Iron And Steel Technology Roadmap
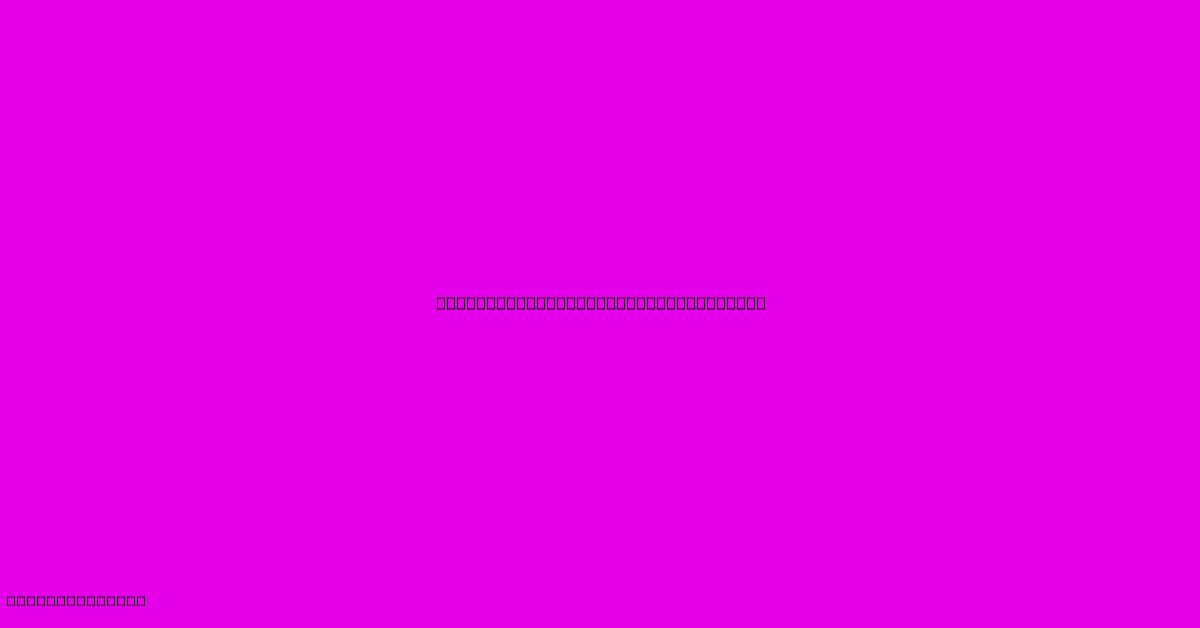
Discover more detailed and exciting information on our website. Click the link below to start your adventure: Visit Best Website mr.cleine.com. Don't miss out!
Table of Contents
Iron and Steel Technology Roadmap: Forging a Sustainable Future
The iron and steel industry, a cornerstone of global infrastructure and manufacturing, faces a critical juncture. Meeting the ever-increasing demand while drastically reducing its environmental footprint requires a radical transformation driven by technological innovation. This article outlines a key technology roadmap for the iron and steel sector, focusing on decarbonization, efficiency, and resource optimization.
1. Decarbonizing Steel Production: The Urgent Need
The industry's reliance on coal-based blast furnaces contributes significantly to global greenhouse gas emissions. Transitioning to a low-carbon future necessitates a multi-pronged approach:
<h3>1.1 Hydrogen-Based Direct Reduction:**
- The core: Replacing coke with hydrogen as the reducing agent in direct reduction processes. This drastically minimizes CO2 emissions.
- Challenges: Requires cost-effective, large-scale green hydrogen production (e.g., electrolysis powered by renewable energy). Infrastructure development and hydrogen storage are crucial.
- Opportunities: Potential for near-zero CO2 emissions steel production.
<h3>1.2 Carbon Capture, Utilization, and Storage (CCUS):**
- The core: Capturing CO2 emissions from existing blast furnaces and steelmaking processes, either utilizing it in other industries (e.g., enhanced oil recovery) or storing it underground.
- Challenges: High capital and operating costs. Requires extensive infrastructure and regulatory frameworks. Long-term storage security is essential.
- Opportunities: A bridge technology enabling continued use of existing infrastructure while significantly reducing emissions.
<h3>1.3 Electric Arc Furnaces (EAFs):**
- The core: Utilizing electricity to melt scrap steel, significantly reducing reliance on iron ore and coke.
- Challenges: Requires a robust and readily available supply of scrap metal. Electricity consumption needs to be sourced from renewable energy sources.
- Opportunities: Already a more sustainable process compared to blast furnaces. Can be easily integrated into a circular economy model.
2. Enhancing Efficiency and Resource Optimization:
Beyond decarbonization, improving efficiency and optimizing resource use is paramount:
<h3>2.1 Advanced Process Control and Automation:**
- The core: Implementing artificial intelligence (AI), machine learning (ML), and advanced sensors to optimize process parameters in real-time, minimizing energy consumption and material waste.
