Inert Gas Technology
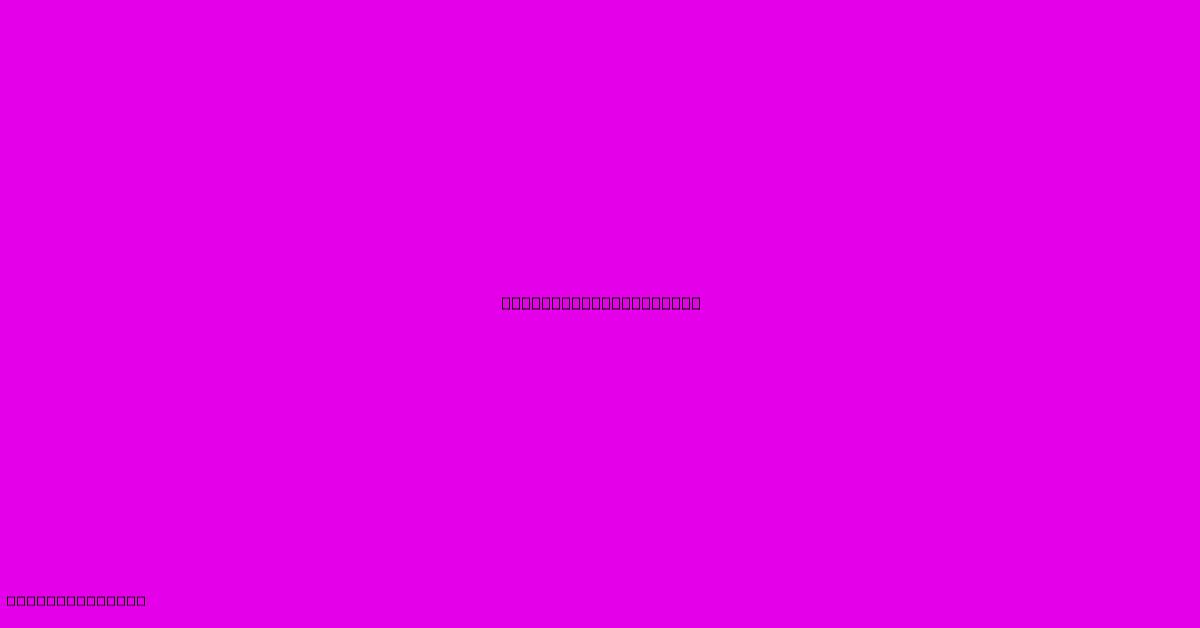
Discover more detailed and exciting information on our website. Click the link below to start your adventure: Visit Best Website mr.cleine.com. Don't miss out!
Table of Contents
Inert Gas Technology: Protecting Your Processes with Inert Atmospheres
Inert gas technology plays a crucial role in various industries, safeguarding processes and products from the harmful effects of oxygen and moisture. This article explores the principles, applications, and benefits of this essential technology.
What is Inert Gas Technology?
Inert gas technology involves the use of gases that are chemically unreactive, preventing oxidation, combustion, and other undesirable chemical reactions. These gases displace oxygen and moisture from a specific environment, creating an inert atmosphere. The most commonly used inert gases are nitrogen, argon, helium, and carbon dioxide, each with its unique properties and applications.
How Does it Work?
The process typically involves purging the desired environment with an inert gas. This carefully controlled displacement removes air and replaces it with the inert gas, effectively creating a low-oxygen, low-moisture environment. The specific method and equipment used depend on the application and the required level of inertness. Techniques include blanketing, purging, and pressure displacement.
Key Applications of Inert Gas Technology:
The applications of inert gas technology are widespread and diverse:
1. Food and Beverage Industry:
- Packaging: Inert gases like nitrogen are used to extend the shelf life of food products by preventing oxidation and microbial growth. This reduces spoilage and maintains product quality.
- Winemaking: Argon is used to protect wine from oxidation during bottling and storage, preserving its flavor and aroma.
2. Chemical Processing:
- Reaction Control: Inert atmospheres prevent unwanted reactions during chemical processing, ensuring product purity and safety.
- Storage of Reactive Materials: Inert gases protect highly reactive chemicals from air exposure, preventing hazardous reactions.
3. Pharmaceutical Industry:
- Drug Manufacturing: Inert gases maintain product quality and prevent oxidation or degradation of sensitive pharmaceuticals.
- Sterile Environments: Inert gas purging helps create and maintain sterile environments during pharmaceutical production.
