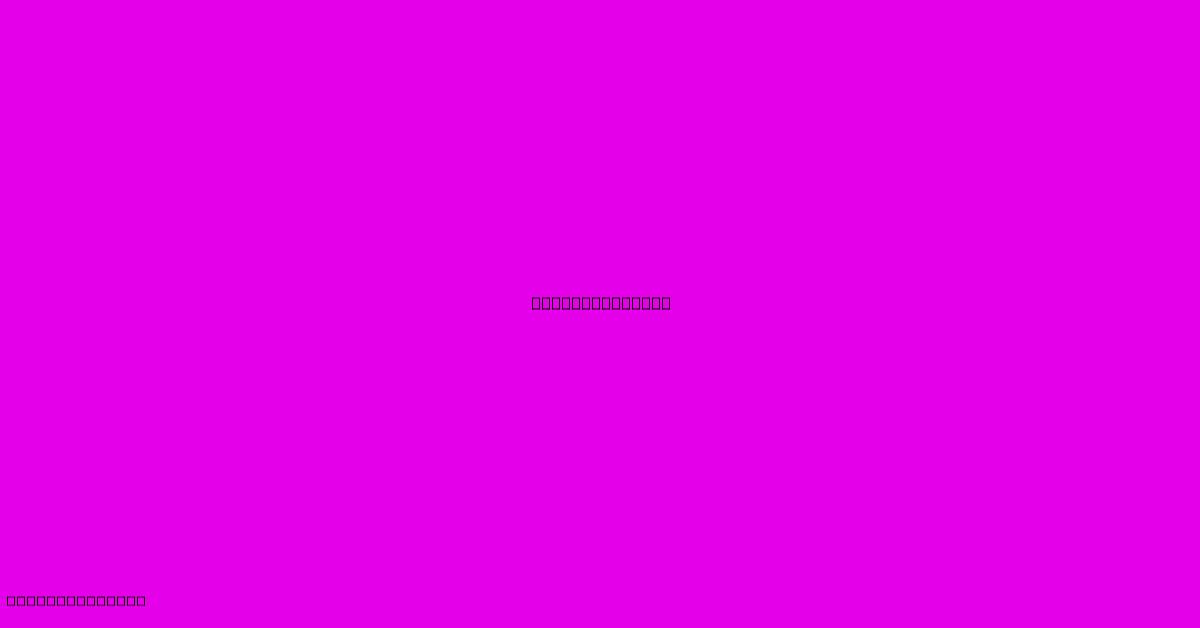
Discover more detailed and exciting information on our website. Click the link below to start your adventure: Visit Best Website mr.cleine.com. Don't miss out!
Table of Contents
MDF Technology: A Deep Dive into Medium-Density Fiberboard
Medium-density fiberboard (MDF) has become a ubiquitous material in manufacturing and construction, thanks to its versatility, affordability, and ease of processing. This article delves into the technology behind MDF, exploring its production process, properties, advantages, disadvantages, and diverse applications.
What is MDF?
MDF is an engineered wood product manufactured by breaking down hardwood or softwood residuals into wood fibers, often combining them with wax and a resin binder, then forming them into panels by applying high temperature and pressure. This process creates a dense, homogenous material with consistent properties throughout. Unlike plywood, which is made from layers of veneer, MDF has a uniform structure, making it ideal for a wide range of applications.
The MDF Manufacturing Process:
The creation of MDF involves several key steps:
-
Wood Preparation: Hardwood or softwood residues are chipped and refined into wood fibers. The size and type of fiber affect the final product's properties.
-
Fiber Refining: The fibers are further refined to create a consistent size and distribution, optimizing bonding and density.
-
Resin and Wax Addition: A resin binder (usually urea-formaldehyde or melamine-urea-formaldehyde) is added to the fibers along with wax. The resin binds the fibers together, while wax improves water resistance and reduces swelling.
-
Mat Formation: The fiber-resin-wax mixture is formed into a mat using a sophisticated process that controls thickness and density.
-
Hot Pressing: The mat is pressed using a high-temperature and high-pressure process, which consolidates the fibers and cures the resin, creating a solid panel.
-
Cooling and Finishing: The panel is cooled and then finished through sanding and sizing to achieve the desired surface quality and dimensions.
Properties of MDF:
- Density: Typically ranges from 500 to 850 kg/m³, resulting in good strength and stability.
- Smooth Surface: Its smooth, homogenous surface allows for easy machining, painting, and finishing.
- Dimensional Stability: MDF is relatively stable in terms of expansion and contraction with changes in humidity.
- Strength: Offers good strength and stiffness, making it suitable for various structural applications.
- Versatility: Its properties make it easy to shape, cut, and rout, enabling complex designs.
Advantages of Using MDF:
- Cost-Effective: Compared to solid wood, MDF is generally less expensive.
- Easy to Work With: Its uniform density allows for precise machining and clean cuts.
