Grinding Technology
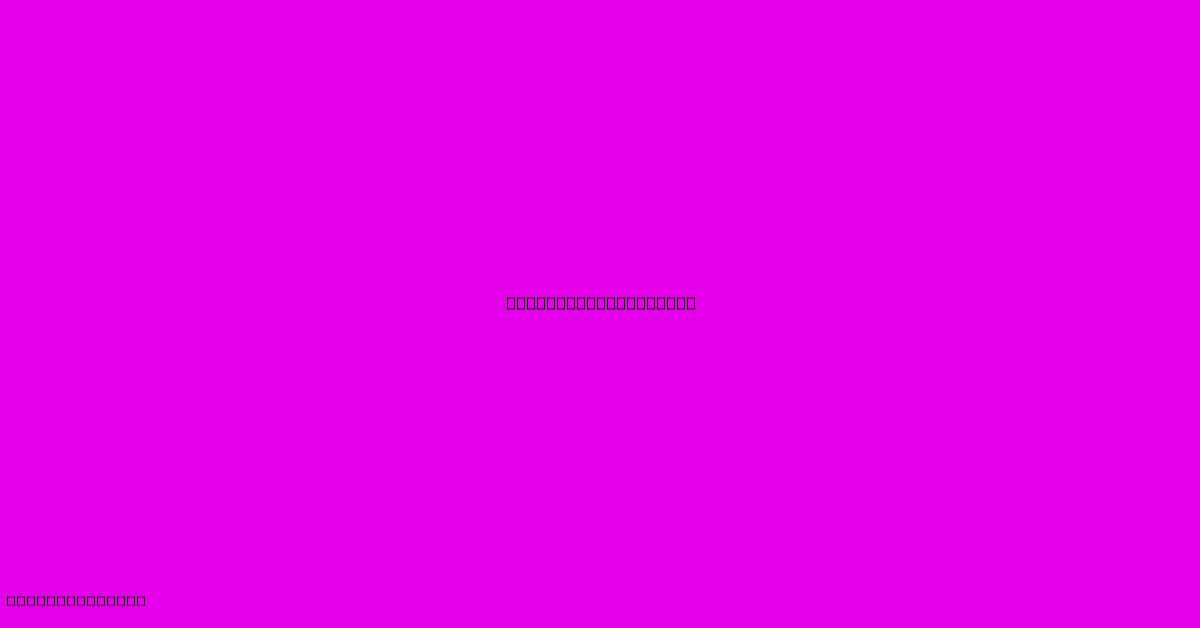
Discover more detailed and exciting information on our website. Click the link below to start your adventure: Visit Best Website mr.cleine.com. Don't miss out!
Table of Contents
Grinding Technology: A Deep Dive into Precision and Efficiency
Grinding technology, a cornerstone of modern manufacturing, encompasses a wide range of processes used to create extremely precise and smooth surfaces on various materials. This article delves into the intricacies of grinding, exploring its diverse applications, underlying principles, and the advancements shaping its future.
What is Grinding?
Grinding is a material removal process that utilizes abrasive particles to remove minute amounts of material from a workpiece's surface. This process differs from other machining methods like milling or turning, as it achieves exceptional surface finish and dimensional accuracy. The abrasive particles, often embedded in wheels, belts, or other tools, progressively wear away the material, leaving behind a highly refined surface.
Types of Grinding Processes:
Several distinct grinding methods cater to diverse industrial needs:
-
Centerless Grinding: This technique grinds cylindrical parts without the need for a center. It's highly efficient for mass production of components like pins and shafts.
-
Surface Grinding: As the name suggests, this method focuses on planar surfaces, achieving flatness and smoothness crucial in various applications.
-
Cylindrical Grinding: This process is used to grind cylindrical workpieces, achieving high precision in diameter and roundness.
-
Internal Grinding: This specialized technique grinds the internal surfaces of components such as bores and holes.
-
Creep Feed Grinding: This method employs a very slow feed rate with a heavy depth of cut, making it ideal for removing large amounts of material.
-
Honing and Lapping: These finishing processes, often following grinding, further refine the surface, achieving exceptional smoothness and precision.
Grinding Wheel Selection:
The selection of the grinding wheel is paramount. Factors to consider include:
-
Abrasive Material: Common abrasives include aluminum oxide (Al2O3) and silicon carbide (SiC), each possessing unique properties suitable for different materials.
-
Bond Type: The bond holds the abrasive grains together. Different bonds, such as vitrified, resinoid, or metal, influence wheel durability and performance.
-
Grain Size: The size of the abrasive grains dictates the rate of material removal and the resulting surface finish. Finer grains produce smoother surfaces.
-
Wheel Structure: This refers to the porosity of the wheel, influencing cooling and chip removal.
Advantages of Grinding:
-
High Precision: Grinding delivers exceptional accuracy and surface finish, vital for critical components.
