Injection Molding Technology
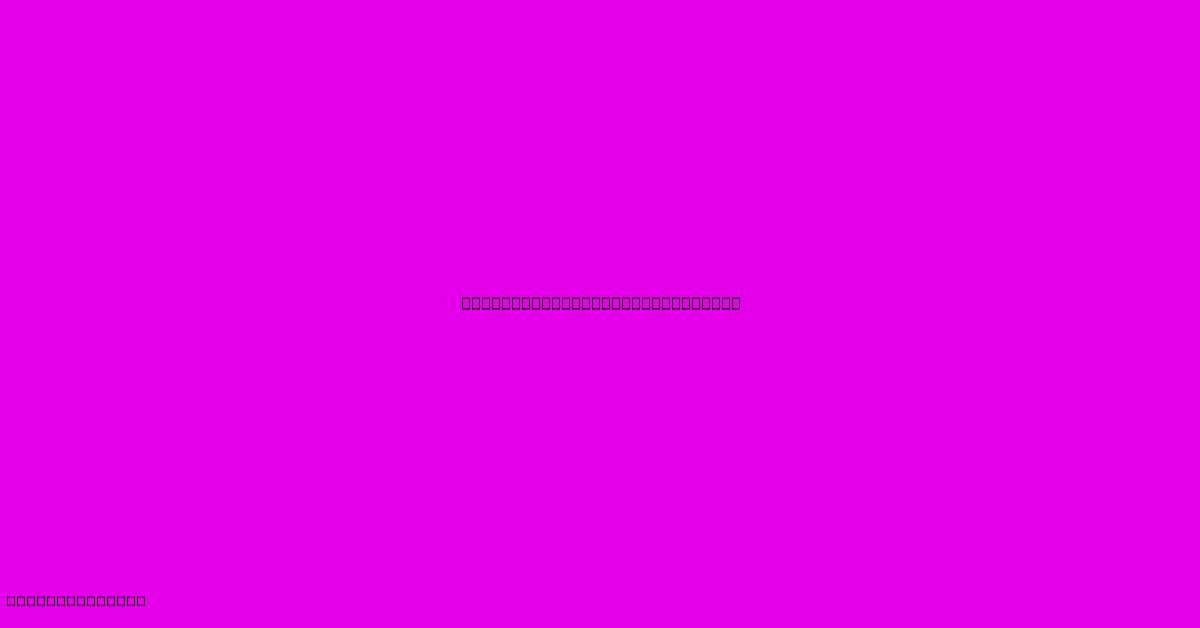
Discover more detailed and exciting information on our website. Click the link below to start your adventure: Visit Best Website mr.cleine.com. Don't miss out!
Table of Contents
Injection Molding Technology: A Comprehensive Guide
Injection molding is a high-volume manufacturing process used to create parts from various materials. It's a cornerstone of modern manufacturing, responsible for producing countless everyday items, from plastic bottle caps to complex automotive components. This comprehensive guide will delve into the technology, its benefits, limitations, and future trends.
What is Injection Molding?
Injection molding involves injecting molten material—typically thermoplastic polymers, but also thermosets, elastomers, and even metals—into a precisely engineered mold cavity. The mold is held under pressure until the material cools and solidifies, taking the shape of the cavity. Once solidified, the mold opens, and the finished part is ejected. This process is highly automated, leading to high production speeds and consistent part quality.
The Injection Molding Process: A Step-by-Step Breakdown
-
Clamping: The mold halves are clamped together tightly to ensure a leak-proof seal during the injection process.
-
Injection: Molten material is injected into the mold cavity under high pressure. The pressure forces the material into every detail of the mold, creating precise parts.
-
Holding: The molten material is held under pressure in the mold cavity while it cools and solidifies. This ensures complete filling of the mold and prevents warping or shrinkage.
-
Cooling: The mold is designed with cooling channels to rapidly cool the injected material. This stage is crucial for maintaining dimensional accuracy and part quality.
-
Ejection: Once the material has solidified, the mold opens, and the finished part is ejected using ejector pins.
-
Part Removal and Finishing: The ejected parts may require further finishing steps such as trimming, deburring, or surface treatment depending on the application.
Types of Injection Molding
Several variations exist, catering to different material types and part complexities:
-
Thermoplastic Injection Molding: The most common type, using materials that melt and solidify repeatedly. Examples include polyethylene (PE), polypropylene (PP), and polyvinyl chloride (PVC).
-
Thermoset Injection Molding: Uses materials that undergo an irreversible chemical change during the molding process, resulting in a permanently hardened part. These materials are typically stronger and more heat-resistant than thermoplastics.
-
Reaction Injection Molding (RIM): Combines two or more reactive components inside the mold, which react and solidify to form a part. This is often used for larger parts with complex geometries.