- Challenges: Requires significant investment in digital infrastructure and skilled workforce training. Data security and integration are crucial.
- Opportunities: Significant improvements in productivity, quality control, and energy efficiency.
<h3>2.2 Smart Manufacturing and Industry 4.0:**
- The core: Integrating digital technologies across the entire value chain – from raw material sourcing to product delivery – to improve traceability, optimize logistics, and reduce waste.
- Challenges: Requires collaboration across the industry and integration with existing legacy systems. Data interoperability and standardization are key.
- Opportunities: Enhanced efficiency, transparency, and supply chain resilience.
<h3>2.3 Closed-Loop Recycling and Circular Economy:**
- The core: Implementing strategies to maximize the reuse and recycling of steel scrap, minimizing the need for virgin materials.
- Challenges: Requires improvements in scrap sorting and processing technologies. Developing standards and infrastructure for end-of-life steel management.
- Opportunities: Significant reduction in resource consumption and waste generation. Creation of a sustainable and resilient steel industry.
3. Future Outlook and Collaboration:
The successful implementation of this technology roadmap requires a collaborative effort between industry stakeholders, governments, and research institutions. This includes:
- Investing in R&D: Continued development and deployment of innovative technologies, especially in green hydrogen production and CCUS.
- Policy Support: Incentivizing the adoption of sustainable steelmaking technologies through carbon pricing, tax credits, and other policy mechanisms.
- Industry Collaboration: Sharing best practices and fostering open innovation to accelerate technological progress.
- Workforce Development: Training and upskilling the workforce to adapt to the changing landscape of the steel industry.
The future of the iron and steel industry hinges on its ability to embrace these technological advancements. By focusing on decarbonization, efficiency, and resource optimization, the industry can forge a sustainable path towards a low-carbon future, ensuring its continued relevance and contribution to global prosperity.
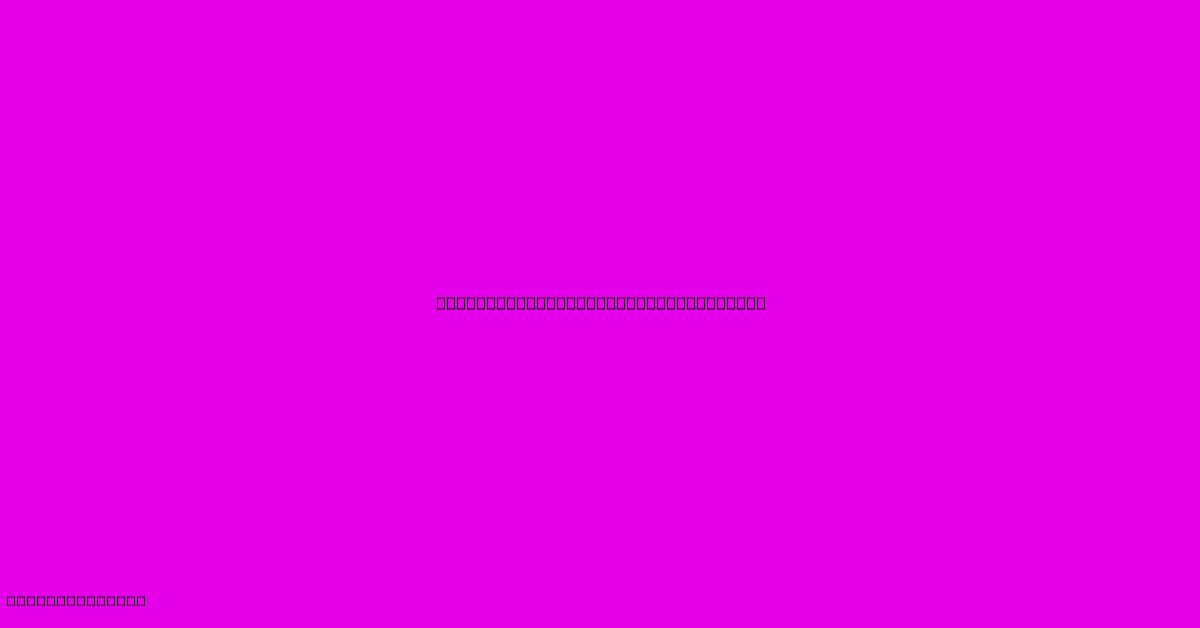
Thank you for visiting our website wich cover about Iron And Steel Technology Roadmap. We hope the information provided has been useful to you. Feel free to contact us if you have any questions or need further assistance. See you next time and dont miss to bookmark.
Featured Posts
-
Bouterse 79 Einde Presidentschap Bevestigd
Dec 26, 2024
-
Azerbaijan Airlines Crash Kills 38 In Kazakhstan
Dec 26, 2024
-
Queda De Aviao Embraer 67 Vitimas No Cazaquistao
Dec 26, 2024
-
Museum Of Art And Technology New York
Dec 26, 2024
-
Cranial Technologies Jupiter
Dec 26, 2024