Kiln Technology
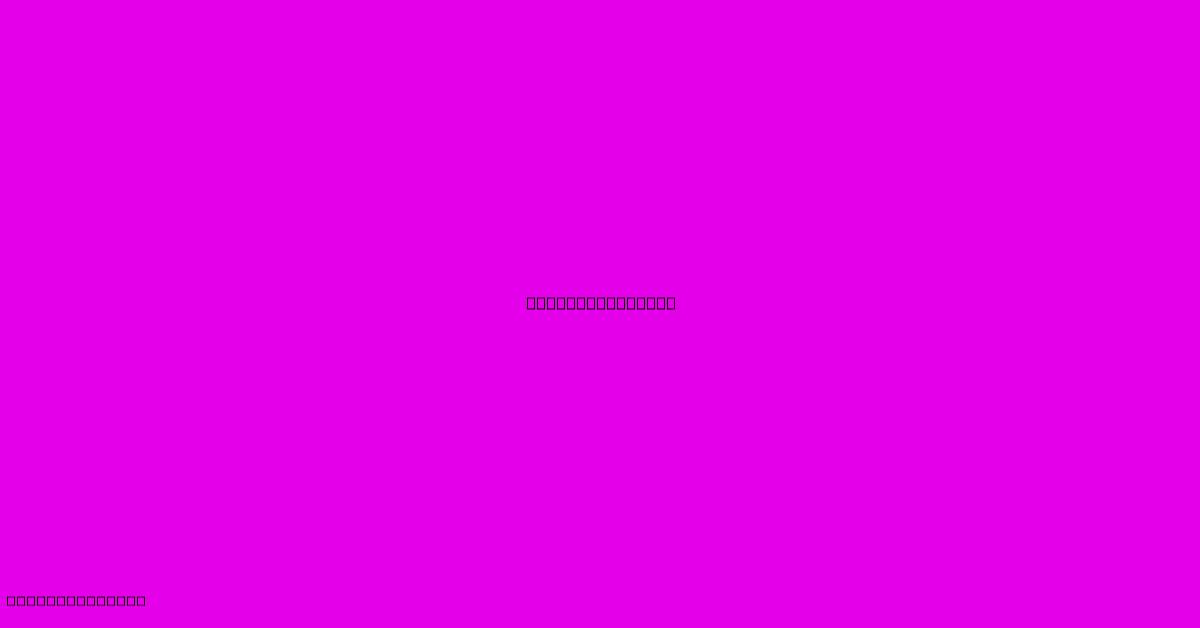
Discover more detailed and exciting information on our website. Click the link below to start your adventure: Visit Best Website mr.cleine.com. Don't miss out!
Table of Contents
Kiln Technology: A Deep Dive into the Heart of High-Temperature Processing
Kiln technology represents a cornerstone of numerous industries, from ceramics and cement production to the manufacturing of advanced materials. Understanding kiln technology involves delving into the intricate processes of heat transfer, material transformation, and efficient energy utilization. This article will explore the various types of kilns, their applications, and the ongoing advancements shaping the future of this crucial technology.
What is a Kiln?
At its core, a kiln is an enclosed chamber designed to subject materials to high temperatures for specific durations. This controlled heating process facilitates chemical and physical transformations, resulting in products with desired properties like strength, durability, and aesthetics. The specific design and operation of a kiln are highly dependent on the intended application and the characteristics of the materials being processed.
Types of Kilns:
Several types of kilns exist, each optimized for particular applications:
-
Shaft Kilns: These are vertical kilns where materials are fed from the top and gradually descend as they are heated. They're often used in cement and lime production due to their continuous operation and high throughput. Keywords: shaft kiln, cement production, lime production, continuous operation, high throughput.
-
Rotary Kilns: These cylindrical kilns rotate slowly, allowing for even heating and mixing of materials. They are widely used in the cement industry, and also find applications in the processing of minerals and chemicals. Keywords: rotary kiln, cement industry, mineral processing, chemical processing, continuous process.
-
Tunnel Kilns: These are long, horizontal kilns with a moving hearth or cars that transport materials through different temperature zones. They provide excellent control over the heating process and are commonly used in the ceramic industry for firing bricks, tiles, and other ceramic products. Keywords: tunnel kiln, ceramic industry, brick firing, tile firing, ceramic processing, controlled heating.
-
Intermittent Kilns: These kilns are loaded with materials, fired, and then cooled before unloading. They offer greater flexibility in the types of materials processed but have lower throughput than continuous kilns. Examples include periodic kilns and various types of electric kilns used for pottery and artistic ceramics. Keywords: intermittent kiln, periodic kiln, electric kiln, pottery, artistic ceramics, batch processing.
-
Fluidized Bed Kilns: These kilns use a stream of air to suspend the material, promoting even heating and efficient heat transfer. They find use in the processing of various materials, including catalysts and powders. Keywords: fluidized bed kiln, catalyst processing, powder processing, even heating, efficient heat transfer.
