Material Handling Technologies
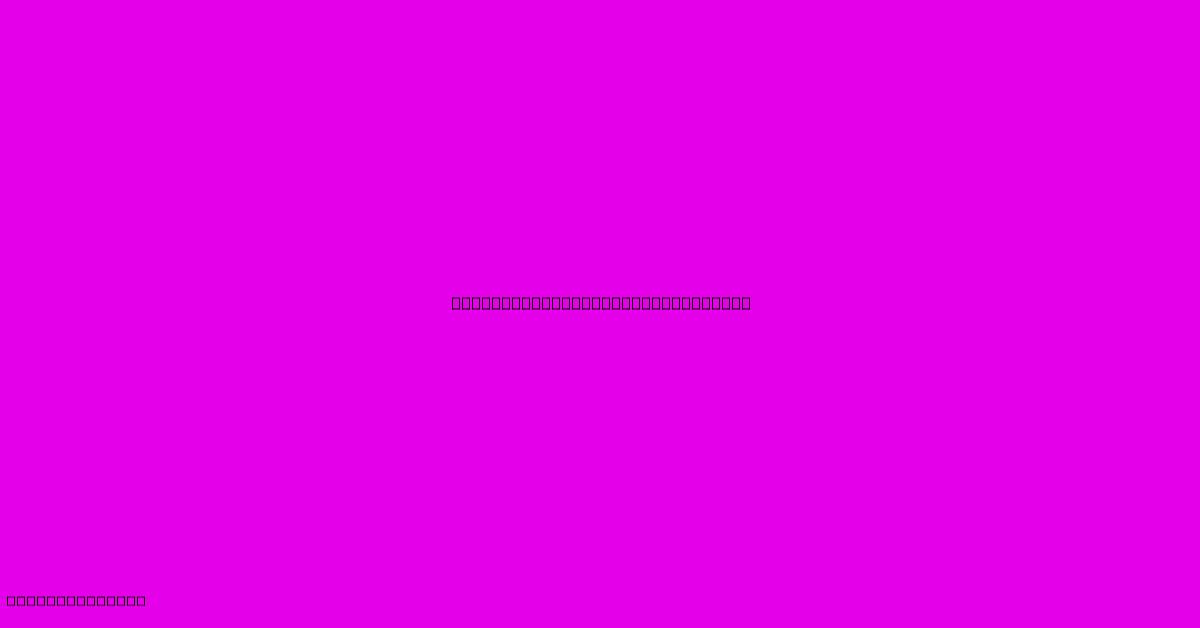
Discover more detailed and exciting information on our website. Click the link below to start your adventure: Visit Best Website mr.cleine.com. Don't miss out!
Table of Contents
Revolutionizing Efficiency: A Deep Dive into Material Handling Technologies
Material handling, the movement, storage, control, and protection of materials, is the backbone of efficient operations across various industries. From manufacturing and warehousing to logistics and retail, optimizing material handling processes directly impacts productivity, cost-effectiveness, and overall success. This article explores the diverse landscape of modern material handling technologies, examining their applications and benefits.
Understanding the Core Components of Material Handling
Effective material handling relies on a synergistic interplay of several key components:
-
Equipment: This encompasses a wide array of machinery, including forklifts, conveyor systems, cranes, automated guided vehicles (AGVs), and robotic systems. The choice of equipment depends heavily on the specific industry, the type of materials handled, and the overall layout of the facility.
-
Processes: Efficient material handling isn't just about the equipment; it's also about the processes that govern the movement of materials. This includes inventory management, order fulfillment, and warehouse layout optimization. Lean manufacturing principles and Six Sigma methodologies are frequently employed to streamline these processes.
-
Software and Automation: Modern material handling relies heavily on sophisticated software solutions, including warehouse management systems (WMS), transportation management systems (TMS), and enterprise resource planning (ERP) systems. These systems integrate data from various sources, enabling real-time tracking, optimized routing, and predictive analytics. Automation, through robotics and AI, is increasingly vital for enhancing efficiency and accuracy.
Key Material Handling Technologies
1. Conveyors: These systems automate the movement of goods along a predetermined path, reducing manual labor and improving throughput. Types include belt conveyors, roller conveyors, and chain conveyors, each suitable for different materials and applications.
2. Forklifts: A ubiquitous piece of equipment, forklifts remain essential for moving palletized goods within warehouses and factories. Recent advancements include electric forklifts, which offer greater efficiency and reduced emissions.
3. Automated Guided Vehicles (AGVs): AGVs utilize sensors and guidance systems to navigate autonomously, carrying materials along pre-programmed routes. This technology is particularly beneficial in large warehouses or manufacturing plants, minimizing human intervention and improving safety.
4. Robotic Systems: Robots are transforming material handling, performing tasks such as picking, packing, palletizing, and sorting with speed and precision far exceeding human capabilities. Collaborative robots (cobots) are increasingly used to work alongside human employees, enhancing productivity and safety.
