Hot Runner Technology
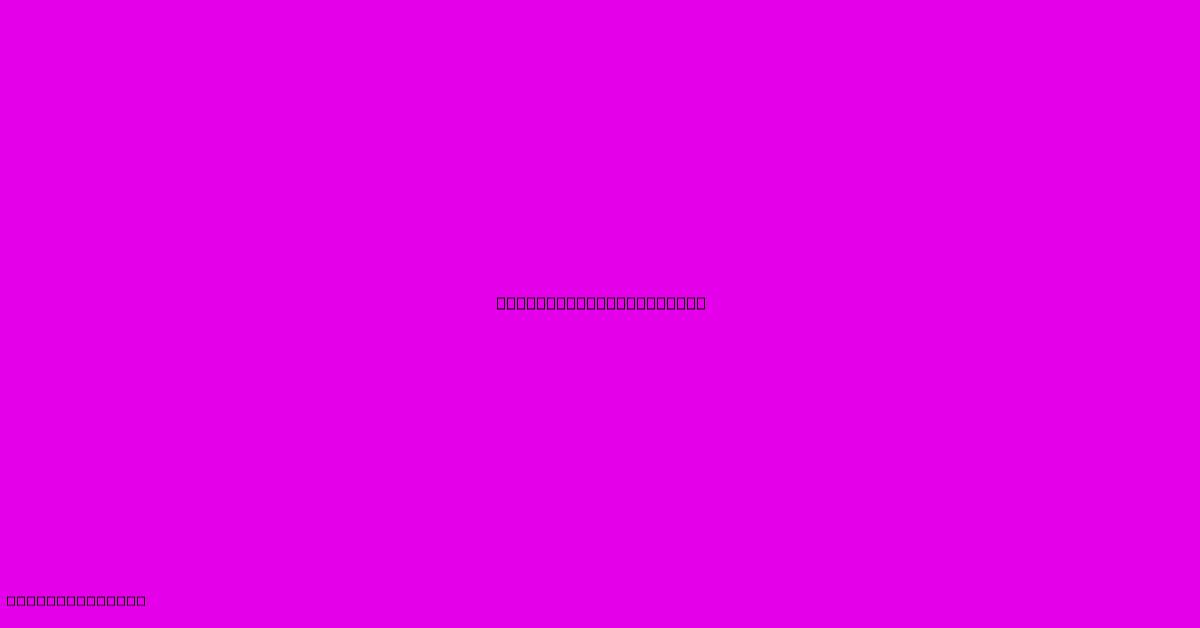
Discover more detailed and exciting information on our website. Click the link below to start your adventure: Visit Best Website mr.cleine.com. Don't miss out!
Table of Contents
Hot Runner Technology: Revolutionizing Plastics Manufacturing
Hot runner technology represents a significant advancement in injection molding, offering substantial benefits in terms of efficiency, material savings, and product quality. This article delves into the intricacies of hot runner systems, exploring their functionality, advantages, and applications across diverse industries.
What is Hot Runner Technology?
Traditional injection molding utilizes a cold runner system where molten plastic flows through a sprue and runners that solidify during the molding cycle. These solidified runners, often referred to as "runners," are then separated from the molded parts, resulting in material waste and additional processing steps. Hot runner systems, conversely, keep the plastic molten within the runner system throughout the entire molding process. This is achieved using electrically heated nozzles or manifolds, eliminating the need for runners and significantly reducing material waste.
How Does it Work?
A hot runner system comprises several key components:
- Manifold: This distributes molten plastic to individual nozzles. The design of the manifold is crucial for uniform plastic flow and temperature control.
- Nozzles: These precisely control the flow of molten plastic into the mold cavities. They are typically equipped with shutoff mechanisms to prevent dripping and ensure clean parting lines.
- Heaters: Electric heaters precisely maintain the temperature of the manifold and nozzles, ensuring the plastic remains molten. Advanced systems incorporate temperature sensors and controllers for precise regulation.
- Insulation: High-quality insulation minimizes heat loss, enhancing efficiency and consistency.
- Control System: A sophisticated control system manages the temperature, pressure, and flow of the molten plastic, optimizing the molding process.
Advantages of Hot Runner Technology:
- Reduced Material Waste: The most significant advantage is the elimination of runners, leading to substantial material savings. This is particularly beneficial when using expensive or specialized materials.
- Improved Cycle Times: Reduced post-processing, such as runner removal, significantly shortens the overall cycle time, boosting production efficiency.
- Enhanced Part Quality: Consistent melt temperature and flow contribute to improved part consistency, reduced defects, and superior surface finish. This is especially crucial for complex parts with intricate details.
