Ld Technology Tm Flow System
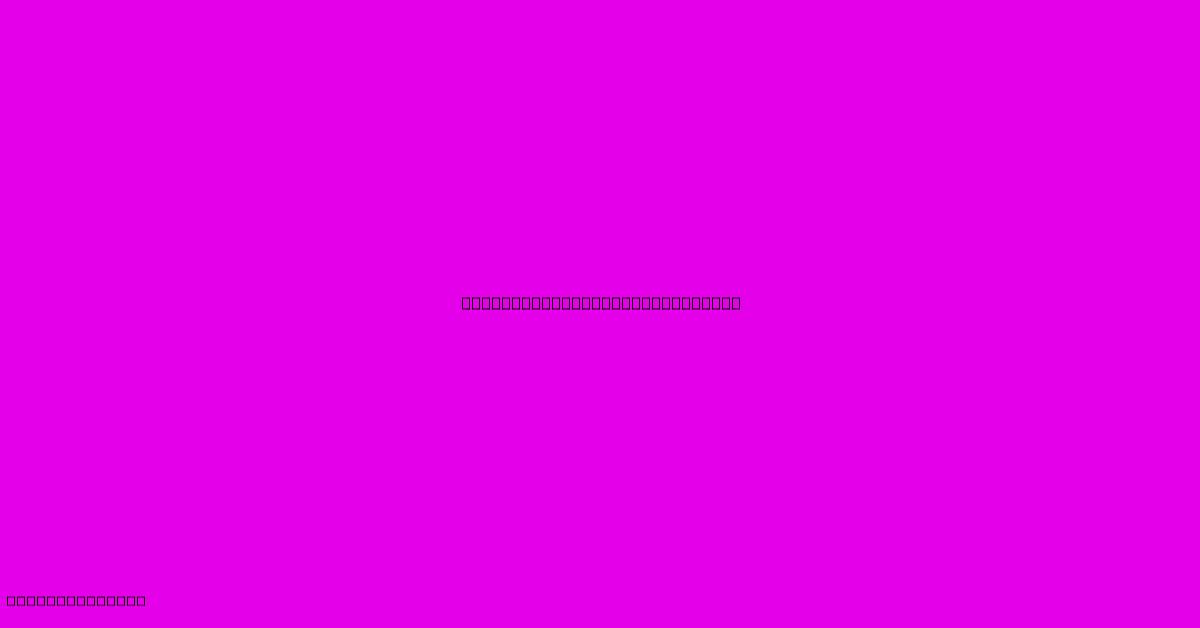
Discover more detailed and exciting information on our website. Click the link below to start your adventure: Visit Best Website mr.cleine.com. Don't miss out!
Table of Contents
LD Technology's TM Flow System: A Deep Dive into Automated Material Handling
LD Technology's TM Flow System represents a significant advancement in automated material handling solutions. This system, designed for efficiency and scalability, offers a compelling alternative to traditional conveyor systems, particularly in environments requiring high throughput and flexible routing. This article will explore the key features, benefits, and applications of the TM Flow System.
What is the TM Flow System?
The TM Flow System is a modular, autonomous material handling system utilizing independent, self-navigating carts. Unlike traditional conveyor belts which follow fixed paths, these carts move freely within a defined area, dynamically adapting to changing demands. This flexibility allows for efficient material flow even in complex layouts and with fluctuating order volumes. The system utilizes advanced sensor technology and sophisticated software to manage and optimize cart movement, minimizing congestion and maximizing throughput.
Key Features & Benefits:
-
Flexibility and Scalability: The modular design allows for easy expansion and reconfiguration to accommodate future growth and changing production needs. Adding or removing carts and modifying the system's layout is relatively straightforward.
-
Improved Throughput: By eliminating the bottlenecks inherent in fixed-path conveyor systems, the TM Flow System significantly increases throughput. Carts can navigate around obstacles and adjust their routes in real-time, maintaining efficient material flow even during peak demand.
-
Reduced Labor Costs: The automated nature of the system minimizes the need for manual handling, reducing labor costs and freeing up personnel for other tasks.
-
Enhanced Efficiency: The system optimizes routing and minimizes travel time through intelligent path planning, resulting in significantly improved efficiency compared to traditional methods.
-
Improved Safety: The system's intelligent control algorithms and safety features minimize the risk of collisions and other accidents, creating a safer working environment.
-
Real-Time Tracking and Monitoring: Comprehensive software provides real-time visibility into the system's operation, allowing for efficient monitoring and management of material flow. This facilitates proactive issue identification and resolution.