5. Warehouse Management Systems (WMS): WMS software provides a centralized platform for managing inventory, tracking shipments, optimizing warehouse layout, and coordinating material flow. Integration with other systems enables real-time visibility and control over the entire material handling process.
The Benefits of Advanced Material Handling
Implementing advanced material handling technologies offers numerous significant advantages:
-
Increased Efficiency: Automation and optimized processes lead to faster throughput and reduced cycle times.
-
Reduced Costs: Automation minimizes labor costs, reduces waste, and improves overall operational efficiency.
-
Improved Safety: Automation and sophisticated safety systems minimize the risk of workplace accidents.
-
Enhanced Accuracy: Automated systems reduce errors in picking, packing, and other material handling tasks.
-
Better Inventory Management: Real-time tracking and optimized storage strategies improve inventory control and reduce stockouts.
-
Increased Flexibility and Scalability: Advanced systems can easily adapt to changing demands and accommodate growth.
Challenges and Considerations
While the benefits are significant, implementing advanced material handling technologies requires careful consideration:
-
High Initial Investment: The cost of implementing new equipment and software can be substantial.
-
Integration Complexity: Integrating new systems with existing infrastructure can be challenging.
-
Maintenance and Support: Automated systems require ongoing maintenance and technical support.
-
Skills Gap: Operating and maintaining advanced technologies requires trained personnel.
Conclusion
Material handling technologies are constantly evolving, driven by the need for greater efficiency, productivity, and cost-effectiveness. By embracing these advancements, businesses can significantly optimize their operations and gain a competitive edge in today's dynamic marketplace. Careful planning, selection of appropriate technologies, and ongoing optimization are essential for realizing the full potential of these transformative solutions.
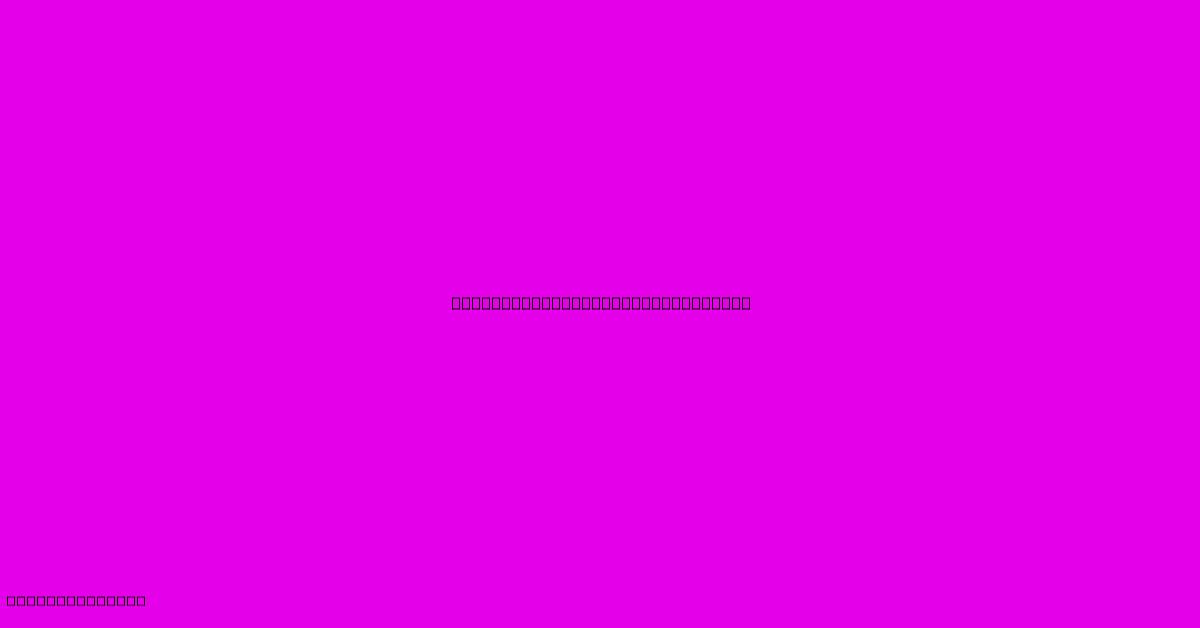
Thank you for visiting our website wich cover about Material Handling Technologies. We hope the information provided has been useful to you. Feel free to contact us if you have any questions or need further assistance. See you next time and dont miss to bookmark.
Featured Posts
-
Advanced Technology Drawing
Dec 26, 2024
-
Marketing Technology Conferences
Dec 26, 2024
-
Conference On Technology In Education
Dec 26, 2024
-
Washington High School Of Information Technology
Dec 26, 2024
-
Taylor Swift At Chiefs Steelers Game
Dec 26, 2024