Laser Cladding Technology
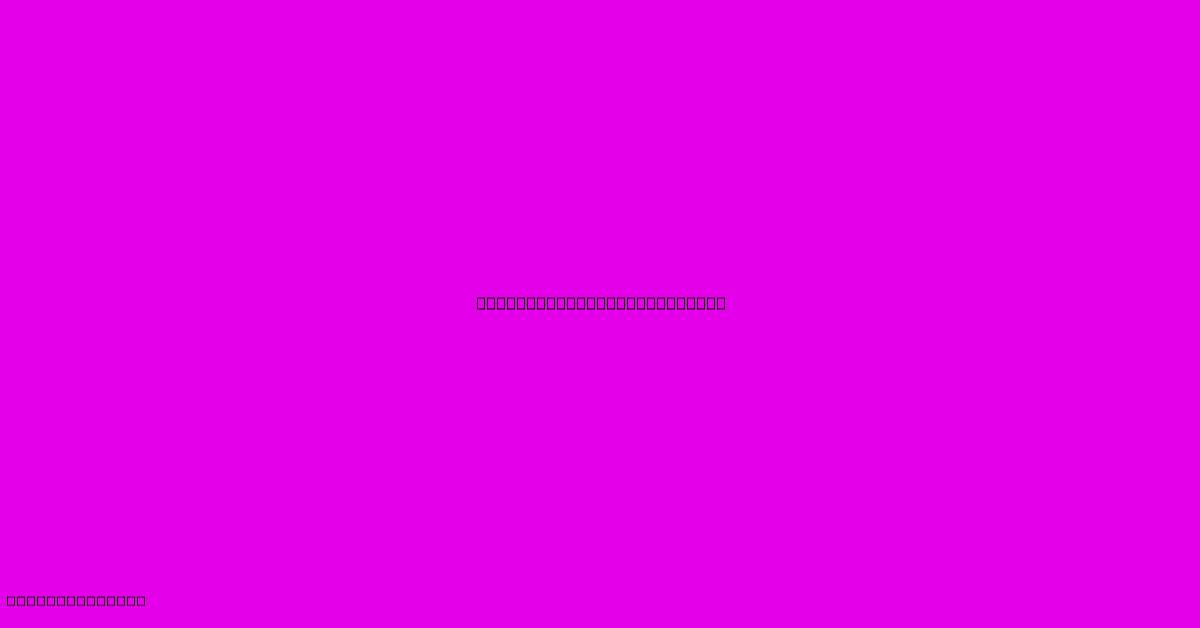
Discover more detailed and exciting information on our website. Click the link below to start your adventure: Visit Best Website mr.cleine.com. Don't miss out!
Table of Contents
Laser Cladding: A Revolutionary Surface Modification Technique
Laser cladding is a powerful additive manufacturing technique used to enhance the surface properties of components. It offers a precise and efficient method to deposit layers of metallic alloys onto a substrate, significantly improving wear resistance, corrosion resistance, and other critical material characteristics. This article delves into the intricacies of laser cladding technology, exploring its applications, advantages, limitations, and future prospects.
Understanding the Process:
Laser cladding leverages a high-powered laser beam to melt a metal powder feedstock, which is then deposited onto a substrate material. This process creates a strong metallurgical bond between the cladding layer and the base material, resulting in a composite structure with improved properties. The laser beam precisely controls the melting and solidification process, enabling the creation of complex geometries and tailored surface features. Different types of lasers are used, with fiber lasers gaining popularity for their efficiency and high power output.
Key Advantages of Laser Cladding:
-
Enhanced Material Properties: Laser cladding dramatically improves the wear, corrosion, and heat resistance of components, extending their lifespan and performance. This is achieved by applying specialized alloys with superior properties to the surface.
-
Precision and Control: The laser beam's precise control allows for the deposition of thin, uniform layers with minimal distortion of the substrate. This is crucial for applications requiring high dimensional accuracy.
-
Reduced Material Waste: Compared to traditional methods like welding or coating, laser cladding minimizes material waste, as the powder is only used where it's needed.
-
Versatility: Laser cladding can be used on a wide range of substrate materials and alloys, offering significant flexibility in applications.
-
High Deposition Rates: Modern laser cladding systems achieve high deposition rates, making the process efficient for mass production or large-scale projects.
-
Complex Geometry Capabilities: The ability to build intricate 3D structures opens doors for customized designs and functional integration.
Applications Across Diverse Industries:
Laser cladding finds widespread applications in various industries:
-
Aerospace: Enhancing the durability and performance of engine components, turbine blades, and other critical parts.
-
Automotive: Improving the wear resistance of engine blocks, cylinder liners, and other high-stress components.
-
Oil and Gas: Enhancing the corrosion resistance of pipelines, valves, and other equipment exposed to harsh environments.
