Friction Stir Welding Technology
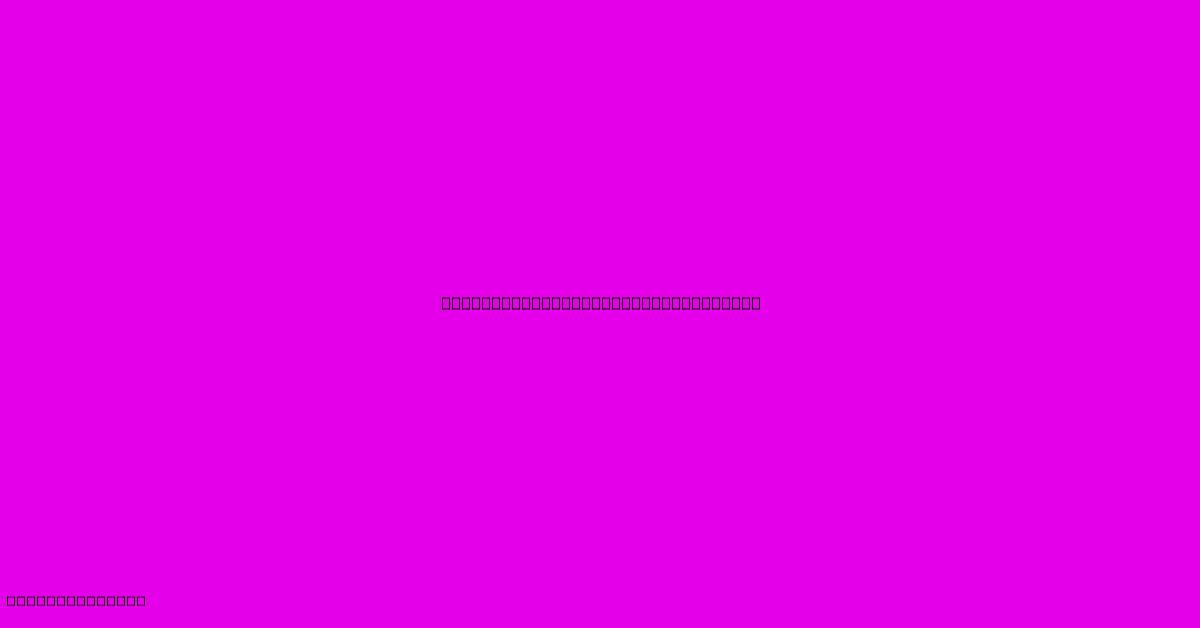
Discover more detailed and exciting information on our website. Click the link below to start your adventure: Visit Best Website mr.cleine.com. Don't miss out!
Table of Contents
Friction Stir Welding: A Revolutionary Joining Technology
Friction Stir Welding (FSW) is a solid-state joining process that's revolutionizing the manufacturing industry. Unlike traditional welding methods that rely on melting the base materials, FSW uses frictional heat generated by a rotating tool to join materials without melting them. This unique approach offers significant advantages in terms of strength, quality, and efficiency, making it an ideal solution for various applications.
How Friction Stir Welding Works:
The process involves a non-consumable tool, typically made of tungsten carbide or steel, with a specially designed pin and shoulder. This tool is inserted into the joint line between two pieces of material and rotated at a high speed (typically 1000-3000 rpm). As the tool moves along the joint, the frictional heat generated softens the material around the tool. The shoulder of the tool then plasticizes the material, forging it together as the tool progresses. The process is completed without melting the base metals, ensuring a high-quality, solid-state bond.
Advantages of Friction Stir Welding:
-
High Strength and Quality: FSW produces welds with superior mechanical properties compared to traditional welding methods. The solid-state nature of the process eliminates porosity and reduces the likelihood of defects, resulting in joints that are strong, ductile, and resistant to cracking.
-
Reduced Distortion: Because the process doesn't involve melting, it minimizes distortion and warping of the joined materials. This is crucial for applications requiring precise dimensional tolerances.
-
Environmentally Friendly: FSW doesn't require filler materials or fluxes, reducing waste and the need for post-weld cleaning. This makes it a more sustainable joining process.
-
Versatile Material Compatibility: FSW can be used to join a wide range of materials, including aluminum alloys, magnesium alloys, steel, and even dissimilar materials. This versatility makes it a highly adaptable technology.
-
Improved Fatigue Resistance: FSW welds often exhibit significantly better fatigue resistance than welds produced by other techniques. This is essential for applications subjected to cyclic loading.
Applications of Friction Stir Welding:
The versatility of FSW makes it suitable for diverse industries and applications:
-
Aerospace: FSW is widely used in the aerospace industry to join lightweight aluminum alloys used in aircraft structures, enhancing strength and reducing weight.