- Smooth Finish: Excellent surface for painting and finishing, resulting in high-quality finishes.
- Versatile: Adaptable to various applications, from furniture to architectural components.
- Strong and Stable: Provides good strength and stability, making it suitable for many structural applications.
Disadvantages of Using MDF:
- Water Sensitivity: Although wax improves water resistance, MDF is still susceptible to moisture damage and swelling.
- Screw Holding Capacity: It can be challenging to drive screws into MDF without pre-drilling pilot holes.
- Formaldehyde Emissions: Some MDF products may release formaldehyde, a volatile organic compound (VOC), which can be harmful to health. Look for low-formaldehyde or formaldehyde-free options.
- Not Ideal for Outdoor Use: Its sensitivity to moisture makes it unsuitable for prolonged outdoor exposure.
Applications of MDF:
MDF finds extensive use in a vast array of applications, including:
- Furniture Manufacturing: Widely used in the production of cabinets, shelves, drawers, and other furniture components.
- Interior Design: Used in wall panels, decorative moldings, and architectural elements.
- Construction: Employed in flooring underlayment, door cores, and other construction elements.
- Manufacturing: Used in various industrial applications, including signage, display cases, and custom-made products.
Conclusion:
MDF technology provides a cost-effective and versatile material with a wide range of applications. Understanding its properties and limitations is crucial for choosing the right material for a specific project. By selecting appropriately treated MDF and following best practices, manufacturers and users can benefit from its advantages while mitigating its drawbacks. The continued development and refinement of MDF manufacturing processes are likely to expand its capabilities and further solidify its position as a leading engineered wood product.
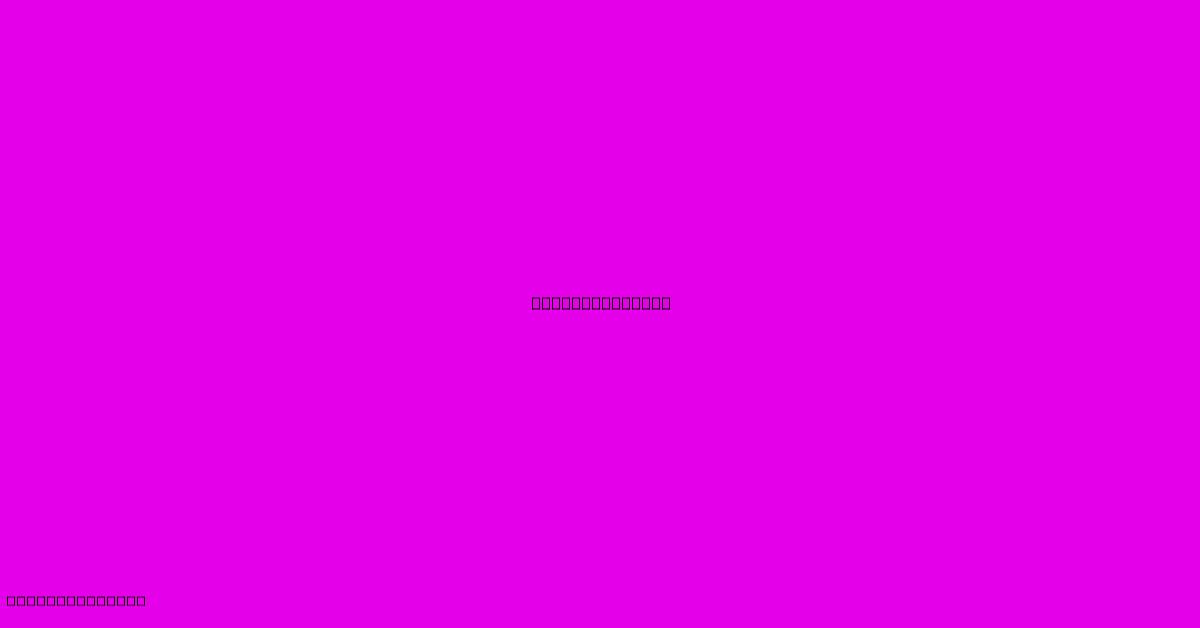
Thank you for visiting our website wich cover about Mdf Technology. We hope the information provided has been useful to you. Feel free to contact us if you have any questions or need further assistance. See you next time and dont miss to bookmark.
Featured Posts
-
Barnskadisar Fran Johanna
Dec 25, 2024
-
Wellfit Technologies
Dec 25, 2024
-
Assistive Technology Professional Jobs
Dec 25, 2024
-
Yellowstone Stars Holiday Tradition
Dec 25, 2024
-
A A A Y A A Y A A A A A A Y A A A A A A A A Ye A A A A Y A A A Y A A A A Y A A A Y A A A Y A A Y A A A A Y A A A A A Y A A A A Y A A A A A A A A Y A A Y A A Y A A A A Y A A A Y
Dec 25, 2024