Injection Technologies
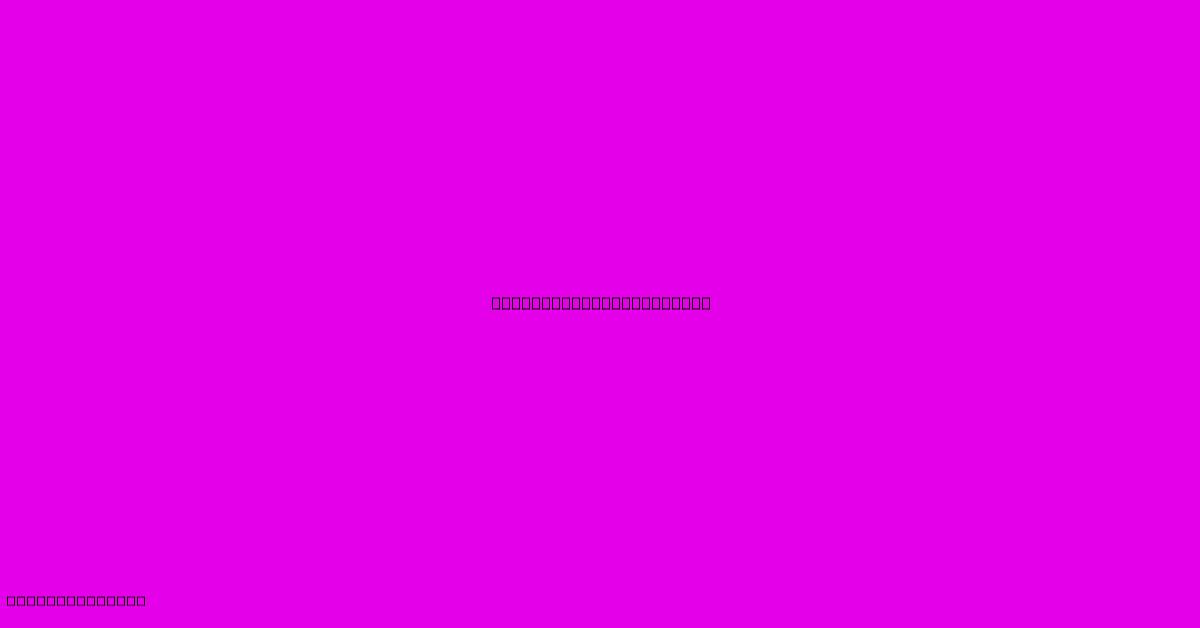
Discover more detailed and exciting information on our website. Click the link below to start your adventure: Visit Best Website mr.cleine.com. Don't miss out!
Table of Contents
Injection Technologies: A Deep Dive into Modern Manufacturing and Medical Processes
Injection technologies are ubiquitous, impacting numerous sectors from manufacturing to medicine. This article explores the diverse applications and underlying principles of injection technologies, delving into their advantages, limitations, and future trends.
What are Injection Technologies?
At its core, injection technology involves forcing a fluid—be it molten plastic, liquid metal, or a pharmaceutical solution—under pressure into a mold or cavity. This process creates precise shapes and forms, offering high levels of control and repeatability. The pressure applied, combined with the material's properties and the mold's design, determines the final product's characteristics.
Types of Injection Technologies:
Several distinct types of injection technologies exist, each tailored to specific applications:
1. Injection Molding: This is arguably the most prevalent type, primarily used in the manufacturing industry. It involves injecting molten thermoplastic polymers into a precisely engineered mold to create parts with intricate details. Applications span from everyday consumer goods like plastic bottles and toys to complex automotive components and medical devices.
- Advantages: High production rates, precise dimensional accuracy, repeatable results, and ability to create complex shapes.
- Limitations: Requires significant upfront investment in molds, limited to thermoplastic materials, and potential for material degradation at high temperatures.
2. Metal Injection Molding (MIM): This process uses powdered metal mixed with a binder, injected into a mold, and then sintered (heated to bond the particles) to create dense, intricate metal parts. MIM is ideal for producing small, complex components with high precision.
- Advantages: Net-shape manufacturing, complex geometries, high precision, and suitability for various metal alloys.
- Limitations: Higher cost compared to other methods, limited to smaller parts, and potential for shrinkage during sintering.
3. Injection Pressure Casting: This technique utilizes molten metal, often aluminum or zinc, injected under high pressure into a die-cast mold. It produces high-quality metal parts with intricate details and superior surface finishes.
- Advantages: High production rates, excellent dimensional accuracy, and smooth surface finish.