-
Versatile Material Applicability: It can be used on a wide range of materials, including metals, ceramics, and composites.
-
Efficient Material Removal: While slow compared to other methods, it is efficient for achieving fine finishes.
-
Excellent Surface Finish: The smooth surfaces generated minimize friction and improve performance.
Challenges and Advancements:
Despite its advantages, grinding faces challenges:
-
Heat Generation: The friction between the abrasive and workpiece generates heat, potentially affecting the workpiece's properties. Cooling systems are crucial.
-
Wheel Wear: Grinding wheels wear down over time, impacting performance and requiring frequent dressing or replacement.
-
Process Optimization: Achieving optimal grinding parameters requires expertise and careful control of various factors.
Advancements in grinding technology include:
-
CNC Grinding Machines: Computer Numerical Control (CNC) systems automate the grinding process, enhancing precision and efficiency.
-
Advanced Abrasives: New abrasive materials and coatings offer improved performance and durability.
-
Improved Coolants: Advanced coolants enhance heat dissipation and extend wheel life.
-
Simulation and Modeling: Computer simulations help optimize grinding parameters and predict outcomes.
Applications of Grinding Technology:
Grinding is essential across diverse industries, including:
-
Aerospace: For producing high-precision engine components and aircraft parts.
-
Automotive: For manufacturing engine blocks, crankshafts, and other precision components.
-
Medical: For creating implants, surgical instruments, and other medical devices.
-
Manufacturing: For producing a wide range of components with exceptional surface finish and dimensional accuracy.
Conclusion:
Grinding technology remains a vital process in modern manufacturing, continuously evolving to meet the demands for higher precision, efficiency, and versatility. As technological advancements continue, grinding will play an increasingly crucial role in shaping the future of manufacturing.
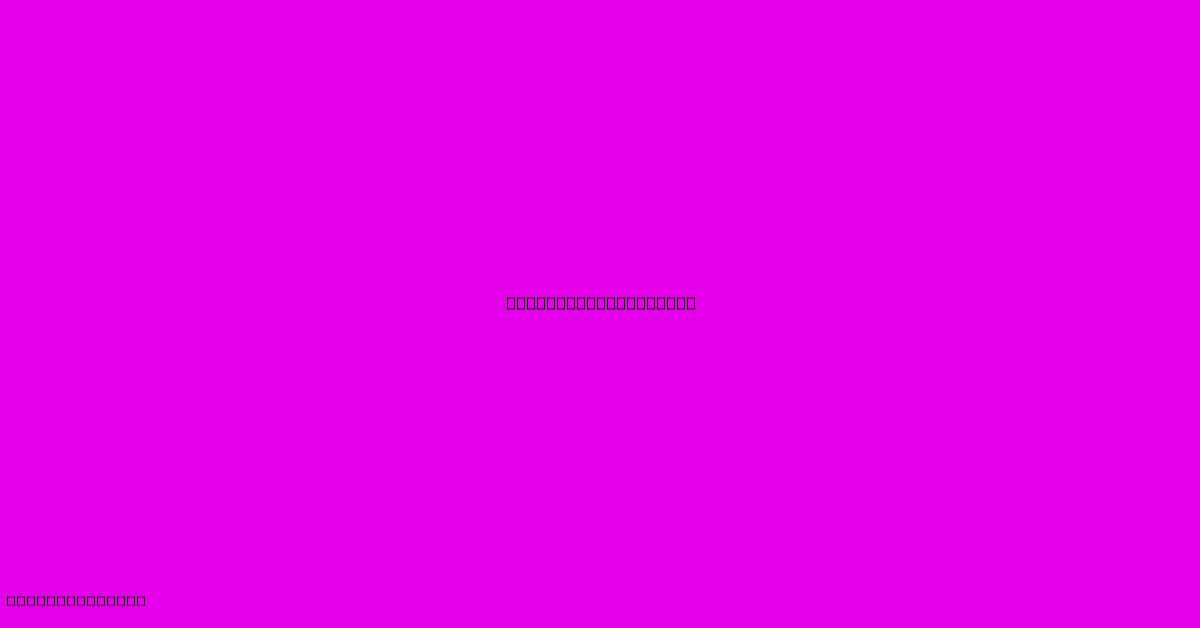
Thank you for visiting our website wich cover about Grinding Technology. We hope the information provided has been useful to you. Feel free to contact us if you have any questions or need further assistance. See you next time and dont miss to bookmark.
Featured Posts
-
Restaurants Oost Vlaanderen Steeds Meer Dicht
Dec 31, 2024
-
Tragedia Na Tailandia Brasileira Morre Em Incendio
Dec 31, 2024
-
Wm Achtelfinale Pietreczkos Arthritis Kampf
Dec 31, 2024
-
Definitive Technology Customer Service
Dec 31, 2024
-
Air Force Aircraft Metals Technology
Dec 31, 2024