4. Metalworking:
- Welding: Inert gases, especially argon and helium, shield the weld pool from atmospheric contamination, ensuring high-quality welds. This process is known as Gas Metal Arc Welding (GMAW) or Gas Tungsten Arc Welding (GTAW).
- Heat Treating: Inert atmospheres prevent oxidation and scaling during heat treatment processes.
5. Oil and Gas Industry:
- Pipeline Protection: Inert gases prevent explosions and fires in pipelines by displacing flammable gases.
- Storage Tanks: Inert atmospheres safeguard the contents of storage tanks from oxidation and other harmful reactions.
Benefits of Using Inert Gas Technology:
- Enhanced Product Quality: Protection from oxidation and moisture significantly improves product quality, extending shelf life and enhancing performance.
- Increased Safety: Preventing fires and explosions in hazardous environments is paramount. Inert gases mitigate risks associated with flammable or reactive materials.
- Reduced Waste: Minimizing spoilage and unwanted reactions reduces waste and improves process efficiency.
- Cost Savings: While there's an initial investment in equipment, the long-term cost savings from reduced waste and improved product quality can be significant.
Choosing the Right Inert Gas:
The selection of the most suitable inert gas depends on the specific application and its requirements. Factors to consider include:
- Purity: The required purity level of the inert gas depends on the sensitivity of the process.
- Cost: The cost of the gas varies depending on its type and availability.
- Properties: The physical and chemical properties of each gas influence its suitability for different applications.
Conclusion:
Inert gas technology is a versatile and essential tool across numerous industries. Its ability to create controlled environments protects products and processes, ensuring safety, quality, and efficiency. As industries continue to demand higher standards and greater precision, the role of inert gas technology will only continue to grow in importance.
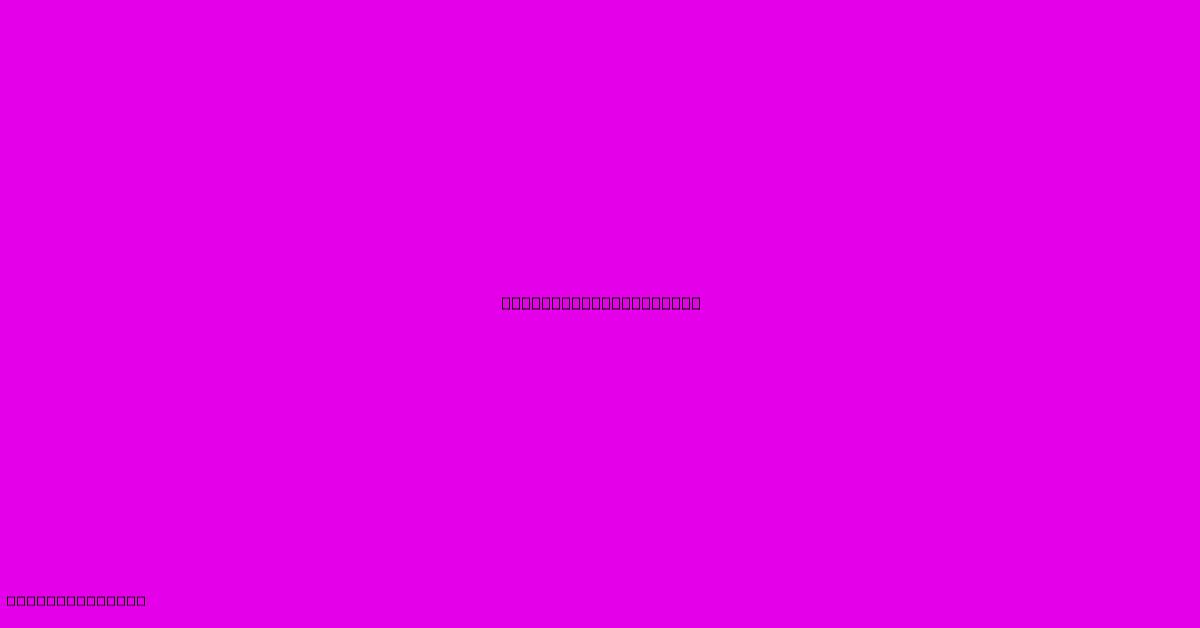
Thank you for visiting our website wich cover about Inert Gas Technology. We hope the information provided has been useful to you. Feel free to contact us if you have any questions or need further assistance. See you next time and dont miss to bookmark.
Featured Posts
-
Advisor Technology
Jan 02, 2025
-
Sic Technologies
Jan 02, 2025
-
Avani Technologies
Jan 02, 2025
-
World Wide Technology Raceway Tickets
Jan 02, 2025
-
Indigenous Technology
Jan 02, 2025