-
Reduced Space Requirements: The ability to dynamically route carts can lead to a more efficient use of space compared to traditional conveyor systems which require extensive fixed infrastructure.
Applications of the TM Flow System:
The TM Flow System's versatility makes it suitable for a wide range of applications, including:
-
E-commerce Fulfillment Centers: Efficiently handling a high volume of orders with varying sizes and destinations.
-
Manufacturing Plants: Streamlining the movement of components and finished goods throughout the production process.
-
Distribution Centers: Optimizing the flow of goods from receiving to shipping.
-
Warehousing: Automating the movement of inventory within the warehouse.
Comparison with Traditional Conveyor Systems:
While traditional conveyor systems offer simplicity and reliability in specific scenarios, they often lack the flexibility and scalability of the TM Flow System. The fixed paths of conveyor belts can become bottlenecks under fluctuating demand, leading to inefficiencies. The TM Flow System's dynamic routing and autonomous carts address these limitations, offering a more adaptable and efficient solution for complex material handling needs.
Conclusion:
LD Technology's TM Flow System represents a significant leap forward in automated material handling. Its flexibility, scalability, and efficiency make it a compelling option for businesses seeking to optimize their logistics and improve operational efficiency. The system's adaptability to diverse environments and its potential for significant cost savings position it as a valuable asset for a wide range of industries. As the demand for efficient and flexible material handling solutions continues to grow, the TM Flow System is likely to play an increasingly important role in shaping the future of logistics and manufacturing.
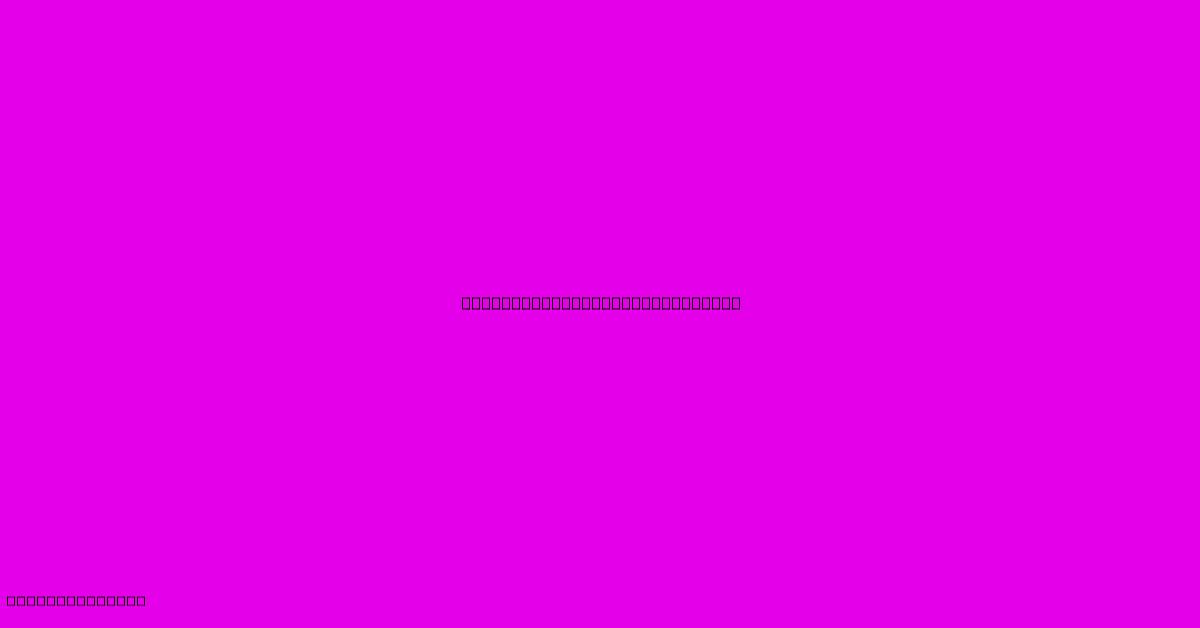
Thank you for visiting our website wich cover about Ld Technology Tm Flow System. We hope the information provided has been useful to you. Feel free to contact us if you have any questions or need further assistance. See you next time and dont miss to bookmark.
Featured Posts
-
Bundesliga Stuttgart Verliert Gegen St Pauli
Dec 22, 2024
-
Atletico Vs Barcelona Alineaciones J18
Dec 22, 2024
-
L3 Harris Technologies Palm Bay Fl
Dec 22, 2024
-
Blake Lively Justin Baldoni Smear Allegations
Dec 22, 2024
-
Los Andes En La B Golazo A Sarmiento
Dec 22, 2024