-
Gas-Assisted Injection Molding: Introduces gas into the molten material, creating hollow parts and reducing weight.
-
Overmolding: Involves molding one material onto another, often used to combine different materials with specific properties.
Advantages of Injection Molding
- High Production Rates: Produces a large number of identical parts quickly and efficiently.
- High Precision and Accuracy: Creates highly precise parts with complex geometries.
- Automation Capabilities: Highly automated, reducing labor costs and improving consistency.
- Material Versatility: Can be used with a wide range of materials.
- Cost-Effective for High Volumes: The per-unit cost decreases significantly as production volume increases.
Limitations of Injection Molding
- High Initial Investment: Requires significant upfront investment in molds and machinery.
- Limited Design Flexibility: Some designs might be unsuitable for injection molding.
- Material Restrictions: Certain materials may be difficult or impossible to mold.
- Potential for Defects: Improper molding parameters can lead to defects such as sink marks, warping, or short shots.
Future Trends in Injection Molding
- Advanced Materials: The use of bioplastics, high-performance polymers, and composites is expanding.
- Smart Manufacturing: Integration of IoT and data analytics for improved process control and predictive maintenance.
- Additive Manufacturing Integration: Combining injection molding with 3D printing to create hybrid parts with unique functionalities.
- Automation and Robotics: Further automation of the injection molding process through the use of robotics and AI.
Conclusion
Injection molding remains a crucial manufacturing process, offering high-volume production of precise and consistent parts. Understanding its capabilities and limitations is essential for selecting the right manufacturing process for a given application. As technology advances, injection molding will continue to evolve, offering even greater precision, efficiency, and material versatility.
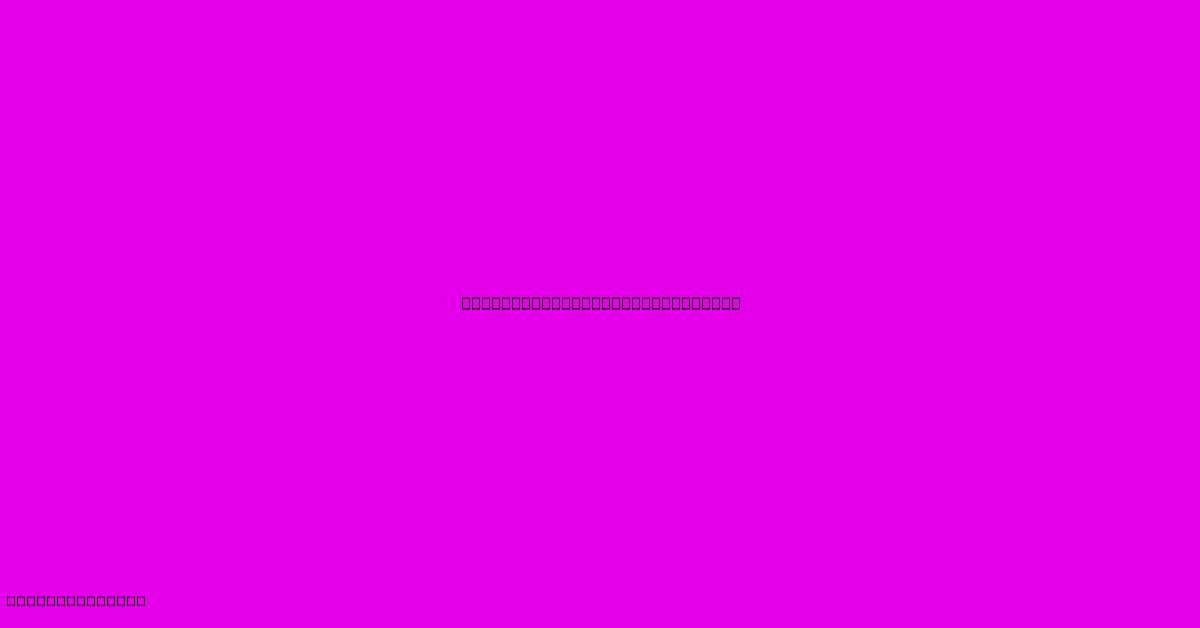
Thank you for visiting our website wich cover about Injection Molding Technology. We hope the information provided has been useful to you. Feel free to contact us if you have any questions or need further assistance. See you next time and dont miss to bookmark.
Featured Posts
-
Luminar Technologies Stock Forecast
Jan 01, 2025
-
Omega Global Technologies Inc
Jan 01, 2025
-
Lake Effect Snow Northwest Pa Alert
Jan 01, 2025
-
College Football Playoff Bracket
Jan 01, 2025
-
New Years Cleaning Fact Or Fiction
Jan 01, 2025