- Limitations: High setup costs, limited to specific metals, and potential for porosity in the finished part.
4. Drug Delivery Systems (Injection): In the medical field, injection technologies play a crucial role in drug delivery. This includes various injection methods such as intravenous (IV), intramuscular (IM), subcutaneous (SC), and intradermal (ID) injections, each designed for specific drug characteristics and therapeutic needs.
- Advantages: Precise drug delivery, rapid onset of action, and suitability for a wide range of drugs.
- Limitations: Requires trained personnel for administration, potential for discomfort or adverse reactions, and challenges in maintaining sterility.
Future Trends in Injection Technologies:
The field of injection technology continues to evolve, driven by the demand for faster, more efficient, and more sustainable manufacturing and medical processes. Key trends include:
- Automation and Robotics: Increased automation and robotics are improving efficiency and reducing labor costs.
- Additive Manufacturing Integration: Combining injection molding with additive manufacturing processes to create hybrid parts with unique properties.
- Sustainable Materials: Greater adoption of bio-based and recycled materials to minimize environmental impact.
- Smart Injection Molding: Utilizing sensors and data analytics to optimize injection parameters and improve product quality.
Conclusion:
Injection technologies are essential to countless industries, offering a diverse range of capabilities for creating precise, high-quality products. As technology advances, we can expect even greater precision, efficiency, and sustainability from injection processes, leading to innovations across various sectors. Understanding the principles and applications of injection technology is crucial for anyone involved in design, manufacturing, or the medical field.
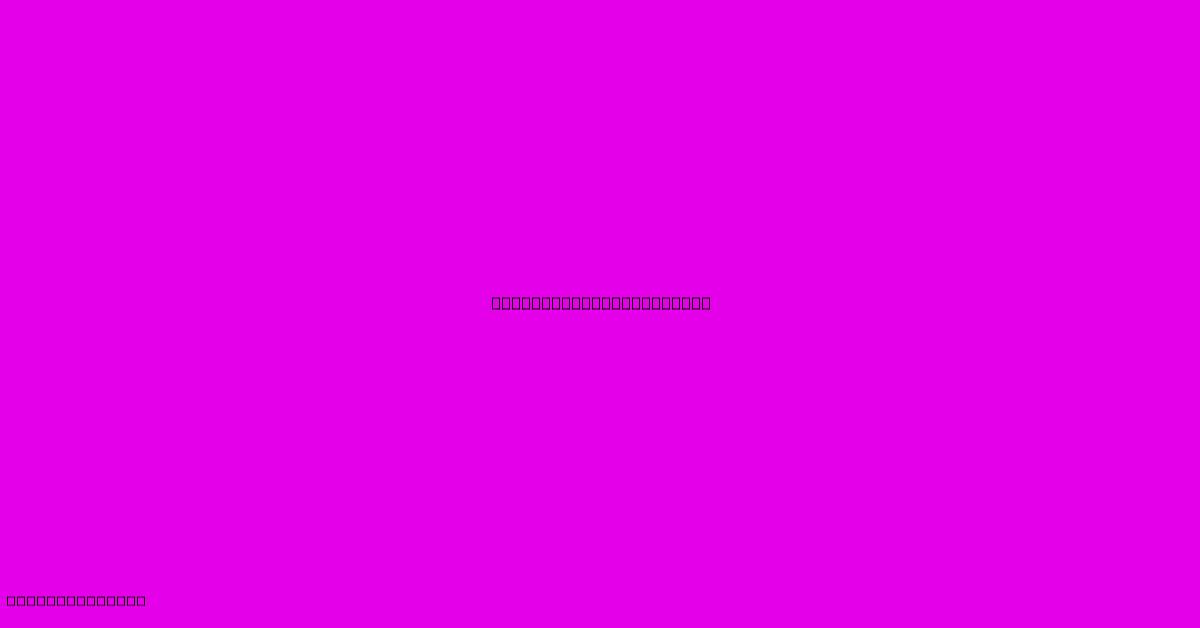
Thank you for visiting our website wich cover about Injection Technologies. We hope the information provided has been useful to you. Feel free to contact us if you have any questions or need further assistance. See you next time and dont miss to bookmark.
Featured Posts
-
41 Saludos Navidad Whats App
Dec 25, 2024
-
Donde Esta Papa Noel Seguimiento En Vivo
Dec 25, 2024
-
Eiffel Tower Evac Christmas Malfunction
Dec 25, 2024
-
Technology Webinars
Dec 25, 2024
-
Trauer Um Sophie Hediger Toedliche Lawine In Den Alpen
Dec 25, 2024