-
Automotive: The automotive industry benefits from FSW for joining lightweight materials in vehicle bodies, improving fuel efficiency and reducing emissions.
-
Maritime: FSW is increasingly used in shipbuilding, especially for joining aluminum alloys in high-strength marine applications.
-
Rail: The railway industry leverages FSW to join lightweight and high-strength materials used in train carriages and tracks.
-
Other Applications: FSW finds applications in various other fields, such as manufacturing of pressure vessels, pipelines, and electronic components.
Challenges and Future Developments:
While FSW offers significant advantages, challenges remain:
-
Tooling: Developing and maintaining appropriate tooling for different materials and geometries can be costly and complex.
-
Process Optimization: Precise control of process parameters (speed, force, tool geometry) is critical to achieving high-quality welds. Optimizing these parameters for different material combinations requires extensive research and development.
-
Inspection: Ensuring the quality of FSW welds can be challenging. Non-destructive testing techniques are often required to validate the integrity of the joints.
Research continues to address these challenges, focusing on:
-
Advanced Tooling Materials: Developing more wear-resistant and robust tooling materials to increase tool life.
-
Automated Process Control: Implementing sophisticated control systems to ensure consistency and repeatability.
-
Improved Nondestructive Testing Techniques: Developing faster and more reliable methods for evaluating the quality of FSW welds.
Conclusion:
Friction Stir Welding is a revolutionary technology that offers significant advantages over traditional welding techniques. Its ability to produce high-strength, high-quality welds with minimal distortion and environmental impact makes it a valuable asset across numerous industries. As research continues to overcome existing challenges and further refine the process, FSW is poised to play an even more prominent role in shaping the future of manufacturing.
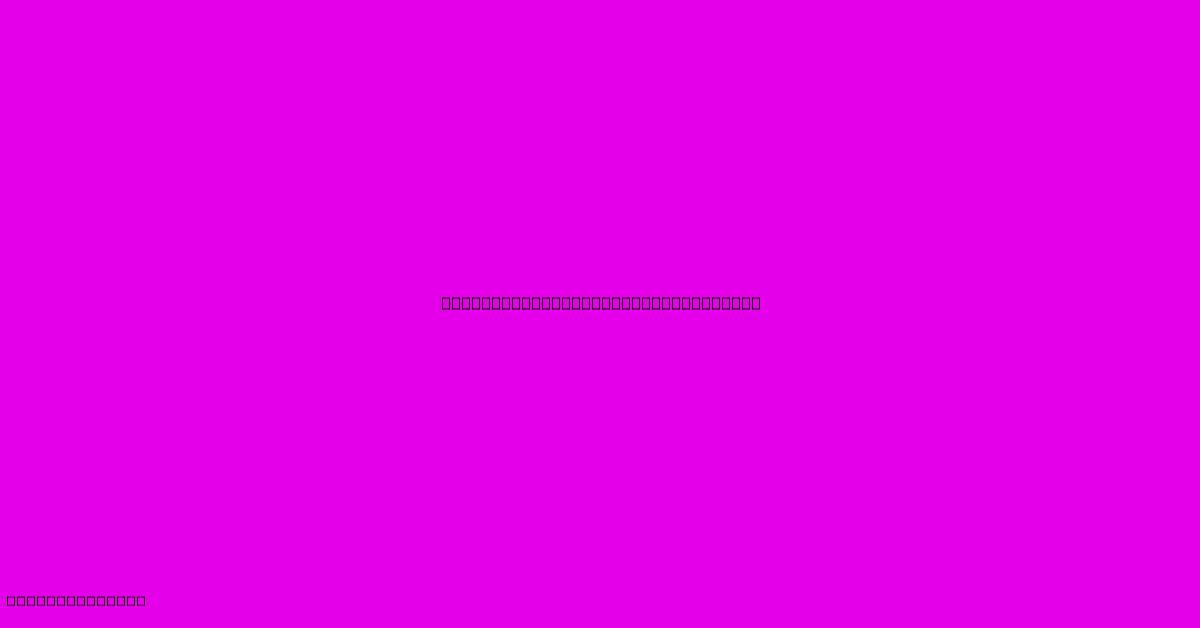
Thank you for visiting our website wich cover about Friction Stir Welding Technology. We hope the information provided has been useful to you. Feel free to contact us if you have any questions or need further assistance. See you next time and dont miss to bookmark.
Featured Posts
-
Bryant Park Fire Holiday Market Blaze
Dec 28, 2024
-
Jerry Jones On Cee Dee Lambs Shoulder
Dec 28, 2024
-
C2 Technology
Dec 28, 2024
-
Construction Technology Conferences 2023
Dec 28, 2024
-
Morte Apos Tiroteio No Palacio
Dec 28, 2024