Jewell Tool Technology
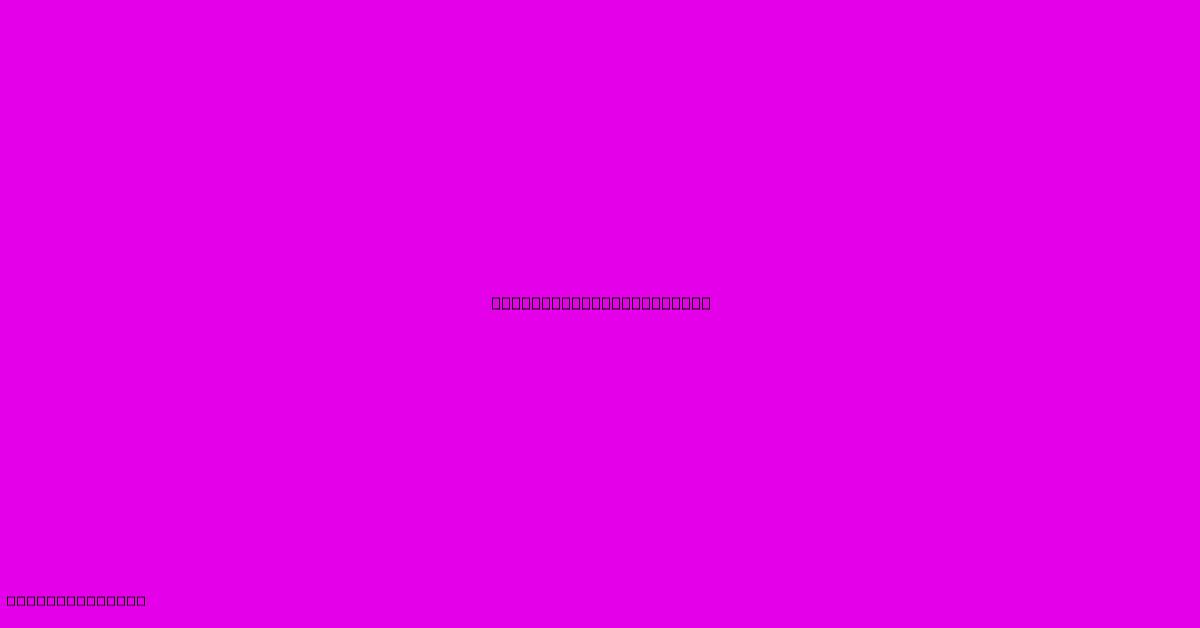
Discover more detailed and exciting information on our website. Click the link below to start your adventure: Visit Best Website mr.cleine.com. Don't miss out!
Table of Contents
Jewell Tool Technology: Precision and Innovation in Tooling Solutions
Jewell Tool Technology isn't just a name; it represents a commitment to precision, innovation, and providing high-quality tooling solutions for a wide range of industries. This article delves into the world of Jewell Tool Technology, exploring its capabilities, the industries it serves, and its impact on modern manufacturing.
What is Jewell Tool Technology?
Jewell Tool Technology, while not a publicly known, large-scale company name like some others, represents a broader concept – the application of advanced technologies and precision engineering to create superior tooling. This includes the design, manufacturing, and maintenance of tools used across various manufacturing processes. It's a field constantly evolving, driven by advancements in materials science, computer-aided design (CAD), and computer-aided manufacturing (CAM).
Key Aspects of Jewell Tool Technology:
-
Precision Engineering: The cornerstone of Jewell Tool Technology is precision. Tools are crafted with exacting tolerances to ensure accuracy, consistency, and optimal performance in manufacturing processes. This minimizes waste, improves product quality, and enhances overall efficiency.
-
Material Selection: The choice of materials is critical. Jewell Tool Technology utilizes a diverse range of materials, selected based on the specific application and required properties. This might include high-speed steels, carbide, ceramics, or even advanced composites, each chosen for its unique strengths – hardness, wear resistance, heat tolerance, etc.
-
Advanced Manufacturing Processes: Jewell Tool Technology often involves sophisticated manufacturing techniques such as wire EDM (electrical discharge machining), grinding, and polishing. These processes allow for the creation of intricate tool geometries and extremely fine surface finishes, essential for producing high-quality parts.
-
Computer-Aided Design and Manufacturing (CAD/CAM): Jewell Tool Technology relies heavily on CAD/CAM software. These tools enable the design and simulation of tools before physical production, allowing for optimization and error correction in the design phase. This significantly reduces lead times and costs associated with tooling.
-
Quality Control and Inspection: Rigorous quality control measures are crucial. This includes regular inspections throughout the manufacturing process, employing advanced measurement techniques to ensure that tools meet the specified tolerances and performance standards.