-
Medical: Creating custom implants and prosthetics with enhanced biocompatibility and durability.
-
Tooling: Increasing the lifespan and performance of cutting tools, molds, and dies.
-
Power Generation: Improving the resistance to wear and corrosion in power plant components.
Limitations of Laser Cladding:
Despite its advantages, laser cladding does have some limitations:
-
High Initial Investment: The equipment required for laser cladding can be expensive, making it a significant upfront investment.
-
Process Complexity: Mastering the laser cladding process requires specialized expertise and training.
-
Potential for Porosity: Depending on process parameters, the cladding layer can exhibit porosity, affecting its mechanical properties. Careful control of parameters is essential to minimize this.
-
Residual Stresses: The rapid heating and cooling during the process can induce residual stresses in the cladding layer and substrate, potentially impacting component performance.
Future Trends and Developments:
The field of laser cladding continues to evolve, with ongoing research focusing on:
-
Improved Powder Feedstock: Development of new powder alloys with enhanced properties and improved flow characteristics.
-
Process Optimization: Advanced process control techniques to further improve precision, efficiency, and reduce defects.
-
Hybrid Processes: Combining laser cladding with other additive manufacturing techniques to achieve more complex geometries and functionalities.
-
In-situ Monitoring and Control: Real-time monitoring of the cladding process to ensure consistent quality and optimize parameters.
Conclusion:
Laser cladding technology offers a revolutionary approach to surface modification, providing significant benefits in terms of material properties, precision, and efficiency. As research continues and technology advances, its applications are poised to expand further, making it a crucial technique for enhancing the performance and lifespan of components across a vast range of industries. The future of laser cladding appears bright, promising further innovations and broader adoption.
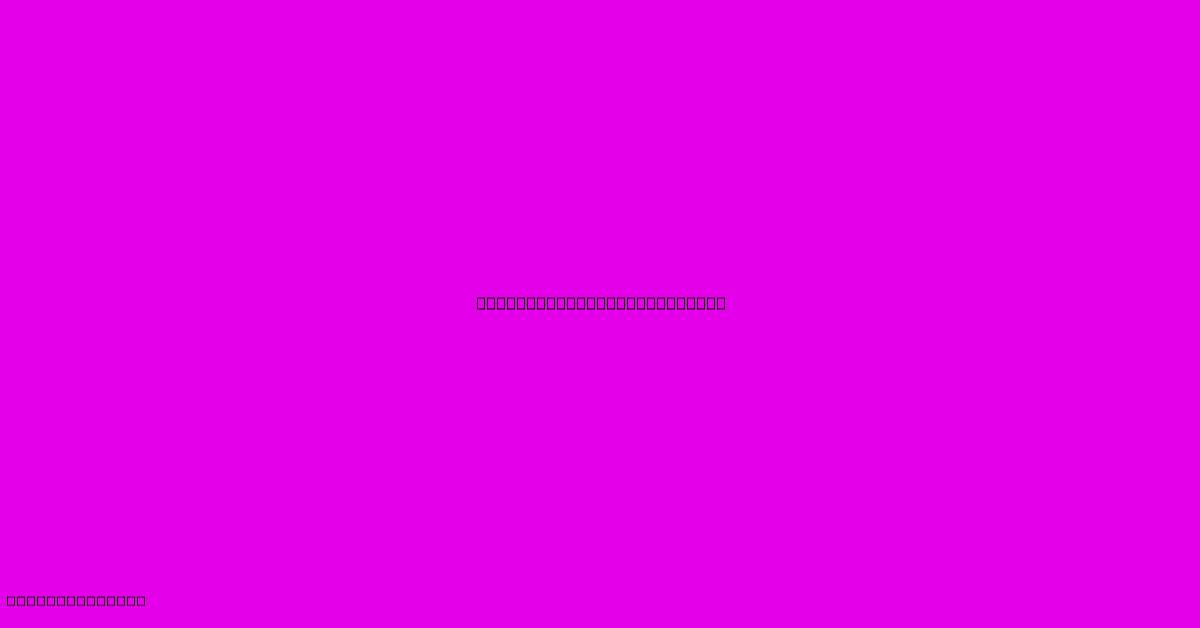
Thank you for visiting our website wich cover about Laser Cladding Technology. We hope the information provided has been useful to you. Feel free to contact us if you have any questions or need further assistance. See you next time and dont miss to bookmark.
Featured Posts
-
Technological Optimists Argue That Technological Advances Have
Jan 04, 2025
-
Carmax Technology Rotation Program
Jan 04, 2025
-
Hagadone Technologies
Jan 04, 2025
-
Ndsu Research And Technology Park
Jan 04, 2025
-
Alvin Sherman Library Research And Information Technology Center
Jan 04, 2025