Key Considerations in Kiln Design and Operation:
Several critical factors influence the design and operation of kilns:
-
Fuel Type: Kilns can be fueled by various sources, including natural gas, coal, oil, or electricity. The choice of fuel impacts operating costs, environmental impact, and the level of control over the heating process. Keywords: fuel type, natural gas, coal, oil, electricity, operating costs, environmental impact.
-
Heat Transfer: Efficient heat transfer is crucial for optimal energy utilization and consistent product quality. Different kiln designs employ various strategies to optimize heat transfer, including radiation, convection, and conduction. Keywords: heat transfer, radiation, convection, conduction, energy efficiency, product quality.
-
Temperature Control: Precise temperature control is essential for achieving desired material properties. Modern kilns utilize sophisticated control systems to maintain consistent temperatures throughout the firing process. Keywords: temperature control, control systems, precise temperature, material properties.
-
Emissions Control: Environmental regulations necessitate the control of emissions from kilns. Advanced technologies, such as scrubbers and filters, are employed to minimize the release of harmful pollutants. Keywords: emissions control, scrubbers, filters, environmental regulations, pollution control.
Advancements in Kiln Technology:
Ongoing advancements are focused on increasing energy efficiency, improving process control, and reducing environmental impact:
- Advanced Control Systems: The integration of advanced sensors and control systems allows for real-time monitoring and optimization of the firing process.
- Improved Insulation: The use of high-performance insulation materials reduces energy consumption and improves temperature control.
- Waste Heat Recovery: Strategies for recovering and reusing waste heat from the kiln process significantly improve energy efficiency.
- Alternative Fuels: The exploration and implementation of alternative and sustainable fuel sources are reducing the environmental footprint of kiln operations.
Conclusion:
Kiln technology plays a vital role across numerous industries. Understanding the different types of kilns, the principles of their operation, and the latest advancements in this field is crucial for optimizing production processes, improving product quality, and minimizing environmental impact. The ongoing development and refinement of kiln technology will continue to drive innovation and efficiency in various sectors for years to come.
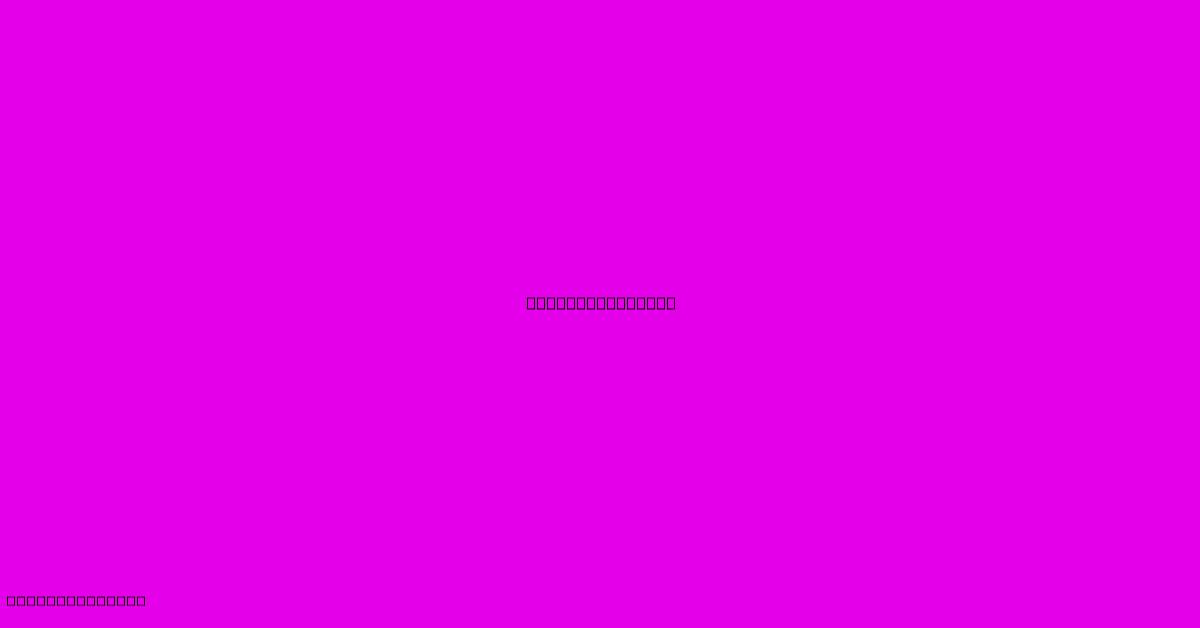
Thank you for visiting our website wich cover about Kiln Technology. We hope the information provided has been useful to you. Feel free to contact us if you have any questions or need further assistance. See you next time and dont miss to bookmark.
Featured Posts
-
Donovan Mitchell Cavs Vs Bucks
Dec 21, 2024
-
Dri Avg Technologies Refund
Dec 21, 2024
-
Auckland Christmas Grinch Mystery
Dec 21, 2024
-
Food Science And Technology Jobs
Dec 21, 2024
-
Australia Usyk Fury 2 Fight Start Time
Dec 21, 2024