Industries Served by Jewell Tool Technology:
Jewell Tool Technology finds application in a wide range of industries, including:
- Automotive: Tools for stamping, machining, and assembly of automotive parts.
- Aerospace: Precision tooling for the manufacture of aircraft components, requiring exceptional accuracy and durability.
- Medical Device Manufacturing: Tools for creating intricate and highly precise medical devices, demanding the highest levels of quality and sterility.
- Electronics: Tools for the production of electronic components, often requiring miniature tooling and extremely tight tolerances.
- Energy: Tools used in the oil and gas, and renewable energy sectors.
The Future of Jewell Tool Technology:
The future of Jewell Tool Technology will likely be shaped by continued advancements in:
- Additive Manufacturing (3D Printing): 3D printing offers the potential to create complex tool geometries that would be difficult or impossible to produce using traditional methods.
- Artificial Intelligence (AI) and Machine Learning: AI and machine learning can be used to optimize tool designs, predict tool wear, and improve manufacturing processes.
- Smart Tools and Sensors: Incorporating sensors into tools allows for real-time monitoring of performance, enabling predictive maintenance and reducing downtime.
Conclusion:
Jewell Tool Technology is a vital component of modern manufacturing. By combining precision engineering, advanced materials, and sophisticated manufacturing processes, it enables the creation of high-quality products across diverse industries. The continued evolution of this field promises even more efficient, precise, and sustainable manufacturing solutions in the years to come. The future of precision lies in the continued advancements within Jewell Tool Technology, however it's ultimately defined within the specifics of each manufacturer and their unique needs.
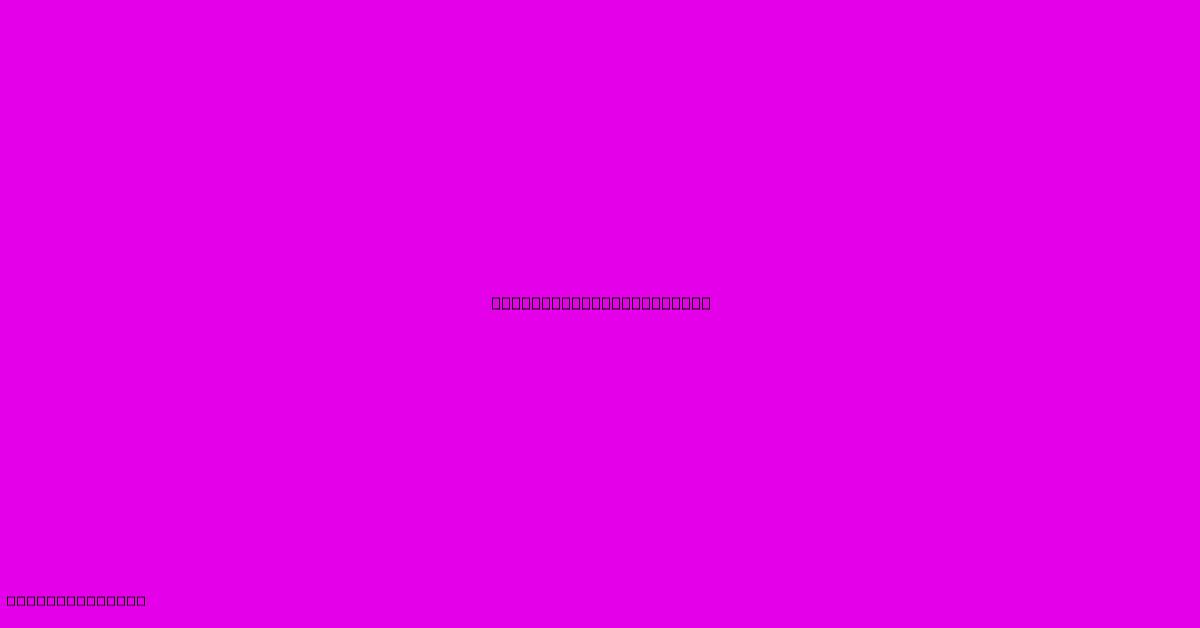
Thank you for visiting our website wich cover about Jewell Tool Technology. We hope the information provided has been useful to you. Feel free to contact us if you have any questions or need further assistance. See you next time and dont miss to bookmark.
Featured Posts
-
Dayle Haddon Model Dies In Co Leak
Dec 28, 2024
-
Viaplay Storing Ziggo Verantwoordelijk
Dec 28, 2024
-
Moran Technology Consulting
Dec 28, 2024
-
R And P Technologies
Dec 28, 2024
-
Legalon Technologies
Dec 28, 2024