- Reduced Labor Costs: Automated operation and minimal post-processing reduce the need for manual labor, lowering overall production costs.
- Improved Energy Efficiency: Precise temperature control and minimized heat loss contribute to increased energy efficiency compared to cold runner systems.
- Suitable for a Wide Range of Materials: Hot runner technology can be adapted for various thermoplastics, including those requiring precise temperature control.
Applications Across Industries:
Hot runner technology finds applications in a wide range of industries, including:
- Automotive: Used for manufacturing intricate interior and exterior components, requiring high precision and consistent quality.
- Medical: Crucial for creating precise medical devices and packaging, demanding high levels of cleanliness and sterility.
- Electronics: Enables the production of complex electronic components with tight tolerances.
- Packaging: Used for manufacturing high-volume packaging components such as bottles, containers, and closures.
- Consumer Goods: Widely adopted for producing a variety of consumer products requiring high-quality and efficient production.
Choosing the Right Hot Runner System:
Selecting the appropriate hot runner system depends on several factors:
- Part Design: Complexity and geometry of the molded part significantly influence the system's design.
- Material Properties: The type of plastic influences the system's temperature control and nozzle design.
- Production Volume: The required production rate determines the system's capacity and automation level.
- Budget: The cost of a hot runner system varies depending on complexity and features.
Conclusion:
Hot runner technology represents a remarkable leap forward in plastics manufacturing. By reducing material waste, improving part quality, and enhancing production efficiency, it has become indispensable in many industries. The ongoing advancements in design and control systems ensure that hot runner technology will continue to play a pivotal role in shaping the future of plastics manufacturing.
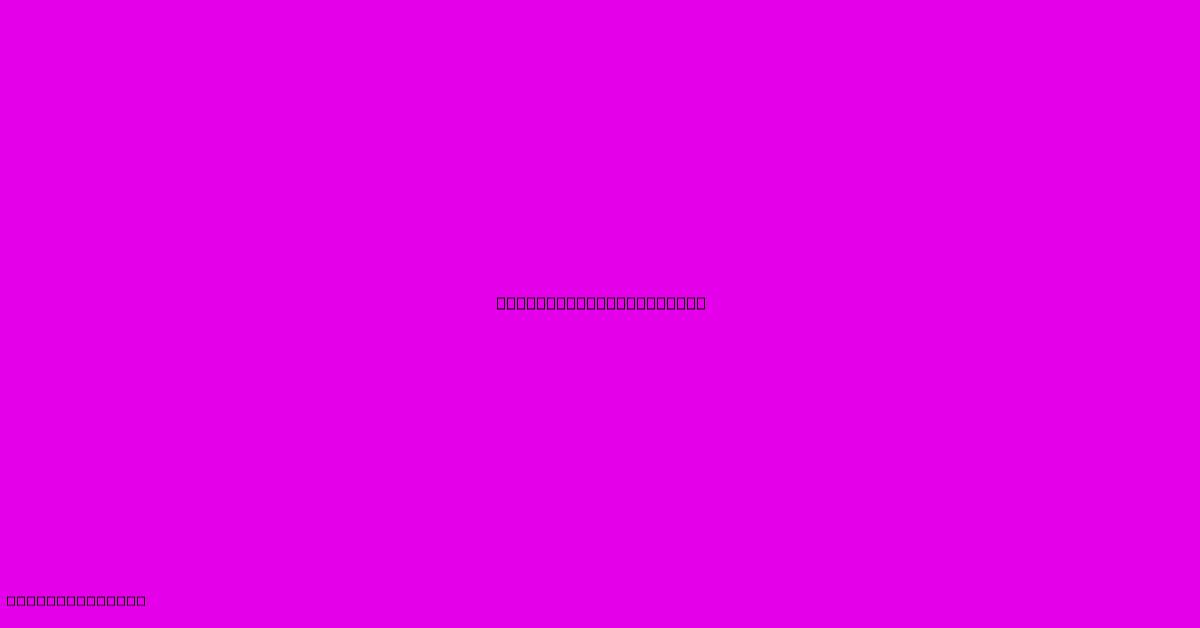
Thank you for visiting our website wich cover about Hot Runner Technology. We hope the information provided has been useful to you. Feel free to contact us if you have any questions or need further assistance. See you next time and dont miss to bookmark.
Featured Posts
-
Women In Technology Conferences
Dec 28, 2024
-
Dia Inocentes Colombia 2024 Bromas
Dec 28, 2024
-
Emerging Technology Libraries
Dec 28, 2024
-
Holiday Market Fire Nycs Bryant Park
Dec 28, 2024
-
Fofana A Rennes Accord Trouve
Dec 28, 2024